
Introduction
The Cummins KTA38 and KTA50 engines are high-performance diesel powerhouses designed for marine, industrial, and power generation applications. To maintain efficiency, reliability, and longevity, regular maintenance is critical. While daily checks focus on fluid levels and leak detection, weekly maintenance takes a more in-depth approach, ensuring vital components function optimally.
Ignoring weekly maintenance can lead to performance degradation, unexpected breakdowns, and costly repairs. This guide provides an extensive breakdown of the essential weekly maintenance tasks, including step-by-step instructions on how to inspect, test, and maintain key engine components.

Parts Catalog for KTA38 Cummins Marine and Industrial Engines
Parts Catalog for KTA50 Cummins Marine and Industrial Engines
Essential Weekly Inspections for Cummins KTA38 and KTA50
Each week, a detailed inspection of various engine systems ensures preventative maintenance is effective. These weekly maintenance operations target electrical, fuel, lubrication, turbocharging, and safety shutdown systems, all of which play critical roles in engine performance.
1. Inspect Battery Connections and Test Voltage Levels
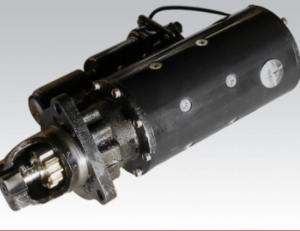
Why It’s Important:
Batteries provide the necessary starting power for the engine. Loose or corroded connections, along with low voltage, can cause hard starts, electrical malfunctions, and even system failures.
How to Perform the Check:
- Visual Inspection – Look for corrosion or loose battery terminals.
- Clean Terminals – If corrosion is present, clean with a mixture of baking soda and water, using a wire brush to remove buildup.
- Tighten Connections – Ensure all battery connections are snug.
- Voltage Testing – Use a multimeter to check battery voltage:
- 12V systems should read between 12.4V and 12.7V when fully charged.
- 24V systems should read between 24.8V and 25.4V when fully charged.
- Load Test the Battery – If voltage drops below 9.6V (for a 12V system) or 19.2V (for a 24V system) under load, consider replacing the battery.
- Check the Alternator – Ensure the alternator is charging correctly (should read 13.8V to 14.5V for a 12V systemand 27.6V to 28.5V for a 24V system).
Signs of Battery Issues:
- Slow engine cranking.
- Flickering dashboard lights.
- Frequent need for jump-starts.
- Sulfur (rotten egg) smell, indicating overcharging.
2. Check the Fuel System for Leaks or Loose Fittings
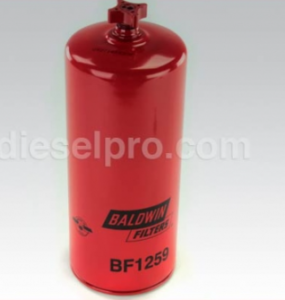
Why It’s Important:
A leaking fuel system can cause engine inefficiencies, increased fuel consumption, and potential fire hazards. Loose fittings and clogged fuel filters can also cause hard starts, misfires, and power loss.
How to Perform the Check:
- Inspect Fuel Lines and Hoses – Look for cracks, wear, and damp spots.
- Check Fuel Fittings – Ensure fittings are tightened to spec and not leaking.
- Drain Water from the Fuel/Water Separator – Water in the fuel system can cause injector damage and poor combustion.
- Check Fuel Pressure – Ensure proper fuel pressure using a fuel pressure gauge:
- Ideal pressure varies by model, but typically ranges between 25-45 PSI.
- Ideal pressure varies by model, but typically ranges between 25-45 PSI.
- Inspect Fuel Injectors – Look for carbon buildup, leaks, or unusual knocking sounds from the cylinders.
Common Fuel System Issues and Fixes:
Issue |
Possible Cause |
Solution |
Fuel leak | Loose fittings or damaged lines | Tighten fittings or replace damaged hoses |
Low fuel pressure | Clogged fuel filter or faulty fuel pump | Replace filter, test fuel pump |
Excessive black smoke | Overfueling or injector issues | Inspect and clean injectors |
White smoke | Water in fuel or leaking head gasket | Drain water separator, check for coolant leaks |
3. Inspect Turbocharger Condition for Unusual Noises or Signs of Oil Leakage
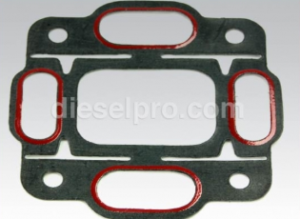
Why It’s Important
The turbocharger is critical for power output and fuel efficiency. A malfunctioning turbo can lead to poor performance, excessive smoke, and increased fuel consumption.
How to Perform the Check:
- Inspect for Oil Leaks – Look around the turbocharger housing and intake piping.
- Check for Excessive Shaft Play – Remove the intake piping and spin the turbine by hand. If it feels loose or wobbles, the bearings may be worn.
- Listen for Unusual Noises
Whining or high-pitched squealing → Indicates bearing failure.
- Rattling → Suggests excessive shaft play.
- Hissing sound → Could indicate a boost leak.
- Check Boost Pressure – Use a boost gauge to confirm the turbo is delivering adequate pressure:
- Most Cummins KTA38 and KTA50 turbochargers should generate 25-35 PSI of boost under load.
- Most Cummins KTA38 and KTA50 turbochargers should generate 25-35 PSI of boost under load.
Signs of Turbocharger Issues:
- Excessive black smoke (due to overfueling from low boost).
- Loss of power and sluggish acceleration.
- Oily residue in the intake system.
- Loud whining noise under acceleration.
Fixes:
- Replace clogged air filters to prevent turbo strain.
- Tighten loose intercooler and intake piping connections.
- Replace the turbo if shaft play is excessive.
4. Test the Safety Shutdown System to Ensure Proper Operation
Why It’s Important:
The safety shutdown system is designed to protect the engine from catastrophic damage caused by overheating, low oil pressure, or over-speeding. Regular testing ensures the system activates when necessary.
How to Perform the Check:
- Verify Sensor Functionality – Check that temperature and oil pressure sensors send correct readings to the ECU.
- Simulate a Fault Condition –
- Temporarily disconnect an oil pressure sensor and start the engine. The shutdown system should engage.
- Allow the engine to warm up, then disconnect the coolant temperature sensor. The system should trigger a shutdown.
- Inspect Emergency Stop Button – Press it to confirm the engine shuts down immediately.
- Reset and Restart the Engine – Ensure the system functions correctly after being reset.
Common Shutdown Issues and Fixes:
Issue |
Possible Cause |
Solution |
Engine doesn’t shut down when sensor is disconnected | Faulty shutdown sensor | Replace sensor |
Frequent unexpected shutdowns | Wiring issues or faulty ECU | Inspect wiring harness, test ECU |
Emergency stop button doesn’t work | Button failure or loose connection | Replace button, check wiring |
5. Lubricate Moving Components to Reduce Friction and Wear
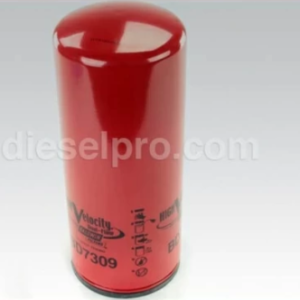
Why It’s Important:
Lubrication prevents excessive wear, overheating, and premature failure of moving components such as throttle linkages, belt tensioners, and fan clutches.
How to Perform the Check:
- Use manufacturer-recommended lubricants for each component.
- Lubricate throttle and governor linkages using light machine oil.
- Grease the water pump and alternator bearings as needed.
- Check fan clutch for proper engagement and lubricate if necessary.
- Inspect and grease driveline components for smooth operation.
Signs of Poor Lubrication:
- Squeaking or grinding noises.
- Stiff throttle or control linkages.
- Excessive heat buildup on rotating parts.
Conclusion
Weekly maintenance ensures that the Cummins KTA38 and KTA50 engines operate at peak performance, preventing unexpected failures, excessive wear, and costly repairs.
Key Takeaways:
Test and maintain battery connections to ensure reliable starts.
Inspect fuel systems for leaks, pressure loss, and contamination.
Check the turbocharger for signs of failure to maintain engine efficiency.
Verify safety shutdown systems to prevent catastrophic engine damage.
Lubricate moving parts to reduce friction and wear.
For premium aftermarket Cummins parts, visit Diesel Pro Power—your trusted source for high-performance diesel engine components.
Parts Catalog for KTA38 Cummins Marine and Industrial Engines
Parts Catalog for KTA50 Cummins Marine and Industrial Engines