
General Cummins B Series Engine FAQs
What is the difference between the Cummins 6B, 6BT, and 6BTA engines?
The Cummins 6B is a naturally aspirated 5.9L inline-six diesel engine with no turbocharger, offering simpler maintenance and reliability at the cost of lower power. The 6BT adds a turbocharger, improving horsepower, torque, and fuel efficiency. The 6BTA includes both a turbocharger and an aftercooler, which cools the compressed air before it enters the engine, providing even greater performance and efficiency. If you need maximum power and reliability for marine or heavy-duty applications, the 6BTA is the best option.
Parts Catalog for Cummins 4B Marine Engine
Parts Catalog for Cummins 4BT Marine Engine
Parts Catalog for Cummins 4BTA Marine Engine
Parts Catalog for Cummins 6B Marine Engine
Parts Catalog for Cummins 6BT Marine Engine
Parts Catalog for Cummins 6BTA Marine Engine
How do I identify my Cummins engine model and serial number?
The engine serial number (ESN) and model number are stamped on a data plate attached to the engine. For Cummins B Series engines, the data plate is typically located on the left side of the timing cover or valvThe serial number is also stamped into the block if the plate is missinge cover. If the plate is missing, the serial number is also stamped into the block. The ESN is critical when ordering replacement parts, identifying engine specifications, and verifying compatibility.

See Reading A Cummins Engine Data Plate
What are the most common applications of Cummins B Series engines?
Cummins B Series engines are used in a wide range of industries due to their durability, efficiency, and versatility. Common applications include:
- Marine: Powering boats, yachts, and commercial fishing vessels (6BTA is preferred).
- Trucking: Used in medium-duty trucks and buses (6BT for high torque output).
- Industrial: Found in generators, compressors, and construction machinery (4BT and 6BT).
- Agricultural: Used in tractors, irrigation systems, and harvesters (4BT for compact equipment).
- Military: Installed in armored vehicles and transport trucks for their rugged design.
What is the expected lifespan of a Cummins B Series engine?
With proper maintenance, a Cummins B Series engine can last between 500,000 and 1,000,000 miles or over 20,000 hours of operation before requiring a rebuild. Factors that affect lifespan include oil change intervals, fuel quality, cooling system health, and load conditions. Engines used in marine or heavy industrial applications may require more frequent servicing due to harsher conditions.
How often should I service my Cummins 6B, 6BT, or 6BTA engine?

- Oil and filter change: Every 250-300 hours or 6,000-10,000 miles.
- Fuel filter replacement: Every 10,000-15,000 miles or if contaminated fuel is suspected.
- Coolant change: Every two years or 4,000 hours to prevent corrosion and overheating.
- Valve adjustments: Every 150,000 miles or 5,000 hours for optimal engine performance.
- Turbo inspection: Every 100,000 miles to check for leaks and efficiency issues.
Regular servicing prevents breakdowns, extends engine life, and improves fuel efficiency.
What type of oil is recommended for Cummins B Series engines?

Cummins recommends using 15W-40 diesel engine oil that meets API CK-4 or CJ-4 specifications. In extreme cold conditions, 5W-40 synthetic oil can be used to improve startup performance. Using the correct oil viscosity is crucial for engine longevity, lubrication, and preventing excessive wear. Always check your specific engine manual for oil capacity and viscosity requirements.
What are the key differences between the 4B, 4BT, and 4BTA models?
- 4B: A naturally aspirated, 3.9L 4-cylinder version of the B Series engine. It has lower power but is reliable and fuel-efficient.
- 4BT: The turbocharged version, which improves power and torque output. This is commonly used in off-road equipment and conversions.
- 4BTA: Includes a turbocharger and an aftercooler, which further enhances fuel efficiency and lowers exhaust temperatures, making it ideal for high-performance applications.
The 4BTA is the most powerful option in the 4-cylinder lineup, while the 4B is preferred for its simplicity and durability.
How do I know if my engine needs an overhaul?
A Cummins B Series engine may require an overhaul if it experiences significant power loss, excessive oil consumption, or low compression. Key signs include:
- Excessive white, black, or blue smoke from the exhaust.
- Low oil pressure even after an oil change.
- Increased fuel consumption without an obvious reason.
- Hard starting or misfires due to worn injectors or pistons.
- Knocking noises from internal components.
- High blow-by levels, indicating worn piston rings.
If your engine shows multiple signs of wear, it may be time for an in-frame or out-of-frame rebuild.
View our customer overhaul a Cummins 6BT.
Part 1:
Part2:
What are the signs of a failing Cummins engine?
A failing engine will often exhibit multiple warning signs before a complete breakdown. Symptoms include:
- Loss of power or difficulty accelerating, often due to fuel system issues.
- Overheating caused by coolant leaks, a faulty thermostat, or a clogged radiator.
- Excessive smoke from the exhaust (black = overfueling, white = coolant leak, blue = oil burning).
- Unusual knocking noises from worn bearings or piston damage.
- Frequent oil or coolant leaks, indicating failing gaskets or seals.
- Hard starting or excessive cranking, possibly due to low compression or weak injectors.
Addressing these issues early can prevent costly repairs and extend the engine’s lifespan.
What is the best way to extend the life of my Cummins B Series engine?
To maximize the lifespan of your Cummins engine, follow these best practices:
- Use high-quality oil and change it at recommended intervals to prevent wear.
- Monitor coolant levels and replace it every two years to avoid overheating and corrosion.
- Inspect and replace fuel filters regularly to prevent injector damage.
- Perform periodic valve adjustments to ensure smooth operation.
- Keep air filters clean to maintain turbocharger and intake efficiency.
- Run the engine at proper operating temperatures—cold starts and excessive idling can cause internal damage over time.
- Use only high-quality aftermarket parts from trusted suppliers to maintain reliability and performance.
Preventive maintenance is key to achieving long-term durability and fuel efficiency.
Oil and Lubrication FAQs for Cummins 6B, 6BT, and 6BTA Engines
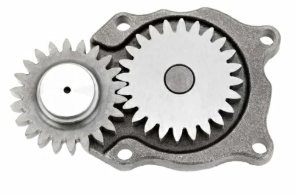
How often should I change the oil in my Cummins 6B, 6BT, or 6BTA engine?
Regular oil changes are critical to extending the life of your Cummins B Series engine. For normal operating conditions, Cummins recommends changing the oil every 250-300 hours or every 6,000-10,000 miles in on-road applications. If your engine is used in harsh environments, such as marine, industrial, or off-road applications, you may need to change the oil more frequently, around 200 hours or 5,000 miles.
Neglecting oil changes can lead to excessive wear, sludge buildup, and reduced engine efficiency, potentially causing premature failure. Always check your oil condition before reaching the maximum interval—if it appears thick, dark, or contaminated, an earlier oil change may be necessary.
What is the correct oil capacity for a Cummins 6BTA engine?
The oil capacity of a Cummins 6BTA engine varies depending on the specific configuration and application, but in general:
- Standard oil capacity: 4.5 gallons (17 liters)
- Marine applications: May have slightly larger sumps, increasing capacity to 5 gallons (19 liters)
- Industrial and generator applications: Capacities can range from 4.5 to 6 gallons (17-23 liters)
When performing an oil change, always check the oil level using the dipstick after refilling to ensure it’s within the correct range. Overfilling or underfilling can cause severe engine damage, such as excessive oil pressure or oil starvation.
What oil viscosity is best for different operating conditions?
Cummins recommends using 15W-40 diesel engine oil for most operating conditions. However, in extreme temperatures, different viscosities may be more appropriate:
- Normal to warm climates (above 0°F/-18°C): 15W-40
- Cold climates (-10°F to -20°F / -23°C to -29°C): 10W-30 or 5W-40 synthetic
- Extreme cold (below -20°F / -29°C): 0W-40 synthetic
Using the correct viscosity ensures proper lubrication, reduces engine wear, and prevents excessive oil consumption.Using oil that is too thick in cold temperatures can lead to difficult startups, while oil that is too thin in hot environments can reduce protection and increase wear.
How do I properly check my Cummins engine’s oil level?
To ensure accurate oil level readings, follow these steps:
- Park on a level surface and shut down the engine. Let the oil settle for at least 10 minutes before checking.
- Locate the dipstick, remove it, and wipe it clean. This ensures no residual oil gives a false reading.
- Reinsert the dipstick fully, then remove it again. Check where the oil reaches on the indicator.
- Ensure the oil level is between the “MIN” and “MAX” marks. If it’s below the minimum, add oil in small increments, checking frequently.
- If overfilled, drain excess oil immediately. Overfilling can lead to excessive crankcase pressure and potential seal damage.
Never check the oil level while the engine is running, as this will produce an inaccurate reading and could result in injury.
What happens if I use the wrong type of oil in my engine?
Using incorrect oil viscosity or low-quality oil can cause serious damage to your Cummins engine. Consequences include:
- Poor lubrication, leading to increased metal-on-metal wear.
- Sludge and deposit buildup, clogging oil passages and reducing efficiency.
- Overheating, as incorrect oil may not dissipate heat effectively.
- Low oil pressure, if the oil is too thin or has lost its viscosity.
- Increased oil consumption, requiring more frequent top-ups.
Always use API-certified diesel engine oil that meets Cummins specifications (API CK-4 or CJ-4). Using non-diesel oil or lower-quality lubricants can shorten engine life and void warranties.
How do I change the oil filter on my Cummins B Series engine?
Replacing the oil filter is a critical step in routine maintenance. Follow these steps:
- Run the engine for 5-10 minutes to warm up the oil, making it easier to drain.
- Turn off the engine and locate the oil filter. On most Cummins B Series engines, it’s found on the driver’s side of the engine block.
- Place an oil catch pan underneath the filter. Use an oil filter wrench to loosen and remove the old filter.
- Lightly coat the rubber gasket on the new filter with fresh oil. This helps create a better seal.
- Install the new filter by hand, tightening it until snug. Do not over-tighten—hand-tight plus ¾ turn is sufficient.
- Refill with the correct oil type and check for leaks.
Always replace the oil filter during every oil change to prevent contamination and sludge buildup.
What are the symptoms of low oil pressure in a Cummins engine?
Low oil pressure is a serious issue that requires immediate attention. Symptoms include:
- Illuminated oil pressure warning light on the dashboard.
- Tapping or knocking noises from the engine due to lack of lubrication.
- Excessive engine wear, leading to power loss or overheating.
- Fluctuating or dropping oil pressure gauge readings.
Common causes include low oil levels, a clogged oil filter, worn bearings, or a failing oil pump. Ignoring low oil pressure can lead to catastrophic engine failure.
Can I use synthetic oil in my Cummins 6BTA engine?
Yes, synthetic oil is safe to use in Cummins 6BTA engines, provided it meets API CK-4 or CJ-4 specifications. Synthetic oil offers better protection in extreme temperatures, improves fuel efficiency, and reduces sludge buildup.
However, switching to synthetic oil in an older engine with existing leaks may worsen oil consumption issues. If your engine has significant wear, consider using a high-mileage synthetic blend instead.
What should I do if my engine is consuming too much oil?
Excessive oil consumption is often caused by:
- Worn piston rings or valve seals, allowing oil to enter the combustion chamber.
- Turbocharger seal leaks, burning oil through the exhaust.
- Overfilling or using low-quality oil, leading to improper lubrication.
To address this:
- Check for external leaks around the oil pan, valve cover, and turbo.
- Perform a compression test to identify worn rings.
- Switch to a higher-viscosity oil if your engine has high mileage.
- Ensure you’re using a high-quality aftermarket oil filter to prevent excess pressure loss.
If oil consumption is excessive, an engine overhaul or turbo rebuild may be required.
How can I reduce oil leaks on my Cummins engine?
Oil leaks are common on older Cummins engines but can be minimized by:
- Replacing worn gaskets and seals (valve cover, oil pan, front/rear main seals).
- Using high-quality aftermarket parts for seals and gaskets.
- Ensuring the crankcase ventilation system is functioning properly to reduce pressure buildup.
- Checking for loose or cracked oil lines, particularly around the turbocharger.
If leaks persist, consider using an oil additive designed to recondition seals, but this is only a temporary fix.
Cooling System FAQs for Cummins 6B, 6BT, and 6BTA Engines

What coolant should I use for my Cummins 6BT engine?
Cummins recommends using a heavy-duty ethylene glycol-based coolant with supplemental coolant additives (SCA)to prevent corrosion, cavitation, and liner pitting. The best options include:
- Pre-mixed 50/50 coolant (ethylene glycol and distilled water)
- Extended-life coolants (ELC) that meet Cummins CES 14603 specifications
- Coolants with nitrite additives for additional protection in wet sleeve engines
Avoid using standard automotive coolant, as it lacks the necessary additives for diesel engines. If using concentrate, always mix it with distilled water (50/50 ratio) to prevent mineral buildup.
How often should I flush and replace the coolant in my engine?
For conventional coolant, Cummins recommends flushing and replacing it every two years or 4,000 hours. If using extended-life coolant (ELC), the interval can extend to 6 years or 12,000 hours with proper maintenance.
Signs that a coolant flush is needed:
- Coolant has turned brown or muddy (indicating contamination)
- Corrosion or rust buildup in the radiator or water pump
- Frequent overheating issues
- Coolant leaks or unexplained coolant loss
Regular flushing removes contaminants and prevents clogged radiators, water pump failure, and overheating.
What are the signs of a failing water pump?
A failing water pump can lead to serious engine overheating and cooling system damage. Watch for these warning signs:
- Coolant leaks from the water pump housing or weep hole
- Engine overheating or fluctuating temperature readings
- Loud whining or grinding noise from the front of the engine
- Low coolant flow when inspecting with the radiator cap removed
- Steam or excessive coolant loss
A faulty water pump should be replaced immediately to prevent catastrophic engine damage.
How do I properly bleed air from the cooling system?
Trapped air in the cooling system can cause hot spots, overheating, and poor coolant circulation. To properly bleed air:
- Fill the radiator and expansion tank with coolant while the engine is off.
- Start the engine and let it run at idle with the radiator cap off.
- Monitor the coolant level and watch for air bubbles escaping.
- Rev the engine slightly (1,500-2,000 RPMs) to help release trapped air.
- Turn the heater to full hot to allow coolant to circulate through the heater core.
- Once bubbles stop appearing, top off the coolant and replace the radiator cap.
- Check coolant levels again after driving for 15-30 minutes.
Never open the radiator cap while the engine is hot, as pressurized steam can cause burns.
What temperature should my Cummins engine run at?
A properly operating Cummins 6BT engine should maintain a temperature between 180°F and 200°F (82°C – 93°C)under normal conditions.
- Too cold (<170°F/77°C): Possible thermostat stuck open, causing poor fuel combustion and efficiency loss.
- Normal range (180°F – 200°F): Ideal operating temperature for performance and longevity.
- Too hot (>220°F/104°C): Overheating issue, potentially caused by a failing water pump, clogged radiator, or coolant leak.
If the engine temperature exceeds 220°F, shut down immediately to avoid major damage to the head gasket or cylinder liners.
How do I check if my thermostat is working properly?
A faulty thermostat can cause overheating or an engine running too cold. To check:
- Start the engine and let it warm up.
- Monitor the temperature gauge. If the engine stays cold for too long, the thermostat might be stuck open.
- Feel the upper radiator hose. If it remains cold after the engine reaches operating temperature, the thermostat is stuck closed.
- Remove and inspect the thermostat. Place it in hot water (190°F) and observe if it opens.
- Replace if necessary. Always use a Cummins-approved thermostat to ensure proper temperature regulation.
What causes overheating in Cummins B Series engines?
Several issues can cause overheating, including:
- Low coolant levels or leaks (hoses, radiator, water pump)
- Clogged radiator or cooling passages from debris or old coolant buildup
- Faulty thermostat stuck closed, preventing coolant circulation
- Water pump failure leading to low coolant flow
- Blown head gasket, allowing coolant loss into the combustion chamber
- Air pockets in the cooling system, causing localized hot spots
Ignoring overheating can lead to severe engine damage, including cracked cylinder heads and warped pistons.
Can I use water instead of coolant in an emergency?
Yes, you can temporarily use water in an emergency to prevent overheating, but it should be replaced with proper coolant as soon as possible. Using only water long-term can cause:
- Corrosion and rust formation in the cooling system
- Cavitation damage to the cylinder liners
- Reduced boiling point, increasing the risk of overheating
- Poor lubrication for the water pump, leading to premature failure
If you must use water, only use distilled water to avoid mineral buildup in the system.
What are the symptoms of a clogged radiator?
A clogged radiator restricts coolant flow, leading to poor cooling performance and overheating. Symptoms include:
- Higher than normal engine temperatures
- Coolant leaks around the radiator due to pressure buildup
- Uneven temperature distribution (one side of the radiator is hotter than the other)
- Discolored or sludgy coolant inside the radiator
- Steam from the radiator cap or expansion tank
If the radiator is clogged, flush it or replace it immediately to prevent overheating damage.
How do I test the coolant level sensor?
A malfunctioning coolant level sensor can cause false low coolant warnings or fail to detect actual coolant loss. To test:
- Locate the coolant level sensor, usually in the coolant reservoir or radiator.
- Disconnect the sensor connector and inspect for corrosion or damage.
- Use a multimeter to check for continuity. If the sensor does not respond when submerged in coolant, it may be faulty.
- Manually test by unplugging the sensor. If the warning light stays on, the sensor circuit may be damaged.
- Replace if necessary and verify proper function by checking coolant levels manually.
Fuel System FAQs for Cummins 6B, 6BT, and 6BTA Engines

How often should I replace the fuel filter on a Cummins 6BTA?
The fuel filter on a Cummins 6BTA should be replaced every 10,000-15,000 miles or every 500 hours of operation, depending on operating conditions. In marine, off-road, or high-dust environments, fuel filters should be replaced every 300-400 hours to ensure proper fuel flow and prevent clogging.
Signs that your fuel filter needs immediate replacement include:
- Hard starting or prolonged cranking before the engine runs
- Loss of power, hesitation, or rough idling
- Excessive black smoke from the exhaust
- Frequent stalling, especially under load
A clogged fuel filter can lead to injector damage, reduced fuel efficiency, and engine failure. Always use high-quality aftermarket fuel filters to maintain optimal engine performance.
What are the symptoms of a bad fuel injector?
A failing fuel injector can cause a variety of performance issues due to improper fuel delivery. Symptoms include:
- Rough idling or misfiring, indicating an injector is not delivering fuel properly
- Loss of power and acceleration, especially under load
- Increased fuel consumption due to inefficient combustion
- Excessive white or black smoke from the exhaust
- Loud knocking or ticking sounds, often referred to as “diesel knock”
- Strong fuel odor, indicating a leaking injector
A bad injector can cause serious engine damage if ignored, including excessive carbon buildup and premature wear on pistons and cylinders. If you suspect injector issues, have them professionally tested or replaced.
How do I bleed air from the fuel system?
Air trapped in the fuel system can cause hard starts, misfires, and fuel starvation. To properly bleed air:
- Locate the manual priming pump on the fuel filter housing.
- Loosen the bleed screw on the fuel filter to allow trapped air to escape.
- Pump the primer until fuel starts flowing without bubbles.
- Tighten the bleed screw once only fuel (no air bubbles) is coming out.
- If the engine still won’t start, slightly crack open an injector line and crank the engine until air escapes.
- Once the engine starts, let it run at idle for a few minutes to ensure all air is purged from the system.
Failing to bleed air properly can result in hard starting, erratic engine operation, and even fuel pump damage.Always prime the system after fuel filter changes or any fuel system repairs.
What fuel pressure should my Cummins 6B engine have?
Proper fuel pressure ensures efficient fuel delivery and injector operation. The recommended fuel pressure for Cummins 6B, 6BT, and 6BTA engines varies depending on system configuration:
- Lift pump pressure: 14-16 PSI at idle, 20+ PSI under load
- Injection pump inlet pressure: Above 10 PSI at all times
- Common rail fuel systems (if applicable): 4,000-25,000 PSI depending on the model
Low fuel pressure can indicate:
- A clogged fuel filter
- Weak or failing lift pump
- Leaking or restricted fuel lines
- Faulty injection pump
If fuel pressure is too low, it can cause poor performance, misfires, and eventual injector failure. Use a fuel pressure gauge to monitor system health regularly.
Can I use biodiesel in my Cummins B Series engine?
Yes, Cummins B Series engines can run on biodiesel blends, but there are important considerations:
- B5 (5% biodiesel, 95% diesel) is fully approved and requires no modifications.
- B20 (20% biodiesel) is acceptable, but requires more frequent fuel filter changes.
- Biodiesel blends above B20 are not recommended as they may cause fuel system damage over time.
Potential risks of biodiesel include:
- Faster fuel filter clogging, as biodiesel cleans fuel lines more aggressively than regular diesel.
- Increased water absorption, leading to microbial growth and fuel contamination.
- Compatibility issues with older rubber fuel lines and seals.
If using biodiesel, ensure it meets ASTM D6751 (U.S.) or EN 14214 (Europe) standards, and monitor fuel system components regularly.
How do I prevent fuel contamination?
Fuel contamination can cause clogged injectors, poor performance, and expensive engine damage. To prevent contamination:
- Use high-quality diesel fuel from reputable sources.
- Drain the fuel/water separator regularly to remove moisture.
- Replace fuel filters at recommended intervals to prevent debris buildup.
- Keep fuel tanks full to reduce condensation and microbial growth.
- Inspect fuel lines and seals for cracks or leaks that could introduce contaminants.
- Use fuel stabilizers and biocides if storing diesel fuel for long periods.
Contaminated fuel is one of the leading causes of diesel engine problems. Regular maintenance and proper storage can help prevent major issues.
Why is my engine losing power under load?
If your Cummins engine is losing power when under load, the most common causes include:
- Clogged fuel filter, restricting fuel flow to the injectors.
- Weak lift pump, failing to maintain adequate fuel pressure.
- Air leaks in fuel lines, causing poor fuel delivery.
- Injector problems, leading to inefficient combustion.
- Turbocharger issues, such as wastegate malfunctions or boost leaks.
- Excessive exhaust restriction, including clogged catalytic converters or mufflers.
Checking fuel pressure, air intake components, and turbo operation can help pinpoint the cause of power loss.
What causes white smoke from the exhaust on startup?
White smoke is typically caused by unburned fuel, coolant leaks, or excessive condensation. Common reasons include:
- Cold starts, where fuel does not fully combust in lower temperatures.
- Injector issues, causing excess fuel to enter the combustion chamber.
- Coolant leaks into the engine, due to a failing head gasket or cracked cylinder head.
- Low cylinder compression, leading to incomplete combustion.
- Water contamination in fuel, which burns off as white steam.
If white smoke disappears after the engine warms up, it’s likely normal condensation. If it continues, check for coolant loss or injector problems.
How do I clean the fuel injectors on my Cummins engine?
Cleaning fuel injectors improves fuel economy, reduces emissions, and restores power. Follow these steps:
- Use a diesel fuel injector cleaner added to the fuel tank every 5,000 miles.
- Perform an injector flush using a professional-grade injector cleaning kit.
- Remove and clean injectors manually using an ultrasonic cleaner or have them serviced by a professional.
- Inspect injectors for spray pattern issues and replace any that are worn or clogged.
Regular fuel system maintenance prevents injector buildup and ensures efficient fuel atomization.
What is the function of the lift pump in the fuel system?
The lift pump is responsible for delivering fuel from the tank to the injection pump, ensuring consistent fuel pressure. Key functions include:
- Maintaining fuel pressure (14-16 PSI at idle, 20+ PSI under load)
- Preventing air from entering the fuel system, which can cause misfires and hard starts.
- Supplying a steady flow of fuel to the injection pump, ensuring smooth operation.
If the lift pump fails, symptoms include hard starting, fuel starvation, and engine stalling. Regular fuel filter maintenance helps extend the life of the lift pump.
Air Intake and Turbocharger FAQs for Cummins 6B, 6BT, and 6BTA Engines
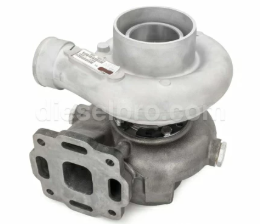
How often should I replace the air filter on my Cummins 6BTA?
The air filter should be replaced every 15,000-30,000 miles or 500 hours, depending on environmental conditions. In dusty, off-road, or marine environments, check the filter every 250 hours and replace it as soon as it appears clogged or damaged.
Signs that your air filter needs immediate replacement include:
- Loss of power and sluggish acceleration
- Increased black smoke from the exhaust
- Higher fuel consumption
- Visible dirt or oil saturation on the air filter
A clogged air filter restricts airflow to the turbocharger, reducing engine efficiency and increasing exhaust temperatures.
What are the signs of a failing turbocharger?
A failing turbocharger can lead to reduced power, increased exhaust smoke, and poor fuel economy. Common symptoms include:
- Excessive black or blue smoke from the exhaust (black = over-fueling, blue = burning oil)
- Loud whining or screeching noise when the turbo spools
- Noticeable loss of power and acceleration
- Increased oil consumption due to leaking turbo seals
- Excessive exhaust temperature (EGT) readings
If you notice these symptoms, inspect the turbo for shaft play, leaks, or excessive carbon buildup.
How do I check for boost leaks in my engine?
Boost leaks cause power loss, turbo lag, and reduced efficiency. To check for leaks:
- Visually inspect all intercooler hoses and clamps for cracks, loose connections, or oil residue.
- Use a boost pressure tester to pressurize the system and listen for hissing sounds.
- Spray soapy water on charge pipes while pressurizing—bubbles indicate leaks.
- Monitor boost pressure with a gauge while driving; a significant drop under load may indicate a leak.
Boost leaks reduce turbo efficiency and can lead to excessive soot buildup in the engine.
What is the recommended turbo boost pressure for a Cummins 6BTA?
Stock turbo boost pressure for a Cummins 6BTA ranges from 18-25 PSI under full load. Modified or high-performance setups may run 30-35 PSI, but exceeding this requires upgraded intercoolers, injectors, and fuel tuning.
Running too much boost without supporting modifications can cause excessive cylinder pressure, leading to head gasket failure or turbo damage.
Can I install a larger turbo on my Cummins 6BT?
Yes, installing a larger turbocharger can increase horsepower and torque, but requires supporting modifications such as:
- Upgraded injectors to supply more fuel
- Higher-flow air intake and exhaust system to improve airflow
- Tuned fuel system and ECM adjustments to optimize performance
- Stronger head studs to handle increased boost pressure
A larger turbo can improve performance but will require additional tuning to avoid excessive exhaust temperatures or engine damage.
What causes turbo lag in a diesel engine?
Turbo lag is the delay between throttle input and turbo boost response. Common causes include:
- Large or improperly sized turbocharger, requiring more time to spool
- Boost leaks, reducing compressor efficiency
- Worn turbo bearings, leading to slower spool times
- Clogged or restrictive exhaust system, delaying exhaust gas flow to the turbine
Reducing turbo lag requires improving airflow, ensuring proper fuel tuning, and using a properly matched turbocharger for your application.
How do I clean my intercooler?
A dirty intercooler can reduce cooling efficiency, leading to higher intake air temperatures and reduced power. To clean it:
- Remove the intercooler and inspect for oil or dirt buildup.
- Flush the inside with a degreaser or brake cleaner, ensuring all oil residue is removed.
- Rinse with warm water and let it dry completely before reinstalling.
- Check for leaks or damaged fins before reinstallation.
Cleaning the intercooler every 50,000 miles or after turbo failure helps maintain efficiency.
What are the symptoms of excessive blow-by?
Blow-by occurs when combustion gases escape past the piston rings into the crankcase. Symptoms include:
- Excessive oil consumption
- White or blue smoke from the crankcase breather
- Oil leaks around gaskets and seals
- Loss of power and increased crankcase pressure
Excessive blow-by may indicate worn piston rings, cylinder wall damage, or a failing PCV system.
How do I prevent dust ingestion in off-road applications?
To protect your engine in dusty environments, follow these steps:
- Use high-quality air filters designed for severe conditions
- Install a pre-filter or snorkel intake to reduce dust intake
- Regularly inspect and replace air filters
- Ensure all intake boots and connections are sealed
Dust ingestion can cause rapid turbocharger and cylinder wear, leading to premature engine failure.
What is the purpose of the aftercooler on a 6BTA engine?
The aftercooler (intercooler) cools compressed air from the turbocharger before it enters the engine. This results in:
- Denser, oxygen-rich air for better combustion efficiency
- Lower exhaust gas temperatures (EGT), reducing the risk of overheating
- Increased power output and fuel efficiency
A functioning aftercooler is critical for turbocharged engines to maintain performance and reliability.
Cylinder Head and Valve Adjustment FAQs for Cummins B Series Engines
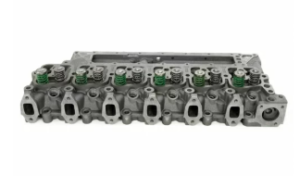
When should I adjust the valves on my Cummins B Series engine?
Valve adjustments should be performed every 150,000 miles or every 5,000 hours.
Signs that valve adjustment is needed:
- Tapping or ticking noises from the valvetrain
- Loss of power or rough idle
- Increased fuel consumption
Neglecting valve adjustments can lead to excessive wear, overheating, and reduced performance.
What are the correct valve clearance settings for my engine?
For most Cummins 6BT and 6BTA engines, the valve clearance settings are:
- Intake: 0.010 inches (0.25mm)
- Exhaust: 0.020 inches (0.50mm)
Always adjust valves when the engine is cold for accurate measurements.
How do I perform a valve adjustment on a Cummins 6BT?
- Rotate the engine to TDC (top dead center) on the compression stroke.
- Check valve clearance with a feeler gauge and adjust using a wrench and screwdriver.
- Tighten the adjustment locknut to factory specs.
- Repeat for all cylinders and double-check clearances.
Valve adjustments should be done by a trained technician to avoid misalignment issues.
What causes valve train noise in Cummins engines?
Common causes include:
- Improper valve clearance (too tight or too loose)
- Worn rocker arms or pushrods
- Low oil pressure, causing poor lubrication
Regular maintenance and proper oil changes can help reduce valve train noise.
Can improper valve adjustment damage my engine?
Yes, incorrect valve adjustments can lead to:
- Poor combustion efficiency and loss of power
- Excessive wear on valve seats and camshaft lobes
- Potential engine overheating due to improper air/fuel mixture
Always follow factory specifications when adjusting valves.
How do I check for a blown head gasket?
Symptoms of a blown head gasket include:
- White smoke from the exhaust (coolant burning in cylinders)
- Overheating and coolant loss
- Milky oil on the dipstick (coolant mixing with oil)
A coolant pressure test or compression test can confirm head gasket failure.
What are the symptoms of a cracked cylinder head?
- Loss of compression
- Coolant or oil leaks
- Excessive smoke from the exhaust
A cracked head requires immediate repair or replacement.
Electrical System FAQs for Cummins 6B, 6BT, and 6BTA Engines
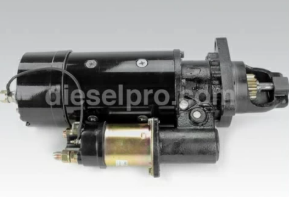
What battery size is recommended for my Cummins B Series engine?
For Cummins B Series engines, the recommended battery size depends on application and climate conditions. A typical setup includes:
- Cold climates: 1,000 CCA (Cold Cranking Amps) or higher for reliable starting.
- Moderate climates: 750-900 CCA is sufficient.
- Marine and industrial applications: Dual battery setups with at least 1,200 CCA total for redundancy.
Using a battery with too low a CCA rating can result in slow cranking, difficult starts, and increased wear on the starter motor. Always choose a deep-cycle AGM or heavy-duty lead-acid battery designed for diesel applications.
Why is my alternator not charging?
A non-charging alternator can cause electrical failures and prevent the battery from maintaining power. Common causes include:
- Loose or corroded battery cables preventing current flow.
- Faulty alternator voltage regulator failing to control charging output.
- Broken alternator belt causing no rotation and loss of charging.
- Blown alternator fuse or wiring harness issues.
- Worn-out alternator brushes or internal failure.
To diagnose, measure battery voltage with the engine running—if it’s below 13.5V, the alternator may not be charging properly.
How do I test my glow plugs?
Glow plugs assist with cold starts in diesel engines. To test them:
- Disconnect the power supply to the glow plugs.
- Use a multimeter set to Ohms (Ω) and place one probe on the glow plug tip and the other on a good ground.
- A healthy glow plug should have a resistance of 0.5 – 2.0 ohms.
- If resistance is too high or the glow plug is open (infinite resistance), it needs replacement.
Bad glow plugs can cause extended cranking times and rough cold starts.
What are the signs of a bad starter motor?
A failing starter can cause intermittent or complete failure to start. Symptoms include:
- A single clicking sound when turning the key (solenoid issue).
- Slow cranking or grinding noises when starting.
- Starter remains engaged after releasing the key.
- No response when turning the key, even with a charged battery.
If tapping the starter lightly with a hammer allows it to start, the motor is failing and should be replaced.
How do I troubleshoot electrical grounding issues?
Poor grounding can cause unreliable electrical performance and sensor malfunctions. Steps to troubleshoot include:
- Inspect battery-to-chassis and engine-to-frame ground connections for corrosion or looseness.
- Use a multimeter to check for resistance between the battery ground terminal and the engine block (should read close to 0 ohms).
- Clean grounding points and apply dielectric grease to prevent future corrosion.
- Check for voltage drops between key electrical components (more than 0.2V indicates a bad ground).
Poor grounds often cause intermittent electrical failures and starter engagement issues.
Why does my engine have trouble starting in cold weather?
Cold-starting issues can be caused by:
- Weak or faulty glow plugs failing to heat the cylinders.
- Low CCA battery not providing enough power to crank the engine.
- Thickened engine oil reducing lubrication (switch to 5W-40 synthetic for cold climates).
- Weak starter motor drawing excessive power.
- Fuel gelling in extreme cold (use anti-gel additives in winter).
Pre-heating the engine block with a block heater helps in extremely cold temperatures.
How do I replace the engine wiring harness?
Replacing the wiring harness involves:
- Disconnecting the battery to prevent shorts.
- Labeling and disconnecting all harness connectors.
- Removing retaining clips and old wiring.
- Installing the new harness and securing all connections.
- Reconnecting the battery and testing electrical components.
A damaged harness can cause misfires, sensor failures, and erratic engine behavior.
What causes a sudden loss of power while driving?
A sudden power loss can indicate:
- Failing alternator or battery, causing voltage drops.
- Bad fuel pump or clogged fuel filter reducing fuel delivery.
- Boost leaks in the intake system causing improper air-to-fuel ratios.
- Faulty sensors (crankshaft position sensor, MAP sensor) disrupting engine operation.
Using a diagnostic scanner to check for fault codes is the best way to pinpoint electrical issues.
Can I install a higher-output alternator on my engine?
Yes, upgrading to a higher-output alternator (160A-220A) is beneficial if running high-power accessories (winches, auxiliary lights, or sound systems).
Ensure upgraded wiring can handle higher amperage to prevent overheating and electrical fires.
What is the best way to protect my electrical system from corrosion?
- Use dielectric grease on all electrical connectors.
- Apply anti-corrosion battery terminal spray.
- Check and clean ground connections regularly.
- Use marine-grade heat-shrink connectors for water-exposed wiring.
Regular inspections help prevent major electrical failures.
Exhaust System and Emissions Control FAQs for Cummins 6B, 6BT, and 6BTA Engines
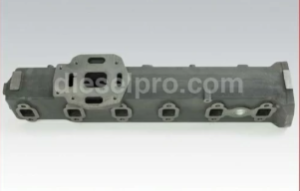
Why is my Cummins 6BT emitting black smoke?
Black smoke is caused by excessive fuel delivery or insufficient air intake. Common causes include:
- Dirty or clogged air filter
- Boost leaks or failing turbocharger
- Over-fueling from bad injectors or injection pump issues
Black smoke means inefficient combustion, which reduces power and fuel efficiency.
What causes excessive white smoke at idle?
White smoke usually indicates unburned fuel or coolant leaks into the combustion chamber. Possible causes:
- Cold starts with incomplete combustion
- Leaking head gasket allowing coolant into cylinders
- Worn injectors or incorrect timing
If the smoke persists, check for coolant loss and inspect injectors.
How do I diagnose excessive blue smoke from the exhaust?
Blue smoke is a sign of oil burning in the combustion chamber. Causes include:
- Worn piston rings or valve seals allowing oil past.
- Failing turbocharger leaking oil into the intake.
- Overfilled engine oil causing excessive crankcase pressure.
Compression tests can help confirm internal engine wear.
What are the signs of a clogged diesel particulate filter (DPF)?
A clogged DPF can cause:
- Loss of power and increased fuel consumption
- Excessive exhaust backpressure, triggering warning lights
- Frequent forced regeneration cycles
If clogging is severe, DPF cleaning or replacement is required.
How can I improve exhaust flow on my Cummins engine?
- Upgrade to a larger-diameter exhaust system
- Install a high-flow catalytic converter or muffler
- Ensure no exhaust leaks affecting backpressure
Better exhaust flow reduces exhaust gas temperatures and improves performance.
Can I remove the EGR system on my engine?
While removing the Exhaust Gas Recirculation (EGR) system may improve power, it may be illegal in some areasand affect emissions compliance.
Check local laws before removing emissions equipment.
How do I fix an exhaust leak on my Cummins B Series engine?
- Locate the leak using a smoke test or by feeling for escaping gases.
- Tighten exhaust manifold bolts to factory torque specs.
- Replace cracked gaskets and rusted pipes.
Exhaust leaks can cause performance loss and excess noise.
Common Problems and Troubleshooting FAQs for Cummins 6B, 6BT, and 6BTA Engines
Why is my Cummins 6BT hard to start?
A hard-starting Cummins 6BT can be caused by multiple factors, including:
- Weak battery – If the battery does not provide enough cranking amps (CCA), the engine may struggle to turn over.
- Faulty fuel system – A clogged fuel filter, air in the fuel lines, or a weak lift pump can prevent proper fuel delivery.
- Glow plug or grid heater failure – In cold weather, these components help start the engine. If they are faulty, cold starts become difficult.
- Low compression – Worn piston rings, valves, or cylinder walls can reduce compression, making starting difficult.
Check battery voltage, inspect the fuel system for leaks, and test glow plugs/grid heaters to diagnose the issue.
What causes rough idling in Cummins B Series engines?
Rough idling is typically caused by:
- Dirty or failing injectors, leading to poor fuel atomization.
- Fuel contamination, such as water or debris in the fuel system.
- Air leaks in the intake or fuel system, causing an unbalanced air-fuel mixture.
- EGR valve or sensor malfunctions (if equipped), affecting combustion.
A fuel system inspection and injector cleaning can often resolve rough idling.
How do I diagnose a misfire in my engine?
A misfire in a Cummins engine can be caused by fuel, air, or compression issues. To diagnose:
- Check for active fault codes using a diagnostic scanner.
- Perform a fuel pressure test to ensure the injection system is delivering adequate fuel.
- Inspect injectors for leaks or poor spray patterns.
- Perform a compression test to rule out cylinder wear or valve issues.
- Check for intake or exhaust restrictions affecting airflow.
Misfires should be diagnosed quickly to prevent long-term engine damage.
What causes excessive vibration in a diesel engine?
Excessive vibration can be caused by:
- Unbalanced injectors, leading to inconsistent combustion.
- Worn engine mounts, allowing excessive movement.
- Harmonic balancer failure, leading to crankshaft imbalance.
- Improper valve timing or injector timing, causing uneven power strokes.
Checking injector balance rates, inspecting engine mounts, and ensuring proper timing can help reduce excessive vibration.
How do I fix a leaking rear main seal?
A rear main seal leak is a common issue in high-mileage engines. To fix it:
- Confirm the leak by inspecting the bell housing for excessive oil.
- Remove the transmission and flywheel to access the rear main seal.
- Use a rear main seal installer tool to properly install a new seal without damaging it.
- Inspect the crankshaft for scoring—if present, a speed sleeve may be required.
- Reassemble and check for leaks after a short test run.
A leaking rear main seal should be addressed promptly to prevent excessive oil loss.
Why is my engine experiencing excessive blow-by?
Excessive blow-by occurs when combustion gases leak past the piston rings into the crankcase. Causes include:
- Worn piston rings, leading to low compression.
- Glazed cylinder walls, reducing ring sealing.
- Clogged crankcase ventilation system, increasing pressure buildup.
A crankcase pressure test or compression test can confirm excessive blow-by. If severe, a rebuild with new rings and honing may be required.
What causes a knocking sound in a Cummins engine?
A knocking sound is often due to:
- Fuel knock, from poor injector spray patterns or incorrect timing.
- Rod bearing wear, leading to excessive play in the crankshaft.
- Piston slap, caused by excessive cylinder wall clearance.
Using a mechanic’s stethoscope can help pinpoint the source of the knock. If internal components are worn, an engine rebuild may be necessary.
How do I test my injectors for leaks?
To test for leaking injectors:
- Perform a leak-down test by pressurizing the fuel system and checking for pressure loss.
- Visually inspect the injector nozzles for wetness after shutting down the engine.
- Use a scan tool to monitor injector return rates—excessive return flow may indicate an internal leak.
- Remove and bench-test injectors, if necessary.
Leaking injectors can cause hard starts, rough idling, and excessive fuel consumption.
Why does my engine shut off randomly?
An engine that shuts off randomly may have:
- A failing fuel pump, leading to fuel starvation.
- Electrical wiring issues, including loose grounds or bad ignition connections.
- A malfunctioning crankshaft position sensor, causing an engine shutdown.
Using a scan tool to check for error codes can help pinpoint the issue.
What are the symptoms of a failing crankshaft position sensor?
The crankshaft position sensor (CKP) monitors engine speed and timing. Symptoms of failure include:
- Intermittent stalling or failure to start
- Loss of RPM signal on the tachometer
- Hard starting, misfires, or rough running
- Check Engine Light with crankshaft sensor-related codes
Replacing a failing CKP sensor can restore normal engine operation.
Major Overhaul and Rebuild FAQs for Cummins 6BTA Engines
When should I consider rebuilding my Cummins 6BTA engine?
A rebuild is needed if the engine has:
- Excessive blow-by and high oil consumption.
- Loss of compression in multiple cylinders.
- Low oil pressure despite using the correct viscosity oil.
- Severe knocking or bottom-end wear.
Engines with 15,000-20,000 hours may require an overhaul.
What parts should be replaced during an engine rebuild?
A complete engine rebuild should include:
- New piston rings and cylinder honing
- Main and rod bearings
- New cylinder head gasket and seals
- Oil pump and timing components
- Inspecting or replacing camshaft and lifters
Replacing these parts ensures reliability and longevity post-rebuild.
How do I know if my pistons need replacement?
Replace pistons if they show:
- Excessive wear or scoring on skirts.
- Cracks or melted tops from overheating.
- Excessive carbon buildup or ring land damage.
A borescope inspection and compression test can help assess piston health.
What is the difference between an in-frame and out-of-frame rebuild?
- In-frame rebuild: Done with the engine in the vehicle, replacing major components like rings, bearings, and head gaskets.
- Out-of-frame rebuild: A full disassembly requiring the engine to be removed, including replacing the crankshaft, camshaft, and block machining.
Out-of-frame rebuilds are more extensive but result in a like-new engine.
How do I properly break in a rebuilt Cummins B Series engine?
- Run at varying RPMs for the first 500 miles.
- Avoid excessive idling or full-throttle acceleration.
- Use break-in oil for the first 500-1,000 miles.
Proper break-in ensures piston rings seat correctly and prevents glazing.
What is the correct torque spec for main bearings and rod bearings?
- Main bearing cap bolts: 95-110 ft-lbs
- Rod bearing bolts: 50-55 ft-lbs
Always follow Cummins’ factory torque specs to avoid premature bearing failure.
How do I test oil pressure after an engine rebuild?
Use an oil pressure gauge and verify readings:
- Idle: 15-25 PSI
- Full throttle: 45-65 PSI
Low oil pressure may indicate worn bearings or an improperly installed oil pump.
Parts Catalog for Cummins 4B Marine Engine
Parts Catalog for Cummins 4BT Marine Engine
Parts Catalog for Cummins 4BTA Marine Engine
Parts Catalog for Cummins 6B Marine Engine
Parts Catalog for Cummins 6BT Marine Engine
Parts Catalog for Cummins 6BTA Marine Engine