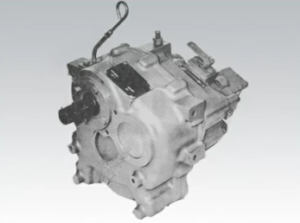
The Twin Disc MG502 Marine Gear is engineered for durability, efficiency, and reliability in demanding marine environments. However, to ensure optimal performance and extend the life of this critical component, it is essential to adhere to a rigorous maintenance schedule. Proper maintenance not only reduces the risk of unexpected failures but also minimizes downtime, increases operational efficiency, and extends the overall lifespan of the gearbox.
This comprehensive guide provides an in-depth 5000-word exploration of maintenance tasks categorized into daily, weekly, monthly, and seasonal checks, along with detailed guidelines on component life expectancy and replacement schedules.
Daily, Weekly, and Monthly Maintenance Tasks for Twin Disc MG502 Marine Gear
Implementing routine maintenance tasks ensures that the MG502 operates smoothly and remains free from common operational risks. Regular checks help in identifying and addressing minor issues before they escalate into significant problems.
Parts Catalog for Twin Disc MG502 Marine Transmissions
Rebuilt Twin Disc MG502 Marine Transmissions
Bearings For Twin Disc MG502 Marine Transmissions
Plate Kit For Twin Disc MG502 Marine Transmission
Gasket Kits For Twin Disc MG502 Marine Transmission
Daily Maintenance Tasks
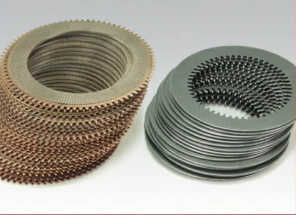
Daily maintenance is essential for detecting immediate issues that could compromise the gearbox’s operation. These tasks should be performed before and after each voyage to ensure reliability.
-
Visual Inspection
- Inspect for Leaks: Check around the gearbox housing, seals, and hydraulic lines for signs of oil or fluid leaks.
- Look for Loose Fasteners: Ensure that all external fasteners and bolts are secure.
- Check for Wear or Damage: Inspect external components for visible signs of damage, such as dents or corrosion.
-
Fluid Level Checks
- Gearbox Oil: Confirm that oil levels are within the manufacturer’s recommended range. Top up if necessary.
- Hydraulic Fluid: Ensure that hydraulic fluid levels are adequate for clutch engagement.
- Coolant Levels: For systems using integrated oil coolers, check the coolant levels.
-
Noise and Vibration Monitoring
- Listen for Abnormal Sounds: Start the gearbox and listen for any grinding, knocking, or whining noises.
- Feel for Vibration: Check for unusual vibrations that could indicate misalignment or component wear.
-
Operational Testing
- Check Gear Engagement: Test clutch engagement and gear shifting to ensure smooth transitions.
- Monitor Hydraulic Pressure: Confirm that hydraulic pressure meets operational standards.
Weekly Maintenance Tasks
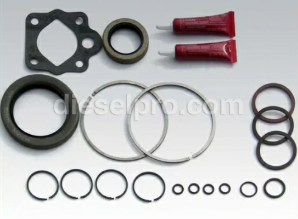
Weekly maintenance focuses on slightly deeper inspections to catch early signs of wear and stress within the gearbox system.
-
Lubrication Checks
- Inspect Oil Quality: Look for any discoloration, unusual smells, or signs of contamination in the gearbox oil.
- Grease Bearings: Apply marine-grade grease to bearings if applicable.
-
Fastener Integrity
- Torque Check: Use a torque wrench to ensure fasteners are tightened according to specifications.
- Check Seals: Inspect seals and gaskets for signs of early wear or cracking.
-
Hydraulic System Testing
- Pressure Test: Conduct a hydraulic pressure test to ensure consistent pressure levels.
- Inspect Hydraulic Lines: Look for blockages, leaks, or wear in the hydraulic hoses and connections.
-
Cleaning External Surfaces
- Remove Salt and Debris: Wash the gearbox housing with fresh water to remove salt deposits, dirt, and other contaminants.
Monthly Maintenance Tasks
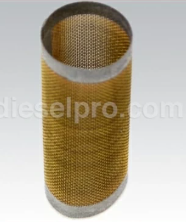
Monthly maintenance tasks are more detailed and involve partial disassembly and in-depth inspections to ensure the long-term health of the gearbox.
-
Fluid System Maintenance
- Oil Sampling and Analysis: Take an oil sample and send it for analysis to detect contaminants such as metal particles or water intrusion.
- Replace Oil Filters: Change oil and hydraulic filters to ensure clean fluid circulation.
-
Detailed Inspection of Components
- Inspect Gears: Visually check the condition of gear teeth for pitting, wear, or deformation.
- Check Bearings for Wear: Rotate and inspect bearings for smoothness, ensuring there is no roughness or noise.
- Assess Shaft Alignment: Use alignment tools to confirm proper shaft alignment.
-
Control System Testing
- Test Control Levers and Linkages: Ensure that controls are responsive and free from binding.
- Inspect Cables for Wear: Check all cables for fraying or corrosion.
-
Cleaning and Lubrication
- Flush and Refill Fluids: If oil or hydraulic fluids show signs of contamination, flush the system and replace the fluids.
- Lubricate Moving Components: Apply grease or oil to joints, bearings, and critical contact points.
Seasonal Checks for Marine Environments
Seasonal maintenance ensures that the gearbox is prepared for the challenges of specific marine conditions, such as temperature extremes, saltwater corrosion, or extended periods of inactivity.
1. Pre-Season Maintenance (Before Launch)
- Full System Inspection: Conduct a comprehensive inspection of the entire gearbox system, including gears, shafts, seals, and housings.
- Oil and Fluid Replacement: Replace all oils and hydraulic fluids to eliminate any contaminants from previous seasons.
- Seal and Gasket Inspection: Replace any seals or gaskets that show signs of wear or cracking.
- Coolant System Check: Inspect oil coolers and coolant systems for blockages, corrosion, or leaks.
- Lubricate Components: Apply fresh lubrication to all bearings, gears, and hydraulic components.
2. Mid-Season Maintenance
- Visual Inspection: Check for early signs of wear or corrosion, especially after heavy use or long voyages.
- Fluid Analysis: Take an oil sample to detect potential contaminants or early wear.
- Clean Cooling Systems: Ensure that oil coolers are free from debris or blockages that could compromise performance.
- Test Clutch Engagement: Ensure the clutch system is operating smoothly without delay or slipping.
3. Post-Season Maintenance (Before Storage)
- Thorough Cleaning: Clean all external components to remove salt, grime, and contaminants.
- Flush Systems: Completely flush oil and hydraulic systems to remove contaminants.
- Dry Storage Preparation: Apply rust inhibitors to metal surfaces and components.
- Seal Protection: Apply a light coat of oil to seals and gaskets to prevent cracking during dry storage.
- Cover and Store: Use waterproof covers to protect the gearbox from dust and moisture.
Component Life Expectancy and Replacement Guidelines for Twin Disc MG502 Marine Gear
Understanding the life expectancy of critical components helps in planning proactive maintenance and avoiding unexpected failures.
1. Bearings

- Life Expectancy: Bearings generally last between 3,000 to 5,000 operational hours, depending on operating conditions.
- Replacement Guidelines:
- Replace bearings that feel rough, produce noise, or show signs of corrosion.
- Perform scheduled inspections every 1,000 operational hours.
2. Seals and Gaskets
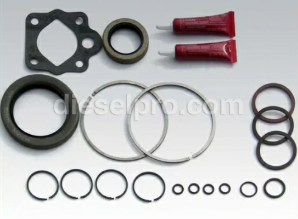
- Life Expectancy: Typically, seals and gaskets last 2 to 3 years in harsh marine environments.
- Replacement Guidelines:
- Replace seals showing signs of hardening, cracking, or leaking.
- Inspect gaskets during every oil change and replace if compressed or deteriorated.
3. Hydraulic Hoses and Fittings
- Life Expectancy: Hydraulic hoses can last between 3 to 5 years, but environmental conditions can reduce this lifespan.
- Replacement Guidelines:
- Inspect hoses for cracks, bulges, or leaks every 6 months.
- Replace hoses showing visible wear or signs of brittleness.
4. Clutch Plates
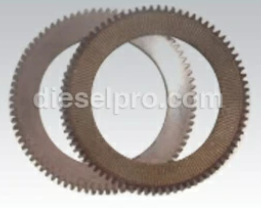
- Life Expectancy: Clutch plates typically last 4,000 to 5,000 operational hours, depending on usage.
- Replacement Guidelines:
- Replace plates that show warping, excessive scoring, or uneven wear.
- Inspect plates during annual maintenance or when engagement issues arise.
5. Gear Sets
- Life Expectancy: Gear sets can last over 10,000 operational hours with proper lubrication and maintenance.
- Replacement Guidelines:
- Replace gears with visible pitting, cracked teeth, or irregular wear.
- Inspect gear backlash and adjust if necessary.
6. Lubrication Systems
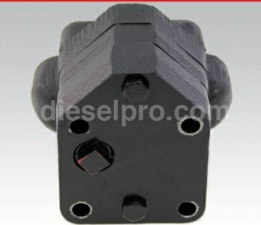
- Life Expectancy: Pumps and lubrication lines can last 5 to 7 years but should be inspected regularly.
- Replacement Guidelines:
- Replace lubrication pumps that fail pressure tests or show reduced flow rates.
- Inspect oil filters every 500 hours and replace if clogged or dirty.
Conclusion
Regular and comprehensive maintenance is crucial for ensuring the longevity, reliability, and efficiency of the Twin Disc MG502 Marine Gear. By adhering to the detailed daily, weekly, monthly, and seasonal maintenance schedules, operators can significantly reduce the risk of unexpected failures and costly downtime.
Key Takeaways:
- Daily Checks: Focus on visual inspections, fluid levels, and immediate operational concerns.
- Weekly Maintenance: Conduct deeper inspections of lubrication systems and check for early signs of wear.
- Monthly Tasks: Include thorough inspections of critical components, lubrication replacement, and testing.
- Seasonal Maintenance: Prepare the gearbox for environmental extremes and long-term storage.
- Component Replacement Guidelines: Replace critical components based on usage hours and condition assessments.
By following this comprehensive maintenance schedule, marine operators can maximize the operational life of the MG502, ensuring reliable service and minimizing repair costs.
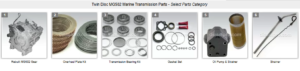
Rebuilt Twin Disc MG502 Marine Transmissions
Bearings For Twin Disc MG502 Marine Transmissions
Plate Kit For Twin Disc MG502 Marine Transmission
Gasket Kits For Twin Disc MG502 Marine Transmission
Videos About Twin Disc Transmissions
6 Reasons Your Twin Disc Transmission Has Low Oil Pressure
7 Reasons Your Twin Disc Transmission Is Overheating
3 Reasons Your Clutch Plates in Your Twin Disc Transmission Are Making Excessive Noise
Bull Gear On A Twin Disc Transmission
Rebuilt Twin Disc Transmissions