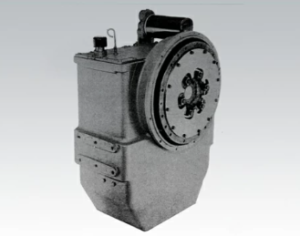
Introduction
The Twin Disc MG516 and MG5161 marine transmissions are engineered for high torque output and continuous-duty marine propulsion. While the gears and clutches inside the transmission are ruggedly built, their performance and longevity depend heavily on one critical system: the cooler and oil circulation system.
Every component in the MG516 relies on oil—not only for lubrication but also for hydraulic actuation and thermal management. Without proper cooling, transmission fluid degrades, clutches overheat, and internal clearances shift due to thermal expansion, leading to wear or failure.
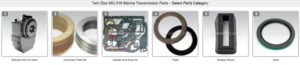
Parts Catalog for Twin Disc MG516 Marine Transmissions
Rebuilt Twin Disc MG516 Marine Transmissions
Plate Kit For Twin Disc MG516 Marine Transmission
Gasket Kits For Twin Disc MG516 Marine Transmission
This detailed guide covers:
- How the oil circulation system works in the MG516
- How to inspect and flush the heat exchanger (cooler)
- Step-by-step instructions for oil flow testing and pressure verification
- Symptoms of cooling system problems
- Best practices to prevent overheating and oil starvation
Disclaimer: Always refer to the OEM Twin Disc manual for your model and gear ratio when performing service. This guide is intended to support safe, thorough, and professional marine transmission maintenance.
Overview of the MG516 Oil Circulation and Cooling System
The MG516 transmission integrates a circulating oil system that powers hydraulic shifting, lubricates gear meshes, and removes heat from friction components. It is a closed-loop system, drawing oil from the sump and returning it after passing through a cooler and filter.
Key Components:
- Engine-driven oil pump (internal)
- Oil pickup and internal passages
- Spin-on or cartridge oil filter
- External oil cooler / heat exchanger
- Oil return line to housing
- Hydraulic control valve body
- Clutch lubrication ports and galleries
- Oil sight glass and drain plug
How Oil Flows Through the MG516 System
- Oil Pump Intake: The internal pump draws oil from the bottom of the transmission sump.
- Oil Pressurization: Oil is routed under pressure to the control valve body.
- Clutch Actuation and Lubrication: Oil is split between hydraulic actuation and lubrication lines.
- Cooler Circuit: Hot oil is sent to the cooler via the external line.
- Heat Exchange: Seawater or freshwater absorbs heat from the transmission oil.
- Return to Transmission: Cooled oil is returned to the case and reused.
Heat Exchanger Inspection for Twin Disc MG516 Marine Gear
The transmission cooler is typically a shell-and-tube or stacked-plate heat exchanger, mounted between the transmission and the vessel’s raw water or closed-loop cooling circuit.
A clogged, leaking, or corroded cooler can result in:
- Overheated oil
- Burned clutch plates
- Seal failure
- Foaming or air contamination
- Complete loss of propulsion under load
When to Inspect or Service the Heat Exchanger
Condition | Action |
Every 250 hours | Visual inspection and cleaning |
Every 1,000 hours | Full flushing and performance check |
Overheat symptoms | Immediate disassembly and inspection |
Dirty oil or cooler clog | Flush or replace unit |
Leaks in housing | Replace cooler or tubeset |
Tools and Supplies Needed
- Cooler flushing tool or pressure washer
- Fresh water or descaling solution
- Brushes for tube cleaning
- Inspection mirror and flashlight
- Temperature gun or infrared scanner
- Nitrile gloves and eye protection
- New gaskets or O-rings
- Torque wrench
- Oil drain pan
- Digital thermometer or flow sensor (optional)
Inspection Procedure: External and Visual
- Locate the Transmission Cooler
- Typically mounted near or beside the transmission
- Connected by two hydraulic hoses (input and return)
- Check Hoses and Fittings
- Look for signs of chafing, bulging, or leaking
- Replace cracked or dry-rotted hoses
- Inspect Mounting Brackets
- Ensure cooler is mounted securely to avoid vibration fatigue
- Ensure cooler is mounted securely to avoid vibration fatigue
- Check for External Corrosion
- Surface pitting, rust, or paint loss could indicate deeper issues
- Use marine-rated anti-corrosion spray after inspection
- Check for Water Leaks
- Salt crust or staining on or around the cooler body is a red flag
- Leaking seawater or freshwater into the oil side causes emulsified oil (milky appearance)
Disassembly and Internal Cleaning
- Drain Transmission Oil
- Fully drain oil before disconnecting cooler lines to prevent spillage
- Fully drain oil before disconnecting cooler lines to prevent spillage
- Disconnect Lines and Remove Cooler
- Mark hose orientation to prevent reverse installation
- Cap hoses or ports to avoid contamination
- Open the Cooler (if serviceable)
- Remove end caps to access tubes (shell-and-tube types)
- Remove gasket and inspect seating surface
- Inspect for Blockage or Debris
- Shine a light through the tubes—any obstruction must be cleared
- Look for barnacle growth, calcium, or sludge buildup
- Flush Tubes with Cleaner or Water
- Use marine-safe descaler (like Rydlyme or Barnacle Buster)
- Brush manually or power flush using a cooler flushing gun
- Inspect for Internal Leaks
- Pressurize seawater side to 20–30 PSI
- Submerge in water to detect air bubbles (indicates breach)
- Clean and Reassemble
- Replace O-rings, torque end caps evenly, reinstall hoses
- Fill system and run engine while monitoring temperature
Oil Flow Testing for Twin Disc MG516 Marine Gear
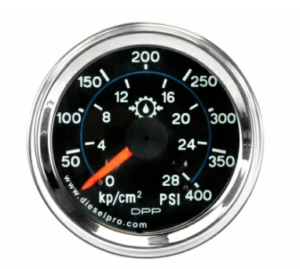
The MG516 relies on correct oil flow to engage clutches, lubricate components, and regulate operating temperature. Inadequate flow leads to low pressure, overheating, and rapid wear.
When to Perform an Oil Flow Test
- After new cooler installation
- After overheating or slipping gears
- During annual maintenance
- When oil pressure is low or fluctuates
- As part of transmission rebuild testing
Tools You’ll Need
- Oil flow meter (gallon or liter per minute)
- Flow direction adapters and hoses
- Hydraulic pressure gauge
- Stopwatch or timer
- Oil catch container
- Thermometer (infrared or probe)
- PPE: gloves, goggles
Flow Test Locations (MG516)
- Cooler inlet hose: Measure pump output before heat exchange
- Cooler outlet hose: Measure flow after cooling
- Test port: Verify clutch pressure (see hydraulic section)
Acceptable Flow Rates (Typical)
RPM | Flow Rate (GPM) |
Idle (600–700 RPM) | 2–3 GPM |
Operating (1,800 RPM) | 5–7 GPM |
Max load (2,100 RPM) | 7–10 GPM |
Values may vary by transmission ratio. Always consult Twin Disc specifications for your gear.
Oil Flow Testing Procedure
- Warm Up Transmission
- Run engine for 15 minutes to bring oil to 160°F (71°C)
- Run engine for 15 minutes to bring oil to 160°F (71°C)
- Shut Down and Connect Flow Meter
- Insert meter in series at cooler inlet or outlet
- Secure fittings tightly; use sealant as needed
- Restart Engine and Monitor
- Observe flow rate on meter while in neutral, forward, and reverse
- Note RPM and corresponding GPM
- Test Oil Temperature
- Use IR gun on inlet/outlet hose to verify cooling delta (ideally 10–30°F drop)
- Use IR gun on inlet/outlet hose to verify cooling delta (ideally 10–30°F drop)
- Compare to Spec
- If flow is <3 GPM at idle or <5 GPM at cruise RPM, proceed with diagnostics
Diagnosing Poor Oil Flow
Symptom | Possible Cause |
Low flow at all RPM | Worn oil pump or cavitation |
Low flow after cooler | Internal blockage or kinked line |
Hot oil, normal flow | Cooler failure or seawater blockage |
Foamy oil | Air ingress from suction side or cooler leak |
Flow drops at load | Filter restriction, pump bypassing |
Corrective Actions
- Replace clogged filter
- Check oil level and refill if needed
- Flush or replace cooler
- Replace oil pump or internal bypass valve
- Inspect pickup screen in sump for obstruction
- Replace kinked or collapsed hoses
Preventative Cooling System Maintenance Tips
- Use Quality Oil Filters
- Low-micron filters protect pump and passages
- Low-micron filters protect pump and passages
- Change Oil at Recommended Intervals
- Contaminated oil raises cooler load and decreases flow
- Contaminated oil raises cooler load and decreases flow
- Flush Coolers Annually
- Salt and growth reduce heat transfer efficiency
- Salt and growth reduce heat transfer efficiency
- Check Cooler Water Source
- Closed loop systems should be serviced separately
- Raw water should be filtered and descaled
- Log Temperature Trends
- Track inlet and outlet temps to catch early signs of reduced cooling
- Track inlet and outlet temps to catch early signs of reduced cooling
Warning Signs of Cooling System Trouble
- Oil temp exceeds 200°F (93°C) under normal load
- Oil pressure drops after warm-up
- Foamy, milky, or discolored oil
- Transmission slips after heavy use
- Gear housing unusually hot to the touch
- Audible whining or chatter from clutch area
Case Studies and Field Examples
Case Study 1: Trawler with Intermittent Overheating
Symptoms: Oil temp fluctuated between 180°F and 230°F on long runs
Diagnosis: Cooler had partial internal blockage from zinc corrosion
Solution: Cooler disassembled and flushed, zinc replaced
Result: Temps stabilized at 185°F under continuous load
Case Study 2: Charter Vessel with Low Flow at Idle
Symptoms: Transmission slipped when docking
Findings: Flow rate only 1.2 GPM at idle
Root Cause: Collapsed return hose from cooler
Fix: Replaced hose, flushed system, pressure returned to spec
Final Checklist for Cooling System Service
✅ Cooler flushed and internally cleaned
✅ All hoses pressure tested and secure
✅ Flow meter readings within Twin Disc tolerances
✅ No external or internal leaks
✅ Filter replaced and oil topped off
✅ Oil temp drop verified at outlet
✅ Transmission operates smoothly under all conditions
Summary: Cooling and Oil Circulation System for MG516 Marine Gear
The cooler and oil circulation system of the Twin Disc MG516 is a core part of the transmission’s functionality. If oil cannot flow and cool properly, even the toughest-built marine gears will suffer wear, pressure loss, or thermal failure.
By routinely inspecting and flushing the heat exchanger, performing oil flow tests, and correcting pressure drops before symptoms appear, you can:
- Prevent clutch failure and gear scoring
- Extend the life of hydraulic components
- Avoid costly mid-season overhauls
- Maintain high performance under load
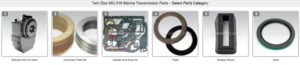
Rebuilt Twin Disc MG516 Marine Transmissions
Plate Kit For Twin Disc MG516 Marine Transmission
Gasket Kits For Twin Disc MG516 Marine Transmission
Videos About Twin Disc Transmissions
6 Reasons Your Twin Disc Transmission Has Low Oil Pressure
7 Reasons Your Twin Disc Transmission Is Overheating
3 Reasons Your Clutch Plates in Your Twin Disc Transmission Are Making Excessive Noise
Bull Gear On A Twin Disc Transmission
Rebuilt Twin Disc Transmissions