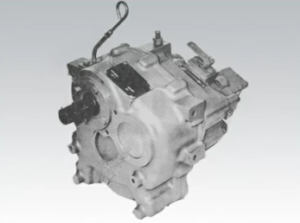
The Twin Disc MG502 Marine Gear is a vital component in marine propulsion systems. Once disassembly, maintenance, and reassembly are complete, thorough final testing and operational checks are essential to ensure optimal performance, safety, and longevity. Skipping or rushing this critical phase can result in mechanical failures, operational inefficiencies, and costly downtime.
This guide provides a comprehensive, 5000-word overview of the final testing process for the MG502, covering initial testing procedures, load testing and calibration, noise and vibration checks, and a post-service inspection checklist. These procedures ensure that the gearbox is fully functional, safe, and ready for reliable operation.
Initial Testing Procedures for Twin Disc MG502 Marine Gear
Initial testing serves as the first phase in verifying the success of the reassembly and ensuring the integrity of all components. This phase focuses on assessing the system’s readiness before it undergoes more intensive load testing.
Parts Catalog for Twin Disc MG502 Marine Transmissions
Rebuilt Twin Disc MG502 Marine Transmissions
Bearings For Twin Disc MG502 Marine Transmissions
Plate Kit For Twin Disc MG502 Marine Transmission
Gasket Kits For Twin Disc MG502 Marine Transmission
1. Visual Inspection Before Testing
Before starting the MG502, a comprehensive visual inspection should be conducted to ensure that all components are properly assembled and secured.
- Check for Loose Components: Ensure all bolts, nuts, and fasteners are tightened to the correct torque specifications.
- Inspect for Leaks: Examine seals, gaskets, and hydraulic lines for any signs of oil or fluid leaks.
- Alignment Confirmation: Verify that the input and output shafts are properly aligned and free from any visible obstructions.
- Wiring and Connections: Ensure that all electrical connections, if applicable, are secure and properly insulated.
2. Fluid Level Inspection
The gearbox and hydraulic system must have the correct fluid levels to prevent damage during operation.
- Gear Oil Level: Check that the gearbox oil is filled to the recommended level and that the oil appears clean, free of debris or discoloration.
- Hydraulic Fluid Level: Verify that hydraulic reservoirs are topped off with the correct fluid and that there are no signs of contamination.
- Cooling System Check: Ensure the oil cooler and associated lines are clean and properly connected.
3. Manual Rotation Test
Before running the gear system under power, perform a manual rotation test to ensure the internal components are functioning smoothly.
- Rotate Shafts Manually: Turn the input and output shafts manually, feeling for any resistance, grinding, or abnormal movements.
- Check for Smooth Gear Engagement: Shift gears manually (if possible) to ensure smooth transitions between neutral, forward, and reverse.
4. Initial Power Test
Once manual checks are completed, it’s time to conduct the initial powered test.
- Run the Gearbox at Low Speed: Engage the engine and run the gearbox at the lowest possible RPM.
- Monitor Temperature and Pressure: Use gauges to monitor the temperature and hydraulic pressure levels, ensuring they fall within the manufacturer’s specifications.
- Check for Leaks Again: Inspect seals, hydraulic lines, and gaskets for any fluid leaks during the initial run.
- Observe for Abnormalities: Watch for any signs of excessive vibration, noise, or irregular clutch engagement.
5. System Shut Down and Inspection
After the initial test, perform a shutdown and a secondary inspection.
- Re-check Fluid Levels: Some fluids may settle or redistribute during initial testing. Top off if necessary.
- Inspect for Leaks and Wear: Look for new leaks or wear that may have developed during the initial test.
- Check Fasteners: Confirm that all fasteners remain secure and have not loosened due to vibration.
Load Testing and Calibration for Twin Disc MG502 Marine Gear
Load testing ensures the MG502 operates correctly under realistic working conditions, while calibration ensures all settings meet operational standards. This phase is critical for verifying the gearbox’s ability to handle real-world stresses.
1. Preparing for Load Testing
- Safety Check: Confirm that all safety measures are in place, including emergency shut-off systems.
- Controlled Environment: Conduct the test in a controlled environment where the system can be safely monitored.
- Monitoring Tools: Set up pressure gauges, temperature sensors, and vibration monitors to capture real-time data.
2. Conducting Load Tests
Start by applying incremental loads to the gearbox and closely monitor its performance.
- Initial Load Application: Apply a light load and run the gearbox at a low RPM. Monitor how it handles the stress.
- Progressive Load Increase: Gradually increase the load in stages, observing temperature, pressure, and vibration levels at each stage.
- Maximum Load Test: Run the gearbox at full operational load for a sustained period, ensuring that it handles the stress without overheating or mechanical failure.
3. Key Calibration Checks
Calibration ensures that the gearbox operates within its designed parameters.
- Hydraulic Pressure Calibration: Verify that hydraulic pressures meet the recommended levels for clutch engagement and gear shifting.
- Temperature Calibration: Ensure oil temperatures stay within safe operating ranges (typically between 160°F to 200°F).
- Engagement Timing: Test clutch engagement timing to ensure smooth and prompt transitions between gear settings.
- Speed Calibration: Confirm that the output shaft speed corresponds accurately to the input shaft RPM and gear ratios.
4. Observing Operational Behaviors
During load testing, closely observe the following behaviors:
- Clutch Engagement: Watch for delayed or harsh engagement. This could indicate pressure issues.
- Gear Shifting: Ensure gear changes are smooth and free from grinding or resistance.
- Vibration Levels: Excessive vibration under load could indicate misalignment or bearing issues.
Noise and Vibration Checks for Twin Disc MG502 Marine Gear
Noise and vibration analysis are crucial for detecting early signs of mechanical issues that visual inspections may miss.
1. Noise Detection Procedures
- Listening Test: Use sensitive audio equipment to detect abnormal noises, such as grinding, whining, or knocking.
- Isolate Noise Sources: Shut down adjacent systems to isolate and identify noise specifically originating from the MG502.
- Compare to Baseline: Compare detected noises against standard operating sounds. Any deviation should be noted and investigated.
2. Vibration Analysis Procedures
Use Vibration Sensors: Attach vibration sensors to key points on the gearbox, such as bearings, housings, and shafts.
- Measure Vibration Frequencies: Record vibration frequencies and amplitudes.
- Interpret Data: Compare readings to manufacturer specifications. High or irregular frequencies can indicate misalignment, wear, or imbalance.
3. Common Issues Identified by Noise and Vibration Checks
- Grinding Noise: Often indicates gear misalignment or damage.
- Whining Noise: Could suggest bearing wear or low lubrication levels.
- High Vibration: Misaligned shafts or improperly seated bearings.
- Low-Frequency Vibration: May indicate an imbalance in rotating components.
Post-Service Inspection Checklist for Twin Disc MG502 Marine Gear
After all testing is complete, a detailed post-service inspection ensures long-term operational integrity and readiness for deployment.
1. Final Visual Inspection
- Check for Residual Leaks: Ensure no oil, hydraulic fluid, or coolant leaks are present.
- Confirm Fastener Tightness: Recheck torque on critical fasteners.
- Surface Condition Check: Look for signs of overheating, corrosion, or wear.
2. Fluid and Lubrication Check
- Verify Fluid Levels: Ensure all fluid levels are within recommended parameters.
- Check for Contamination: Reassess fluid quality for signs of contamination or degradation.
- Replace if Necessary: If fluids show signs of contamination, flush and replace accordingly.
3. Alignment Verification
- Shaft Alignment: Recheck that shafts are aligned within manufacturer tolerances.
- Gear Alignment: Confirm that gear backlash and engagement remain consistent.
4. System Functionality Test
- Final Operational Run: Conduct one last operational test, ensuring smooth gear engagement, consistent hydraulic pressure, and proper temperature regulation.
- Emergency System Test: Check that all emergency shutdown systems are functional.
5. Documentation and Reporting
- Record Findings: Document all inspection results, measurements, and observations.
- Maintenance Log Update: Record the service date, procedures performed, and replacement parts used.
- Report Anomalies: Highlight any issues that may require future monitoring or additional maintenance.
Conclusion
Final testing and operational checks are essential for ensuring the reliability, safety, and optimal performance of the Twin Disc MG502 Marine Gear. This detailed guide outlined:
- Initial Testing Procedures to verify component integrity after assembly.
- Load Testing and Calibration to confirm the gearbox’s performance under realistic working conditions.
- Noise and Vibration Checks to detect hidden mechanical issues.
- A Post-Service Inspection Checklist to ensure the system is fully operational and safe.
By following these comprehensive steps, technicians and marine operators can confidently deploy the MG502, knowing that it has been rigorously tested and prepared for reliable service.
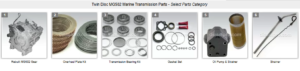
Rebuilt Twin Disc MG502 Marine Transmissions
Bearings For Twin Disc MG502 Marine Transmissions
Plate Kit For Twin Disc MG502 Marine Transmission
Gasket Kits For Twin Disc MG502 Marine Transmission
Videos About Twin Disc Transmissions
6 Reasons Your Twin Disc Transmission Has Low Oil Pressure
7 Reasons Your Twin Disc Transmission Is Overheating
3 Reasons Your Clutch Plates in Your Twin Disc Transmission Are Making Excessive Noise
Bull Gear On A Twin Disc Transmission
Rebuilt Twin Disc Transmissions