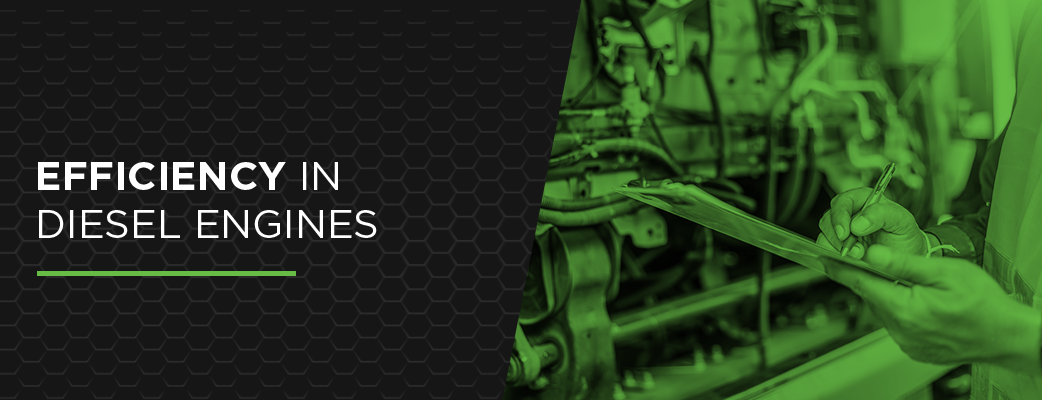
Efficiency in Diesel Engines: A Marine Perspective With a Focus on Detroit Diesel, Cummins, and Caterpillar Engines
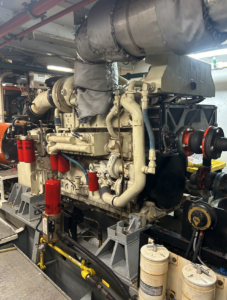
Introduction: Why Marine Diesel Efficiency Matters
Diesel engines are the backbone of the maritime industry. From commercial fishing vessels, tugboats, and ferries, to massive cargo ships and offshore supply vessels, marine diesel engines move the global economy. They power everything from short coastal hops to transoceanic voyages.
But marine operators face unique challenges that make diesel engine efficiency absolutely critical:
-
Fuel is often the largest single operating cost. A tugboat might burn hundreds of gallons a day. Even a modest efficiency gain translates into massive annual savings.
-
Extended continuous operation. Unlike trucks that idle at lights, marine diesels often run under load for 10-20 hours a day or more, making small inefficiencies compound dramatically over thousands of hours.
-
Remote operations. Ships can’t pull over for repairs. Efficient engines are typically more reliable and put less stress on components.
-
Tighter environmental regulations. From IMO Tier III to regional restrictions on emissions, efficient combustion is key to compliance.
This is especially important for operators relying on proven workhorses from Detroit Diesel, Cummins, and Caterpillar— brands synonymous with marine power.
What Diesel Engine Efficiency Really Means in a Marine Context
When we talk about efficiency at sea, we’re talking about how effectively your engine turns each gallon of diesel fuel into useful propulsion or auxiliary power.
Two Key Metrics
-
Specific fuel consumption (SFC): Often measured in grams per kWh or pounds per horsepower-hour. Lower SFC means you’re extracting more work from each unit of fuel.
-
Thermal efficiency: The percentage of the diesel’s chemical energy converted into mechanical work. Modern large marine diesels might hit 45-50% thermal efficiency. Smaller high-speed marine engines typically range 35-42%.
Why Marine Applications Are Different
Marine engines:
-
Run for long periods at steady loads, often near their maximum continuous rating (MCR), which actually allows them to be designed for higher efficiencies at those loads.
-
Must deal with variable conditions, from heavy seas requiring more torque to calm days under light load — meaning they need a broad efficiency curve.
-
Often run auxiliary systems off the main engine, impacting load and efficiency calculations.
For example, a shrimp trawler powered by a Detroit Diesel 8V92 might run at 80% load for 14 hours straight, whereas a delivery truck’s engine cycles through stop-and-go.
How Detroit Diesel, Cummins, and Caterpillar Approach Marine Efficiency
Detroit Diesel
Detroit Diesel 671 Engines In A Tugboat
Detroit Diesel’s two-stroke Series 71, 92, and 149 engines have powered fishing boats, workboats, and tugs for decades.
-
Strengths: Simple, robust design, direct mechanical control, easy to rebuild onboard or dockside.
-
Efficiency: These engines have decent thermal efficiency (about 32-36%), thanks to high firing frequency — every revolution is a power stroke.
-
Challenges: Two-stroke scavenging can let unburned fuel escape, slightly reducing efficiency versus modern four-strokes.
However, for operators running rebuilt Detroit Diesels, optimizing turbo and blower efficiency, valve timing, and injector calibration can claw back wasted fuel.
Cummins
A Rebuilt Cummins 6CTA Engine Being Installed Into A Commercial Fishing Boat By Diesel Pro Power, Inc. customer Imperial Diesel Service, LLC.
Cummins’ marine line — from the 6BTA to the QSK series — is popular on small to medium commercial vessels.
-
Strengths: Modern four-stroke designs with high-pressure fuel systems, electronic controls, and advanced turbocharging give Cummins excellent fuel economy, especially in the ISX and QSK lines.
-
Efficiency: High-speed Cummins marine engines can achieve 38-42% thermal efficiency under optimal load.
-
Support: Cummins has extensive marine calibration options to fine-tune for specific hull resistance and propeller curves, improving vessel-specific efficiency.
Caterpillar
Caterpillar C32 Marine Engine
Caterpillar’s C-series and 3500 series marine engines dominate offshore supply, fishing fleets, and large yachts.
-
Strengths: Designed for high continuous loads, with aftercooling and sophisticated fuel management.
-
Efficiency: Caterpillar’s large bore engines, like the C32 and 3516, regularly hit 40-45% efficiency when propped correctly and maintained.
-
Unique: Cat offers performance mapping, letting operators select fuel maps prioritizing either economy or max power.
Key Engineering Drivers of Efficiency in Marine Diesel Engines
1. Proper Engine Loading
Marine engines are most efficient when operating in their sweet spot:
-
Typically 70-85% of rated load.
-
Below this, combustion temperatures drop, leading to incomplete burn (visible as black smoke) and lower efficiency.
-
Above this, fuel delivery might be enriched to prevent excessive exhaust temps, also reducing efficiency.
This is why matching the propeller pitch and vessel resistance to the engine’s power curve is critical. Over-propped vessels “lug” the engine, causing poor combustion. Under-propped ones let the engine overspeed, wasting fuel.
2. Turbocharging and Charge Air Cooling
Turbochargers extract energy from exhaust gases that would otherwise be wasted, compressing intake air. This allows more oxygen into each cylinder, burning more fuel efficiently.
-
Detroit Diesel: Classic 8V92 turbos work in tandem with blowers. Ensuring the turbo matches the blower air demand is key. An undersized turbo can’t keep up, leading to overloading the blower and wasted fuel.
-
Cummins: Uses aftercoolers extensively, cooling compressed air to increase density and improve combustion. A Cummins QSB6.7 running with a fouled intercooler may lose 5-8% efficiency.
-
Caterpillar: Cat’s ADEM controls often optimize turbo vane position in real-time on larger engines, ensuring best boost and fuel economy across varying loads.
3. Fuel Injection Precision
-
Older Detroit Diesels use mechanical unit injectors, which rely on cam timing. Keeping these adjusted ensures precise fuel delivery. A single miscalibrated injector on a V8 could throw off the balance and waste significant fuel.
-
Cummins and Caterpillar marine engines with electronic controls can adjust injection timing by microseconds, optimizing for load and RPM. Modern common-rail systems spray at 20,000 to 40,000 psi, creating a fine mist that burns completely, maximizing energy extraction.
-
4. Reducing Mechanical Losses
Friction losses consume 5-10% of engine power. In marine diesels, this means:
-
Proper oil viscosity, especially under cold starts or in tropical waters. Too thick oil increases drag, too thin risks wear.
-
Keeping valve lash and cam timing correct.
-
Using low-friction coatings on rebuilds (modern Cummins and Cat rebuild kits include coated pistons and advanced rings).
5. Maintaining Clean Systems
Heat exchangers clogged with scale or fouled sea strainers lead to higher engine temps. The ECU may enrich fuel to keep temps down, directly reducing efficiency. Similarly:
-
Dirty aftercoolers reduce charge air density.
-
Exhaust leaks reduce turbo efficiency.
-
Worn impellers lower coolant flow, increasing cylinder temps.
All impact fuel economy on long passages.
Why Two-Stroke vs. Four-Stroke Matters for Marine Efficiency
Detroit Diesel’s Classic Two-Strokes
The Roots Blower Makes The 2 Stroke Principal Work For Detroit Diesel Engines -
-
The Detroit Diesel 71 and 92 series are two-stroke engines. This means:
-
Every crankshaft rotation produces a power stroke. This gives excellent torque and responsiveness, valuable for tugs or trawlers pulling heavy loads.
However:
-
They rely on blowers to scavenge exhaust, and some fresh charge air inevitably escapes through the exhaust ports, reducing combustion efficiency.
A well-tuned 8V92 might still see 0.36-0.38 lbs/hp-hr fuel consumption, which is respectable but higher than a modern Cummins QSM11.
Modern Four-Strokes (Cummins & Caterpillar)
-
Burn more completely under lean conditions.
-
Use exhaust gas more effectively via turbocharging without the mandatory blower drag of two-strokes.
Thus, in applications where steady cruise fuel economy matters most, like a ferry running 100 miles daily, a modern Cat or Cummins typically delivers better specific fuel consumption than an old Detroit.
Advanced Strategies for Improving Marine Diesel Efficiency
-
-
Modern engines such as this Cummins QSB used sophisticated computers called ECM’s to make adjustments to the engine.
Propeller Matching and Hull Condition
The prop is as critical as the engine. Marine diesels must be loaded properly. An overly large propeller lugging the engine under RPM results in incomplete combustion and smoky exhaust — a tell-tale sign of wasted fuel. Conversely, a prop that’s too small causes the engine to run above optimal RPM with less load.
Similarly, a fouled hull can add enough drag to push the engine outside its efficiency band.
Electronic Engine Management
Modern Cummins and Caterpillar marine engines use sophisticated ECMs (like Caterpillar’s ADEM or Cummins’ CM2350). They adjust:
-
Injection timing.
-
Turbo vane positions.
-
Fuel quantity based on real-time load.
Keeping sensors clean and software up to date ensures these systems maintain peak efficiency.
Waste Heat Recovery
Larger vessels sometimes employ exhaust gas boilers (economizers) to capture heat and create steam for auxiliary systems, reducing the load on generators. This doesn’t apply directly to most fishing boats or tugs but is common on offshore supply ships running massive Caterpillar or Cummins prime movers.
Regular Sea Trials and Fuel Audits
Many commercial operators now track:
-
Fuel burn vs. speed over ground.
-
Engine load via load meters.
-
Exhaust temps on each cylinder.
This data helps identify when hull fouling, injector issues, or improper loading start sapping efficiency — catching problems before they become costly.
Practical Tips for Maximizing Efficiency on Your Detroit, Cummins, or Caterpillar
-
Maintain injectors and calibration. For Detroit 92s, keep unit injector timing adjusted. For Cummins/Cat, ensure sensors and electronics are clean.
-
Keep turbos and aftercoolers clean. A marine turbo caked with carbon or a salt-scaled intercooler drastically reduces air mass, hurting combustion.
-
Watch exhaust color. A light haze is normal under load, but black smoke means wasted fuel. White smoke under load could mean injector issues or cold combustion.
-
Run at optimal load. Aim for 75-85% of rated RPM at cruise, matching the prop and hull to keep the engine in its sweet spot.
-
Document fuel usage. Logging gallons per hour at various RPMs over time builds a baseline. Increases often indicate fouling or injector drift.
Conclusion: Efficient Diesel Operation is Smart Business at Sea
Whether you’re running a rugged Detroit Diesel 8V92 powering a shrimp boat in the Gulf, a Cummins QSM11 on a pilot boat, or a pair of Caterpillar C18s pushing a crew transfer vessel, efficiency matters. It affects:
-
Operating cost: On a boat burning 50 gallons/hour, even a 5% improvement saves over $15,000/year at typical marine diesel prices.
-
Reliability: Engines operating efficiently run cooler and cleaner, with fewer unburnt deposits to foul injectors or turbos.
-
Environmental compliance: More complete combustion reduces NOx, soot, and CO₂ — helping meet MARPOL and local coastal restrictions.
Diesel engines remain the heart of the marine industry. By understanding how Detroit, Cummins, and Caterpillar design for efficiency — and how your maintenance and operational habits impact it — you protect your investment, your profits, and the oceans we all rely on.
-