
Overview of the Cooling System
The cooling system is one of the most critical subsystems in Detroit Diesel V71 engines, designed to maintain optimal operating temperatures and prevent overheating. These engines operate in diverse applications, from industrial machinery to marine vessels, requiring different types of cooling systems to suit their environments. Efficient cooling not only extends engine life but also ensures consistent performance under varying workloads.
The cooling system’s primary goal is to dissipate the heat generated during combustion, keeping engine components within safe temperature limits. This is achieved through the circulation of coolant or raw water, depending on the application, across vital components like cylinder liners, heads, and oil coolers.
Types of Cooling Systems
Detroit Diesel V71 engines can be equipped with several types of cooling systems, depending on the application and environmental requirements. Each system has its unique configuration and advantages:
-
Radiator Cooling System
Radiator for Detroit Diesel 8V71 industrial engines.
- Commonly used in land-based applications such as construction equipment and industrial machinery.
- Features a closed-loop system where the coolant is circulated through the engine and cooled by air as it passes through the radiator.
- A fan assists in drawing air over the radiator, enhancing heat dissipation.
-
Heat Exchanger Cooling System
Heat Exchanger Tank for 6V71 and 8V71 Marine Engines
- Standard for marine engines where freshwater or antifreeze circulates through the engine and transfers heat to raw water via a heat exchanger.
- The heat exchanger prevents raw water, which often contains debris or corrosive elements, from coming into direct contact with internal engine components.
-
Keel Cooling System
- Used in marine applications where space constraints or specific operating conditions make heat exchangers impractical.
- Heat is transferred from the engine coolant to the surrounding water through external tubes or plates mounted along the vessel’s keel.
- This system eliminates the need for raw water pumps and reduces the risk of clogging or corrosion.
Key Components of the Cooling System
To effectively manage engine temperatures, the cooling system relies on several interconnected components:
- The heart of the cooling system, responsible for circulating coolant throughout the engine.
- Gear-driven centrifugal pumps are commonly used in V71 engines. These pumps are highly efficient and reliable.
-
Water Manifold
- Directs the flow of coolant through the cylinder liners, cylinder heads, and other engine components.
- Ensures even distribution of coolant to prevent localized overheating.
- Regulate coolant temperature by controlling the flow of coolant to the radiator or heat exchanger.
- Typically designed to open at a preset temperature (e.g., 170°F or 180°F), allowing coolant to circulate through the cooling system when the engine reaches operating temperature.
-
Radiator (Land Applications)
- Transfers heat from the coolant to the surrounding air.
- Includes a fan to enhance airflow and cooling efficiency. Radiators are made from corrosion-resistant materials like aluminum or copper for durability.
-
Raw Water Pump (Marine Applications)
Raw Water Pump For Detroit Diesel 671 , 6V71 , 8V71
- Draws seawater or lake water into the cooling system in heat exchanger or direct raw water-cooled setups.
- Equipped with flexible impellers that handle debris and sand, although regular inspection is necessary to prevent wear.
-
Heat Exchanger (Marine Applications)
Marine heat exchanger core for Detroit Diesel marine engine
- Facilitates heat transfer between the engine coolant and raw water, ensuring the engine operates within safe temperature limits.
- Includes tubes and baffles to maximize contact between the two fluids for efficient cooling.
Raw Water Pump Specifics for Marine Engines
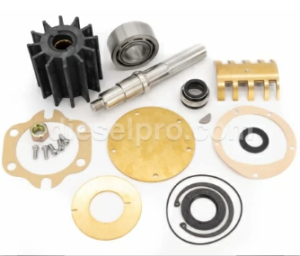
Marine engines require raw water pumps to bring in external water for cooling purposes. These pumps differ from standard water pumps in their design and maintenance requirements:
- Flexible Impeller Design: Raw water pumps use flexible rubber impellers to handle foreign objects like sand and small debris. The impeller’s flexibility prevents it from jamming but makes it susceptible to wear over time.
- Materials: Marine pumps are constructed with corrosion-resistant materials such as bronze or stainless steel to withstand exposure to saltwater.
- Common Failures: Impeller damage, clogged intake screens, and corrosion are common issues. Regular inspection and replacement of worn parts are essential.
Cooling System Maintenance Tips
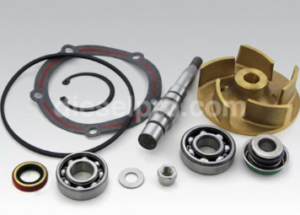
Proper maintenance of the cooling system is essential to ensure optimal performance and prevent engine damage. Follow these recommended procedures for routine care:
-
Draining and Flushing Procedures
For Radiator Systems:
- Draining:
- Allow the engine to cool completely before draining the coolant.
- Open the drain cock at the bottom of the radiator and the engine block to ensure complete removal of old coolant.
- Collect the drained coolant in a container for proper disposal, as it may contain hazardous materials.
- Flushing:
- Flush the system with clean water to remove sediment and rust. Use a flushing agent for stubborn deposits.
- Refill the system with a 50/50 mix of coolant and distilled water. This mix prevents freezing, boiling, and corrosion.
For Marine Heat Exchanger Systems:
- Draining:
- Open the raw water drain plugs on the heat exchanger and water pump. Ensure that all water is drained to prevent freezing in cold climates.
- Remove the heat exchanger end caps for thorough cleaning if necessary.
- Flushing:
- Backflush the heat exchanger with a solution of oxalic acid and water to remove scale and marine growth. Rinse thoroughly with fresh water.
- Inspect and replace zinc anodes to prevent galvanic corrosion.
For Keel Cooling Systems:
- Draining:
- Open the keel cooler drain valves and engine block drains. Allow gravity to remove all coolant.
- Ensure that the system is completely empty to avoid freezing in cold climates.
- Flushing:
- Flush the system with clean water to remove any sediment or contaminants.
- Refill the system with the appropriate antifreeze solution and bleed air from the system to ensure proper circulation.
-
Water Pump Maintenance
- Inspect the pump impeller regularly for wear or damage. Replace impellers at the first sign of cracking or deformation.
- Check the pump housing and seals for leaks. Worn seals can lead to coolant loss and air ingress, reducing pump efficiency.
- Torque the water pump mounting bolts to the specifications outlined in the service manual.
-
Thermostat Maintenance
- Remove and test thermostats periodically to ensure they open and close at the correct temperatures. A malfunctioning thermostat can cause overheating or undercooling.
- Replace thermostats with factory-approved parts to maintain precise temperature control.
- Clean the thermostat housing and inspect gaskets for leaks during reassembly.
-
Radiator Care (Land-Based Engines)
- Clean radiator fins regularly to remove dirt and debris that can block airflow. Use compressed air or a soft brush to prevent damage to the fins.
- Inspect hoses and clamps for wear and tightness. Replace any hoses showing signs of cracking or bulging.
- Use only the recommended coolant type to avoid scaling or corrosion in the radiator.
-
Heat Exchanger and Raw Water Pump Care (Marine Engines)
- Check raw water intake screens and strainers for blockages. Clean them regularly to ensure adequate water flow.
- Inspect and replace the flexible impeller of the raw water pump annually or more frequently in high-use environments.
- Remove the heat exchanger for a thorough cleaning during major service intervals. Replace corroded or damaged tubes and gaskets.
Troubleshooting Cooling System Issues
-
Overheating:
- Check for low coolant levels, clogged radiators, or malfunctioning thermostats.
- Inspect the water pump for leaks or impeller failure.
- Ensure proper belt tension on belt-driven pumps.
-
Coolant Leaks:
- Inspect hoses, clamps, and seals for damage. Replace worn or cracked components.
- Check for corrosion in the radiator, heat exchanger, or keel cooler.
-
Poor Cooling Efficiency:
- Flush and clean the cooling system to remove scale and sediment.
- Ensure thermostats and temperature sensors are functioning correctly.
Importance of Cooling System Maintenance
The cooling system plays a vital role in the performance and longevity of Detroit Diesel V71 engines. By following the recommended maintenance schedules and addressing issues promptly, operators can avoid costly repairs and downtime. Regular inspections, timely replacements, and proper cleaning procedures will ensure that these engines continue to perform at their peak, even in the most demanding environments.