
The cylinder block is the foundational structure of the Detroit Diesel 53 Series engines, responsible for housing and supporting critical components like the crankshaft, pistons, and cylinder liners. Proper maintenance of the cylinder block is essential to ensure engine reliability and performance. This includes thorough cleaning, meticulous inspection, and rigorous pressure testing to identify cracks or weaknesses.
Parts Catalog for 353 Detroit Diesel Marine Engine
Parts Catalog for 453 Detroit Diesel Marine Engine
Parts Catalog for 6V53 Detroit Diesel Marine Engine
Parts Catalog for 8V53 Detroit Diesel Marine Engine
Cleaning the Cylinder Block
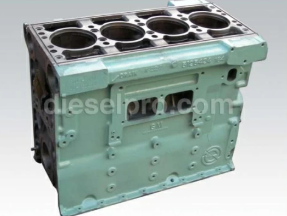
Overview: Cleaning the cylinder block is a vital step during engine maintenance and rebuilds. It removes contaminants like carbon deposits, oil residues, and rust, ensuring that the surfaces are prepared for inspection and reassembly. Proper cleaning methods enhance the longevity and efficiency of the engine by eliminating materials that could cause wear or obstruction.
Cleaning Process:
-
Initial Cleaning:
- Remove external grime and debris using a steam cleaner or solvent. Ensure the block is free from loose dirt before deeper cleaning begins.
- Use a high-pressure water spray or air blower to dislodge stubborn dirt from crevices.
-
Removal of Plugs:
- Remove all plugs (except cup plugs) to expose oil and coolant passages for cleaning. This step ensures thorough cleaning of internal cavities.
- Remove all plugs (except cup plugs) to expose oil and coolant passages for cleaning. This step ensures thorough cleaning of internal cavities.
-
Chemical Cleaning:
- Immerse the cylinder block in a heated solvent tank containing a commercial heavy-duty cleaning solution. Maintain the temperature between 180–200°F (82–93°C) to maximize the cleaning efficacy.
- Allow the block to soak for sufficient time to loosen oil residues and other deposits.
-
Mechanical Scrubbing:
- Use wire brushes and scrapers to clean gasket surfaces and remove stubborn deposits from hard-to-reach areas like oil galleries and water jackets.
- Pay special attention to areas with carbon build-up, as these can hinder proper inspection later.
-
Air Box and Oil Passage Cleaning:
- Use a 0.020-inch wire to clean jets and small passages, ensuring no blockage remains in oil and air systems.
- Use a 0.020-inch wire to clean jets and small passages, ensuring no blockage remains in oil and air systems.
-
Final Rinse and Drying:
- Rinse the block thoroughly with hot water to remove any remaining cleaning solution or debris.
- Dry the block with compressed air, ensuring all internal passages are free from moisture.
Safety Measures During Cleaning:
- Wear protective gear such as gloves, goggles, and an apron to guard against chemical burns or steam scalding.
- Avoid using compressed air above 40 psi to prevent injury or damage to the block.
Importance of Rust Prevention:
- Immediately after drying, coat the block with a light layer of rust-preventive oil, especially if reassembly will not occur promptly.
Inspection of the Cylinder Block
Once the cleaning process is complete, the cylinder block must be carefully inspected to identify wear, damage, or defects. This step is critical to assess whether the block is fit for reuse or requires repair or replacement.
Key Areas of Inspection:
The video above features cylinder blocks for Detroit Diesel 6V53 Engines. The cylinder blocks were removed from core engines and sent to the machine shop for cleaning, pressure testing and any machining needed in order to bring them back to standard condition. In some cases the blocks may require additional machining and in that case the blocks will be considered oversized which if often classified as standard oversize 10, oversize 20 and oversize 30 with increasing numbers meaning that the machine shop had to remove additional metal in order to get the blocks into a uniform condition. The measurements of 10, 20, and 30 refer to ten thousands of an inch removed twenty thousands and thirty thousands respectively with thirty thousands is being the end of the road for how much you really can cut out of an engine block. These standardadized measurements will help you to determine what type of cylinder liner will fit in the new machined block.
-
Visual Inspection:
- Examine the block for visible cracks, erosion, or scoring.
- Check for pitting or rust, particularly in water jackets and oil passages.
-
Dimensional Checks:
- Measure cylinder bores for wear, taper, and out-of-round conditions using a dial bore gauge or inside micrometer.
- Verify that bore diameters fall within the specified tolerances for standard or oversized liners. For instance:
- Maximum bore diameters for reuse: 4.5235 inches at position A, 4.4900 inches at position B.
- Taper and out-of-round should not exceed 0.0015 inches.
-
Counterbore Inspection:
- Inspect the counterbores for the cylinder liners to ensure they are clean, smooth, and dimensionally accurate.
- Depth specifications should range between 0.300 to 0.302 inches with no more than 0.0015-inch variance across the circumference.
-
Main Bearing Bores:
- Measure main bearing bores with caps in place. Proper alignment ensures smooth crankshaft operation.
- Acceptable bore diameters for inline engines: 3.251 to 3.252 inches; for V-type engines: 3.751 to 3.752 inches.
-
Threaded Holes and Machined Surfaces:
- Inspect all threaded holes for damage or debris. Repair threads with a tap or install helical inserts if necessary.
- Remove any burrs or nicks on machined surfaces to ensure proper sealing during assembly.
Handling Cracked Blocks:
- Replace blocks exhibiting significant cracks, particularly around water transfer holes and bolt holes.
- Minor cracks may be repaired, but this should only be attempted by experienced machinists using approved welding or sealing techniques.
Pressure Testing the Cylinder Block for Cracks
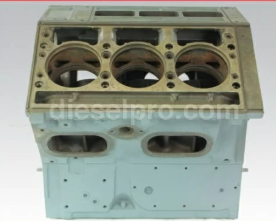
Pressure testing is a non-negotiable step in assessing the integrity of the cylinder block. It ensures there are no cracks or leaks in the water jacket, oil passages, or cylinder walls that could compromise engine performance.
Testing Methods:
- Preparation:
- Install cylinder liners with new seal rings to simulate normal operating conditions.
- Use steel plates with rubber gaskets to seal the top surface and water inlet openings of the block.
-
Method A: Submersion Testing:
- Immerse the cylinder block in a tank filled with water heated to 180–200°F (82–93°C).
- Apply 40 psi of air pressure to the water jackets using a connected air line.
- Observe for bubbles indicating leaks or cracks.
-
Method B: Surface Testing:
- When a water tank is unavailable, fill the water jacket with a mixture of water and ethylene glycol.
- Pressurize the jacket with 40 psi air and maintain the pressure for two hours.
- Check for coolant leakage into oil passages or external surfaces.
-
Detection of Cracks:
- Focus inspection on high-stress areas like cylinder bores, air box drain openings, and main bearing supports.
- Use dye penetrant or magnetic particle testing for additional crack detection in suspect areas.
Addressing Test Results:
- Blocks with minor, localized leaks may be salvageable using appropriate repair techniques.
- Blocks with significant structural cracks must be replaced to ensure reliability and safety.
Understanding Cylinder Liner and Seal Ring Specifications
Cylinder liners in Detroit Diesel 53 Series engines play a critical role in forming the combustion chamber and transferring heat to the cooling system. Seal rings ensure proper isolation of coolant and oil systems.
Cylinder Liner Specifications:
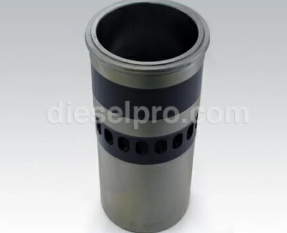
-
Design Features:
- Wet-type liners with a flange at the upper end for a secure fit.
- Direct contact with the block’s water jacket for efficient cooling.
-
Dimensional Tolerances:
- Standard liners have an outer diameter of 4.5065 inches at the upper sealing ring position.
- Oversized liners are available in 0.010, 0.020, and 0.030-inch increments to accommodate worn block bores.
-
Installation Guidelines:
- Always use a light coating of anti-seize or assembly lubricant on the seal rings to prevent damage during installation.
- Verify that the liner flange height is consistent and within specifications to ensure proper compression gasket sealing.
Seal Ring Specifications:
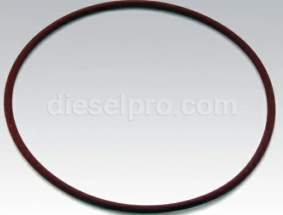
-
Material and Composition:
- Synthetic rubber construction provides durability and flexibility.
- Seal rings for oversized liners are identified with colored stripes for easy identification.
-
Placement and Sealing:
- Install rings in the counterbores of the block, ensuring they lay flat and untwisted.
- Use adhesive to hold water seals in place during assembly, minimizing the risk of displacement.
-
Inspection and Replacement:
- Replace seal rings with new ones during every rebuild to ensure effective sealing.
- Inspect grooves for debris or damage that could compromise the seal.
Key Takeaways for Cylinder Block Maintenance
- Cleaning: Proper cleaning removes contaminants and prepares the block for accurate inspection and assembly.
- Inspection: Identifying wear, cracks, or dimensional inaccuracies is crucial to preventing future engine failures.
- Pressure Testing: Detecting cracks or leaks ensures the integrity of the block under operational pressures.
- Cylinder Liner and Seal Rings: Following specifications and using quality replacement parts enhance reliability and performance.
By following these comprehensive steps for cleaning, inspection, and testing, you can maintain the integrity of the Detroit Diesel 53 Series engine cylinder block, ensuring it meets the demanding requirements of marine, industrial, and trucking applications.
Parts Catalog for 353 Detroit Diesel Marine Engine
Parts Catalog for 453 Detroit Diesel Marine Engine
Parts Catalog for 6V53 Detroit Diesel Marine Engine
Parts Catalog for 8V53 Detroit Diesel Marine Engine