
Introduction
The Cummins C Series engines—including the 6C, 6CT, and 6CTA—are renowned for their durability, fuel efficiency, and power output. Two critical systems that contribute significantly to these engines’ performance are the air intake and turbocharger systems. Together, they ensure that the engine receives clean, pressurized air, essential for efficient combustion, which in turn maximizes power output and fuel efficiency while reducing emissions.
Turbocharger & Related Components for Cummins 6CT Marine & Industrial Engines
Turbocharger & Related Components for Cummins 6CTA Marine & Industrial Engines
This comprehensive guide covers:
- Maintaining Clean Air Filters and Ducts
- Servicing Turbochargers to Maximize Engine Efficiency
- Diagnosing Air-Related Performance Issues
Understanding how these systems work and how to maintain them will help keep your Cummins C Series engine performing at its best, ensuring reliability, longevity, and optimal fuel economy.
1. Maintaining Clean Air Filters and Ducts
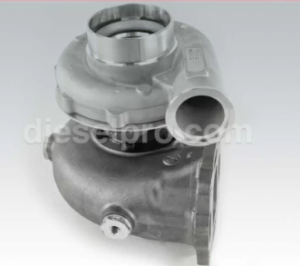
A. The Role of the Air Intake System

The air intake system in Cummins C Series engines is responsible for delivering clean, filtered air to the combustion chamber. Air is drawn through the air filter, passed through ducts, and sometimes cooled in an aftercooler before reaching the intake manifold. Clean air is essential because any contamination can cause premature engine wear, reduce fuel efficiency, and even lead to engine failure.
The air intake system typically includes:
- Air Filter: Removes dust, dirt, and debris from the incoming air.
- Air Intake Ducts: Channels air from the filter to the turbocharger.
- Turbocharger: Compresses incoming air to increase oxygen availability for combustion.
- Aftercooler/Charge Air Cooler: Cools the compressed air from the turbocharger, increasing air density.
- Intake Manifold: Distributes air evenly to each cylinder.
B. Importance of Maintaining Clean Air Filters and Ducts
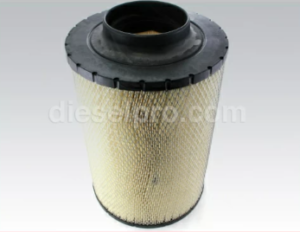
- Optimal Combustion:
Clean air ensures complete combustion, which improves fuel efficiency and reduces emissions.
- Prevention of Engine Wear:
Contaminants like dust and dirt can cause abrasion on cylinder walls, pistons, and valves, leading to premature engine wear.
- Turbocharger Protection:
The turbo relies on clean air. Dirty air can damage the compressor wheel and reduce turbo efficiency.
- Consistent Power Output:
A restricted air filter reduces airflow, causing power loss and poor engine performance.
C. Air Filter Maintenance
- Inspection Frequency:
- Standard Conditions: Inspect every 250 hours or monthly.
- Dusty Environments: Inspect more frequently, possibly weekly.
- How to Inspect the Air Filter:
- Remove the air filter carefully to avoid dislodging debris into the intake system.
- Check for visible dirt, tears, or oil contamination.
- Use a flashlight to look through the filter—if little to no light passes through, it’s time to replace it.
- Cleaning Air Filters (If Reusable):
- Tap the filter gently to remove loose debris.
- Use compressed air to blow out dust from the inside out (never the other way around).
- Do NOT wash or oil paper filters unless they are designed for it.
- When to Replace the Air Filter:
- When damaged, excessively dirty, or after 500 hours of use (even if it looks clean).
- Always replace with a genuine Cummins filter or an OEM-equivalent for proper fit and filtration.
D. Maintaining Air Intake Ducts
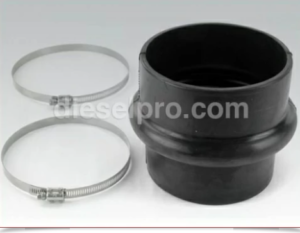
- Visual Inspection:
- Check ducts for cracks, holes, or loose connections.
- Inspect for signs of oil contamination, which could indicate turbocharger seal failure.
- Cleaning Air Ducts:
- Remove ducts and clean with a mild detergent and water.
- Allow ducts to dry completely before reinstallation.
- Check for blockages like leaves, debris, or dirt buildup.
- Sealing Leaks:
- Ensure all clamps and fittings are tight and secure.
- Replace worn-out gaskets or seals immediately.
Air Filter & Related Components for Cummins 6CT Marine & Industrial Engines
Air Filter & Related Components for Cummins 6CTA Marine & Industrial Engines
2. Servicing Turbochargers to Maximize Engine Efficiency
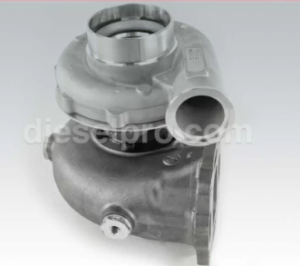
A. How the Turbocharger Works
The turbocharger is a vital component of the Cummins C Series engines, designed to increase air pressure entering the combustion chamber. It utilizes exhaust gas energy to spin a turbine, which drives a compressor wheel that forces more air into the engine. This process improves:
- Power output without increasing engine size.
- Fuel efficiency by enabling complete combustion.
- Lower emissions through better air-fuel ratios.
B. Key Components of the Turbocharger
- Turbine Wheel: Driven by exhaust gases.
- Compressor Wheel: Compresses intake air for combustion.
- Center Housing (Bearing System): Contains oil-fed bearings for smooth rotation.
- Wastegate (if equipped): Controls boost pressure to prevent over-boosting.
- Oil and Coolant Lines: Keep the turbocharger lubricated and cooled.
C. Turbocharger Maintenance Procedures
- Regular Inspection:
- Visual Check: Inspect for oil leaks, cracks, or damaged hoses.
- Shaft Play Test: Check for excessive radial or axial play. Some movement is normal, but excessive play can indicate bearing wear.
- Cleaning the Turbocharger:
- Use solvent or steam to clean the exterior (avoid getting moisture into the oil passages).
- Inspect for carbon buildup on the turbine housing.
- For internal cleaning, it’s best to have the turbo professionally disassembled and cleaned.
- Oil and Lubrication:
- Clean oil is essential. Replace oil and filters at regular intervals to prevent bearing wear.
- Check oil supply lines for blockages—restricted flow can lead to turbo failure.
D. Rebuilding the Turbocharger
If performance drops significantly, or there are signs of internal damage (e.g., excessive shaft play, strange noises), the turbo may need to be rebuilt or replaced.
Common Symptoms Indicating a Rebuild Is Needed:
- Whining noises or unusual sounds under load.
- Excessive exhaust smoke (blue indicates oil burning, black indicates over-fueling).
- Loss of boost pressure despite normal engine operation.
- Oil leakage into the intake or exhaust.
Turbocharger & Related Components for Cummins 6CT Marine & Industrial Engines
Turbocharger & Related Components for Cummins 6CTA Marine & Industrial Engines
3. Diagnosing Air-Related Performance Issues

A. Common Air Intake Problems and Symptoms
- Restricted Airflow:
- Symptoms: Loss of power, black smoke, poor fuel economy.
- Causes: Clogged air filter, collapsed intake duct, or blocked aftercooler.
- Boost Pressure Issues:
- Symptoms: Low power, turbo lag, engine knocking.
- Causes: Faulty wastegate, damaged turbo seals, or boost leaks.
- Turbocharger Failure:
- Symptoms: High-pitched whining, oil leaks, excessive exhaust smoke.
- Causes: Lack of lubrication, foreign object damage, or overheating.
- Air Leaks in Intake System:
- Symptoms: Hissing sounds, erratic engine performance.
- Causes: Loose clamps, cracked hoses, or gasket failures.
B. Diagnostic Procedures
- Checking for Air Leaks:
- Perform a smoke test to identify leaks in intake ducts.
- Use soapy water sprayed on suspected areas; bubbles indicate leaks.
- Boost Pressure Testing:
- Connect a boost pressure gauge to the intake manifold.
- Compare readings to manufacturer specifications (typically 20–25 PSI under load).
- Turbocharger Inspection:
- Spin Test: Ensure the compressor wheel spins freely without resistance.
- Shaft Play Test: Check for excessive side-to-side or in-and-out movement.
- Visual Inspection: Look for oil inside the compressor housing, which indicates seal failure.
C. Resolving Air Intake and Turbo Issues
- Clean or Replace Air Filters:
- Replace clogged filters immediately to restore airflow.
- Replace clogged filters immediately to restore airflow.
- Tighten All Clamps and Hoses:
- Loose fittings can cause pressure loss, leading to poor performance.
- Loose fittings can cause pressure loss, leading to poor performance.
- Repair or Replace Damaged Components:
- Replace cracked hoses, damaged intercoolers, or faulty gaskets.
- Replace cracked hoses, damaged intercoolers, or faulty gaskets.
- Turbocharger Repair:
- If damaged, have the turbo professionally rebuilt or replaced.
- If damaged, have the turbo professionally rebuilt or replaced.
Proactive Maintenance Tips
- Regular Inspection:
- Check the air intake system and turbocharger every 250 hours.
- Inspect after operating in dusty environments or after heavy loads.
- Keep Oil Clean:
- Dirty oil causes turbo bearing failure. Change oil regularly as per Cummins recommendations.
- Dirty oil causes turbo bearing failure. Change oil regularly as per Cummins recommendations.
- Cool Down After Heavy Loads:
- Allow the engine to idle for 2-3 minutes after heavy operation to prevent heat soak damage to the turbocharger.
- Allow the engine to idle for 2-3 minutes after heavy operation to prevent heat soak damage to the turbocharger.
- Monitor Boost Pressure:
- Regularly check boost pressure with a gauge to catch issues early.
- Regularly check boost pressure with a gauge to catch issues early.
- Maintain Tight Seals:
- Replace gaskets, seals, and clamps as needed to prevent leaks.
- Replace gaskets, seals, and clamps as needed to prevent leaks.
Conclusion
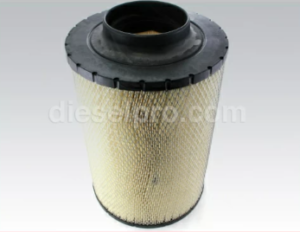
The air intake and turbocharger systems are critical to the performance of Cummins C Series engines (6C, 6CT, 6CTA). Proper maintenance of air filters, ducts, and turbochargers ensures optimal engine performance, fuel efficiency, and reliability.
By following the best practices outlined in this guide—regular inspections, timely cleaning, and proactive maintenance—operators can prevent costly repairs, maximize engine life, and keep their Cummins engines running at peak performance.
Turbocharger & Related Components for Cummins 6CT Marine & Industrial Engines
Turbocharger & Related Components for Cummins 6CTA Marine & Industrial Engines