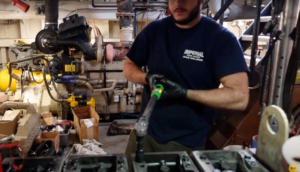
The Cummins KTA19 is a powerful, versatile engine widely used in marine, industrial, construction, and vehicle applications. Its robust design and adaptability make it a preferred choice for equipment requiring high power output and reliability. However, to fully leverage the engine’s capabilities, it’s critical to understand the mounting adaptations and custom installation requirements that ensure optimal performance and longevity.
This guide covers everything you need to know about configuring the KTA19 for different applications, adapter plate installations, and custom modifications to suit unique operational needs. Additionally, we’ll explore best practices for safe engine mounting to prevent mechanical issues and ensure compliance with Cummins’ installation standards.
Parts Catalog for Cummins KTA19 Marine Engine
Configuring the KTA19 for Various Applications
The Cummins KTA19 can be configured for a wide range of applications, including:
- Marine vessels: Tugboats, fishing trawlers, workboats, ferries
- Industrial equipment: Generators, compressors, drilling rigs, pumps
- Vehicles: Heavy-duty trucks, off-highway equipment, construction machinery
Each application requires specific adaptations to ensure the engine operates efficiently and safely under different load conditions, environments, and stress factors.
Factors to Consider When Configuring the KTA19:
- Power Requirements:
- Determine the horsepower and torque needed for the application.
- Select appropriate fuel injection settings, turbocharger configurations, and cooling systems.
- Mounting Orientation:
- The engine can be installed in various orientations (vertical, inclined) based on space availability and design constraints.
- The engine can be installed in various orientations (vertical, inclined) based on space availability and design constraints.
- Cooling Systems:
- Marine applications often require raw water cooling or keel cooling systems.
- Industrial setups typically use radiator-based cooling systems.
- Drive Adaptations:
- Power take-off (PTO) configurations for auxiliary equipment such as hydraulic pumps or generators.
- Power take-off (PTO) configurations for auxiliary equipment such as hydraulic pumps or generators.
- Exhaust Routing:
- Proper exhaust system design reduces backpressure and ensures compliance with emission regulations.
- Proper exhaust system design reduces backpressure and ensures compliance with emission regulations.
- Environmental Conditions:
- Consider temperature extremes, humidity, saltwater exposure, dust, and vibration levels.
- Consider temperature extremes, humidity, saltwater exposure, dust, and vibration levels.
Engine Mounting Considerations for Marine, Industrial, and Vehicle Setups
Proper engine mounting is critical to prevent vibration issues, misalignment, and structural damage. The mounting system must absorb engine vibrations while maintaining alignment with the driven equipment.
1. Marine Installations
Marine environments demand robust engine mounts due to constant motion, vibration, and corrosion exposure.
Key Considerations:
- Flexible Mounts: Reduce vibrations and absorb shock from wave impacts.
- Corrosion-Resistant Materials: Stainless steel brackets and anti-corrosion coatings are essential for saltwater environments.
- Engine Alignment: Precise alignment with the propeller shaft is crucial to avoid excessive wear on bearings and seals.
Common Mounting Types for Marine:
- Resilient Mounts: Absorb vibrations and prevent structural resonance.
- Rigid Mounts: Used in vessels where vibration isolation is less critical (e.g., barges).
2. Industrial Installations
In stationary applications such as power generators or pumps, the mounting system focuses on stability and ease of maintenance.
Key Considerations:
- Foundation Mounting: Securely bolt the engine to a reinforced concrete or steel base to minimize vibration transmission.
- Isolation Pads: Rubber or elastomer pads can reduce vibrations in sensitive environments (like hospitals with backup generators).
- Accessibility: Ensure there’s adequate space around the engine for maintenance and inspection.
3. Vehicle Installations
For on-road or off-road vehicles, mounting systems must withstand constant motion, sudden shocks, and variable loads.
Key Considerations:
- Vibration Dampening: Use high-quality engine mounts to reduce cabin noise and improve driver comfort.
- Dynamic Load Handling: Ensure mounts can withstand sudden impacts and load shifts, especially in construction equipment.
- Compact Design: Space constraints require innovative mounting designs that don’t compromise engine performance.
Adapter Plate Configurations and Installation Tips
Adapter plates are often used when installing the KTA19 into equipment not originally designed for it. They help align the engine with the drivetrain or power transmission system.
Functions of Adapter Plates:
- Facilitate the connection between the engine and transmissions, gearboxes, or PTO units.
- Ensure precise alignment of rotating components to prevent premature wear.
- Allow for custom mounting in specialized equipment.
Common Adapter Plate Configurations:
- Flywheel Housing Adapters:
- Connect the engine’s flywheel to the transmission.
- Must match both the engine’s bolt pattern and the transmission’s input shaft.
- Mounting Frame Adapters:
- Attach the engine to custom frames or skids.
- Provide additional support in heavy-duty applications.
- PTO Adapter Plates:
- Used in industrial equipment like pumps, compressors, and winches.
- Used in industrial equipment like pumps, compressors, and winches.
Installation Tips for Adapter Plates:
- Check Compatibility:
- Verify that the adapter matches both the engine’s and the equipment’s specifications.
- Verify that the adapter matches both the engine’s and the equipment’s specifications.
- Proper Alignment:
- Misalignment can cause vibration, bearing failure, and gear damage. Use dial indicators to achieve precise alignment.
- Misalignment can cause vibration, bearing failure, and gear damage. Use dial indicators to achieve precise alignment.
- Torque Specifications:
- Tighten all bolts to Cummins’ recommended torque settings to prevent loosening during operation.
- Tighten all bolts to Cummins’ recommended torque settings to prevent loosening during operation.
- Use of Dowel Pins:
- Dowel pins ensure accurate positioning, especially for flywheel housing adapters.
- Dowel pins ensure accurate positioning, especially for flywheel housing adapters.
- Inspect for Clearance Issues:
- Ensure there’s enough space around the adapter plate for proper ventilation and maintenance access.
- Ensure there’s enough space around the adapter plate for proper ventilation and maintenance access.
Custom Installations and Modifications
In many applications, especially in custom-built machinery or retrofitted equipment, standard mounting configurations may not suffice. This is where custom installations and modifications come into play.
When Custom Installations Are Required:
- Retrofitting older equipment with new KTA19 engines
- Installing the engine in limited-space environments
- Marine repowers, where the engine must fit existing hull dimensions
- Heavy machinery with unique PTO requirements
Adapting the KTA19 for Unique Equipment
1. Custom Engine Mounts:
- Fabricate mounts from high-strength steel to handle engine weight and torque.
- Use polyurethane bushings for additional vibration isolation.
2. Modified Exhaust Systems:
- Design custom exhaust routing for compact spaces.
- Ensure proper backpressure to maintain engine performance.
3. Custom Cooling Solutions:
- In marine applications, modify the engine for keel cooling instead of standard radiators.
- For industrial use, integrate auxiliary coolers or larger radiators for hot climates.
4. Electrical System Adaptations:
- Custom harnesses may be needed to integrate the KTA19’s electrical system with the equipment’s controls.
5. Custom Driveline Adaptations:
- Modify driveshafts and couplings to handle the engine’s torque output.
Best Practices for Safe Engine Mounting
Incorrect engine mounting can cause severe damage to both the engine and the equipment. To ensure a safe, reliable installation, follow these best practices:
1. Conduct a Detailed Site Assessment:
- Understand the application’s requirements, including space constraints, load conditions, and environmental factors.
2. Follow Manufacturer Guidelines:
- Always refer to the Cummins KTA19 installation manual for specific mounting instructions.
- Use Cummins-approved mounting hardware and torque specifications.
3. Ensure Proper Load Distribution:
- Mounts should evenly distribute the engine’s weight to avoid stress fractures in the frame or engine block.
4. Use High-Quality Fasteners:
- Use grade 8 bolts or equivalent for structural integrity.
- Apply thread-locking compounds to prevent loosening from vibration.
5. Check for Proper Alignment:
- Misalignment can lead to:
- Premature wear of engine components
- Driveline vibrations
- Seal failures
- Use laser alignment tools or dial indicators for precision.
6. Vibration Isolation:
- Install vibration isolators to minimize the transfer of engine vibrations to the chassis, reducing wear on both the engine and the equipment.
7. Secure Fuel and Electrical Lines:
- Properly route and secure fuel hoses, wiring harnesses, and coolant lines to prevent chafing and leaks.
8. Regular Inspection and Maintenance:
- After installation, perform regular checks on:
- Mounting bolts for tightness
- Engine mounts for cracks or deformation
- Alignment of the driveline and PTO shafts
Common Engine Mounting Issues and How to Avoid Them
Issue | Cause | Solution |
Excessive Vibration | Poor mount alignment | Realign mounts, add vibration isolators |
Mounting Bolt Failures | Under-torqued bolts | Re-torque bolts to manufacturer specs |
Cracked Engine Brackets | Uneven load distribution | Reassess mounting geometry, reinforce frame |
Driveline Misalignment | Inaccurate adapter plate fitment | Re-check alignment using precision tools |
Overheating | Inadequate cooling system placement | Install auxiliary coolers or modify airflow |
Case Study: Marine Repower with Cummins KTA19
A commercial fishing vessel needed to replace an older engine with a new Cummins KTA19. The challenge was fitting the larger engine into an existing hull without modifying the boat’s structure.
Solution:
- Custom Mount Fabrication:
- Designed steel engine mounts with anti-vibration pads to absorb shock.
- Designed steel engine mounts with anti-vibration pads to absorb shock.
- Adapter Plate Installation:
- Created a custom flywheel adapter plate to connect the engine to the existing marine transmission.
- Created a custom flywheel adapter plate to connect the engine to the existing marine transmission.
- Cooling System Upgrade:
- Integrated a keel cooling system to replace the outdated raw water cooling setup.
- Integrated a keel cooling system to replace the outdated raw water cooling setup.
- Final Adjustments:
- Aligned the propeller shaft using laser alignment tools to reduce wear.
- Aligned the propeller shaft using laser alignment tools to reduce wear.
Results:
- Improved fuel efficiency by 15%
- Reduced engine noise by 20%
- Increased vessel reliability with minimal downtime
Conclusion
The Cummins KTA19 is designed to be adaptable across various applications, but proper mounting and custom installations are key to maximizing performance and longevity. Whether you’re configuring the engine for a marine vessel, industrial generator, or heavy equipment, understanding the principles of mounting adaptations, custom modifications, and alignment is essential.
By following Cummins’ guidelines, using high-quality components, and adhering to best practices, you can ensure your KTA19 engine operates safely and efficiently for years to come.
Disclaimer
Incorrect engine mounting can lead to severe damage. Always consult installation guidelines from Cummins for secure adaptation. Follow proper torque specifications, alignment procedures, and safety protocols to prevent mechanical failures and ensure optimal performance.
Parts Catalog for Cummins KTA19 Marine Engine