Introduction
Proper storage and preservation of Cummins QSC 8.3 and QSL 9 engines is essential for preventing corrosion, component degradation, and startup failures after long periods of inactivity. Following correct preservation procedures ensures optimal performance and longevity when storing an engine for seasonal downtime, transportation, or extended inactivity.
This guide provides a detailed approach to long-term storage procedures, corrosion prevention methods, and correct restart procedures after storage.
Parts Catalog for QSC 8.3 Cummins Marine and Industrial Engines
Parts Catalog for QSL 9 Cummins Marine and Industrial Engines
Long-Term Engine Storage Procedures
Engines that remain unused for three months or longer require specific preservation techniques to prevent internal and external deterioration. The goal of long-term storage is to protect engine components, fuel systems, cooling systems, and electrical connections from moisture, rust, and contamination.
Key Considerations Before Storage
Before storing an engine, the following factors must be evaluated:
- Storage duration (short-term vs. long-term)
- Environmental conditions (humidity, temperature, exposure to contaminants)
- Fuel and coolant stability
- Battery preservation and electrical system disconnection
- Engine position (horizontal vs. vertical storage)
Step-by-Step Long-Term Storage Procedure
1. Cleaning and External Protection
- Wash the engine exterior to remove dirt, oil, and grease that could lead to corrosion.
- Inspect for leaks and address any seals or gasket failures before storage.
- Apply a corrosion inhibitor or a light coat of rust-preventive oil on exposed metal surfaces.
- Cover the engine with a breathable tarp or storage cover to prevent dust accumulation.
2. Fuel System Preparation
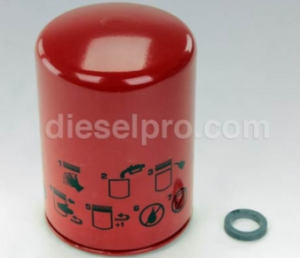
Fuel left in the system for extended periods can degrade, leading to fuel contamination, injector clogging, and microbial growth.
- Drain the fuel tank or add a diesel fuel stabilizer to prevent oxidation.
- Run the engine for 10-15 minutes to circulate the stabilizer through the fuel lines and injectors.
- Drain water separators and replace fuel filters to prevent condensation buildup.
- Seal the fuel system by covering vent tubes and disconnecting fuel lines.
3. Lubrication System Preparation
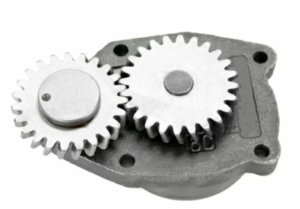
- Change engine oil and filters before storage to remove contaminants that cause corrosion.
- Add a fogging oil or long-term storage lubricant to the cylinders to protect against moisture damage.
- Crank the engine briefly (without starting) to distribute oil evenly.
4. Cooling System Preparation
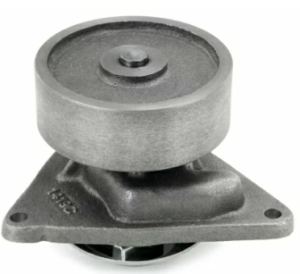
- Flush the coolant system and refill with a long-life antifreeze that contains corrosion inhibitors.
- Check all hoses and seals for wear or leaks.
- Leave the radiator cap slightly open to relieve pressure buildup.
5. Electrical System and Battery Maintenance
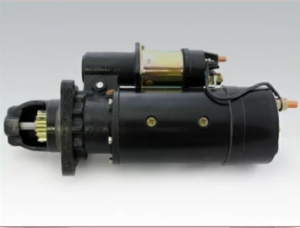
- Disconnect the battery to prevent drainage and sulfation during storage.
- Store batteries in a dry, climate-controlled environment and periodically charge to prevent discharge.
- Apply dielectric grease to electrical connections to prevent corrosion.
6. Exhaust and Air Intake Protection
- Seal the intake and exhaust ports with moisture-resistant plugs to prevent humidity and insect infestation.
- Use desiccant packs or silica gel inside the intake system to absorb excess moisture.
7. Engine Positioning and Storage Environment
- Store the engine in a dry, climate-controlled environment to prevent moisture exposure.
- Place the engine on wooden blocks or a pallet to prevent condensation damage from cold surfaces.
- If storing outdoors, ensure the engine is fully covered with a breathable tarp.
Preventing Corrosion and Damage During Downtime
When an engine is stored, moisture, contaminants, and inactivity can lead to severe component damage. Corrosion prevention is critical in marine, industrial, and outdoor environments, where exposure to saltwater, humidity, and temperature fluctuations increases the risk of deterioration.
Effects of Long-Term Inactivity on Engine Components
Component |
Common Issues Due to Storage |
Prevention Methods |
Fuel System | Microbial growth, fuel degradation, injector clogging | Add fuel stabilizer, drain water separator |
Oil System | Moisture contamination, sludge buildup | Change oil, use protective lubricants |
Cooling System | Corrosion, seal degradation, freeze damage | Flush system, use corrosion-inhibited coolant |
Electrical Components | Battery discharge, wiring corrosion | Disconnect battery, apply dielectric grease |
Turbocharger | Rust formation, oil seal hardening | Apply rust inhibitor, rotate turbo shaft periodically |
Cylinders and Pistons | Rust, loss of lubrication film | Use fogging oil, rotate crankshaft monthly |
Steps to Prevent Corrosion and Damage
1. Controlling Moisture and Humidity
- Store the engine in a low-humidity environment or use dehumidifiers in storage areas.
- Apply anti-corrosion spray on all exposed metal surfaces.
- Use vapor corrosion inhibitors (VCI) bags for extended storage.
2. Protecting Seals and Gaskets
- Apply silicone-based protectants on rubber seals to prevent drying and cracking.
- Ensure hoses are properly secured to prevent leaks when restarting the engine.
3. Maintaining Bearings and Rotating Components
- Rotate the crankshaft manually every 30 days to prevent piston rings from sticking.
- Lubricate moving parts before storage to maintain a protective oil film.
Restarting Procedures After Storage
When removing a stored engine from storage, proper recommissioning is necessary to ensure safe startup and smooth operation.
Step-by-Step Engine Restart Procedure
1. Inspect and Remove Storage Precautions
- Remove all intake and exhaust seals or plugs before starting.
- Inspect for any leaks, cracks, or loose fittings caused by long-term storage.
- Check belts and hoses for stiffness or signs of deterioration.
2. Refilling and Replacing Fluids
- Drain and replace old fuel if not stabilized before storage.
- Replace engine oil and coolant if stored for over 12 months.
- Prime the fuel system by cycling the key or using a manual priming pump.
3. Reinstalling the Battery and Checking the Electrical System
- Reconnect the battery terminals and check voltage levels before starting.
- Test the alternator and starter motor for proper function.
- Verify wiring harness connections to prevent electrical faults.
4. Manually Crank the Engine
- Rotate the crankshaft manually before attempting to start the engine.
- This ensures lubrication is distributed evenly and prevents dry starts.
5. Initial Startup and Monitoring
- Start the engine and let it idle for 10-15 minutes.
- Monitor oil pressure and coolant temperature for any irregularities.
- Listen for abnormal noises, such as knocking or rough idling.
- Check exhaust emissions for excessive smoke, which may indicate fuel system issues.
6. Post-Startup Inspection
- Inspect for fluid leaks around the engine block, turbocharger, and cooling system.
- Perform a load test to ensure the engine runs smoothly under normal conditions.
- Verify torque settings for critical fasteners to confirm no loosening occurred during storage.
Preventative Maintenance After Storage
To keep the engine in peak condition, follow a preventative maintenance checklist after long-term storage.
- Change all fluids and filters to ensure system cleanliness.
- Inspect turbocharger for free movement and apply fresh lubrication.
- Test fuel injectors for spray pattern and fuel delivery consistency.
- Run a full diagnostic scan using Cummins INSITE or another diagnostic tool to check for ECM faults.
- Perform a test run under load to verify performance and efficiency.
Conclusion
Proper storage and preservation of Cummins QSC 8.3 and QSL 9 engines is essential for protecting critical components, preventing corrosion, and ensuring a smooth restart. By following structured storage procedures, implementing corrosion prevention measures, and correctly restarting the engine, operators can extend the lifespan and efficiency of their engines.
Parts Catalog for QSC 8.3 Cummins Marine and Industrial Engines
Parts Catalog for QSL 9 Cummins Marine and Industrial Engines