
Optimizing performance for Detroit Diesel 92 Series engines ensures efficiency, reliability, and longevity. By tuning and calibrating key systems, maintaining critical components, and conducting regular inspections, operators can maximize the engines’ potential while reducing downtime and maintenance costs. This section provides detailed guidelines for tuning, component-specific adjustments, and inspection schedules.
Tuning and Calibration

Precise tuning and calibration are essential for ensuring the engine operates at its optimal efficiency. Injector rack adjustments and valve clearance settings are critical steps in this process.
1. Injector Rack Adjustments

-
Purpose:
- Ensures synchronized fuel delivery across all cylinders for balanced combustion.
- Ensures synchronized fuel delivery across all cylinders for balanced combustion.
-
Tools Required:
- Feeler gauge, dial indicator, and torque wrench.
- Feeler gauge, dial indicator, and torque wrench.
-
Procedure:
- Preparation:
- Warm up the engine to its normal operating temperature.
- Remove valve covers to access injector racks.
- Position the Cylinder at Top Dead Center (TDC):
- Rotate the crankshaft until the first cylinder is at TDC on the compression stroke.
- Rotate the crankshaft until the first cylinder is at TDC on the compression stroke.
- Adjust the Injector Rack:
- Loosen the adjusting screw and set the rack to move freely.
- Use a dial indicator to measure the plunger height, ensuring it matches the following specifications:
- Naturally Aspirated Engines: 1.485 inches (37.7 mm).
- Turbocharged Engines: 1.495 inches (37.9 mm).
- Secure the Adjustment:
- Tighten the lock nut without altering the setting.
- Tighten the lock nut without altering the setting.
- Repeat for All Cylinders:
- Rotate the crankshaft to position each cylinder at TDC and repeat the adjustment process.
- Rotate the crankshaft to position each cylinder at TDC and repeat the adjustment process.
- Preparation:
Injector & Related Components for 6V92 Non- Turbo Detroit Diesel Marine & Industrial Engines
Injector & Related Components for 6V92 Turbo Detroit Diesel Marine & Industrial Engines
Injector & Related Components for 8V92 Non- Turbo Detroit Diesel Marine & Industrial Engines
Injector & Related Components for 8V92 Turbo Detroit Diesel Marine & Industrial Engines
Injector & Related Components for 12V92 Non- Turbo Detroit Diesel Marine & Industrial Engines
Injector & Related Components for 12V92 Turbo Detroit Diesel Marine & Industrial Engines
Injector & Related Components for 16V92 Non- Turbo Detroit Diesel Marine & Industrial Engines
Injector & Related Components for 16V92 Turbo Detroit Diesel Marine & Industrial Engines
2. Valve Clearance Settings
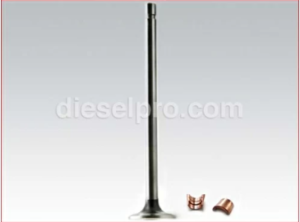
-
Purpose:
- Ensures valves open and close at the correct times, optimizing air intake and exhaust flow.
- Ensures valves open and close at the correct times, optimizing air intake and exhaust flow.
-
Tools Required:
- Feeler gauge and torque wrench.
- Feeler gauge and torque wrench.
-
Procedure:
- Set Cylinder to TDC:
- Rotate the crankshaft to position the cylinder being adjusted at TDC on the compression stroke.
- Rotate the crankshaft to position the cylinder being adjusted at TDC on the compression stroke.
- Measure Clearance:
- Insert the correct size feeler gauge between the rocker arm and valve stem:
- Naturally Aspirated Engines: 0.015 inches (0.38 mm).
- Turbocharged Engines: 0.013 inches (0.33 mm).
- Insert the correct size feeler gauge between the rocker arm and valve stem:
- Adjust Clearance:
- Loosen the lock nut and turn the adjusting screw until the gauge moves with slight resistance.
- Loosen the lock nut and turn the adjusting screw until the gauge moves with slight resistance.
- Secure Adjustment:
- Tighten the lock nut and recheck the clearance.
- Tighten the lock nut and recheck the clearance.
- Repeat for All Valves:
- Adjust each valve according to the firing order of the engine.
- Adjust each valve according to the firing order of the engine.
- Set Cylinder to TDC:
Valve & Related Components for 6V92 Non- Turbo Detroit Diesel Marine & Industrial Engines
Valve & Related Components for 6V92 Turbo Detroit Diesel Marine & Industrial Engines
Valve & Related Components for 8V92 Non- Turbo Detroit Diesel Marine & Industrial Engines
Valve & Related Components for 8V92 Turbo Detroit Diesel Marine & Industrial Engines
Valve & Related Components for 12V92 Non- Turbo Detroit Diesel Marine & Industrial Engines
Valve & Related Components for 12V92 Turbo Detroit Diesel Marine & Industrial Engines
Valve & Related Components for 16V92 Non- Turbo Detroit Diesel Marine & Industrial Engines
Valve & Related Components for 16V92 Turbo Detroit Diesel Marine & Industrial Engines
Component-Specific Guidelines
Optimizing individual components ensures overall engine efficiency and performance. Key components include the turbocharger, exhaust system, and fuel injectors.
1. Turbocharger Tuning
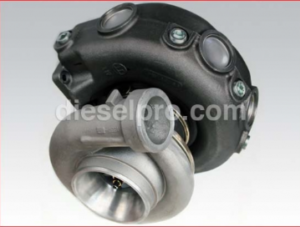
- Purpose:
- Maximizes air intake and compression for enhanced combustion efficiency.
- Maximizes air intake and compression for enhanced combustion efficiency.
- Steps:
- Inspect for oil leaks, blade damage, or excessive play in the shaft.
- Clean the turbocharger housing and blades to remove soot and debris.
- Verify boost pressure under load, ensuring it meets the specified range: 15–25 psi (1.0–1.7 bar).
- Replace worn seals or bearings to prevent performance loss.
Turbocharger & Related Components for 6V92 Turbo Detroit Diesel Marine & Industrial Engines
Turbocharger & Related Components for 8V92 Turbo Detroit Diesel Marine & Industrial Engines
Turbocharger & Related Components for 12V92 Turbo Detroit Diesel Marine & Industrial Engines
Turbocharger & Related Components for 16V92 Turbo Detroit Diesel Marine & Industrial Engines
2. Exhaust System Inspections
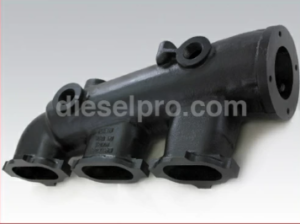
- Purpose:
- Ensures unrestricted exhaust flow and minimizes backpressure.
- Ensures unrestricted exhaust flow and minimizes backpressure.
- Steps:
- Check for cracks, leaks, or blockages in the exhaust manifold and pipes.
- Inspect gaskets for wear or deterioration, replacing as needed.
- Clean or replace mufflers and catalytic converters to maintain flow efficiency.
Exhaust Manifold & Related Components for 6V92 Non- Turbo Detroit Diesel Marine & Industrial Engines
Exhaust Manifold & Related Components for 6V92 Turbo Detroit Diesel Marine & Industrial Engines
Exhaust Manifold & Related Components for 8V92 Non- Turbo Detroit Diesel Marine & Industrial Engines
Exhaust Manifold & Related Components for 8V92 Turbo Detroit Diesel Marine & Industrial Engines
Exhaust Manifold & Related Components for 12V92 Non- Turbo Detroit Diesel Marine & Industrial Engines
Exhaust Manifold & Related Components for 12V92 Turbo Detroit Diesel Marine & Industrial Engines
Exhaust Manifold & Related Components for 16V92 Non- Turbo Detroit Diesel Marine & Industrial Engines
Exhaust Manifold & Related Components for 16V92 Turbo Detroit Diesel Marine & Industrial Engines
3. Injector Performance Checks
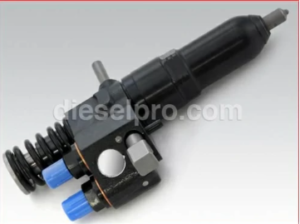
- Purpose:
- Maintains precise fuel delivery for consistent combustion.
- Maintains precise fuel delivery for consistent combustion.
- Steps:
- Test injectors for proper spray patterns using an injector tester.
- Clean injectors to remove carbon deposits or replace them if performance is compromised.
- Verify injector timing to ensure it aligns with engine specifications.
Injector & Related Components for 6V92 Non- Turbo Detroit Diesel Marine & Industrial Engines
Injector & Related Components for 6V92 Turbo Detroit Diesel Marine & Industrial Engines
Injector & Related Components for 8V92 Non- Turbo Detroit Diesel Marine & Industrial Engines
Injector & Related Components for 8V92 Turbo Detroit Diesel Marine & Industrial Engines
Injector & Related Components for 12V92 Non- Turbo Detroit Diesel Marine & Industrial Engines
Injector & Related Components for 12V92 Turbo Detroit Diesel Marine & Industrial Engines
Injector & Related Components for 16V92 Non- Turbo Detroit Diesel Marine & Industrial Engines
Injector & Related Components for 16V92 Turbo Detroit Diesel Marine & Industrial Engines
Periodic Inspection Recommendations
Routine monitoring and maintenance are vital for sustaining peak engine performance. Establishing a regular inspection schedule helps detect issues early and extend engine life.
1. Daily Checks for Detroit Diesel 92 Series Engines (6V92, 8V92, 12V92, 16V92)

1. Fluids
- Oil: Check level, wait 20 min after shutdown, inspect for leaks.
- Coolant: Verify level, check hoses for leaks/wear.
- Fuel: Keep full, drain water if needed.
2. Key Metrics
- Oil Pressure: 50-70 PSI; low = leaks or pump issues.
- Coolant Temp: 160-195°F; overheating = thermostat/pump problem.
- Exhaust Smoke: Black = excess fuel, White = coolant leak, Blue = oil burning.
3. Systems Check
- Air: Clean/replace filter, inspect turbo.
- Fuel: Check lines, injectors, pump for leaks.
- Lubrication: Inspect oil lines, filters, cooler.
4. Belts & Mounts
- Belts: Check for cracks/wear.
- Hoses: Inspect for leaks.
- Mounts: Look for excessive vibration.
5. Electrical
- Battery: Clean terminals, check connections.
- Alternator/Starter: Listen for issues, inspect belts/wiring.
2. Weekly Checks for Detroit Diesel 92 Series Engines (6V92, 8V92, 12V92, 16V92)
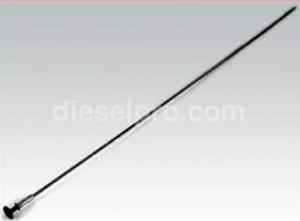
1. Belts, Hoses, and Filters
- Belts: Inspect for cracks, fraying, or looseness. Adjust or replace as needed to maintain proper tension and prevent slippage.
- Hoses: Check coolant and fuel hoses for swelling, cracks, or leaks. Ensure clamps are secure to avoid pressure loss or fluid leaks.
- Filters: Examine air, fuel, and oil filters for clogging or excessive dirt. Replace as necessary to ensure clean airflow, proper fuel delivery, and lubrication.
2. Air Intake System
- Filter Housing: Remove debris or obstructions in the intake system to prevent airflow restriction.
- Connections & Seals: Check for leaks or loose fittings that could allow unfiltered air into the engine, causing damage.
- Turbocharger (if equipped): Inspect for oil leaks, shaft play, or unusual noises indicating wear.
3. Battery & Electrical System
- Voltage Test: Use a multimeter to verify proper battery voltage (typically 12V or 24V, depending on system). Low voltage may indicate charging issues.
- Connections: Inspect battery terminals for corrosion and ensure all cables are tight. Clean if necessary to maintain strong electrical contact.
- Charging System: Check alternator function and belt condition to confirm the battery is receiving a charge during operation.
Performing these weekly checks ensures reliable engine operation and prevents minor issues from escalating into major failures.
3. Monthly Checks for Detroit Diesel 92 Series Engines (6V92, 8V92, 12V92, 16V92)

1. Test Fuel Injectors & Verify Timing
- Injector Performance: Inspect injectors for signs of wear, leaks, or carbon buildup. Symptoms of faulty injectors include rough idling, excessive smoke, or loss of power.
- Injector Calibration: Use a test bench or diagnostic tools to verify proper spray pattern and fuel atomization. Replace faulty injectors as needed.
- Timing Inspection: Ensure injector timing is set correctly to optimize combustion efficiency. Misaligned timing can lead to power loss, increased emissions, and poor fuel economy.
2. Clean or Replace Air & Fuel Filters
- Air Filter: Remove and inspect the air filter for dirt, debris, or blockages. If clogged, clean with compressed air or replace if excessively dirty. A restricted air filter can reduce engine performance and fuel efficiency.
- Fuel Filters: Replace both the primary fuel strainer and secondary fuel filter to ensure clean fuel reaches the injectors. Contaminated fuel can lead to injector clogging and engine misfires.
- Inspect Fuel Lines: Look for cracks, leaks, or loose connections that could introduce air into the system, affecting fuel delivery.
3. Check Turbocharger Performance & Inspect for Oil Leaks
- Turbo Functionality: Listen for excessive whistling or grinding noises that may indicate worn bearings. Check for proper boost pressure during operation.
- Oil Leaks: Inspect the turbocharger for oil leaks around the seals and connections. Oil in the intake or exhaust may indicate a failing turbo seal.
- Shaft Play: Manually check the turbo shaft for excessive movement. Too much side-to-side or in-and-out play could indicate impending turbo failure.
Regular monthly maintenance of these components ensures efficient fuel delivery, clean air intake, and proper turbocharger function, helping to maximize engine performance and longevity.
4. Annual Maintenance for Detroit Diesel 92 Series Engines (6V92, 8V92, 12V92, 16V92)
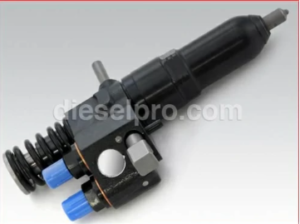
Best Practices for Performance Optimization
-
Follow Manufacturer Guidelines
- Adhere to recommended procedures and specifications for tuning and maintenance.
- Adhere to recommended procedures and specifications for tuning and maintenance.
-
Use Quality Components
- Replace worn parts with high-quality premium aftermarket components to enhance durability and performance.
- Replace worn parts with high-quality premium aftermarket components to enhance durability and performance.
-
Document Adjustments
- Maintain detailed records of tuning adjustments, inspections, and replaced components for future reference.
- Maintain detailed records of tuning adjustments, inspections, and replaced components for future reference.
-
Train Personnel
- Ensure operators and mechanics are trained in advanced tuning and calibration techniques.
- Ensure operators and mechanics are trained in advanced tuning and calibration techniques.
Conclusion
Optimizing the performance of Detroit Diesel 92 Series engines requires precise tuning, regular component inspections, and adherence to a strict maintenance schedule. By focusing on injector rack adjustments, valve clearance settings, and the performance of critical components like turbochargers and exhaust systems, operators can maximize efficiency, reduce wear, and extend the engine’s operational life. Implementing these practices ensures that these robust engines continue to perform reliably across all applications.
Parts Catalog for 6V92 Detroit Diesel Marine & Industrial Engines
Parts Catalog for 8V92 Detroit Diesel Marine & Industrial Engines
Parts Catalog for 12V92 Detroit Diesel Marine & Industrial Engines
Parts Catalog for 16V92 Detroit Diesel Marine & Industrial Engines