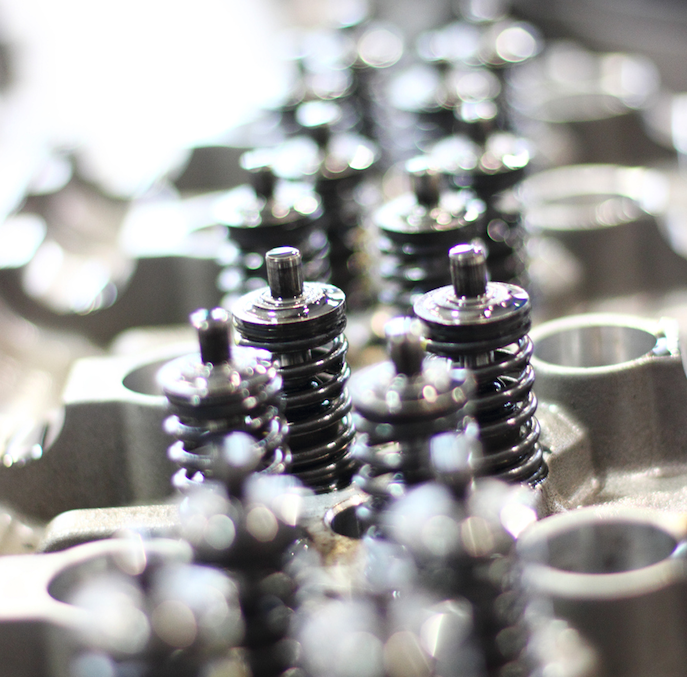
How The Cummins Valve Train Works
The valve train is a critical component of any internal combustion engine, and the Cummins valve train is no exception. It is responsible for controlling the flow of air and fuel into the engine and the exhaust gasses out of the engine. The valve train also ensures that the engine operates smoothly and efficiently, with maximum power output and minimum emissions.
The Cummins valve train is a complex system that consists of several components working together to control the valves. These components include the camshaft, lifters, pushrods, rocker arms, and valves.

The camshaft is a rotating shaft that controls the opening and closing of the valves. It is driven by the engine’s crankshaft through a timing belt or chain. The camshaft is designed with lobes that push against the lifters, which are cylindrical components that ride on the camshaft. The camshaft’s shape determines the timing and duration of the valve opening and closing.
The lifters are responsible for transferring the motion of the camshaft to the pushrods. They ride on the camshaft’s lobes and are designed to move up and down as the camshaft rotates. The lifters are available in two types: hydraulic and solid. Hydraulic lifters use oil pressure to adjust the valve clearance automatically, while solid lifters require periodic manual adjustment.
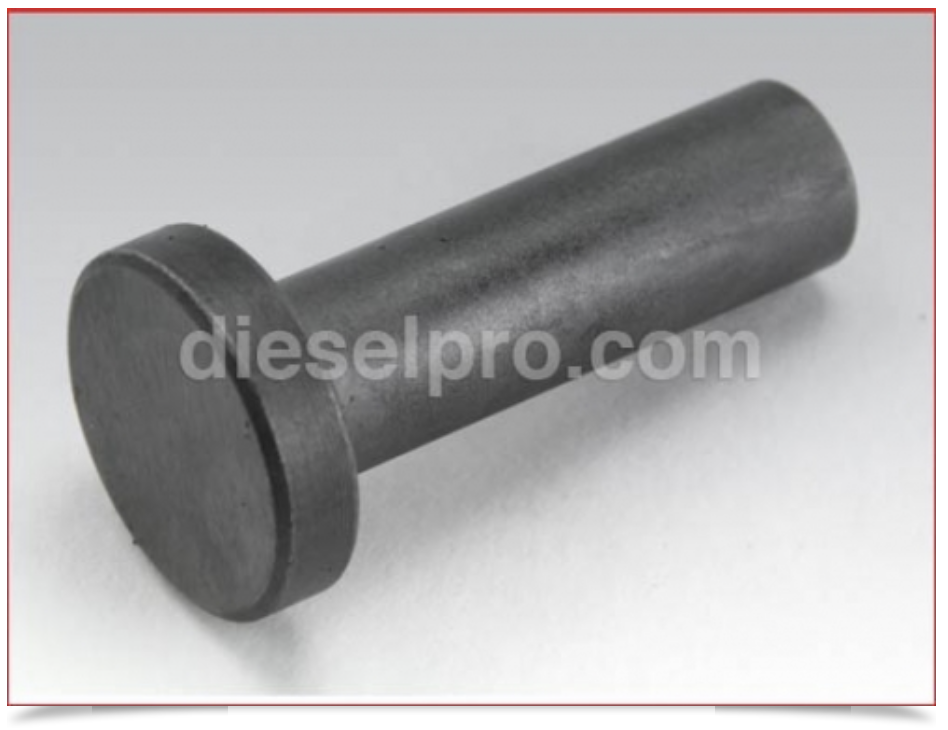
The pushrods are long, slender rods that transfer the motion from the lifters to the rocker arms. They are typically made of steel or chrome-moly and are designed to withstand the high stress and temperature of the engine. Pushrods come in different lengths and diameters, depending on the engine’s configuration and application.
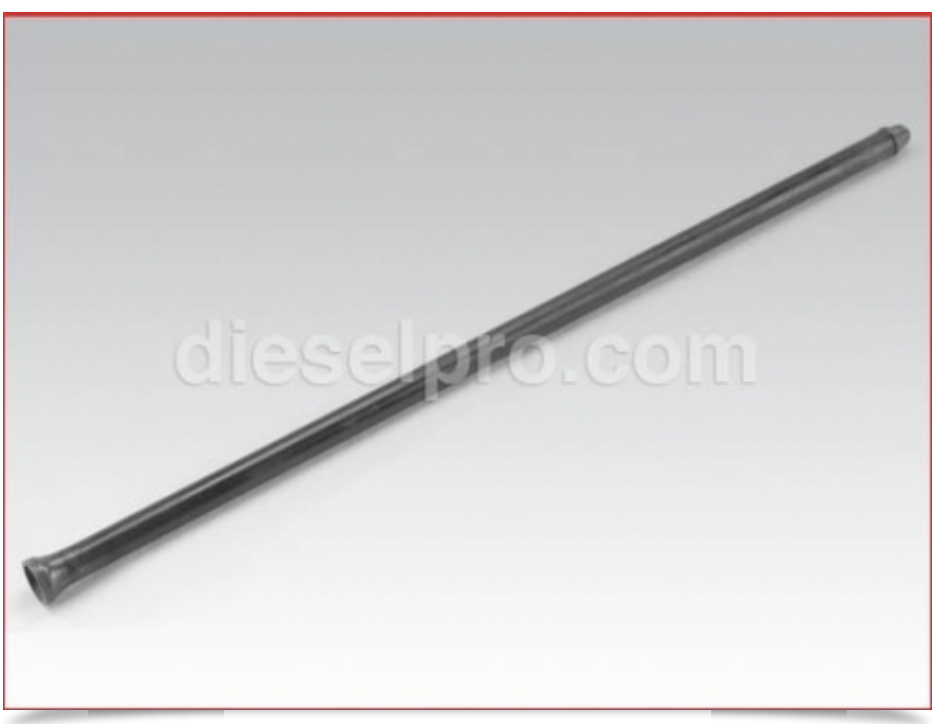
The rocker arms are components that pivot on a shaft and actuate the valves. As the camshaft rotates, it pushes the lifters up, which in turn push the pushrods up. The pushrods then push on the rocker arms, causing them to pivot and actuate the valves. The rocker arms are typically made of steel or aluminum and come in different designs, depending on the engine’s configuration.
The valves are the final component of the valve train. They are responsible for controlling the flow of air and fuel into the engine and the exhaust gasses out of the engine. Valves are typically made of steel or stainless steel and come in different designs, depending on the engine’s configuration and application.
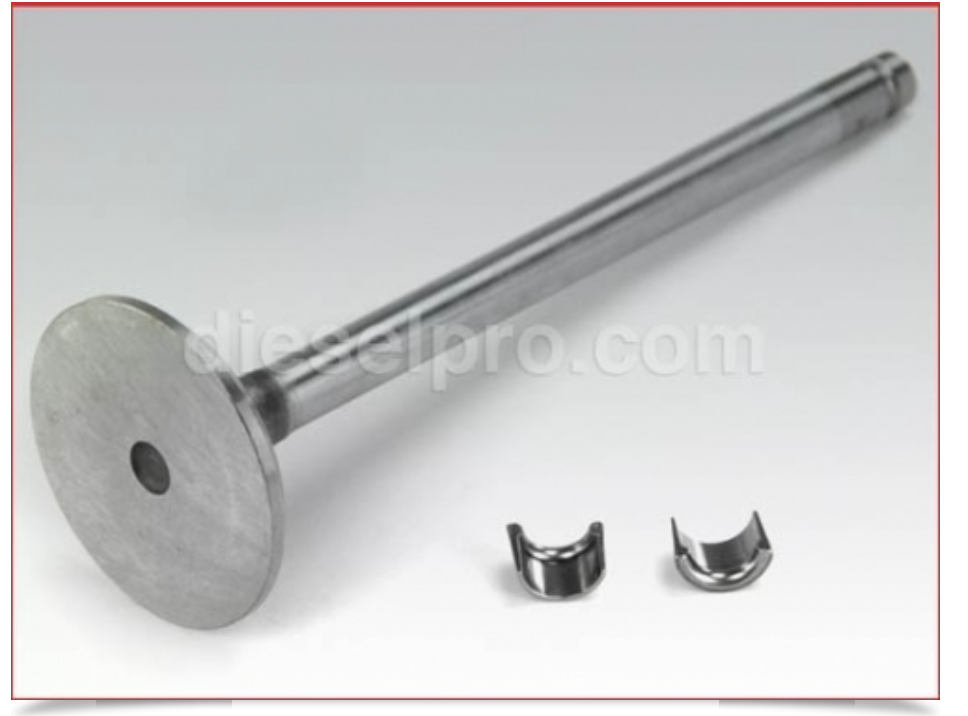
The Cummins valve train also includes hydraulic lash adjusters, which are components that compensate for any wear or clearance between the valve and the rocker arm. This ensures that the valves remain properly adjusted and in contact with the rocker arms at all times. Hydraulic lash adjusters use oil pressure to adjust the valve clearance automatically, eliminating the need for periodic manual adjustment.
The Cummins valve train is designed to provide reliable, efficient operation in a variety of applications. Its robust construction and precise engineering help ensure that the engine operates smoothly and reliably over its lifespan. However, like any mechanical component, the valve train requires periodic maintenance to ensure optimal performance and longevity.
One of the most critical maintenance tasks for the Cummins valve train is valve adjustment. Valve adjustment involves checking and adjusting the valve clearance between the valve and the rocker arm. Over time, the valve clearance can increase due to wear or thermal expansion, causing the valves to open and close at the wrong time. Incorrect valve clearance can lead to poor engine performance, increased emissions, and even engine damage.
Valve adjustment should be performed according to the manufacturer’s recommendations. The process typically involves removing the valve cover and rotating the engine to the proper position. The valve clearance is then checked using a feeler gauge, and the hydraulic lash adjuster is adjusted as necessary to achieve the correct clearance.
Another critical maintenance task for the Cummins valve train is regular inspection and replacement of worn or damaged components. Wear and tear can occur on any of the valve train components, particularly the lifters, pushrods, and rocker arms, which are subjected to high stress and temperature. Over time, these components can become worn, bent, or damaged, affecting the performance and longevity of the engine.
Regular inspection of the valve train components can help identify any issues before they escalate into more significant problems. For example, bent pushrods can cause valve train noise and affect engine performance, while worn rocker arms can cause valve stem and seat damage, leading to engine misfires and decreased power.
Replacing worn or damaged components in the valve train is a critical maintenance task that should be performed according to the manufacturer’s recommendations.
In addition to valve adjustment and component replacement, the Cummins valve train also requires regular lubrication. The valve train components rely on proper lubrication to reduce friction and wear, and to dissipate heat. Insufficient lubrication can cause the valve train components to wear prematurely, leading to poor engine performance and even engine damage.
The engine’s oil system provides lubrication to the valve train components, so it is essential to use the recommended oil viscosity and type. The oil should be changed regularly according to the manufacturer’s recommendations, and the oil filter should be replaced at every oil change.
In conclusion, the Cummins valve train is a critical component of any internal combustion engine, responsible for controlling the flow of air and fuel into the engine and the exhaust gasses out of the engine. The valve train requires regular maintenance to ensure optimal performance and longevity, including valve adjustment, component replacement, and lubrication. By following the manufacturer’s recommendations and performing these critical maintenance tasks, you can help ensure that your Cummins engine operates smoothly and efficiently for many years to come.