
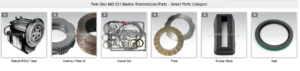
Parts Catalog for Twin Disc MG521 Marine Transmissions
Rebuilt Twin Disc MG521 Marine Transmissions
Plate Kit For Twin Disc MG521 Marine Transmission
Gasket Kits For Twin Disc MG521 Marine Transmission
Pre-Installation Inspection For Twin Disc MG521 Marine Gear
Before installing the Twin Disc MG521 marine transmission, a comprehensive pre-installation inspection is essential. This step ensures that the gear arrives undamaged, matches your configuration, and is ready to be integrated with your marine engine and propulsion system. Skipping or rushing this inspection may lead to alignment problems, hydraulic failures, or catastrophic damage once the engine is started.
1. Visual Inspection
Upon uncrating the MG521 transmission, inspect all sides of the unit for shipping damage, rust, cracks, or evidence of oil leakage. Common issues include:
- Hairline cracks in the housing
- Bent mounting feet
- Damaged input or output shafts
- Missing inspection covers or shipping plugs
If any damage is noticed, do not proceed with installation. Contact the supplier immediately.
2. Verify Model and Ratio
Check the identification tag on the transmission housing. This will list the model number (MG521), gear ratio (e.g., 2.00:1), and serial number. Cross-reference this with your engine’s specifications to confirm compatibility. An incorrect gear ratio can result in poor performance, cavitation, or engine strain.
3. Rotate Input and Output Shafts
Manually rotate the input shaft and observe the movement of the output flange. Listen for grinding or irregular noises. A smooth, quiet rotation indicates the internal gears are correctly aligned and lubricated.
4. Check Oil Level and Condition
Most MG521 units are shipped with break-in oil or test fluid. Check the sight glass or dipstick:
- Oil should be golden to amber, free of debris or water contamination.
- If oil appears milky (indicating water intrusion), flush the unit before use.
Replace the shipping oil with your vessel’s approved marine transmission fluid before startup.
5. Inventory All Mounting and Coupling Hardware
Ensure you have:
- Grade 8 mounting bolts
- Proper length and thread pitch for engine bell housing
- Coupling hardware for the propeller shaft flange
- Alignment shims
- Hydraulic control lines (if electronic or hydraulic shift is used)
- Rubber vibration isolators or resilient mounts
Missing or mismatched fasteners are a common source of alignment and vibration issues during initial operation.
Alignment With Engine and Shaft For Twin Disc MG521 Marine Gear
Proper alignment of the MG521 to both the engine and propeller shaft is one of the most critical aspects of the installation process. Even minor misalignments can lead to bearing wear, coupling failure, and eventual internal gear damage.
1. Aligning with the Engine
- The MG521 is typically mounted directly to the engine’s SAE bell housing.
- Use a hoist to bring the transmission into position, ensuring that the input shaft slides smoothly into the engine’s drive plate or flywheel coupling.
- Do not force the mating process—any binding indicates misalignment or improper angular contact.
2. Face Runout Check
Use a dial indicator to measure the runout between the engine flywheel housing and the transmission’s mating flange.
- Acceptable tolerance: ±0.003 inches
- Out of tolerance: Shim the mounting face accordingly or consult a machinist.
3. Shaft Runout and Parallelism
Once bolted to the engine:
- Measure shaft runout on both the input and output sides.
- Ensure the engine crankshaft centerline aligns with the MG521’s input shaft.
Misalignment between these axes causes axial and radial stress on bearings and clutch packs, leading to premature wear.
4. Soft Foot Check
Before torquing mounting bolts, use feeler gauges to check for gaps between the transmission’s feet and the mounting base.
- Shim any gaps exceeding 0.002 inches.
- Failure to correct soft foot conditions may crack the transmission housing when bolts are torqued.
Foundation and Mounting Bolt Torque For Twin Disc MG521 Marine Gear
The MG521 must be installed on a vibration-resistant and level foundation capable of supporting the unit’s dynamic weight and stress. Mounting procedures should be completed before connecting any hydraulic lines or controls.
1. Base Foundation Requirements
- Must be level within 0.010 inches per foot.
- Should be made of marine-grade steel or reinforced composite.
- Surface must be free of corrosion, rust scale, and contaminants.
2. Mounting Bolt Specifications
- Use Grade 8 or higher tensile-strength bolts.
- Thread engagement should be at least 1.5x the bolt diameter.
- Apply Loctite 271 or equivalent threadlocker for vibration resistance.
- Torque bolts according to diameter:
Bolt Size (SAE) | Torque (lb-ft) |
3/8”-16 | 33–37 |
1/2”-13 | 75–85 |
5/8”-11 | 150–165 |
3/4”-10 | 250–270 |
Re-torque bolts after 25 hours of operation and check every 250 hours thereafter.
3. Vibration Isolators
Install rubber or neoprene isolation pads between the transmission mounting feet and the hull to:
- Absorb torsional vibration
- Minimize shock loading from wave impacts
- Prevent bolt loosening over time
Ensure that isolators are compressed equally to maintain alignment.
Flange Connections For Twin Disc MG521 Marine Gear
The flange connection between the MG521 output and the propeller shaft is the final mechanical link in the drive system. This connection must be precise, clean, and torqued correctly.
1. Cleaning and Surface Prep
- Remove rust preventative from the flange using a degreaser.
- Inspect both mating flanges for pitting, burrs, or warping.
- Use a flat sanding block to true the flange face if minor imperfections are found.
2. Bolt and Nut Selection
- Use SAE Grade 8 or ISO Class 10.9 hardware.
- Bolts should pass completely through the flange with at least one thread exposed beyond the nut.
- Always install with flat washers on both ends.
3. Torque Specifications
Flange Bolt Size | Torque (lb-ft) |
1/2” | 80–90 |
5/8” | 150–165 |
3/4” | 250–275 |
Torque in a star pattern (cross-diagonally) and re-torque after 5 hours of initial operation.
4. Shaft Flange Alignment
Use a dial indicator to ensure concentric alignment between the MG521 flange and the propeller shaft flange:
- Radial runout: < 0.002”
- Axial misalignment: < 0.003”
If tolerance is exceeded, adjust with alignment tools or reposition the shaft.
Coupling Procedures and Tolerances For Twin Disc MG521 Marine Gear
Proper coupling between the MG521 and the propeller shaft is essential to smooth power transfer. Misaligned couplings can create vibration, cause seal wear, and generate destructive resonance.
1. Types of Couplings
- Rigid Couplings: Provide zero play and require perfect alignment.
- Flexible Couplings: Absorb small misalignments and reduce vibration. Ideal for workboats and vessels with hull flex.
Diesel Pro Power recommends flexible couplings with high torque capacity and replaceable bushings for MG521 installations.
2. Shaft Alignment Procedure
- With both flanges bolted loosely, use a feeler gauge and dial indicator to check for gaps.
- Rotate the shaft and re-check alignment at 90° intervals.
- Shim engine or gearbox mounts as needed to correct misalignment.
3. Keyed Shaft Installations
- If using a keyed output shaft, inspect the key and keyway for burrs or deformation.
- Apply anti-seize compound and slide the coupling into place without force.
- Use a torque wrench to secure the nut and check for shaft endplay.
Hydraulic and Mechanical Control Hookup Procedures For Twin Disc MG521 Marine Gear
The Twin Disc MG521 can be operated via mechanical cable linkage or through electronic/hydraulic controls, such as the EC300 series. Correct hookup is crucial for safety, responsiveness, and shift timing.
1. Mechanical Controls
- Use high-quality marine-grade control cables (e.g., Morse type 33C or 43C).
- Route cables with smooth bends, avoiding sharp turns under 8 inches in radius.
- Secure every 12–18 inches with cushioned clamps.
- Check for full engagement of forward, neutral, and reverse detents at the gearbox.
- Adjust throw length to match the shift lever stroke on the MG521.
2. Hydraulic Controls
- Confirm the MG521 is fitted with the appropriate hydraulic servo or actuator.
- Connect pressure and return lines using SAE JIC or ORFS fittings for leak resistance.
- Bleed the system of air using manual bleeders or pump cycling.
- Monitor clutch pack pressure during testing:
Function | Pressure (PSI) |
Forward | 250–300 |
Reverse | 250–300 |
Hydraulic pressure should reach full value within 1–2 seconds of actuation.
3. Electronic Controls (EC300 Integration)
- Connect data cables and power leads according to EC300 wiring diagram.
- Ensure system grounding is correct and EMI-resistant.
- Calibrate shift positions through the controller interface.
- Confirm clutch response using system diagnostics before sea trials.
Safety and PPE Requirements During Installation For Twin Disc MG521 Marine Gear

Installation of a marine transmission such as the MG521 involves several hazards: heavy lifting, hydraulic pressure, rotating shafts, and confined engine rooms. The following safety practices must be followed at all times.
1. Required Personal Protective Equipment (PPE)
- Steel-Toe Boots: Prevent crush injuries from dropped gear or tools.
- Cut-Resistant Gloves: Protect against sharp edges, especially during flange prep.
- Safety Goggles: Shield eyes from debris, especially when using power tools or pressurized fluids.
- Hearing Protection: Use during test starts or when working near running engines.
- Coveralls: Prevent oil exposure and burns from hot components.
2. Installation Environment Safety
- Ensure adequate ventilation, especially in enclosed engine rooms.
- Keep fire extinguishers rated for oil and electrical fires within reach.
- Use oil absorbent pads under the gear and pump area.
- Tag out any live controls or ignition circuits before connecting wiring.
3. Lifting and Handling
- Use a chain hoist, gantry crane, or hydraulic engine hoist rated above the MG521’s weight (approx. 450–550 lbs).
- Balance the gearbox with lifting eyelets or adjustable straps.
- Never position body parts under suspended loads.
4. Emergency Preparedness
- Have a first aid kit accessible on-site.
- Assign a spotter or safety officer if working in confined spaces.
- Document any incidents and report them before resuming work.
Conclusion: Ensuring Success When Installing the Twin Disc MG521 Marine Gear
Installing the Twin Disc MG521 transmission is not just a mechanical process—it’s a precision operation that demands attention to detail, safety, and alignment. Done properly, the MG521 will deliver years of reliable marine propulsion with minimal service interruptions.
To recap:
- Pre-inspection ensures the unit is free from defects and ready for integration.
- Precise alignment with the engine and shaft avoids vibration and internal damage.
- Correct mounting torque and hardware lock the gear in place against hull stresses.
- Flange and coupling techniques ensure power flows smoothly to the propeller.
- Control hookup—whether mechanical, hydraulic, or electronic—must be free of slop or delay.
- Safety protocols and PPE are mandatory to protect technicians and prevent accidents.
Diesel Pro Power carries a complete line of Twin Disc MG521-compatible parts, including:
- Mounting kits
- Couplings
- Control cables
- Hydraulic pumps and fittings
- Rebuild kits with gasket and seal sets
- Filters and lubricants
Parts Catalog for Twin Disc MG521 Marine Transmissions
Rebuilt Twin Disc MG521 Marine Transmissions
Plate Kit For Twin Disc MG521 Marine Transmission
Gasket Kits For Twin Disc MG521 Marine Transmission
Videos About Twin Disc Transmissions
6 Reasons Your Twin Disc Transmission Has Low Oil Pressure
7 Reasons Your Twin Disc Transmission Is Overheating
3 Reasons Your Clutch Plates in Your Twin Disc Transmission Are Making Excessive Noise
Bull Gear On A Twin Disc Transmission
Rebuilt Twin Disc Transmissions