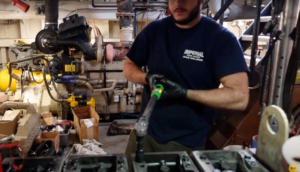
The Cummins KTA19 is a powerful and robust engine designed for heavy-duty applications in marine, industrial, and power generation environments. Despite its durability, like any complex machinery, it can experience operational issues that require effective troubleshooting. This guide outlines advanced troubleshooting techniques to identify, diagnose, and resolve problems quickly and efficiently.
Parts Catalog for Cummins KTA19 Marine Engine
Using Diagnostic Flowcharts for Quick Problem Solving
1. What Are Diagnostic Flowcharts?
Diagnostic flowcharts are visual tools that help technicians systematically approach engine problems. They guide you through a series of yes/no questions and decision points to narrow down potential causes of an issue. These flowcharts are designed to:
- Simplify complex troubleshooting processes
- Ensure consistency in diagnostics
- Minimize the risk of overlooking key symptoms
2. Benefits of Using Diagnostic Flowcharts
- Efficiency: Quickly pinpoint the root cause without unnecessary guesswork.
- Accuracy: Follow a structured path that reduces the chance of missing critical steps.
- Training Tool: Helps less-experienced technicians learn systematic diagnostic approaches.
3. Example: Troubleshooting Engine Overheating
- Step 1: Is the coolant level within the recommended range? (Yes/No)
- Step 2: If no, check for coolant leaks. If yes, proceed to thermostat check.
- Step 3: Is the thermostat functioning correctly? (Yes/No)
- Step 4: If yes, inspect the water pump. If no, replace the thermostat.
This method ensures each potential cause is evaluated logically and efficiently.
Step-by-Step Diagnostic Processes for Common Issues
Advanced troubleshooting requires a structured diagnostic process. Here’s how to approach common Cummins KTA19 problems systematically.
1. Engine Won’t Start
Initial Checks:
- Verify battery charge and connections.
- Check fuel supply and fuel filters.
- Inspect starter motor and wiring.
Advanced Diagnostics:
- Use a diagnostic scanner to check for active fault codes.
- Test fuel pressure at the injectors.
- Verify crankshaft and camshaft sensor signals using an oscilloscope.
2. Loss of Power
Initial Checks:
- Inspect air filters for clogs.
- Check for fuel filter restrictions.
- Examine turbocharger for damage or boost leaks.
Advanced Diagnostics:
- Perform a cylinder cut-out test to identify weak cylinders.
- Measure exhaust backpressure to detect restrictions.
- Use diagnostic software to analyze fuel injector performance.
3. Excessive Smoke
Black Smoke:
- Check for over-fueling (injector leaks or faulty sensors).
- Inspect turbocharger and boost system for leaks.
White Smoke:
- Investigate possible coolant leaks into the combustion chamber.
- Verify correct fuel injection timing.
Blue Smoke:
- Check for oil leaks into the combustion chamber (worn piston rings, valve seals).
Reducing Downtime with Efficient Troubleshooting
Minimizing engine downtime is critical, especially in commercial operations. Here are strategies to improve troubleshooting efficiency:
1. Pre-Diagnostic Preparation
- Gather Engine Information: CPL number, serial number, recent maintenance history.
- Review Fault Codes: Use an ECM diagnostic tool to identify stored codes.
- Visual Inspection: Look for leaks, damaged hoses, loose connections.
2. Prioritize Common Issues
Start with the most likely causes based on symptoms:
- Fuel-related issues often cause starting problems.
- Air intake and turbo problems frequently result in power loss.
- Electrical faults can cause intermittent issues.
3. Use of Predictive Maintenance Tools
Advanced engines like the KTA19 can benefit from predictive diagnostics:
- Oil analysis to detect contamination or wear metals.
- Vibration analysis to identify mechanical imbalance.
- Thermal imaging to spot overheating components.
In-Depth Failure Analysis for Major Components
When a major engine failure occurs, understanding the root cause is essential to prevent recurrence. Here’s how to conduct a detailed failure analysis.
1. Cylinder Head Failures
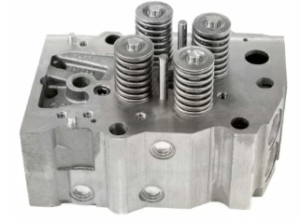
Symptoms:
- Overheating
- Coolant loss
- Loss of compression
Analysis Process:
- Perform a pressure test to detect cracks or leaks.
- Use dye penetrant to identify hairline cracks.
- Inspect valve seats, guides, and combustion chambers for damage.
2. Crankshaft Failures
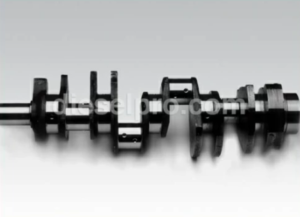
Symptoms:
- Low oil pressure
- Knocking noises
- Metal shavings in oil
Analysis Process:
- Measure crankshaft journals for out-of-round conditions.
- Check for misalignment using a runout gauge.
- Inspect for signs of oil starvation or improper lubrication.
3. Piston and Liner Failures

Symptoms:
- Excessive blow-by
- Loss of compression
- White smoke (coolant leak)
Analysis Process:
- Measure liner protrusion and piston clearance.
- Look for scuffing, scoring, or thermal damage.
- Analyze oil for coolant contamination.
Identifying Root Causes of Engine Failures
Identifying the root cause of a failure is critical for preventing future issues. Use the 5 Whys Method:
- Why did the engine fail? (Example: Crankshaft broke.)
- Why did the crankshaft break? (Oil starvation.)
- Why was there oil starvation? (Clogged oil passage.)
- Why was the oil passage clogged? (Debris from a previous failure.)
- Why wasn’t the debris cleaned during the last overhaul? (Lack of thorough cleaning process.)
This process helps uncover both technical and procedural issues.
Common Root Causes:
- Poor maintenance practices
- Incorrect assembly techniques
- Component fatigue or manufacturing defects
- Operating beyond engine limits
Best Practices for Documenting and Resolving Issues
Proper documentation is key to effective troubleshooting and long-term engine reliability.
1. Diagnostic Logs
Maintain detailed logs of:
- Symptoms observed
- Diagnostic steps taken
- Test results
- Repairs performed
This information helps identify patterns in recurring issues.
2. Photographic Evidence
Take photos of:
- Damaged components
- Wiring connections before disassembly
- Unusual wear patterns
Photos are invaluable for comparing before-and-after conditions and for warranty claims.
3. Clear Communication
When multiple technicians are involved:
- Document findings clearly for seamless hand-offs.
- Use standardized checklists for consistency.
Disclaimer
Advanced diagnostics involve complex systems. Always use diagnostic equipment as outlined in the official Cummins KTA19 service manual. Incorrect diagnostic procedures can lead to misdiagnosis, engine damage, or personal injury. If unsure, consult with a certified Cummins technician.
Parts Catalog for Cummins KTA19 Marine Engine