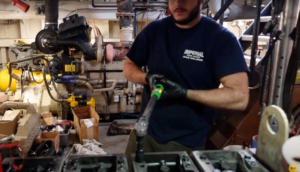
The Cummins KTA19 engine is widely used in heavy-duty applications, including trucks, buses, and construction vehicles. In these setups, the engine plays a crucial role in supporting the brake system, particularly in vehicles equipped with air brakes and brake booster systems. Ensuring that the engine and brake systems are correctly interfaced and maintained is essential for safe and efficient vehicle operation.
Parts Catalog for Cummins KTA19 Marine Engine
In this comprehensive guide, we will cover the following key areas:
- Air compressor maintenance
- Identifying issues with air supply systems
- Servicing and replacing the air compressor
- Brake booster system checks
- Diagnosing brake system failures related to engine performance
- Adjusting engine components to support braking efficiency
Proper maintenance and troubleshooting of these systems are critical because brake failures can lead to life-threatening situations. Always refer to vehicle-specific manuals alongside Cummins’ service guidelines for safe operation and repairs.
Air Compressor Maintenance
The air compressor is the heart of the air brake system in heavy vehicles. It supplies the compressed air needed to activate the brake system. Since the air compressor is driven by the engine, regular maintenance is crucial to prevent brake failures and ensure consistent performance.
Functions of the Air Compressor:
- Generates compressed air for the brake system.
- Maintains proper air pressure in the air tanks (reservoirs).
- Powers other pneumatic systems in the vehicle (e.g., suspension, transmission controls).
Identifying Issues with Air Supply Systems
Issues with the air supply system can lead to reduced braking efficiency, brake lag, or even complete brake failure. Recognizing early warning signs can prevent accidents and costly repairs.
Common Symptoms of Air Supply Issues:
- Slow Air Build-Up:
- The air pressure gauge takes too long to reach normal operating levels.
- May indicate a worn compressor, air leaks, or restricted lines.
- Excessive Moisture in the Air System:
- Water in the air tanks can cause corrosion and freezing in cold weather.
- Indicates a failing air dryer or faulty drain valves.
- Unusual Noises:
- Hissing sounds may indicate air leaks in hoses or connections.
- Knocking or rattling noises could suggest internal compressor damage.
- Frequent Compressor Cycling:
- The compressor cycles on and off more than usual.
- This can be caused by air leaks or a malfunctioning governor.
- Overheating Compressor:
- A hot compressor may indicate poor lubrication, blocked cooling lines, or overloading.
- A hot compressor may indicate poor lubrication, blocked cooling lines, or overloading.
Air Supply System Inspection Checklist:
- Check Air Pressure Gauges: Ensure the system reaches and maintains the correct pressure (typically 90-120 psi for most vehicles).
- Inspect Air Lines: Look for cracks, wear, or loose fittings.
- Listen for Leaks: Use a spray bottle with soapy water to detect leaks around fittings and hoses.
- Drain Air Tanks: Remove moisture regularly to prevent corrosion.
- Test the Governor: Verify that the compressor cuts in and out at the correct pressures.
Servicing and Replacing the Air Compressor
Regular maintenance of the air compressor ensures reliable brake system performance. In cases of compressor failure, timely replacement is critical to avoid brake system malfunctions.
Air Compressor Service Intervals:
- Inspect and service the compressor every 6,000 to 10,000 miles or as recommended by the vehicle manufacturer.
- Perform a full inspection during routine engine maintenance.
Servicing the Air Compressor:
1. Preparation:
- Turn off the engine and allow it to cool.
- Depressurize the air system by draining all air tanks.
2. Visual Inspection:
- Check for oil leaks, air leaks, and damaged components.
- Inspect the drive belt (if belt-driven) for wear and proper tension.
3. Clean the Air Intake Filter:
- Replace or clean the air intake filter to ensure proper airflow to the compressor.
4. Lubrication Check:
- For compressors that rely on engine lubrication, ensure the oil supply lines are clean and unrestricted.
- For self-lubricated compressors, check and change the oil according to the service schedule.
Replacing the Air Compressor:
Tools Required:
- Wrenches and sockets
- Torque wrench
- Gasket scraper
- Replacement air compressor
- New gaskets and seals
Step-by-Step Replacement Procedure:
- Disconnect the Battery: Prevent accidental engine starts during the procedure.
- Depressurize the System: Drain all air from the tanks.
- Disconnect Air Lines: Label and remove the air supply and discharge lines.
- Remove Drive Components: Detach belts or disconnect the gear-driven mechanism.
- Unbolt the Compressor: Carefully remove mounting bolts and detach the compressor.
- Prepare for Installation: Clean mounting surfaces and install new gaskets.
- Install the New Compressor: Align properly, bolt in place, and reconnect air lines.
- Reconnect Drive Mechanism: Ensure proper belt tension or gear alignment.
- Refill and Bleed the System: Start the engine, build air pressure, and check for leaks.
- Test the Brakes: Verify proper air pressure and brake response.
Brake Booster System Checks
The brake booster system amplifies the force applied to the brake pedal, reducing the effort needed to engage the brakes. In air brake systems, this is typically achieved using air-assisted brake boosters.
Functions of the Brake Booster:
- Enhances brake pedal force using compressed air.
- Provides consistent braking performance with minimal driver effort.
- Reduces brake fade during heavy-duty operations.
Diagnosing Brake System Failures Related to Engine Performance
Brake system issues can sometimes be linked to engine performance problems, especially since the air compressor and brake booster rely on engine power.
Symptoms of Brake System Failures:
- Hard Brake Pedal:
- Indicates a failing brake booster or insufficient air pressure.
- May be caused by a faulty compressor or engine vacuum issues (in vacuum-assisted systems).
- Brake Lag:
- Delayed braking response can result from air supply restrictions, leaks, or governor malfunctions.
- Delayed braking response can result from air supply restrictions, leaks, or governor malfunctions.
- Engine Stalling When Braking:
- A severe vacuum leak in the brake booster can affect engine idle in certain applications.
- A severe vacuum leak in the brake booster can affect engine idle in certain applications.
- Low Air Pressure Warnings:
- Frequent low-pressure warnings may point to compressor issues or leaking air lines.
- Frequent low-pressure warnings may point to compressor issues or leaking air lines.
- Excessive Brake Noise:
- Hissing noises during braking can indicate air leaks in the booster diaphragm or valves.
- Hissing noises during braking can indicate air leaks in the booster diaphragm or valves.
How Engine Performance Affects Brake Systems:
- Reduced Engine Power: Low RPMs or engine load fluctuations can affect compressor output, reducing air supply to brakes.
- Faulty Governor: If the air compressor governor fails to regulate pressure correctly, the brake system may be compromised.
- Exhaust Brake Malfunctions: Integrated engine braking systems (like Jake brakes) can affect brake performance if not properly adjusted.
Adjusting Engine Components to Support Braking Efficiency
To ensure the brake system operates effectively, it’s essential to adjust and maintain engine components that directly or indirectly influence braking performance.
Key Engine Components Affecting Braking Efficiency:
- Air Compressor:
- Adjust the governor cut-in and cut-out pressures to maintain optimal air pressure levels.
- Adjust the governor cut-in and cut-out pressures to maintain optimal air pressure levels.
- Exhaust Brake (if equipped):
- Adjust the exhaust brake settings for proper engagement during downhill braking to reduce wear on service brakes.
- Adjust the exhaust brake settings for proper engagement during downhill braking to reduce wear on service brakes.
- Engine Speed Governor:
- Verify that the governor maintains appropriate RPMs to support consistent air compressor output.
- Verify that the governor maintains appropriate RPMs to support consistent air compressor output.
- Idle Speed Adjustment:
- Ensure the engine’s idle speed is sufficient to keep the compressor functioning effectively, especially in stop-and-go traffic.
- Ensure the engine’s idle speed is sufficient to keep the compressor functioning effectively, especially in stop-and-go traffic.
- Cooling System Maintenance:
- Overheating can reduce compressor efficiency. Regularly service the cooling system to prevent thermal-related compressor failures.
- Overheating can reduce compressor efficiency. Regularly service the cooling system to prevent thermal-related compressor failures.
Tips for Enhancing Braking Efficiency:
- Regular Air System Maintenance: Check for leaks, drain moisture, and service the air dryer.
- Monitor Brake Adjustment: Keep brakes properly adjusted to prevent uneven wear and improve response times.
- Optimize Engine Braking Systems: For vehicles with Jake brakes, ensure proper integration with the primary braking system.
Best Practices for Brake System Maintenance in Cummins KTA19 Applications
-
Conduct Regular Inspections:
- Perform pre-trip brake system checks for commercial vehicles.
- Inspect air lines, fittings, and brake chambers regularly.
-
Monitor Air Pressure Gauges:
- Always ensure the system operates within the recommended 90–120 psi range.
- Always ensure the system operates within the recommended 90–120 psi range.
-
Service the Air Dryer:
- Prevent moisture buildup that can lead to freezing and corrosion in the brake lines.
- Prevent moisture buildup that can lead to freezing and corrosion in the brake lines.
-
Maintain Proper Lubrication:
- Ensure the air compressor receives adequate lubrication from the engine to prevent premature wear.
- Ensure the air compressor receives adequate lubrication from the engine to prevent premature wear.
-
Train Operators and Technicians:
- Educate drivers on recognizing brake system issues early.
- Provide training for technicians on air brake systems and engine interfaces.
Common Brake System Issues and Troubleshooting
Symptom | Possible Cause | Solution |
Hard Brake Pedal | Failing brake booster, low air pressure | Check booster, inspect air compressor |
Slow Air Pressure Build-Up | Worn compressor, air leaks | Service compressor, repair air leaks |
Frequent Air Loss | Leaking hoses, faulty valves | Replace damaged hoses, inspect valves |
Brake Drag | Faulty brake chamber or return springs | Adjust or replace brake chamber |
Hissing Noise When Braking | Air leaks in booster or lines | Inspect for leaks, replace faulty parts |
Conclusion
Proper maintenance of the brake system interfaces in Cummins KTA19-equipped vehicles is critical for safety, performance, and reliability. Since the engine plays an integral role in supporting the brake system through the air compressor and booster components, understanding these connections is essential for effective troubleshooting and repairs.
By regularly inspecting the air supply system, servicing the compressor, and ensuring proper engine adjustments, you can significantly reduce the risk of brake-related failures and improve overall vehicle safety.
Disclaimer
Brake system failures can be life-threatening. Always refer to vehicle-specific manuals alongside the Cummins service guide when troubleshooting. Ensure that all maintenance and repairs are performed by qualified personnel, and never compromise on safety when working with braking systems.
Parts Catalog for Cummins KTA19 Marine Engine