Guide To Tuning Up Your Detroit Diesel 71 Series Inline Engine
Parts For Detroit Diesel 271 Engines
Parts For Detroit Diesel 371 Engines
Parts For Detroit Diesel 471 Engines
Parts For Detroit Diesel 671 Engines
In this article we cover a basic tune up for a Detroit Diesel 71 Series inline engine. Your 71 series inline engine has no scheduled interval for performing an engine tune-up. As long as the engine’s performance is satisfactory, no tune up should be needed. Minor adjustments to the valve and injector operating mechanism, gover, etc should only be required periodically to compensate for normal wear and tear on parts.
The type of governor used depends on the engine applications. Since the application of the governor has different characteristics, the tune-up procedure varies accordingly. The following types of governors are used.
- Limiting speed mechanical
- Variable speed mechanical
The mechanical governor is identified by the plate attached to the governor housing. The D.W.-L.S. stamped name plate denotes a double-weight limiting speed governor. A single-weight variable speed governor name plate is stamped S.W.-V.S.
Normally, when performing a tune-up on an engine in service, it is only necessary to check various adjustments for a possible change in settings. However, if a cylinder head, governor, or injectors have been replaced or overhauled, then certain preliminary adjustments are required before the engine is started.
The preliminary adjustments consist of the first four items in the tune-up sequence. The procedures are the same except the valve clearance is greater for a cold engine.
Note: If a supplementary governing device such as a throttle delay mechanism is used, it must be disconnected prior to the tune-up. After the governor and the injector rack adjustments are completed, the supplementary governing device must be re-connected and adjusted.
To tune-up an engine completely, perform all of the adjustments in the applicable tune-up sequence given below after the engine has reached normal operating temperature. Since the adjustments are normally made while the engine is stopped, it may be necessary to run the engine between adjustments to maintain normal operating temperature.
Use new rocker cover gaskets after the tune up is completed.
Tune-Up Sequence for Mechanical Governor
Note: Before starting the engine after a speed control adjustment or after removal of the engine speed control adjustment or after removal of the engine governor cover, the serviceman must determine that the injector racks move to the no fuel position when the governor stop lever is placed in the stop position. Engine overspeed will result if the injector racks cannot be positioned at no-fuel with governor stop lever.
CAUTION: An overspeeding engine can result in engine damage which could result in personal injury.
- Adjusting the exhaust valve clearance
- Time the fuel injectors
- Adjust the governor gap
- Position the injector rack control levers
- Adjust the maximum no-load speed
- Adjust the idle speed
- Adjust the Belleville spring For “TT” horsepower
- Adjust the buffer screw
- Adjust the throttle booster spring (variable governor only)
- Adjust the supplementary governing device if used
Tune-Up Sequence For Hydraulic Governor
- Adjust the exhaust valve clearance
- Time the fuel injectors
- Position the injector rack control levers
- Adjust the governor linkage
- Adjust the load limit screw
- Compensation adjustment (PSG governors only)
- Adjust the speed drop
- Adjust the maximum no-load speed
Full notes about how to tune up your engine can be found in your service manual for Detroit Diesel 71 Series engine.
Service Manual For Detroit Diesel 271, 371, 471, 671
Valve Adjustments For Your 71 Series Engine
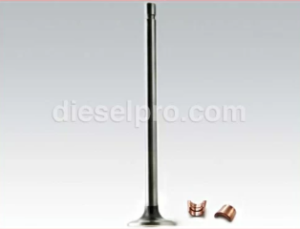
Engine valves regulate, control and direct the proper amount of air and fuel inside the engine’s combustion chamber for ignition to occur. Making sure your valves are properly calibrated is important for proper engine performance.
Two Valve Cylinder Heads
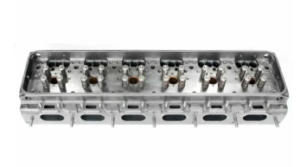
Valve Clearance Adjustment (Cold Engine)
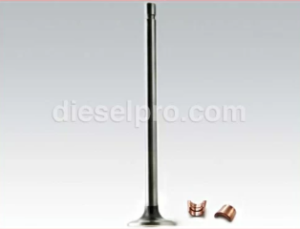
- Remove the loose dirt from the valve rocker cover and remove the cover.
- Place the governor speed control lever in the idle position. If a stop lever is provided, secure it in the stop position.
- Rotate the crankshaft, manually or with the starting motor, until the injector follower is fully depressed on the particular cylinder to be adjusted.
- Note: If a wrench is used on the crankshaft bolt at the front of the engine, do not turn the crankshaft in a left-hand direction of rotation because the bolt could loosen.
- Note: If a wrench is used on the crankshaft bolt at the front of the engine, do not turn the crankshaft in a left-hand direction of rotation because the bolt could loosen.
- Loosen the exhaust valve rocker arm push rod locknut.
- Place a .012” feeler gauge (J 9708-01) between the exhaust valve stem and the rocker arm. Adjust the push rod to obtain smooth pull on the feeler gage.
- Remove the feeler gage. Hold the push rod with a 5/16” wrench and tighten the locknut with a ½ “ wrench.
- Recheck the clearance. At this time if the adjustment is correct, the .011” feeler gage will pass freely between the valve stem and the rocker arm, but the .013” feeler gauge will not pass through. Readjust the push rod, if necessary.
Valve Clearance Adjustment (Hot Engine)
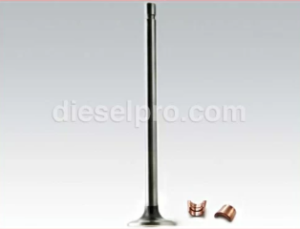
Note: it is not necessary to make a final hot engine exhaust valve clearance adjustment after a cold engine adjustment has been performed. However, if a hot engine adjustment is desired use the following procedure.
Maintaining normal engine operating temperature is particularly important when making the hot engine exhaust valve clearance adjustment. If the engine is allowed to cool before setting any of the valves, the clearance, when running at full load, may become insufficient.
Note: Since these adjustments are normally made when the engine is stopped, it may be necessary to run the engine between adjustments to maintain normal operating temperature.
- With the engine at normal operating temperature, set the exhaust valve clearance with feeler gage J 9708-01. At this time, if the valve clearance is correct, the .008” feeler gage will pass freely between the end of the valve stem and the rocker arm and the .010” feeler gage will not pass through. Readjust the push rod, if necessary.
- After the exhaust valve clearance has been adjusted, check the fuel injector timing.
Check Exhaust Valve Clearance Adjustment
- With the engine at 100 degrees fahrenheit ( 38 degrees celsius) or less, check the valve clearance.
- If a 0.012” feeler gage (plus or minus .004”) will pass between the valve stem and the rocker arm bridge, the valve clearance is satisfactory. If necessary, adjust the push rod.
Four Valve Cylinder Heads
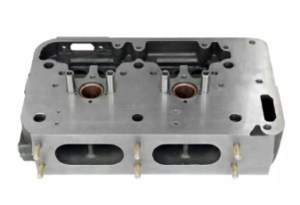
The exhaust valve bridges must be adjusted and the adjustment screws locked securely at the time the cylinder head is installed on the engine.
The exhaust valve bridge balance should be checked when a general adjustment is performed. After the bridges are balanced, adjust the valve clearance at the push rods only. Do not disturb the exhaust valve bridge adjusting screw.
All of the exhaust valves may be adjusted in firing order sequence during one full revolution of the crankshaft. Refer to the General Specifications at the front of your service manual for the engine firing order.
Valve Clearance Adjustment (Cold Engine)
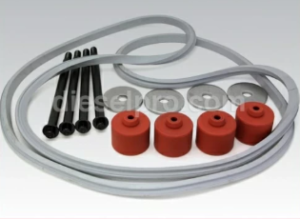
-
- Remove the loose dirt from the valve rocker cover and remove the cover.
- Place the governor speed control level in the idle speed position. If a stop lever is provided, secure it in the stop position.
- Rotate the crankshaft manually, or with the starting motor, until the injector follower is fully depressed on the particular cylinder.
- Note: If a wrench is used on the crankshaft bolt at the front of the engine, do not turn the crankshaft in a left-hand direction of rotation because the bolt could loosen.
- Loosen the exhaust valve rocker arm push rod locknut.
- Place a .016” feeler gage (J 9708-01) between the exhaust valve stem and the valve bridge adjustment screw (spring-loaded bridge only) or between the valve bridge and the valve rocker arm pallet (unloaded bridge only). Adjust the push rod to obtain a smooth pull on the feeler gage.
- Remove the feeler gage. Hold the push rod witha 5/16” wrench and tighten the locknut with a ½” wrench.
- Recheck the clearance at this time if the adjustment is correc the .015” feeler gage will pass freely between the valve stem and the adjusting screw (spring loaded bridge) or between the valve bridge and the rocker arm pallet (unloaded bridge), but the 0.017” feeler gage will not pass through. Readjust the push rod, if necessary.
- Check and adjust the remaining exhaust valves in the same manner as outlined above.
Valve Clearance Adjustment (Hot Engine)
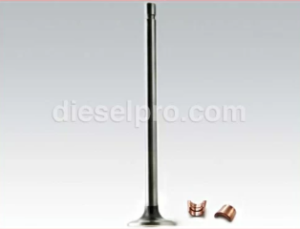
Note: It is not necessary to make final hot engine exhaust valve clearance adjustments after a cold engine adjustment has been performed. However, if a hot engine adjustment is desired use the following procedure.
Maintaining normal engine operating temperature is particularly important when making the hot engine exhaust valve clearance adjustment. If the engine is allowed to cool before setting any of the valves, the clearance, when running at full load may become insufficient.
Note: Since these adjustments are normally made while the engine is stopped, it may be necessary to run the engine between adjustments to maintain normal operating temperature.
- With the engine at normal operating temperature, set the exhaust valve clearance with feeler gage J9708-01. At this time, if the valve clearance is correct, the .013” gage will pass freely between the valve stem and the valve bridge adjusting screw (spring-loaded bridge) or between the value bridge and rocker arm pallet (unloaded bridge), but the .015” feeler gage will not pass through. Readjust the push rod, if necessary.
- After the exhaust valve clearance has been adjusted, check the fuel injector timing.
Check The Exhaust Valve Clearance Adjustment
- With the engine at 100 degrees fahrenheit (38 degrees celsius) or less, check the valve clearance.
- If the 0.016” feeler gage (plus or minus 0.004”) will pass between the valve stem and the rocker arm bridge, the valve clearance is satisfactory. If necessary, adjust the push rod.
Fuel Injector Timing For Your 71 Series Inline Engine

Injection timing, also called spill timing, is the moment when diesel fuel enters the cylinder during the combustion phase. When you adjust the timing, you can alter when the engine injects the fuel, therefore changing when combustion occurs.
To time an injector properly the injector follower must be adjusted to a definite height in relation to the injector body.
All of the injectors can be timed in firing order sequence during one full revolution of the crankshaft. Refer to your service manual and the General Specifications section at the front of the manual for engine firing order.
Time Fuel Injector
After the exhaust valve clearance has been adjusted, time the fuel injectors as follows.
- Place the governor speed control in the idle speed position. If a stop lever is provided, secure it in the stop position.
- Rotate the crankshaft, manually or with the starting motor, until the exhaust valve are fully depressed on the particular cylinder to be timed.
- Note: If a wrench is used on the crankshaft bolt at the front of the engine, do not turn the crankshaft in a left-hand direction of rotation or the bolt may be loosened.
- Note: If a wrench is used on the crankshaft bolt at the front of the engine, do not turn the crankshaft in a left-hand direction of rotation or the bolt may be loosened.
- Place the small end of the injector timing gage in the hole provided in the top of the injector body with the flat of the gage towards the injector follower.
- Loosen the injector rocker arm push rod locknut.
- Turn the push rod and adjust the injector rocker arm until the extended part of the gage will just pass over the top of the injector follower.
- Hold the push rod and tighten the locknut. Check the adjustment and, if necessary, readjust the push rod.
- Time the remaining injectors in the same manner as outlined above.
- If no further engine tune up is required, install the valve rocker cover, using a new gasket.
Limiting Speed For Your Mechanical Governor Of Your 71 Series Inline Engine
The following video posted on Youtube by user “adrossi85” is a great example of how to limit the speed for your mechanical governor for the 71 Inline series.
After adjusting the exhaust valves and timing the fuel injectors, adjust the limiting speed mechanical governor and the injector rack control levers.
Note: Before proceeding with the governor and injector rack adjustments, disconnect any supplementary governing device. After the adjustments are completed, reconnect and adjust the supplementary governing device.
Back out the external starting aid screw.
Note: On “TT” engines, back out the Belleville spring retainer nut until there is approximately 0.60” clearance between the washers and the retainer nut.
With the engine stopped and at normal operating temperature, adjust the governor gap as follows.
Caution: If the gap adjustment is made with the engine in the vehicle, it is suggested that the fan assembly be removed due to the closeness of the fan blades to the engine governor.
- Remove the governor high-speed spring retainer cover.
- Back out the buffer screw or fast idle cylinder until it extends ⅝” from the locknut.
- Start the engine and loosen the idle speed adjusting screw locknut to hold the adjustment.
Note: Current limiting speed governors used in turbocharged engines include a starting aid screw threaded into a boss on the governor housing.
-
- Stop the engine. Clean and remove the valve rocker cover, the governor cover and the lever assembly. Discard the gaskets.
- Remove the fuel rod from the differential lever and the injector control tube lever.
- Check the gap between the low-speed spring cap and the high-speed spring plunger with gage J 5407 (0.170”).
- Stop the engine. Clean and remove the valve rocker cover, the governor cover and the lever assembly. Discard the gaskets.
- Note: Be sure the external starting aid screw (if used) is back out far enough to make it ineffective when making this adjustment.
- If required, loosen the locknut and turn the gap adjusting screw until a slight drag is felt on the gage.
- Hold the adjusting screw and tighten the locknut.
- Recheck the gap, readjust if necessary.
- Install the fuel rod between the governor and injector control tube lever.
- Use a new gasket and install the governor and lever assembly.
With the engine stopped and at normal operating temperature, adjust the gap as follows:
Note: If the governor gap is to be made with the engine in the vehicle, it is suggested that the fan assembly be removed due to closeness of the fan blades to the engine governor.
- Remove the governor high-speed spring retainer cover.
- Back out the buffer screw until it extends approximately ⅝” from the locknut.
- Start the engine and loosen the idle speed adjusting screw locknut and adjust the iddle screw to obtain the desired engine idle speed. Hold the screw and tighten the locknut to hold the adjustment.
- Note: Current limiting speed governors used in turbocharged engines include a starting aid screw threaded into a boss on the governor housing.
- Note: Current limiting speed governors used in turbocharged engines include a starting aid screw threaded into a boss on the governor housing.
- Stop the engine. Clean and remove the valve rocker cover, the governor cover and lever assembly. Discard the gaskets.
- Remove the fuel rod from the differential lever and the injector control tube lever.
- Start and run the engine between 1100 and 1300 rpm by manual operation of the differential lever.
Note: Do not overspeed the engine.
- Check the gap between the low-speed spring cap and the high-speed spring plunger with a feeler gage. The gap should be 0.002” -0.004”. If the gap setting is incorrect, reset the gap adjusting screw.
- On governors without the starting aid screw, hold the gap adjusting screw and tighten the locknut.
- Recheck the gap with the engine operating between 1100 and 1300 rpm. Readjust if necessary.
- Stop the engine and install the fuel rod between the differential level and the control tube lever.
- Use a new gasket and install the governor cover and lever assembly.
Position Injector Rock Control Levers
The position of the injector racks must be correctly set in relation to the governor. Their position determines the amount of fuel injected into each cylinder and ensures equal distribution of the load.
Properly positioned injector rack control levers with the engines at full load will result in the following.
- Speed control lever at the maximum speed position.
- Governor low-speed gap closed.
- High-speed spring plunger on the seat in the governor control housing.
- Injector racks in the full-fuel position.
Note: When positioning the injector racks on an early engine equipped with a fuel modulator, be sure no interference is encountered from the fuel modulator. Loosen the fuel modulator lever (“U” bolt) and move the modulator lever along the injector control tube to avoid contact with the modulator cam or the adjacent cylinder head stud nut.
Adjust the No. 1 injector rack control lever first to establish a guide for adjusting the remaining injector rack control levers.
- Disconnect any linkage attached to the governor speed control lever.
- Turn the idle speed adjusting screw until ½” of the threads (12-14 threads) project from the locknut when the nut is against the high speed plunger. This adjustment lowers the tension of the low-speed spring so it can easily be compressed. This permits closing the low-speed gap without bending the fuel rods or causing the yield mechanism springs to yield or stretch.
Note: A false fuel rack setting may result if the idle speed adjusting screw is not backed out as noted above.
Injector racks must be adjusted so that the effort to move the throttle from the idle speed position to the maximum speed position is uniform. A sudden increase in effort can result from.
- Injector racks adjusted too tight, not allowing the speed control lever to reach the end of its travel.
- Binding of the fuel rod.
- Failure to back out the idle screw.
- Back out the buffer screw approximately ⅝” if it has not already been done.
- Loosen all of the inner and outer injector rack control lever adjusting screws or adjusting screws and locknuts. Be sure all the injector rack control levers are free on the injector control tube.
- Move the speed control lever to the maximum speed position. Hold the lever in that position with light finger pressure and proceed as follows:
Two screw assembly – Turn the inner adjusting screw on the No. 1 injector rack control lever down until a slight movement of the control tube is observed or a step-up in effort is noted. Tighten the screw approximately ⅛ of a turn more and lock securely with the adjusting screw locknut. This will place the No. 1 injector rack in the full-fuel position.
Note: Overtightening of the injector rack control lever adjusting screw during installation or adjustment can result in damage to the injector control tube. The recommended torque of the adjusting screws is 24-36 Lb-in (3-4 Nm).
The above step should result in placing the govenor linkage and control tube assembly in the same position that they will attain while the engine is running at full load.
- To be sure of the proper rack adjustment, hold the speed control lever in the maximum speed position and press down on the injector rack with a screwdriver or finger tip and note the “rotating” movement of the injector control rack when speed control lever is in the maximum speed position. Hold the speed control lever in the maximum speed position and, using a screwdriver, press downward on the injector control rack. The rack should tilt downward and when the pressure of the screwdriver is released, the control rack should “spring” back upward.
If the rack does not turn to its original position, it is too loose. To correct this condition with the Two Screw Assembly , back off the outer adjusting screw slightly and tighten the inner adjusting screw slightly. To correct this condition with the One Screw and Locknut Assembly, loosen the locknut and turn the adjusting screw clockwise a slight amount and retighten the locknut.
The setting is too tight if, when moving the speed control lever from the idle position, the injector rack becomes tight before the speed control lever reaches the end of its travel ( as determined by the stop under the governor cover). This will result in a step-up in effort required to move the speed control level to the end of its travel. To correct this condition with the Two Screw Assembly, back off the inner adjusting screw slightly and tighten the outer adjusting screw slightly. To correct this condition with the One Screw and Locknut Assembly loosen the locknut and turn the adjusting screw counter clockwise a slight amount and retighten the locknut.
7) To adjust the remaining injector rack control levers, remove the clevis pin from the fuel rod and the injector control tube lever. Hold the injector control racks in the full-fuel position by means of the lever on the end of the control tube, and proceed as follows.
Two Screw Assembly:
- Turn down the inner adjusting screw of the No. 2 injector until the injector rack has moved into the full-fuel position and the inner adjusting screw is bottomed on the injector control tube. Then, alternatively tighten both the inner and outer adjusting screws.
Note: Overtightening of the injector rack control lever adjusting screws during installation or adjustment can result in damage to the injector control tube. The recommended torque of the adjusting screws is 24-36 lb-in (3-4 Nm).
- Recheck the No. 1 injector rack to be sure that it has remained snug on the ball end of the injector rack control lever while adjusting the No. 2 injector. If the rack fo the No. 1 injector becomes loose, back off slightly on the inner adjusting screw on the No. 2 injector rack control lever and tighten the outer adjusting screw.
One Screw and Locknut Assembly
- Tighten the adjusting screw of the No. 2 injector rack control lever until the injector rack clevis is observed to roll up or an increase in the effort to turn the screwdriver is noted. Securely lock the adjusting screw locknut.
Note: Overtightening of the injector rack control tube lever adjusting screws during installation or adjustment can result in damage to the injector control tube. The recommended torque of the adjusting screws is 24-36 lb-in (3-4 Nm).
- Verify the injector rack of No. 1 as outlined in Step 6. If No 1 does not “spring” back upward, turn the No. 2 adjusting screw counterclockwise slightly until the No. 1 injector rack returns to its full-fuel position and secure the adjusting screw locknut. Verify proper injector rack adjustment for both No. 1 and No. 2 injectors. Turn clockwise or counterclockwise the No. 2 injector rack adjusting screw until both No. 1 and No. 2 injector racks are in the full-fuel position when the locknut is securely tightened.
When the settings are correct, the racks of both inspectors must be snug on the ball end of their respective rack control levers.
8) Position the remaining injector rack control levers as Outlined in Step 7.
9) Connect the fuel rod to the injector control tube lever.
10) Turn the idle speed adjusting screw until it projects 3/16” from the locknut to permit starting the engine.
Note: Remove the “C” clamp from the fuel rod on units equipped with a yield link.
11) On current turbocharged engines, adjust the external starting aid screw as follows:
- With the engine stopped, place the governor stop lever in the run position and the speed control lever in the idle speed position.
- Adjusting the starting aid screw to obtain the required setting between the shoulder on the injector rack clevis and the injector body. Select the proper gage and measure the setting at any convenient cylinder. When the starting aid screw is properly adjusted, the gage should have a small clearance of 1/64” in the space along the injector rack shaft between the rack clevis and the injector body.
- After completing the adjustment, hold the starting aid screw and tighten the locknut.
- Check the injector rack clevis-to-body clearance after performing the following:
- Position the stop lever in the run position.
- Move the speed control lever from the idle speed position to the maximum speed position.
- Return the speed control lever to the idle speed position.
Movement of the speed control lever is to take-up the clearance in the governor linkage. The injector rack clevis-to-body clearance can be increased by turning the starting aid screw farther in against the operating shaft lever or reduced by backing it out.
Note: The starting aid screw will be ineffective if the speed control lever is advanced toward wide open throttle during startup.
- Use a new gasket and replace the valve rocker cover.
Adjust Maximum No-Load Engine Speed
All governors are properly adjusted before leaving the factory. However if the governor has been reconditioned or replaced, and to ensure the engine speed will not exceed the recommended no-load speed as given on the option plate, set the maximum no-load speed as follows:
- Loosen the locknut and back off the high speed spring retainer approximately 5 turns.
- With the engine at operating temperature and no load on the engine, place the speed control lever in the full-fuel position. Turn the high speed spring retainer IN until the engine is operating at the recommended no-load speed. The best method of determining the engine speed is with an accurate tachometer.
- Holding the high-speed spring retainer and tighten the locknut.
Adjust Idle Speed
With the maximum no-load speed properly adjusted, adjust the idle speed as follows:
- Remove the spring housing to uncover the idle speed adjusting screw.
- With the engine at normal operating temperature and with the buffer screw back out to avoid contact with the differential lever, turn the idle speed adjusting screw until the engine is operating at approximately 15 rpm below the recommended idle speed.
- Hold the idle screw and tighten the locknut.
- Install the high-speed spring retainer and tighten the two bolts.
- For “TT” engines, refer to section 14.3.5 of your service manual for adjustment of the Belleville spring.
Adjust Buffer Screw
With the idle speed properly set, adjust the buffer screw as follows:
- With the engine running at normal operating temperature, turn the buffer screw in so it contacts the differential lever as lightly as possible and still eliminates engine roll.
Note: Do not increase the engine idle speed more than 15rpm with the buffer screw
- Recheck the maximum no-load speed. If it has increased more than 25 rpm, back off the buffer screw until the increase is less than 25 rpm.
- Hold the buffer screw and tighten the locknut.
Variable Speed Mechanical Governor Injector Rack Control Adjustment
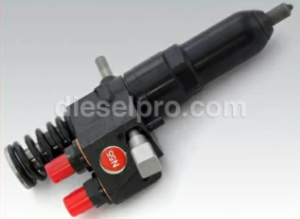
Adjust engines with variable speed mechanical governors after adjusting the exhaust valves and timing the fuel injectors.
Adjust Governor Gap
With the engine stopped, the governor gap may be set as follows:
- Remove the governor cover.
- Place the speed control lever in the FULL FUEL position.
- Insert a 0.006” feeler gage between the spring plunger and the plunger guide. If required, loosen the lock nut and turn the adjusting screw in or out until a slight drag is noted on the feeler gage.
- Hold the adjusting screw and tighten the lock nut. Check the gap, and reset it, if necessary.
- Install the governor cover.
Position Injector Rack Control Levers
The position of the injector control rack levers must be correctly set in relation to the governor. Their position determines the amount of fuel injected into each cylinder and ensures equal distribution of the load.
Properly positioned injector rack control levers with the engine at full load will result in the following:
Speed control lever at maximum speed position.
Stop lever in the RUN position.
High speed spring plunger is within 0.005” to 0.007” of its seat in the governor control housing.
Injector fuel control racks in the full fuel position.
NOTE: The cross link equalizer spring must be removed from multiple engine units before performing the individual engine tune-up.
Adjust the No. 1 injector rack control lever first, to establish a guide for adjusting the remaining injector rack control levers.
- Disconnect any linkage attached to the stop lever.
- Loosen the lock nut and back out the buffer screw.
- Loosen all the inner and outer adjusting screws. Be sure all the injector rack control levers are free on the injector control tubes.
- Move the speed control lever to the maximum speed position.
- Move the stop lever to the run position. Hold in that position with light finger pressure. Turn the inner adjusting screw of the No. 1 injector control lever down until a step up in effort is noted. This will place the No. 1 injector rack in the full fuel position. TUrn down the outer adjusting screw until it bottoms lightly on the injector control control tube. Then alternately tighten both the inner and outer adjusting screws.
NOTE: The above step should result in placing the governor linkage and control tube assembly in the same position that they will attain while the engine is running at full load.
- To be sure the control lever is properly adjusted, the following check should performed.
Hold the stop lever in the RUN position and press down on the injector rack with a screw driver or finger tip, causing the rack to rotate. The setting is sufficiently tight if the injector returns to its original position.
If the rack does not return to its original position, it is too loose. To correct, back off the outer adjusting screw slightly and tighten the inner adjusting screw slightly.
The setting is too tight if when moving the stop lever from the stop to the RUN position, the injector rack becomes tight before the stop lever reaches the end of its travel as determined by the stop under the governor cover. This will result in a step up in effort required to move the stop lever to the end of its travel. To correct this condition, back off the inner adjusting screw slightly and tighten the outer adjusting screw slightly.
- Manually hold the No. 1 injector rack in the full fuel position and turn down the inner adjusting screw of the No. 2 injector until the injector rack has moved into full fuel position and the inner adjusting screw is bottomed on the injector control tube. Turn the outer adjusting screw down until it bottoms lightly on the injector control tube. Then alternately tighten both the inner and outer adjusting screws until tight.
- Recheck the No. 1 injector rack to be sure that it has remained snug on the ball end of the rack control lever while positioning the No 2. Injector rack. If the rack of the No. 1 injector has become loose, back off slightly the inner adjusting screw on the No. 2 injector control lever. Tighten the outer adjusting screw.
- Position the remaining injector rack control levers as outlined in steps 7 and 8.
Adjust Maximum No Load Speed
The maximum no-load speed on engines equipped with variable speed governors must not be less than 125 rpm or more than 150 rpm above the recommended full load speed.
With a hand tachometer, determine the maximum no-load speed of the engine, then make the adjustments if required:
- Disconnect the booster.
- Remove the two bolts and withdraw the variable speed spring housing and the variable speed spring plunger from inside the spring housing.
- Refer to Table 1 . determine the stop or shim required for the desired full load speed for engines with two valve-cylinder heads.
- A split stop can only be used with a solid stop.
Table 1 – Series 71 Engine Two Valve Cylinder Heads
Full Load Speed | Stops | Shims |
1200 to 1425 rpm | 2 | Up to .325” |
1426 to 1825 rpm | 1 | Up to .325” |
1826 to 2100 rpm | 0 | Amount required to get necessary speed. |
Refer to Table to and determine the stops or shims required for the desired full-load speeds for engines with four valve cylinder heads.
Table 2 – Series 71 Engine Four Valve Cylinder Heads
Full Load Speed | Stops | Shims |
1450 to 1800 rpm | 2 | Amount required to get necessary speed. |
1801 to 2250 rpm | 1 | Amount required to get necessary speed. |
2251 to 2450 rpm | 0 | Amount required to get necessary speed. |
- Install the variable speed spring housing and recheck the maximum no-load speed.
- If required, add shims to obtain the necessary operating speed. For each 0.001” shim added the operating speed will increase approximately 1 rpm. Governor shims are available in 0.10” and approximately 0.078”.
NOTE: If the maximum speed no-load speed is raised or lowered more than 50 rpm by the installation or removal of the governor shims, the governor gap should be rechecked.
If readjustment of the governor gap is required, the position of the injector racks must be rechecked.
Adjust Idle Speed
With the maximum no-load speed properly adjusted, the idle speed may be adjusted as follows:
- Place the speed control lever in the idle position and the stop lever in the run position.
- With the engine running at normal operating temperature, back out the buffer screw to avoid contact with the differential lever.
- Loosen the lock nut and turn the idle speed adjusting screw until the engine is operating at approximately 15rpm below the recommended idle speed.
The recommended idle speed is 500-600rpm but may vary with the engine application.
- Hold the idle speed adjusting screw and tighten the lock nut.
Adjust Buffer Screw
With the idle speed set at approximately 15rpm below the recommended idle speed, the buffer screw may be set as follows:
- Turn the buffer screw in until the engine is operating at the recommended idle speed. Do not raise the engine speed more than 15 rpm with the buffer screw.
- Hold the buffer screw and tighten the lock nut.
Adjust Booster Spring
With the idle speed adjusted, the booster spring is adjusted as follows:
- Move the speed control lever to the idle speed position.
- Loosen the booster spring retaining nut on the speed control lever. Loosen the locknuts on the eyebolt at the opposite end of the spring.
- Move the spring retaining bolt in the slot of the speed control lever until the center of the bolt is on or slightly over the center (toward the idle speed position) of an imaginary line through the bolt, lever shaft and eyebolt. Hold the bolt and tighten the locknut.
- Start the engine and move the speed control lever to the maximum speed position and release it. The lever should not return to the idle speed position. If it does not reduce the booster spring tension. If it does continue to increase the spring tension. If it does not reduce the booster spring tension until the point it is reached where it will not return to idle. Then reduce the spring tension until the point is reached where it will not return to idle. Then reduce the spring tension until the lever does return to idle and tighten the lockouts on the eyebolt. This setting will result int he minimum force required to operate the speed control lever.
- Connect the linkage to the governor levers.
If the engine is equipped with a supplementary governing device adjust it at this time.
No patent liability is assumed with respect to the use of information contained in this blog post. While every precaution has been taken in preparation of this blog post, the author assumes no responsibility for errors and omissions. Neither is any liability assumed for damages resulting from the use of the information contained in this blog post.
All instructions, diagrams, videos have been checked for accuracy and ease of application; however success and safety in working with tools depend to a great extent upon individual accuracy, skill, and caution. For this reason, the authors are not able to guarantee the result of any procedure contained in this blog post. Nor can they assume responsibility for any damages to property or injury to persons occasioned from the procedures. Persons engaging in the procedures do so entirely at their own risk.
Parts For Detroit Diesel 271 Engines
Parts For Detroit Diesel 371 Engines
Parts For Detroit Diesel 471 Engines
Parts For Detroit Diesel 671 Engines