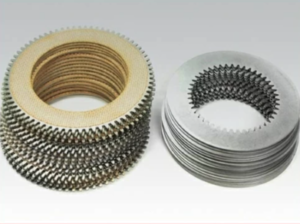
Parts catalog for Twin Disc MG50590A Marine Transmissions
Overhaul Plate Kit For Twin Disc MG5090A Marine Transmission
Gasket Kits For Twin Disc MG5090A Marine Transmission
Introduction: Why Control Systems Matter for the MG-5090A Marine Transmission
The Twin Disc MG-5090A marine transmission is a reliable and high-performing hydraulic gear, but like any transmission, it depends heavily on precise control inputs to operate correctly. Whether you’re using manual mechanical linkages or an electronic control system such as the Twin Disc EC300, it’s vital that these systems be correctly adjusted, smoothly operating, and free from wear.
Failure to inspect and maintain the control system can lead to symptoms that mimic internal transmission failure, such as:
- Slipping or harsh shiftingÂ
- Delayed engagementÂ
- Stuck in gearÂ
- Inability to shift between forward and reverseÂ
This comprehensive guide will walk you through how to inspect, test, lubricate, and adjust both mechanical and electronic control systems, as well as explain the role of each part and provide troubleshooting tips. This is essential reading for marine mechanics, vessel owners, and service managers responsible for keeping their MG-5090A-equipped vessels running smoothly.
Control System Overview for Twin Disc MG-5090A Marine Gear
Mechanical vs. Electronic Control Systems
The MG-5090A can be operated via:
- Mechanical cable-actuated systems, using traditional Morse-style shift levers and linkage armsÂ
- Electronic control systems, such as the Twin Disc EC300, which convert lever motion to electronic signals that actuate solenoids or motorsÂ
Each system has different maintenance requirements, but both must achieve full travel of the clutch valve lever (also known as the control lever or shift lever on the transmission).
Function of the Control Lever
The clutch control lever on the MG-5090A:
- Directs oil pressure to either the forward or reverse clutch packÂ
- Interfaces with either a mechanical cable or actuator motorÂ
- Has detent positions for forward, neutral, and reverseÂ
- Must move fully into each position to ensure complete clutch engagementÂ
Improper lever movement, resistance, or misalignment can result in partial engagement, leading to slippage and increased wear on the clutch components.
Visual Inspection of Mechanical Linkages
Step 1: Identify All Linkage Components
On a mechanical system, identify and inspect the following:
- Shift lever at helmÂ
- Push-pull control cableÂ
- Cable mounts at helm and transmissionÂ
- Transmission-side lever armÂ
- Clevis pins and bushingsÂ
- Detent mechanism (spring and ball assembly on gear housing)Â
Step 2: Disconnect and Test Lever Movement by Hand
- Disconnect the shift cable from the transmission leverÂ
- Manually move the clutch lever through forward, neutral, and reverseÂ
You should feel:
- Smooth movementÂ
- Firm detents (clicks) at each gear positionÂ
- No grinding, catching, or bindingÂ
If resistance is felt, lubricate pivot points and inspect for corrosion, bent hardware, or cracked brackets.
Step 3: Inspect Cable for Wear and Binding
- Run the control lever at the helm through full range of motionÂ
- Observe the cable housing and mounting clampsÂ
- Check that cable doesn’t bend excessively, kink, or chafe on adjacent componentsÂ
Signs of a failing cable:
- Excessive play in leverÂ
- Cable feels spongy or stiffÂ
- Delay between lever movement and clutch responseÂ
- Visible rust or broken strands in the cable jacketÂ
Correction: Replace the cable with a marine-grade stainless core cable of the same length and travel range.
Step 4: Lubricate the Mechanical Linkage
Use marine-grade lithium grease or water-resistant anti-seize lubricant on:
- Clevis pinsÂ
- Pivot jointsÂ
- Detent lever spring area (if accessible)Â
- Helm lever linkage jointsÂ
Do not lubricate the inside of the cable sheath unless it’s a serviceable type. Many modern cables are sealed and designed to operate dry.
Checking and Adjusting Lever Travel
Step 1: Verify Full Lever Travel
From neutral, push the helm lever into forward and reverse, and observe if the clutch lever on the MG-5090A fully moves into its respective detent.
If the lever fails to:
- Reach the detent stopÂ
- Return to center reliablyÂ
- Stay positively in gearÂ
…it could result in partial clutch engagement, causing slippage and heat buildup.
Step 2: Adjust Cable Endpoints
On both the helm and transmission ends:
- Loosen the cable clampsÂ
- Reposition the cable anchor so the lever reaches full travelÂ
- Confirm the neutral detent aligns with the control lever’s center pointÂ
- Retighten and testÂ
Cable travel should be:
- Approximately 2.5 inches for most shift armsÂ
- Aligned so the detents click firmly into placeÂ
Step 3: Inspect Control Brackets and Bushings
Over time, transmission-mounted control brackets and shift arm bushings may develop:
- Elongated holesÂ
- Cracks or fatigueÂ
- Worn bushings, causing lever slopÂ
- Loose bolts that allow lever misalignmentÂ
Replace damaged brackets and re-torque mounting bolts to factory specification to prevent movement under load.
Electronic Control System Checks (e.g., Twin Disc EC300)
Step 1: Run System Diagnostics
Modern control systems like the EC300 have built-in diagnostic tools, which can be accessed via:
- Display module (LCD screen)Â
- Laptop interfaceÂ
- LED light codes on actuatorÂ
Diagnostic Functions May Include:
- Actuator response testÂ
- Position sensor calibrationÂ
- Error code historyÂ
- Voltage input/output verificationÂ
Step 2: Observe Shifting Behavior
With the vessel powered but engine off:
- Move the shift lever at the helmÂ
- Watch the actuator on the transmission move the clutch leverÂ
- Confirm full travel into forward and reverse detentsÂ
Signs of actuator failure or miscalibration:
- Incomplete movement of the clutch leverÂ
- Slow or jerky responseÂ
- Lever returns to neutral unexpectedlyÂ
- Actuator emits clicking or grinding noisesÂ
Step 3: Calibrate Shift Points
Use the manufacturer’s calibration procedure to:
- Set the neutral, forward, and reverse limitsÂ
- Program the shift delay (optional)Â
- Adjust actuator travel to match the MG-5090A’s lever arcÂ
Important: Misaligned shift limits will result in incomplete clutch engagement—even if the lever appears to be in gear.
Step 4: Check Electrical Connections
Inspect:
- Power and ground terminals at the actuatorÂ
- CANbus or harness connectorsÂ
- Signs of corrosion or pin misalignmentÂ
Use dielectric grease to prevent future moisture ingress.
Detent Mechanism Inspection and Adjustment
The MG-5090A features an internal detent mechanism, often located at the base of the clutch valve lever, consisting of:
- SpringÂ
- Steel ball or rollerÂ
- Detent plateÂ
This provides a tactile “click” at gear positions and helps hold the transmission in gear even if the cable tension fluctuates.
Step 1: Inspect Detent Action
With the transmission off and lever disconnected:
- Move the clutch lever slowlyÂ
- Feel for 3 distinct detents: forward, neutral, and reverseÂ
Step 2: Troubleshoot Weak Detent
If detents feel soft or missing:
- The detent spring may be worn or brokenÂ
- Debris may be obstructing the detent trackÂ
- Internal corrosion could be presentÂ
Fix: Remove the clutch lever cover (if accessible) and inspect the spring-ball detent. Replace worn components with a detent repair kit from Diesel Pro Power.
Step 3: Verify Hold Strength
Shift into gear and attempt to gently nudge the lever. It should not slip out of gear unless pulled manually with force.
Final Test and Adjustment Checklist
Once all mechanical or electronic components are verified, conduct a full operational test.
Mechanical System Test:
- Move helm lever through full rangeÂ
- Confirm cable does not bind or flex excessivelyÂ
- Verify full clutch lever travel at the transmissionÂ
- Confirm firm detents at forward, neutral, and reverseÂ
- Shift under engine power and test responseÂ
- Inspect for slippage, delays, or vibrationÂ
Electronic System Test:
- Perform full system calibrationÂ
- Verify shift lever inputs match actuator responseÂ
- Listen for any actuator hesitationÂ
- Confirm visual detent alignment on the MG-5090AÂ
- Shift under engine power and observe oil pressure (250–300 PSI is ideal)Â
Final Adjustments:
- Adjust cable clamps, actuator stops, or lever brackets as neededÂ
- Tighten all hardware to torque specsÂ
- Apply marine-grade grease to all moving jointsÂ
- Record shift lever position and system status in your logbookÂ
Troubleshooting Control System Symptoms
Symptom | Likely Cause | Recommended Action |
Transmission won’t shift | Cable failure / actuator fault | Replace cable or inspect EC300 wiring |
Slipping despite oil pressure OK | Lever not reaching detent | Adjust cable endpoints or recalibrate ECU |
Lever returns to neutral | Weak detent mechanism | Inspect and replace spring/ball |
Shudder during shift | Partial clutch engagement | Confirm full lever travel and clutch inspection |
Harsh shifting (electronic) | Incorrect actuator timing | Recalibrate EC300 or update firmware |
Pro Tips to Prevent Control Issues on the MG-5090A
- Grease linkages every 6 months or more frequently in saltwater useÂ
- Check cable mounting brackets for movement at every oil changeÂ
- Replace cables every 3–5 years regardless of appearanceÂ
- Keep EC300 software updated and record calibration settingsÂ
- Never force the lever—stiffness indicates a problem needing correctionÂ
Diesel Pro Power Control Support and Replacement Parts
At Diesel Pro Power, we supply:
- Twin Disc MG-5090A control leversÂ
- Replacement detent kitsÂ
- Shift cables (standard and custom lengths)Â
- EC300-compatible actuatorsÂ
- Bushing kits and bracket assembliesÂ
- Rebuilt MG-5090A transmissions with pre-calibrated controlsÂ
We also provide expert guidance on mechanical-to-electronic conversion, system calibration, and complete transmission rebuilds.
Summary: Control Systems = Transmission Health on the MG-5090A
The clutch packs and gears inside your Twin Disc MG-5090A are engineered for durability, but they only function correctly if the control system delivers the right signals—mechanically or electronically. Improper cable routing, misaligned shift arms, weak detents, or actuator calibration issues can all lead to symptoms that appear to be transmission failures but are actually external control problems.
Proper linkage and control inspection is an essential part of your MG-5090A’s annual maintenance schedule—and one of the easiest ways to prevent costly misdiagnoses and premature wear.
Quick Reference Inspection Chart
Component |
Check Frequency |
Inspection Criteria |
Mechanical shift cable | Every 6 months | No binding, full travel, no corrosion |
Lever travel and detents | Every 1,000 hours | Positive stops at FWD/NEUTRAL/REV |
Brackets and bushings | Every oil change | No cracks, proper alignment |
EC300 actuator calibration | Annually or after repair | Full travel, correct gear assignment |
Grease pivot points | Every 6 months | No dry or corroded joints |
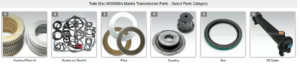
Overhaul Plate Kit For Twin Disc MG5090A Marine Transmission
Gasket Kits For Twin Disc MG5090A Marine Transmission
Videos About Twin Disc Transmissions
6 Reasons Your Twin Disc Transmission Has Low Oil Pressure
7 Reasons Your Twin Disc Transmission Is Overheating
3 Reasons Your Clutch Plates in Your Twin Disc Transmission Are Making Excessive Noise
Bull Gear On A Twin Disc TransmissionÂ
Rebuilt Twin Disc Transmissions