Kona Hawaii fishing boat powered by Detroit Diesel 8.2 L photo provided by James David
Overview of Electrical Systems in Detroit Diesel 8.2L Engines
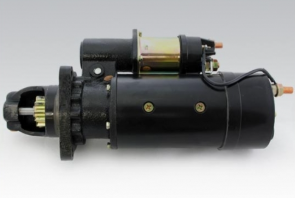
The Detroit Diesel 8.2L engine is a marvel of engineering that combines robust design with precision electrical systems. The electrical components are not only integral to starting and running the engine but also critical in monitoring and protecting it during operation. A well-maintained electrical system ensures optimal performance and longevity, while protective systems enhance safety for both the engine and operator.
Electrical systems in this engine include the battery, starter motor, and alternator, which work together to power the engine and its accessories. These components are complemented by a suite of protective systems designed to safeguard the engine against damage due to overheating, low oil pressure, or electrical faults. This combination of equipment ensures that the Detroit Diesel 8.2L engine operates reliably under a variety of demanding conditions.
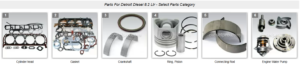
Battery: The Heart of the Electrical System
Functionality and Role
The battery is the primary source of electrical energy for the Detroit Diesel 8.2L engine, particularly during startup. It stores energy in chemical form and delivers a high burst of current to the starter motor when the ignition key is turned. In addition to starting the engine, the battery powers auxiliary systems such as lighting, instrumentation, and communication equipment, especially when the alternator is not generating power.
Battery Types
- Lead-Acid Batteries: Commonly used due to their cost-effectiveness and reliability. They come in flooded, gel, and absorbed glass mat (AGM) variants.
- Maintenance-Free Batteries: Designed to minimize upkeep, requiring no periodic addition of water.
- Deep-Cycle Batteries: Ideal for applications where sustained power is required over longer periods, although less common in engine starting roles.
Maintenance Tips
- Visual Inspection: Regularly check for cracks, leaks, or bulging. These signs indicate imminent failure.
- Terminal Cleaning: Corrosion at the terminals can impede power flow. Clean terminals with a wire brush and apply an anti-corrosion compound.
- Voltage Testing: Use a multimeter to verify voltage levels. A fully charged battery typically reads between 12.6 and 12.8 volts.
- Charge Retention: If the engine is not run regularly, ensure the battery is kept on a trickle charger to prevent sulfation.
Signs of Battery Failure
- Slow engine cranking.
- Dim headlights or dashboard lights.
- Frequent need for jump-starting.
Starter Motor: Energizing the Engine
Functionality and Operation
The starter motor is responsible for cranking the engine, initiating the combustion cycle. It converts electrical energy from the battery into mechanical energy, using a small gear (the pinion) to engage with the engine’s flywheel. Once the engine starts, the starter motor disengages automatically to prevent damage.
Key Components
- Armature: A rotating coil that generates mechanical motion.
- Solenoid: Acts as a switch to connect the battery to the starter motor.
- Drive Assembly: Engages and disengages the starter gear with the flywheel.
- Brushes and Commutator: Facilitate electrical flow within the motor.
Maintenance Tips
- Inspect Connections: Loose or corroded wires can reduce the motor’s efficiency.
- Clean the Solenoid Contacts: Dirty contacts may result in erratic engagement.
- Check Brushes: Replace worn brushes to maintain electrical contact.
Common Issues
- Clicking Sound: Indicates a weak battery or faulty solenoid.
- Grinding Noise: Suggests improper alignment of the starter gear with the flywheel.
- No Response: Could point to a completely discharged battery or a defective starter motor.
Alternator: Sustaining Power Generation
Functionality and Role
The alternator maintains the battery’s charge and supplies power to electrical systems while the engine is running. Unlike the battery, which provides short-term power bursts, the alternator ensures a continuous supply of electrical energy, making it vital for long-term operation.
Components
- Rotor and Stator: Generate alternating current (AC).
- Rectifier: Converts AC to direct current (DC) for the battery.
- Voltage Regulator: Maintains a consistent output voltage to prevent overcharging.
Maintenance Tips
- Belt Inspection: Ensure proper tension and check for cracks or fraying.
- Voltage Output: Measure the output using a multimeter. It should range between 13.8 and 14.4 volts when the engine is running.
- Bearing Lubrication: Listen for whining or squealing noises that could indicate worn bearings.
Signs of Alternator Issues
- Flickering dashboard lights.
- Dead battery despite frequent driving.
- Unusual noises from the alternator.
Protective Systems for Engine Health and Operator Safety
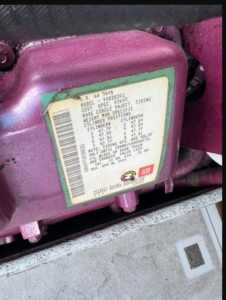
The Detroit Diesel 8.2L engine incorporates advanced protective systems to mitigate risks and prevent damage during operation. These systems continuously monitor critical parameters and provide alerts or automatic intervention in case of abnormalities.
Temperature Monitoring System
- Role: Prevents engine overheating by monitoring coolant temperature.
- Components:
-
Temperature sensors located near the coolant passages.
- Thermostat to regulate coolant flow.
- Dashboard gauge or warning light for real-time temperature readings.
-
- Maintenance:
-
Check coolant levels and replace periodically to maintain effectiveness.
- Inspect thermostat functionality and replace if stuck open or closed.
- Test sensor accuracy using diagnostic tools.
-
Oil Pressure Monitoring

- Role: Alerts the operator of low oil pressure, which can lead to engine seizure.
- Components:
-
Oil pressure sensors and warning indicators.
- Relief valves to maintain pressure within acceptable limits.
-
- Maintenance:
-
Replace sensors if they provide erratic readings.
- Ensure oil levels are adequate and oil filters are clean.
- Use the recommended grade of oil to maintain proper viscosity.
-
Engine Shutdown Systems
- Role: Automatically shuts down the engine under extreme conditions, such as severe overheating or critical oil pressure loss.
- Types:
-
Mechanical governors that stop fuel delivery.
- Electronic systems integrated with the engine control module (ECM).
-
- Maintenance:
-
Test shutdown mechanisms during routine inspections.
- Verify sensor-triggered responses by simulating fault conditions.
-
Electrical Overload Protection
- Role: Safeguards electrical circuits from excessive current, preventing fires or component damage.
- Components:
-
Fuses and circuit breakers.
- Relays for current distribution.
-
- Maintenance:
-
Replace blown fuses with ones of the correct amperage rating.
- Test circuit breakers to ensure they trip as designed.
- Inspect for melted wires or burnt insulation.
-
Fuel System Safety
- Role: Prevents fuel leaks and ensures consistent fuel delivery.
- Components:
-
Fuel lines and filters.
- Shutoff valves to prevent leaks in emergencies.
-
- Maintenance:
-
Replace worn or cracked fuel lines.
- Regularly clean or replace fuel filters to prevent clogging.
-
Common Troubleshooting Scenarios
Issue 1: Engine Overheating
- Possible Causes:
- Low coolant levels.
- Malfunctioning thermostat.
- Faulty temperature sensor.
- Solution:
- Refill coolant and check for leaks.
- Replace the thermostat if it is not opening or closing properly.
- Test and replace the temperature sensor as needed.
Issue 2: Low Oil Pressure
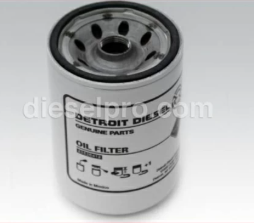
- Possible Causes:
- Insufficient oil.
- Clogged oil filter.
- Worn oil pump.
- Solution:
- Top up oil to the correct level.
- Replace the oil filter if clogged.
- Inspect and replace the oil pump if it shows signs of wear.
Issue 3: Electrical System Failure
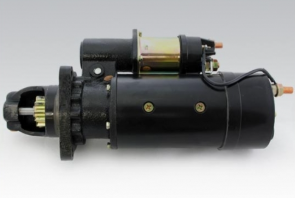
- Possible Causes:
- Dead battery.
- Faulty alternator.
- Blown fuses or damaged wiring.
- Solution:
- Recharge or replace the battery.
- Test the alternator and repair or replace if needed.
- Replace blown fuses and repair damaged wires.
Best Practices for Electrical and Protective System Maintenance
- Scheduled Inspections: Adhere to the manufacturer’s maintenance schedule to identify issues before they escalate.
- Component Testing: Use diagnostic tools to evaluate the performance of sensors, fuses, and circuit breakers.
- Record Keeping: Maintain a detailed log of inspections, repairs, and replacements to track system health.
- Emergency Preparedness: Train operators on responding to warnings and shutdowns to minimize downtime and prevent damage.
This comprehensive approach to understanding and maintaining the electrical and protective systems ensures that the Detroit Diesel 8.2L engine operates efficiently and reliably under all conditions.
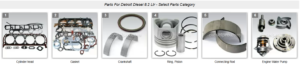