Introduction
The Cummins N14 engine is a powerful and durable six-cylinder diesel engine widely used in heavy-duty trucking, industrial machinery, and marine applications. Understanding its identification process and key components is crucial for maintenance, troubleshooting, and part replacement.
This guide will walk you through how to locate the engine data plate, interpret key identification numbers, and examine critical engine components that contribute to the Cummins N14’s reliable performance.
Parts Catalog for N14 Cummins Industrial Engines
Locating the Engine Data Plate
Importance of the Engine Data Plate
The engine data plate is essential for identifying the specific configuration of your Cummins N14 engine. It contains critical information that helps with:
- Ordering replacement parts
- Performing diagnostics and repairs
- Understanding the engine’s performance characteristics
- Ensuring proper tuning and calibration
Where to Find the Engine Data Plate
The Cummins N14 engine data plate is located on the fuel pump side of the rocker lever housing. This placement makes it easily accessible for technicians and owners who need to verify engine specifications.
Information on the Engine Data Plate
The data plate provides several crucial details about the engine, including:
1. Engine Serial Number (ESN)
- A unique identifier assigned to each engine.
- Essential for tracking engine history and performing accurate diagnostics.
- Used when ordering replacement parts to ensure compatibility.
2. Control Parts List (CPL)
- Defines the engine’s specific build, including turbocharger, fuel system, and emissions control components.
- Ensures that replacement parts match the original engine configuration.
- Helps technicians calibrate the engine correctly based on its intended specifications.
3. Model and Calibration Codes
- Identifies the engine’s horsepower rating, torque output, and fuel system tuning.
- Indicates software and firmware versions for engines equipped with CELECT™ or CELECT™ Plus ECMs.
Why Engine Identification Matters
Without the correct engine identification, installing the wrong parts or using incorrect calibration settings can lead to:
- Reduced engine efficiency
- Increased wear and tear
- Potential engine damage
- Voided warranties and compliance issues
For any repair or service, always refer to the engine data plate before purchasing parts or making adjustments.
Key Engine Components
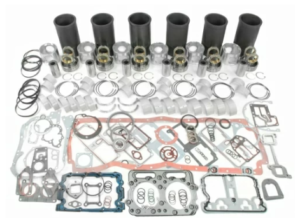
The Cummins N14 is composed of several essential systems that work together to provide power, fuel efficiency, and longevity. Below is a breakdown of its major components and their functions.
Rebuild Kit & Related Components for Cummins N14 Industrial Engine
1. Cylinder Block & Cylinder Head
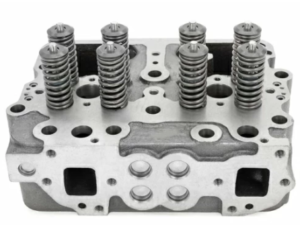
Cylinder Block
- Foundation of the engine that houses the cylinders, pistons, and crankshaft.
- Made of high-strength cast iron to withstand high combustion pressures.
- Includes oil and coolant passages for lubrication and temperature regulation.
Cylinder Head
- Located on top of the cylinder block.
- Contains intake and exhaust valves, valve guides, and fuel injectors.
- Helps seal the combustion chamber to maximize power output.
Common Issues & Maintenance
- Cracks in the cylinder head can cause coolant leaks and overheating.
- Valve wear leads to loss of compression, affecting fuel efficiency.
- Regular inspections and gasket replacements prevent head gasket failures.
Cylinder Head & Related Components for Cummins N14 Industrial Engine
2. Fuel System
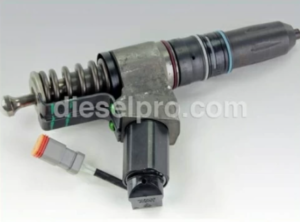
The fuel system is responsible for delivering the correct amount of diesel fuel to the combustion chamber under high pressure.
Components of the Fuel System
- Fuel Injectors – Deliver precise amounts of fuel into the combustion chamber.
- Fuel Lines – Transport fuel from the tank to the injectors.
- Fuel Pump – Pressurizes the fuel for proper combustion.
N14 Fuel System Variants
- PT (Pressure-Time) Fuel System (STC Models):
- Mechanical fuel injection system with Step Timing Control (STC) for optimized timing under varying conditions.
- Mechanical fuel injection system with Step Timing Control (STC) for optimized timing under varying conditions.
- CELECT™ and CELECT™ Plus Electronic Fuel Systems:
- Electronically controlled fuel injection using an ECM (Engine Control Module) for precise delivery.
- Improves fuel efficiency and emissions control.
Common Fuel System Issues
- Clogged injectors reduce power and increase fuel consumption.
- Leaky fuel lines lead to air infiltration and poor combustion.
- Faulty ECM tuning (CELECT™ models) can result in over-fueling or under-fueling.
Injector & Related Components for Cummins N14 Industrial Engine
3. Lubrication System
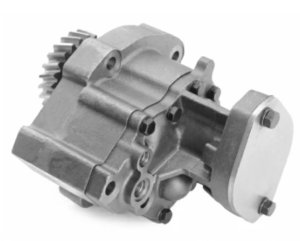
The lubrication system reduces friction and heat between moving engine parts, ensuring longevity and reliability.
Key Lubrication System Components
- Oil Pump – Circulates oil through the engine.
- Oil Filters – Remove contaminants to protect engine components.
- Bearings – Ensure smooth movement of crankshaft and camshaft.
- Piston Cooling Nozzles – Spray oil on the pistons to prevent overheating.
Lubrication System Maintenance
- Check oil levels daily to prevent engine damage.
- Replace oil and filters every 15,000 miles (24,000 km).
- Inspect for oil leaks around the filter and pump area.
Lubrication System & Related Components for Cummins N14 Industrial Engine
4. Cooling System
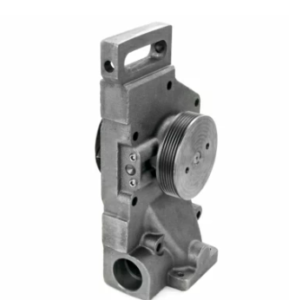
The cooling system prevents overheating and keeps the engine operating at an optimal temperature.
Components of the Cooling System
- Radiator – Dissipates engine heat into the air.
- Thermostat – Regulates coolant flow based on engine temperature.
- Water Pump – Circulates coolant through the system.
- Coolant Filters – Prevent contaminants from clogging passages.
Common Cooling System Issues
- Clogged radiator reduces cooling efficiency.
- Stuck thermostat leads to overheating.
- Coolant leaks cause loss of cooling efficiency, resulting in potential engine damage
.
Cooling System & Related Components for Cummins N14 Industrial Engine
5. Air Intake & Exhaust System
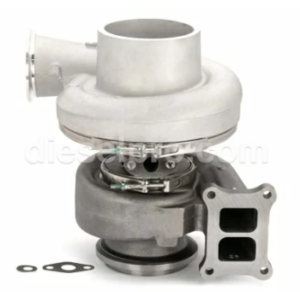
The air intake and exhaust system ensures proper air delivery for combustion and removes exhaust gases.
Air Intake System Components
- Turbocharger – Increases air intake pressure for more efficient combustion.
- Air Filter – Removes dust and debris from intake air.
- Aftercooler – Cools compressed air before entering the engine.
Exhaust System Components
- Exhaust Manifold – Collects exhaust gases from the cylinders.
- Turbocharger Turbine – Uses exhaust gases to spin the intake compressor.
- Muffler and Exhaust Pipe – Reduce noise and direct gases away from the vehicle.
Common Air Intake & Exhaust Issues
- Dirty air filters reduce performance and fuel efficiency.
- Turbocharger failure leads to reduced power output.
- Exhaust leaks can cause reduced boost pressure and increased emissions.
Turbocharger & Related Components for Cummins N14 Industrial Engine
6. Electrical System
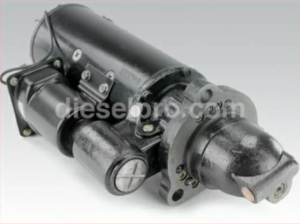
The electrical system provides power distribution, control, and monitoring for the engine.
Components of the Electrical System
- Engine Control Module (ECM) – Manages fuel injection, timing, and diagnostics.
- Wiring Harness – Distributes power to sensors and components.
- Sensors – Monitor pressure, temperature, and airflow.
Electrical System Maintenance
- Inspect wiring connections regularly for corrosion or damage.
- Ensure ECM software is updated for optimal fuel mapping and performance.
- Test sensors periodically to prevent incorrect readings and malfunctions.
Starter & Related Components for Cummins N14 Industrial Engine
Conclusion
Understanding engine identification and key components is essential for efficient maintenance and troubleshooting of the Cummins N14 engine.
By properly locating the engine data plate, you can identify critical details like the serial number, CPL, and calibration codes, ensuring that you use the correct parts and settings for repairs.
Regular maintenance of fuel, lubrication, cooling, air intake, exhaust, and electrical systems ensures your Cummins N14 engine remains in peak operating condition, delivering maximum performance and longevity.
Parts Catalog for N14 Cummins Industrial Engines