
Understanding and maintaining optimal operating conditions is essential for ensuring the performance, efficiency, and longevity of Detroit Diesel 92 Series engines. This section provides detailed guidance on recommended parameters for lubrication, air, fuel, cooling systems, and compression levels, tailored to the specific requirements of the 6V92, 8V92, 12V92, and 16V92 engine models.
Parts Catalog for 6V92 Detroit Diesel Engines
Parts Catalog for 8V92 Detroit Diesel Engines
Parts Catalog for 12V92 Detroit Diesel Engines
Parts Catalog for 16V92 Detroit Diesel Engines
Lubrication, Air, and Fuel System Parameters
Proper lubrication, air intake, and fuel delivery are fundamental to the reliable operation of any engine. The following parameters ensure these systems function effectively under varying operating conditions.
1. Lubrication System Parameters
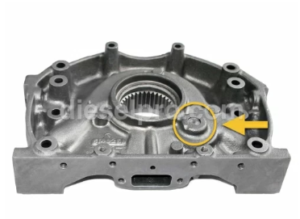
- Oil Pressure:
Mechanical Marine Oil Pressure Gauge 100 PSI
- Recommended range: 30–60 psi (2.1–4.1 bar) at operating RPMs.
- Idle oil pressure: Minimum 10 psi (0.7 bar).
- Low pressure may indicate issues such as oil pump wear, clogged filters, or insufficient oil levels.
- Oil Temperature:
Mechanical Oil Temperature Gauge 6FT
- Ideal range: 180–200°F (82–93°C).
- Temperatures above 230°F (110°C) can degrade oil quality and cause damage.
- Oil Flow:
Electrical Oil Pressure Gauge – 12 Volt
- Maintain proper flow to bearings, camshafts, and turbochargers to prevent friction and wear.
- Maintain proper flow to bearings, camshafts, and turbochargers to prevent friction and wear.
2. Air System Parameters
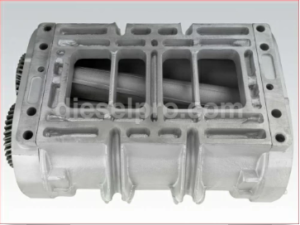
- Intake Air Temperature:
- Optimal range: 70–110°F (21–43°C).
- High intake temperatures can reduce combustion efficiency, while excessively cold air may affect fuel atomization.
- Air Flow:
- Ensure unrestricted air intake by inspecting and maintaining clean filters and ducts.
- Ensure unrestricted air intake by inspecting and maintaining clean filters and ducts.
- Turbocharger Boost Pressure (if equipped):
Target range: 15–25 psi (1.0–1.7 bar) under load, depending on configuration.
Turbo for Detroit Diesel Marine Aftercooled Engines (6V92, 8V92, 12V92, 16V92)
3. Fuel System Parameters
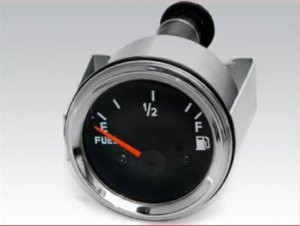
- Fuel Pressure:
- Recommended range: 60–70 psi (4.1–4.8 bar) at the fuel manifold.
- Pressure below this range may indicate clogged filters or a failing fuel pump.
- Fuel Temperature:
- Ideal range: 85–105°F (29–41°C).
- Elevated fuel temperatures can reduce energy density and affect injector performance.
- Fuel Flow Rate:
- Ensure sufficient flow to meet engine demand under all load conditions.
- Ensure sufficient flow to meet engine demand under all load conditions.
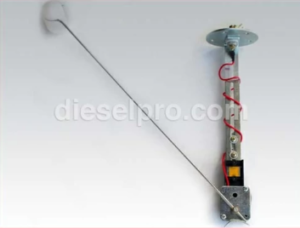
Cooling System Parameters
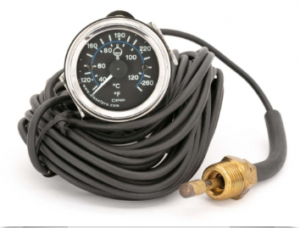
The cooling system plays a critical role in maintaining engine temperature and preventing overheating or thermal stress. Proper flow, temperature, and pressure are essential for optimal performance.
1. Coolant Temperature
- Operating Range:
- Maintain coolant temperatures between 160–195°F (71–90°C).
- Temperatures above 210°F (99°C) may indicate issues such as radiator blockage, low coolant levels, or a failing thermostat.
2. Coolant Flow
- Flow Rates:
- Flow should be sufficient to circulate coolant throughout the engine, radiator, or heat exchanger.
- Inspect for obstructions in the radiator, hoses, or heat exchanger that could impede flow.
3. System Pressure
- Normal Pressure:
- Typical system pressure is 7–15 psi (0.5–1.0 bar), maintained by the radiator cap or pressure valve.
- Low pressure may indicate leaks or a failing pressure cap.
4. Auxiliary Cooling Components
- Raw Water Pumps (Marine Engines):
- Ensure the pump is primed and operating efficiently, delivering adequate cooling water to the heat exchanger.
Sea Water Pump for Detroit Diese 92 Series Marine Engines (6V92 and 8V92)
- Ensure the pump is primed and operating efficiently, delivering adequate cooling water to the heat exchanger.
- Heat Exchanger Efficiency:
- Inspect the heat exchanger for fouling or scale buildup, which can reduce heat transfer and cooling performance.
Raw Water Pump & Related Components for 6V92 Non- Turbo Detroit Diesel Marine Engine
Raw Water Pump & Related Components for 6V92 Turbo Detroit Diesel Marine Engine
Raw Water Pump & Related Components for 8V92 Non- Turbo Detroit Diesel Marine Engine
Raw Water Pump & Related Components for 8V92 Turbo Detroit Diesel Marine Engine
Raw Water Pump & Related Components for 12V92 Non- Turbo Detroit Diesel Marine Engine
Raw Water Pump & Related Components for 12V92 Turbo Detroit Diesel Marine Engine
Raw Water Pump & Related Components for 16V92 Non- Turbo Detroit Diesel Marine Engine
Raw Water Pump & Related Components for 16V92 Turbo Detroit Diesel Marine Engine
- Inspect the heat exchanger for fouling or scale buildup, which can reduce heat transfer and cooling performance.
Compression Standards
Compression pressure is a key indicator of engine health and efficiency, as it affects combustion quality and power output.
1. Target Compression Levels
Engine Configuration | Compression Range (psi) | Notes |
Naturally Aspirated (N/A) | 425–450 psi | Check for consistency across all cylinders to detect wear or damage. |
Turbocharged (T) | 475–500 psi | Increased compression due to forced air induction. |
Turbo-Intercooled (TI) | 480–510 psi | Enhanced cooling allows for slightly higher compression pressures. |
Turbo-Aftercooled (TA) | 490–520 psi | Maximized efficiency from post-turbo cooling systems. |
2. Measuring Compression
- Procedure:
- Conduct a compression test by removing injectors and connecting a compression gauge to each cylinder.
- Rotate the engine using the starter and record the peak pressure for each cylinder.
- Interpreting Results:
- Variations greater than 10% between cylinders may indicate worn piston rings, damaged valves, or cylinder head issues.
- Variations greater than 10% between cylinders may indicate worn piston rings, damaged valves, or cylinder head issues.
Best Practices for Maintaining Operating Conditions
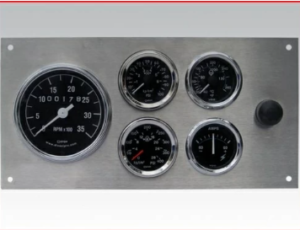
- Monitor Key Metrics
- Continuously observe oil pressure, coolant temperature, and exhaust emissions during operation to detect anomalies early.
- Continuously observe oil pressure, coolant temperature, and exhaust emissions during operation to detect anomalies early.
- Inspect Components Regularly
- Perform periodic inspections of hoses, filters, and connections to ensure all systems operate within the recommended parameters.
- Perform periodic inspections of hoses, filters, and connections to ensure all systems operate within the recommended parameters.
- Use Approved Fluids and Components
- Maintain optimal performance by using Detroit Diesel-approved fluids or premium aftermarket alternatives.
- Maintain optimal performance by using Detroit Diesel-approved fluids or premium aftermarket alternatives.
- Document Readings
- Record operating metrics regularly to establish a performance baseline and identify trends over time.
Mechanical Gauges & Related Components for Detroit Diesel 92 Series Marine & Industrial Engines
Mechanical Gauges with Alarm & Related Components for Detroit Diesel 92 Series Marine & Industrial Engines
12 Volt Electronic Gauges & Related Components for Detroit Diesel 92 Series Marine & Industrial Engines
24V Electrical Gauges & Related Components for Detroit Diesel 92 Series Marine & Industrial Engines
- Record operating metrics regularly to establish a performance baseline and identify trends over time.
Conclusion
Adhering to the recommended operating conditions for lubrication, air, fuel, cooling, and compression ensures reliable performance and extends the service life of Detroit Diesel 92 Series engines. By maintaining parameters within specified ranges and performing routine checks, operators and technicians can optimize engine efficiency, minimize downtime, and prevent costly repairs.
Parts Catalog for 6V92 Detroit Diesel Engines
Parts Catalog for 8V92 Detroit Diesel Engines
Parts Catalog for 12V92 Detroit Diesel Engines
Parts Catalog for 16V92 Detroit Diesel Engines