
The fuel system in Cummins ISB and QSB engines plays a critical role in ensuring optimal engine performance. It is responsible for delivering the right amount of fuel, at the correct pressure, to the combustion chamber for efficient power generation. Any issues within the fuel system can lead to problems such as hard starting, reduced power, poor fuel economy, excessive emissions, and even engine failure. This guide will cover key areas of fuel system troubleshooting, including diagnosing fuel pressure issues, identifying clogged fuel filters, and addressing injector problems and their solutions.
Parts Catalog Main Page for Cummins ISB Marine Engine
Fuel Pump & Related Components for Cummins ISB 4.5 Engine
Fuel Pump & Related Components for Cummins ISB 5.9 Engine
Fuel Pump & Related Components for Cummins ISB 6.7 Engine
Injector & Related Components for Cummins ISB 4.5 Engine
Injector & Fuel Pump Related Components for Cummins ISB 5.9 Engine
Injector & Related Components for Cummins ISB 6.7 Engine
Parts Catalog Main page for Cummins QSB Marine Engine
Fuel Pump & & Related Components for Cummins QSB 4.5 Engine
Fuel Pump & & Related Components for Cummins QSB 5.9 Engine
Fuel Pump & & Related Components for Cummins QSB 6.7 Engine
Fuel Pump & & Related Components for Cummins QSB 7.0 Engine
Injector & Fuel Pump Related Components for Cummins QSB 4.5 Engine
Injector & Fuel Pump Related Components for Cummins QSB 5.9 Engine
Injector & Fuel Pump Related Components for Cummins QSB 6.7 Engine
Injector & Fuel Pump Related Components for Cummins QSB 7.0 Engine
1. Diagnosing Fuel Pressure Issues

Why Fuel Pressure Matters
Proper fuel pressure is essential for the efficient operation of diesel engines. The Cummins ISB and QSB engines use high-pressure common rail (HPCR) fuel systems, which rely on precise fuel pressure control for effective combustion. Inadequate or inconsistent fuel pressure can cause starting difficulties, engine misfires, power loss, and excessive exhaust emissions.
Common Causes of Fuel Pressure Issues
Understanding the root causes of fuel pressure problems is the first step in effective troubleshooting. Some common causes include:
- Faulty Fuel Pump: The high-pressure fuel pump or lift pump may fail to deliver sufficient pressure.
- Clogged Fuel Filters: Restrictions in the fuel flow due to clogged filters reduce pressure downstream.
- Air in the Fuel System: Air pockets disrupt fuel flow and cause inconsistent pressure.
- Leaking Fuel Lines: Cracks or loose fittings in the fuel lines can lead to pressure drops.
- Faulty Pressure Relief Valve: A malfunctioning valve can cause the system to lose pressure prematurely.
- Defective Fuel Pressure Sensor: Incorrect readings can cause improper fuel delivery and pressure fluctuations.
Symptoms of Fuel Pressure Problems
Some of the most common symptoms indicating fuel pressure issues include:
- Hard Starting or No-Start Condition: Insufficient fuel pressure prevents proper combustion.
- Rough Idling: Irregular fuel delivery causes the engine to run unevenly at idle.
- Loss of Power: The engine may hesitate or struggle under load due to poor fuel delivery.
- Stalling: A sudden drop in fuel pressure can cause the engine to stall, especially when idling.
- Excessive Smoke: Incomplete combustion from inconsistent fuel delivery may result in black or white smoke from the exhaust.
Step-by-Step Fuel Pressure Troubleshooting Process
Step 1: Visual Inspection
- Check for Leaks: Inspect fuel lines, fittings, and connections for signs of leakage or loose connections.
- Examine Fuel Lines: Look for cracks, abrasions, or kinks that could restrict fuel flow.
- Inspect Fuel Tank: Ensure the fuel tank is not empty, contaminated, or suffering from clogged pickup screens.
Step 2: Check for Diagnostic Trouble Codes (DTCs)
- Use a diagnostic scanner, such as Cummins INSITE, to check for active or stored fault codes related to the fuel system. Codes may point to issues with the fuel pressure sensor, injector performance, or fuel pump functionality.
Step 3: Test Fuel Pressure
- Attach a Fuel Pressure Gauge
- Connect the gauge to the fuel rail using an adapter if necessary.
- Crank the engine and observe the pressure reading.
- Compare Readings:
- Refer to the Cummins service manual for the specific fuel pressure specifications for your engine model.
- Low Pressure: Indicates possible issues with the fuel pump, clogged filters, or leaks.
- High Pressure: May suggest a faulty pressure relief valve or a blocked return line.
- Perform a Key-On Test:
- Turn the ignition key to the “ON” position without starting the engine.
- This primes the fuel system; observe if the pressure builds up as expected.
Step 4: Check the Fuel Pump
- Lift Pump Test: Ensure the lift pump is supplying fuel to the high-pressure pump.
- High-Pressure Pump Test: Verify that the high-pressure pump delivers the necessary pressure under load conditions.
Fuel Pressure Issue Solutions
- Replace Faulty Components: If the pump, pressure regulator, or sensor is defective, replace it with OEM or high-quality aftermarket parts.
- Repair Leaks: Tighten or replace leaking fuel lines and fittings.
- Bleed the System: Remove air from the fuel system using the manual priming pump or follow the manufacturer’s bleeding procedure.
- Clean or Replace Filters: Ensure fuel filters are clean to maintain optimal pressure.
Fuel Pump & Related Components for Cummins ISB 4.5 Engine
Fuel Pump & Related Components for Cummins ISB 5.9 Engine
Fuel Pump & Related Components for Cummins ISB 6.7 Engine
Fuel Pump & & Related Components for Cummins QSB 4.5 Engine
Fuel Pump & & Related Components for Cummins QSB 5.9 Engine
Fuel Pump & & Related Components for Cummins QSB 6.7 Engine
Fuel Pump & & Related Components for Cummins QSB 7.0 Engine
2. Identifying Clogged Fuel Filters
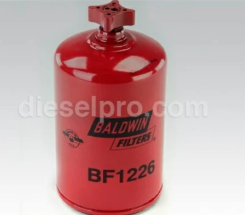
The Importance of Fuel Filters
Fuel filters play a vital role in protecting the engine’s fuel system components by removing contaminants, debris, and water from the fuel before it reaches the injectors. Cummins ISB and QSB engines rely on primary and secondary fuel filters to ensure clean fuel delivery. Over time, these filters can become clogged, leading to performance issues.
Causes of Clogged Fuel Filters
- Poor Fuel Quality: Contaminated diesel with dirt, algae, or water accelerates filter clogging.
- Long Service Intervals: Delaying filter replacement beyond recommended intervals increases the risk of clogging.
- Debris in the Fuel Tank: Rust or sediment from the fuel tank can accumulate in the filter.
- Cold Weather Gel Formation: In cold climates, diesel can gel, restricting fuel flow through the filter.
Symptoms of a Clogged Fuel Filter
Recognizing the signs of a clogged fuel filter can help prevent more severe engine damage:
- Hard Starting: Restricted fuel flow makes it difficult to achieve proper combustion.
- Poor Acceleration: The engine struggles to get enough fuel under load, causing sluggish performance.
- Rough Idling: Inconsistent fuel delivery leads to engine misfires and vibration.
- Engine Stalling: The engine may stall unexpectedly, especially during acceleration or uphill driving.
- Unusual Engine Noise: A whining sound from the fuel pump may indicate it’s working harder to push fuel through a clogged filter.
How to Identify and Troubleshoot Clogged Fuel Filters
Step 1: Visual Inspection
- Primary Fuel Filter: If equipped with a clear housing, inspect for visible dirt, discoloration, or water contamination.
- Fuel Filter Indicator: Some Cummins engines have a dashboard indicator for fuel filter restrictions.
Step 2: Fuel Pressure Test
- Install a pressure gauge before and after the fuel filter:
- High Pressure Drop: Indicates a clogged filter restricting fuel flow.
- Normal Pressure: Suggests the filter is not the issue.
Step 3: Drain the Filter (If Applicable)
- Drain a small amount of fuel from the filter into a clear container to check for contaminants like water, rust, or debris.
Step 4: Remove and Inspect the Filter
- Carefully remove the fuel filter and inspect it for excessive dirt buildup or damage.
Solutions for Clogged Fuel Filters
- Replace the Filter: Always use Cummins-approved filters or high-quality aftermarket alternatives.
- Check for Contamination: If the filter is clogged with debris, inspect the fuel tank and lines for contamination sources.
- Bleed the Fuel System: After replacing the filter, bleed the system to remove air pockets that may have entered during maintenance.
- Regular Maintenance: Follow Cummins’ recommended intervals for filter replacement to prevent future issues.
Fuel Filter & Related Components for Cummins ISB 4.5 Engine
Fuel Filter & Related Components for Cummins ISB 5.9 Engine
Fuel Filter & Related Components for Cummins ISB 6.7 Engine
Fuel Filter & Related Components for Cummins QSB 4.5 Engine
Fuel Filter & Related Components for Cummins QSB 5.9 Engine
Fuel Filter & Related Components for Cummins QSB 6.7 Engine
Fuel Filter & Related Components for Cummins QSB 7.0 Engine
3. Injector Problems and Solutions
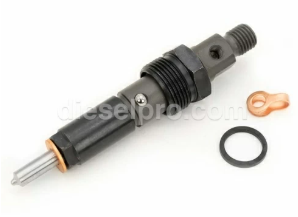
Role of Fuel Injectors in Engine Performance
Fuel injectors are responsible for delivering precise amounts of fuel into the combustion chamber at high pressure. In Cummins ISB and QSB engines, the common rail fuel system operates injectors electronically, allowing for improved fuel atomization, efficiency, and emissions control. When injectors fail, it can significantly impact engine performance.
Common Injector Problems
A. Clogged or Dirty Injectors
- Cause: Build-up of carbon deposits, poor-quality fuel, or infrequent maintenance.
- Symptoms: Rough idling, misfires, poor fuel economy, and white smoke from unburned fuel.
B. Leaking Injectors
- Cause: Worn seals, cracked injector bodies, or improper installation.
- Symptoms: Fuel smell, black smoke, hard starting, and decreased fuel efficiency.
C. Faulty Injector Solenoids
- Cause: Electrical failures in the solenoid that controls fuel flow.
- Symptoms: Misfires, loss of power, and diagnostic trouble codes (DTCs) related to injector performance.
D. Incorrect Injector Timing
- Cause: ECM calibration errors or mechanical timing issues.
- Symptoms: Knocking noises, rough engine operation, and increased emissions.
Symptoms of Fuel Injector Issues
- Rough Engine Idle: Uneven fuel delivery causes irregular combustion.
- Loss of Power: The engine struggles to maintain performance under load.
- Excessive Smoke: White smoke from unburned fuel or black smoke from over-fueling.
- Poor Fuel Economy: Leaking or malfunctioning injectors reduce efficiency.
- Engine Knock: Faulty injectors can cause abnormal combustion noises.
How to Diagnose Injector Problems
Step 1: Check for Diagnostic Trouble Codes (DTCs)
- Use a diagnostic scanner to retrieve fault codes related to injector performance, such as cylinder misfire codes or fuel trim errors.
Step 2: Perform a Cylinder Balance Test
- Measures the contribution of each cylinder to engine power.
- An underperforming cylinder may indicate an injector issue.
Step 3: Conduct an Injector Leak Test
- Monitors fuel pressure drop to identify internal injector leaks.
Step 4: Inspect Electrical Connections
- Check the wiring harness and injector connectors for corrosion, damage, or loose connections.
Injector & Related Components for Cummins ISB 4.5 Engine
Injector & Fuel Pump Related Components for Cummins ISB 5.9 Engine
Injector & Related Components for Cummins ISB 6.7 Engine
Injector & Fuel Pump Related Components for Cummins QSB 4.5 Engine
Injector & Fuel Pump Related Components for Cummins QSB 5.9 Engine
Injector & Fuel Pump Related Components for Cummins QSB 6.7 Engine
Injector & Fuel Pump Related Components for Cummins QSB 7.0 Engine
Solutions for Injector Problems
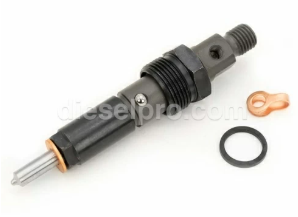
A. Cleaning Injectors
- Use fuel additives designed to clean injectors and improve spray patterns.
- For severe clogging, ultrasonic cleaning may be necessary.
B. Replacing Faulty Injectors
- If injectors are beyond cleaning, replacement is the best option.
- Always replace injectors in matched sets to maintain balance across cylinders.
C. Addressing Leaks
- Replace worn O-rings and seals to stop leaks.
- Ensure injectors are properly torqued to prevent installation-related leaks.
D. ECM Calibration
- Reprogram the ECM if injector timing issues are due to software errors.
Injector Maintenance Tips
- Use High-Quality Fuel: Prevents deposit buildup and prolongs injector life.
- Regular Fuel Filter Changes: Protects injectors from contaminants.
- Add Fuel Stabilizers: Especially in marine or seasonal equipment to prevent gelling and deposits.
Conclusion
Proper maintenance and timely troubleshooting of the fuel system are crucial for keeping Cummins ISB and QSB engines running smoothly. By understanding the causes and symptoms of fuel pressure issues, clogged filters, and injector problems, operators and technicians can diagnose and resolve problems efficiently. Regular inspections, using high-quality fuel, and adhering to Cummins’ maintenance schedules will minimize downtime, enhance performance, and extend the engine’s lifespan.
Parts Catalog Main Page for Cummins ISB Marine Engine
Fuel Pump & Related Components for Cummins ISB 4.5 Engine
Fuel Pump & Related Components for Cummins ISB 5.9 Engine
Fuel Pump & Related Components for Cummins ISB 6.7 Engine
Injector & Related Components for Cummins ISB 4.5 Engine
Injector & Fuel Pump Related Components for Cummins ISB 5.9 Engine
Injector & Related Components for Cummins ISB 6.7 Engine
Parts Catalog Main page for Cummins QSB Marine Engine
Fuel Pump & & Related Components for Cummins QSB 4.5 Engine
Fuel Pump & & Related Components for Cummins QSB 5.9 Engine
Fuel Pump & & Related Components for Cummins QSB 6.7 Engine
Fuel Pump & & Related Components for Cummins QSB 7.0 Engine
Injector & Fuel Pump Related Components for Cummins QSB 4.5 Engine
Injector & Fuel Pump Related Components for Cummins QSB 5.9 Engine
Injector & Fuel Pump Related Components for Cummins QSB 6.7 Engine
Injector & Fuel Pump Related Components for Cummins QSB 7.0 Engine