
Fuel pipe installation is a critical aspect of maintaining and rebuilding Detroit Diesel 53 Series engines (3-53, 4-53, 6V53, and 8V53). The fuel pipes play a vital role in delivering high-pressure fuel to the injectors and ensuring the return of unused fuel to the system. Proper installation techniques, including adherence to torque specifications, are essential to achieving leak-free connections that maintain system integrity and fuel efficiency.
This guide provides a detailed exploration of fuel pipe installation procedures, including inspection, alignment, torque requirements, troubleshooting, and best practices to ensure a leak-free and efficient fuel system.
Fuel pipes & Related Components for Detroit Diesel 353 Non–Turbo Marine & Industrial Engines
Fuel pipes & Related Components for Detroit Diesel 353 Turbo Marine & industrial Engines
Fuel pipes & Related Components for Detroit Diesel 453 Non – Turbo Marine & industrial Engines
Fuel pipes & Related Components for Detroit Diesel 453 Turbo Marine & industrial Engines
Fuel pipes & Related Components for Detroit Diesel 6V53 Non – Turbo Marine & industrial Engines
Fuel pipes & Related Components for Detroit Diesel 6V53 Turbo Marine & industrial Engines
Fuel pipes & Related Components for Detroit Diesel 8V53 Non – Turbo Marine & industrial Engines
Fuel pipes & Related Components for Detroit Diesel 8V53 Turbo Marine & industrial Engines
Importance of Proper Fuel Pipe Installation
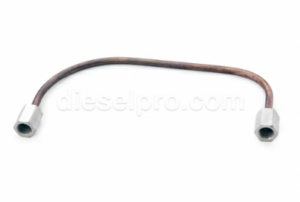
The fuel pipes in a diesel engine operate under extreme pressure and are subjected to constant vibrations. Improper installation or incorrect torque can lead to:
- Fuel Leaks: Causing reduced efficiency, increased emissions, and potential fire hazards.
- Pressure Loss: Resulting in poor fuel delivery, misfires, and reduced power.
- System Contamination: Dirt and debris entering the fuel lines can damage injectors and other components.
Proper fuel pipe installation ensures:
- Optimal Fuel Pressure: Delivering consistent and accurate fuel to the injectors.
- System Integrity: Preventing leaks and maintaining a clean, contamination-free environment.
- Engine Performance: Ensuring reliable and efficient operation under all conditions.
Types of Fuel Pipes in Detroit Diesel 53 Series Engines
Detroit Diesel 53 Series engines utilize two main types of fuel pipes:
- High-Pressure Pipes:
- Transport fuel from the fuel pump to the injectors.
- Designed to withstand high pressures exceeding 15,000 psi.
- Return Pipes:
- Carry unused fuel back to the fuel tank or return manifold.
- Operate under lower pressures but are equally important for maintaining system balance.
Tools and Materials Required for Installation
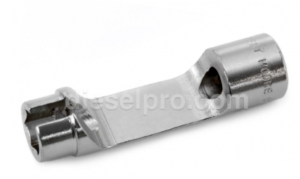
Before beginning fuel pipe installation, gather the necessary tools and materials:
- Torque wrench (calibrated for low to medium torque settings)
- Flare nut wrench (to prevent rounding fuel pipe nuts)
- Fuel pipe alignment tool
- Clean, lint-free cloths
- Anti-seize compound or thread lubricant (if specified)
- Replacement O-rings or seals (if applicable)
Fuel Pipe Installation Procedure

1. Preparation
Proper preparation is crucial for a successful installation:
- Cleanliness: Ensure all tools, pipes, and connections are clean. Contaminants can damage the system or block the injectors.
- Inspect Components:
- Check pipes for cracks, bends, or worn flares.
- Inspect connectors and sealing surfaces for damage or dirt.
- Replace any components showing signs of wear or damage.
2. Aligning the Fuel Pipes
Alignment is critical to avoid unnecessary stress on the fittings, which could cause leaks or premature failure:
- Pre-Alignment:
- Position the pipes close to their respective connections before threading the nuts.
- Ensure no twisting or bending of the pipes.
- Use an Alignment Tool:
- If pipes are slightly out of alignment, use an alignment tool to adjust them gently without introducing stress fractures.
- If pipes are slightly out of alignment, use an alignment tool to adjust them gently without introducing stress fractures.
3. Installing the Pipes
Follow these steps for secure and leak-free installation:
- Hand-Tighten First:
- Thread the nuts or connectors by hand to prevent cross-threading.
- Ensure the pipe seats properly against the injector or fuel manifold.
- Lubricate Threads:
- For O-ring sealed pipes, lightly lubricate the seals with clean engine oil to ensure a snug fit and prevent tearing.
- For O-ring sealed pipes, lightly lubricate the seals with clean engine oil to ensure a snug fit and prevent tearing.
- Tighten with a Flare Nut Wrench:
- Use a flare nut wrench for a secure grip without damaging the fittings.
- Use a flare nut wrench for a secure grip without damaging the fittings.
4. Applying Torque
Adhering to the correct torque specifications is essential for ensuring leak-free connections without over-tightening, which can damage components.
Torque Specifications for Detroit Diesel 53 Series Fuel Pipes
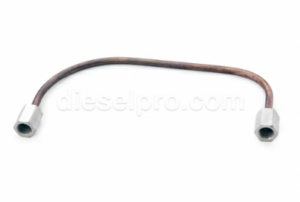
- Flared-End Pipes:
- Uncoated nuts: 160 lb-in (18.3 N·m)
- Endurion® coated nuts: 130 lb-in (14.7 N·m)
- O-Ring Sealed Pipes:
- 143 lb-in (16.2 N·m)
- 143 lb-in (16.2 N·m)
Torque Application Steps:
- Set the Torque Wrench:
- Adjust the torque wrench to the specified value for the type of fuel pipe being installed.
- Adjust the torque wrench to the specified value for the type of fuel pipe being installed.
- Tighten Gradually:
- Tighten the nut in small increments to avoid sudden stress on the fitting.
- Tighten the nut in small increments to avoid sudden stress on the fitting.
- Verify Tightness:
- Once the specified torque is reached, stop tightening to prevent over-torquing.
- Once the specified torque is reached, stop tightening to prevent over-torquing.
Testing for Leak-Free Connections
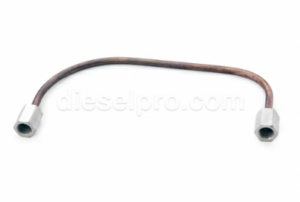
After installation, test the fuel system to ensure all connections are secure and free from leaks.
1. Visual Inspection
- Inspect all pipe connections for visible signs of fuel seepage.
- Look for misaligned pipes or improperly seated connectors.
2. Pressure Testing
- Use a pressure tester to simulate operating conditions:
- Apply system pressure gradually and monitor for leaks at each connection.
- If leaks are detected, release pressure and re-tighten the affected connection to the specified torque.
3. Fuel System Priming
- Prime the fuel system by operating the fuel pump to fill the lines and remove air pockets.
- Check for leaks during priming, as pressurized fuel can expose weak connections.
Troubleshooting Common Fuel Pipe Installation Issues
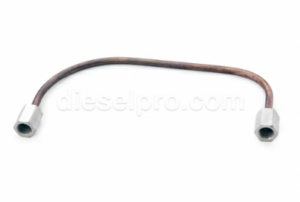
1. Cross-Threaded Connections
- Cause: Misalignment during installation.
- Solution: Remove and re-thread carefully by hand before applying torque.
2. Fuel Leaks
- Cause: Insufficient torque, damaged threads, or worn seals.
- Solution: Inspect and replace seals if necessary. Re-tighten to the correct torque specification.
3. Bent or Twisted Pipes
- Cause: Improper alignment during installation.
- Solution: Use an alignment tool to straighten the pipes without introducing stress fractures.
4. O-Ring Damage
- Cause: Dry installation or excessive force during assembly.
- Solution: Replace the O-ring and lubricate it before reinstallation.
Best Practices for Fuel Pipe Installation
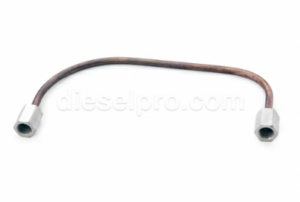
Adopting these practices can prevent issues and ensure long-lasting, leak-free connections:
- Follow Manufacturer Specifications:
- Always adhere to Detroit Diesel’s guidelines for torque values, materials, and procedures.
- Always adhere to Detroit Diesel’s guidelines for torque values, materials, and procedures.
- Use Quality Replacement Parts:
- Install high-quality, OEM-equivalent fuel pipes and seals to maintain system integrity.
- Install high-quality, OEM-equivalent fuel pipes and seals to maintain system integrity.
- Maintain Cleanliness:
- Avoid introducing contaminants into the fuel system during installation.
- Avoid introducing contaminants into the fuel system during installation.
- Inspect Regularly:
- Periodically inspect fuel pipes and connections for signs of wear or leaks.
- Periodically inspect fuel pipes and connections for signs of wear or leaks.
The Role of Proper Installation in Engine Performance
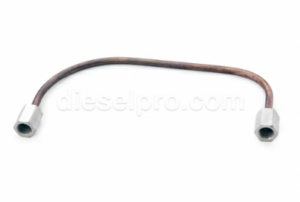
Correct fuel pipe installation has a significant impact on the overall performance of Detroit Diesel 53 Series engines:
- Enhanced Efficiency: Leak-free connections ensure consistent fuel pressure, optimizing combustion.
- Reduced Emissions: Proper sealing minimizes unburned hydrocarbons and fuel wastage.
- Prolonged Component Life: Reduces wear on injectors and fuel pumps caused by pressure fluctuations or contamination.
Key Takeaways
Proper fuel pipe installation is a vital component of maintaining Detroit Diesel 53 Series engines. By following the detailed procedures outlined above, including adhering to torque specifications and ensuring proper alignment, you can achieve leak-free connections that enhance engine performance, efficiency, and reliability. Regular inspection and maintenance of fuel pipes will further ensure your engine remains in peak condition for years to come.
Fuel pipes & Related Components for Detroit Diesel 353 Non–Turbo Marine & Industrial Engines
Fuel pipes & Related Components for Detroit Diesel 353 Turbo Marine & industrial Engines
Fuel pipes & Related Components for Detroit Diesel 453 Non – Turbo Marine & industrial Engines
Fuel pipes & Related Components for Detroit Diesel 453 Turbo Marine & industrial Engines
Fuel pipes & Related Components for Detroit Diesel 6V53 Non – Turbo Marine & industrial Engines
Fuel pipes & Related Components for Detroit Diesel 6V53 Turbo Marine & industrial Engines
Fuel pipes & Related Components for Detroit Diesel 8V53 Non – Turbo Marine & industrial Engines
Fuel pipes & Related Components for Detroit Diesel 8V53 Turbo Marine & industrial Engines