
Proper stopping procedures are essential for ensuring the longevity and reliability of Detroit Diesel 92 Series engines. By following controlled shutdown steps, adhering to emergency protocols, and performing post-run maintenance, operators can prevent unnecessary wear and identify potential issues early. This section provides detailed guidelines for safe and effective engine shutdown.
Parts Catalog for 6V92 Detroit Deisel Engines
Parts Catalog for 8V92 Detroit Deisel Engines
Parts Catalog for 12V92 Detroit Deisel Engines
Parts Catalog for 16V92 Detroit Deisel Engines
Normal Stopping Process

A gradual shutdown process minimizes mechanical stress and thermal shock to the engine, ensuring a smooth transition to an idle state before stopping.
1. Gradual Load Reduction
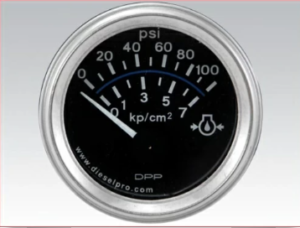
- Unload the Engine:
- Reduce the engine’s load incrementally, allowing it to operate at light or no load for 2–5 minutes.
- For marine engines, disengage the propeller or set the transmission to neutral.
- Why It’s Important:
- Gradual load reduction allows components such as turbochargers and pistons to cool evenly, preventing thermal stress.
- Gradual load reduction allows components such as turbochargers and pistons to cool evenly, preventing thermal stress.
2. Lowering RPM
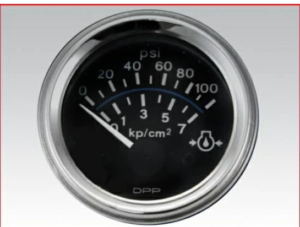
- Step-Down Procedure:
- Reduce engine speed to idle (600–650 RPM) before initiating shutdown.
- Avoid sudden drops in RPM to allow proper stabilization of oil pressure and coolant flow.
- Coolant Circulation:
- At idle, ensure the coolant continues to circulate to dissipate heat from critical components like the cylinder head and turbocharger.
- At idle, ensure the coolant continues to circulate to dissipate heat from critical components like the cylinder head and turbocharger.
3. Final Shutdown
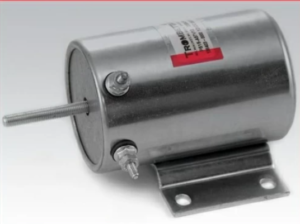
- Engine Stop Mechanism:
- Use the engine stop lever or switch to turn off the engine.
- Avoid using manual overrides or emergency shutoff valves for routine shutdowns.
Emergency Shutdown Protocols
In situations where immediate engine shutdown is necessary to prevent damage or danger, follow these emergency protocols:
1. Proper Use of Air Shutoff Valves
- Purpose:
- Air shutoff valves are designed to cut off airflow to the engine, halting combustion in emergencies such as runaway engines.
- Air shutoff valves are designed to cut off airflow to the engine, halting combustion in emergencies such as runaway engines.
- Activation:
- Pull the air shutoff lever or activate the switch, if equipped, to immediately starve the engine of air.
- Pull the air shutoff lever or activate the switch, if equipped, to immediately starve the engine of air.
- Reset Procedures:
- After activation, inspect the air intake system for obstructions or issues before resetting the valve.
- Ensure the valve is fully open and free of debris before attempting to restart the engine.
2. Emergency Scenarios
- Runaway Engine:
- Shut down immediately using the air shutoff valve to prevent over-revving and potential catastrophic failure.
- Shut down immediately using the air shutoff valve to prevent over-revving and potential catastrophic failure.
- Fire or Severe Overheating:
- Stop the engine and activate fire suppression systems if necessary. Avoid restarting until the cause is identified and resolved.
- Stop the engine and activate fire suppression systems if necessary. Avoid restarting until the cause is identified and resolved.
- Loss of Lubrication or Coolant:
- Shut down the engine if oil pressure drops below 10 psi or coolant temperature exceeds 210°F (99°C) to avoid severe damage.
- Shut down the engine if oil pressure drops below 10 psi or coolant temperature exceeds 210°F (99°C) to avoid severe damage.
Post-Run Maintenance
Post-run maintenance ensures the engine is in optimal condition for future use, reducing downtime and preventing cumulative wear.
1. Inspect for Leaks
- Cooling System:
- Inspect the radiator, heat exchanger, hoses, and connections for signs of coolant leaks.
- Inspect the radiator, heat exchanger, hoses, and connections for signs of coolant leaks.
- Lubrication System:
- Check for oil leaks around the oil pan, seals, and gaskets.
- Check for oil leaks around the oil pan, seals, and gaskets.
- Fuel System:
- Inspect fuel lines and connections for leaks or signs of wear.
- Inspect fuel lines and connections for leaks or signs of wear.
2. Adjust Fluid Levels
- Engine Oil:
- Measure the oil level using the dipstick and top off if necessary.
- Ensure the oil level is within the specified range to avoid overfilling.
- Coolant:
- Verify that coolant levels are adequate and refill as needed.
- Inspect for contamination or discoloration, indicating the need for a system flush.
3. Drain Condensation
- Air System:
- For engines with air compressors, drain condensation from air tanks to prevent moisture buildup that can corrode components.
- For engines with air compressors, drain condensation from air tanks to prevent moisture buildup that can corrode components.
- Fuel Filters and Water Separators:
- Drain accumulated water from fuel-water separators to ensure clean fuel delivery.
- Drain accumulated water from fuel-water separators to ensure clean fuel delivery.
4. Visual Inspection
- Belts and Hoses:
- Check for wear, cracks, or looseness in belts and hoses. Replace any components showing signs of failure.
- Check for wear, cracks, or looseness in belts and hoses. Replace any components showing signs of failure.
- Fasteners and Mountings:
- Inspect bolts, nuts, and engine mounts for tightness and alignment.
- Inspect bolts, nuts, and engine mounts for tightness and alignment.
5. Record Observations
- Maintenance Log:
- Document oil pressure, coolant temperature, and any anomalies during operation or shutdown.
- Include notes on fluid levels and any repairs made post-run.
Best Practices for Stopping Procedures
- Follow Routine and Emergency Protocols
- Use normal shutdown procedures whenever possible and reserve emergency protocols for critical situations.
- Use normal shutdown procedures whenever possible and reserve emergency protocols for critical situations.
- Prioritize Inspections
- Conduct thorough post-run inspections to identify potential issues before the next operation.
- Conduct thorough post-run inspections to identify potential issues before the next operation.
- Keep Tools Ready
- Have essential tools and spare parts on hand to address leaks or other maintenance needs promptly.
- Have essential tools and spare parts on hand to address leaks or other maintenance needs promptly.
- Maintain Logs
- Record shutdown and maintenance details to establish a history for trend analysis and troubleshooting.
- Record shutdown and maintenance details to establish a history for trend analysis and troubleshooting.
Conclusion
Following proper stopping procedures ensures the safe and efficient shutdown of Detroit Diesel 92 Series engines. By gradually reducing load and RPM, adhering to emergency protocols when necessary, and performing thorough post-run maintenance, operators can preserve engine integrity, prevent damage, and prepare the engine for its next use. These practices are critical for extending the life of the engine and maintaining reliable performance.
Parts Catalog for 6V92 Detroit Deisel Engines
Parts Catalog for 8V92 Detroit Deisel Engines
Parts Catalog for 12V92 Detroit Deisel Engines
Parts Catalog for 16V92 Detroit Deisel Engines