
Engine Performance Tests | Fuel Flow Measurement

Ensuring optimal engine performance in Cummins ISM, ISMe, and QSM11 engines requires thorough engine testing and fuel flow measurement. These engines are designed for heavy-duty applications, including commercial trucks, industrial machinery, and marine vessels, making regular performance testing essential to maintain efficiency, power output, and emissions compliance.
Engine testing helps identify early signs of wear, fuel inefficiency, air intake issues, and performance irregularities. A properly maintained engine delivers maximum power output, improved fuel economy, and reduced downtime.
This guide provides a comprehensive step-by-step process for performing engine performance tests, evaluating fuel flow, diagnosing performance issues, and ensuring the engine operates within manufacturer specifications.
For specific torque values, fuel pressure settings, and performance benchmarks, consult an OEM service manual or contact Diesel Pro Power for expert assistance.
Parts Catalog for ISM Cummins Marine and Industrial Engines
Parts Catalog for QSM11 Cummins Marine and Industrial Engines
Engine Performance Tests for Cummins ISM, ISMe, and QSM11
Engine performance tests measure key indicators such as horsepower, torque, fuel efficiency, emissions, and temperature stability. These tests help identify underperforming components, airflow restrictions, fuel delivery inefficiencies, and excessive wear.
Key Engine Performance Indicators
Horsepower Output – Measures the engine’s ability to generate power efficiently.
Torque Measurement – Assesses the rotational force produced by the engine.
Fuel Economy Testing – Evaluates fuel consumption relative to power output.
Combustion Efficiency – Determines how effectively the engine burns fuel.
Boost Pressure and Airflow – Checks turbocharger function and intake efficiency.
Oil Pressure and Temperature – Ensures proper lubrication and cooling.
Exhaust Emissions Levels – Monitors pollutants to meet emissions regulations.
Common Symptoms of Engine Performance Issues
A malfunctioning engine may exhibit power loss, excessive fuel consumption, rough idling, or excessive emissions.
Symptom | Possible Cause | Recommended Action |
Loss of Power | Clogged air filter, failing turbocharger | Inspect air intake, test turbo boost pressure |
High Fuel Consumption | Incorrect fuel timing, weak fuel injectors | Check injector calibration, verify ECM settings |
Engine Misfires | Low compression, faulty fuel delivery | Perform compression test, check fuel pressure |
Excessive Black Smoke | Over-fueling, poor combustion efficiency | Inspect injectors, test turbocharger airflow |
Rough Idle and Vibrations | Unbalanced cylinders, worn mounts | Perform balance test, inspect engine mounts |
Step-by-Step Engine Performance Testing
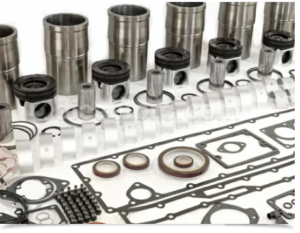
Engine testing involves several key diagnostic procedures to measure efficiency and detect potential mechanical or electronic issues.
Step 1: Pre-Test Inspection and Setup
- Check Fluid Levels
- Ensure engine oil, coolant, and fuel levels are at manufacturer-recommended levels.
- Ensure engine oil, coolant, and fuel levels are at manufacturer-recommended levels.
- Inspect Air and Fuel Filters
- Clogged filters restrict flow and reduce engine performance.
- Clogged filters restrict flow and reduce engine performance.
- Warm Up the Engine to Operating Temperature
- Run the engine for 10-15 minutes to ensure accurate test results.
- Run the engine for 10-15 minutes to ensure accurate test results.
- Connect a Diagnostic Tool (ECM Scanner)
- Use Cummins INSITE™ or an OBD-II scanner to check for fault codes.
- Use Cummins INSITE™ or an OBD-II scanner to check for fault codes.
Step 2: Performing a Dynamometer Test
A dynamometer (dyno) test measures the horsepower, torque, and load efficiency of the engine.
- Secure the Engine on a Chassis or Engine Dyno
- Ensure the engine is properly secured to prevent movement during testing.
- Ensure the engine is properly secured to prevent movement during testing.
- Run the Engine Through RPM Ranges
- Record horsepower and torque output at different RPM levels.
- Compare results to OEM engine specifications.
- Analyze Engine Load and Response
- A weaker than expected torque curve may indicate fuel delivery or compression issues.
- A weaker than expected torque curve may indicate fuel delivery or compression issues.
- Monitor Exhaust Gas Temperature (EGT)
- High EGT readings can indicate fuel overuse or improper combustion.
- High EGT readings can indicate fuel overuse or improper combustion.
Step 3: Measuring Airflow and Boost Pressure
- Check the Turbocharger Boost Pressure
- Use a boost pressure gauge to verify proper operation.
- Compare readings against OEM boost pressure specifications.
- Inspect the Intercooler for Leaks
- Use a smoke machine to detect air leaks in the intercooler and intake pipes.
- Use a smoke machine to detect air leaks in the intercooler and intake pipes.
- Perform an Airflow Test on the Intake System
- Blocked air passages reduce combustion efficiency.
- Blocked air passages reduce combustion efficiency.
Step 4: Evaluating Oil Pressure and Temperature Stability

- Measure Oil Pressure at Different RPM Levels
- Proper oil pressure prevents engine wear and overheating.
- Normal oil pressure readings:
- Idle: 20-30 psi
- Full Load: 50-70 psi
- Check for Excessive Temperature Fluctuations
- Fluctuating oil temperatures may indicate cooling system inefficiencies.
- Fluctuating oil temperatures may indicate cooling system inefficiencies.
Fuel Flow Measurement for Cummins ISM, ISMe, and QSM11
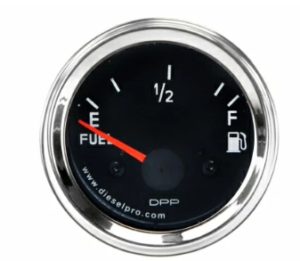
Proper fuel flow measurement ensures accurate fuel delivery, optimal combustion, and efficient power output. A fuel system imbalance can lead to power loss, excessive fuel consumption, and emissions non-compliance.
Key Fuel System Components for Accurate Flow Measurement
Fuel Pump – Supplies pressurized fuel to the injectors.
Fuel Injectors – Deliver atomized fuel into the combustion chamber.
Fuel Rail and Pressure Regulator – Maintain consistent pressure.
Fuel Return Lines – Recirculate excess fuel to prevent waste.
ECM Fuel Control Module – Adjusts fuel delivery based on real-time engine data.
Common Symptoms of Fuel Flow Issues
Symptom |
Possible Cause |
Recommended Action |
Low Fuel Pressure Warning | Clogged fuel filter, weak fuel pump | Replace fuel filter, test pump pressure |
Excessive Smoke from Exhaust | Over-fueling, leaking injector seals | Inspect injectors, check fuel trims |
Engine Surging or Stalling | Inconsistent fuel pressure | Test fuel rail pressure, check ECM for errors |
Fuel Leaks | Worn seals, cracked fuel lines | Inspect and replace damaged components |
Step-by-Step Fuel Flow Measurement
- Connect a Fuel Pressure Gauge to the Fuel Rail
- Compare readings with OEM specifications:
- Idle Fuel Pressure: 25-35 psi
- Full Load Fuel Pressure: 50-70 psi
- Compare readings with OEM specifications:
- Perform a Fuel Flow Rate Test
- Measure the amount of fuel delivered per minute.
- A significant drop in flow may indicate blockages or pump failure.
- Check the Return Line for Fuel Restrictions
- If fuel return is slower than expected, inspect clogged return lines.
- If fuel return is slower than expected, inspect clogged return lines.
- Inspect the Fuel Pump for Proper Operation
- Listen for abnormal noise from the pump.
- Test fuel pump voltage to verify electrical functionality.
Final Notes on Engine Testing and Fuel Flow Measurement for Cummins ISM, ISMe, and QSM11
Perform regular engine performance tests to identify early issues.
Monitor fuel flow and fuel pressure to optimize efficiency.
Check ECM diagnostics to detect sensor or injector faults.
Maintain proper airflow and boost pressure for full power output.
Consult Diesel Pro Power for expert guidance and replacement parts.
By following these detailed procedures, you ensure optimal engine performance, improved fuel economy, and extended service life for Cummins ISM, ISMe, and QSM11 engines.
Parts Catalog for ISM Cummins Marine and Industrial Engines
Parts Catalog for QSM11 Cummins Marine and Industrial Engines