The fuel system in Detroit Diesel 149 Series engines, including the 8V149, 12V149, and 16V149 models, is a critical component that ensures efficient fuel delivery for optimal combustion and power output. This system consists of multiple interconnected components designed to supply fuel under high pressure to each cylinder, where it is atomized and ignited to drive the engine. Proper maintenance of the fuel system is essential for maintaining the engine’s performance, fuel efficiency, and longevity.
Components and Operation in the Detroit Diesel 149 Series Engine (8V149, 12V149, 16V149): Fuel Pump, Filter, Injectors, and Manifold

The Detroit Diesel 149 Series engine relies on a robust fuel system to deliver fuel efficiently and effectively to its combustion chambers. The system includes several critical components, each playing a vital role in ensuring reliable performance and longevity. Below is an expanded explanation of these components and their functions:
Parts Catalog for 8V149 Detroit Diesel Marine Engine
Parts Catalog for 12V149 Detroit Diesel Marine Engine
Parts Catalog for 16V149 Detroit Diesel Marine Engine
Fuel Pump
The fuel pump serves as the backbone of the fuel delivery system, drawing fuel from the tank and delivering it under precise pressure to the injectors. In the Detroit Diesel 149 Series engines, which often operate under high-load conditions, the fuel pump must meet demanding performance requirements. Key points to consider include:
- Function:
Ensures a steady supply of pressurized fuel to maintain engine efficiency and power output.
- Maintenance Tips:
Regular inspection for signs of wear, such as leaks or reduced pressure, can prevent power loss, poor fuel economy, and starting issues. Replace worn or damaged fuel pumps promptly.
- Performance Indicators:
A failing pump can result in symptoms like rough idling, engine misfires, or a noticeable drop in power, especially during acceleration or heavy loads.
Fuel Filter
The fuel filter is a safeguard against impurities that could damage the precision components within the fuel system. Clean fuel is essential for maintaining efficient operation, especially in the high-performance environment of the 149 Series engines.
- Function
Removes contaminants such as dirt, rust, and debris before they reach the injectors or combustion chambers.
- Location
Positioned between the fuel pump and the injectors, ensuring filtered fuel is delivered for combustion.
- Maintenance Tips
Replace the fuel filter according to the manufacturer’s recommendations or when symptoms of clogging appear, such as restricted fuel flow, lean running, or power loss.
- Failure Risks
A clogged or dirty filter can lead to injector clogs, reduced fuel pressure, or engine misfires.
Fuel Injectors
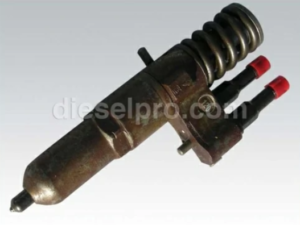
The fuel injectors are precision components responsible for atomizing the fuel and delivering it into the combustion chamber at the exact timing required for efficient combustion.
- Function
Atomizes fuel into a fine mist, ensuring optimal mixing with air for complete combustion.
- Design Considerations
Built to withstand the high pressures of the 149 Series engine, ensuring consistent and reliable operation.
- Maintenance Tips
Routine inspection for clogging or wear is critical. Clean injectors regularly to maintain spray pattern integrity, and replace them if wear compromises performance.
- Symptoms of Issues
Problems with injectors can manifest as uneven fuel distribution, rough idling, poor fuel efficiency, or noticeable loss of power.
Fuel Injector & Related Components for 8V149 Non- Turbo Detroit Diesel
Fuel Injector & Related Components for 8V149 Turbo Detroit Diesel
Fuel Injector & Related Components for 12V149 Non-Turbo Detroit Diesel
Fuel Injector & Related Components for 12V149 Turbo Detroit Diesel
Fuel Injector & Related Components for 16V149 Non- Turbo Detroit Diesel
Fuel Injector & Related Components for 16V149 Turbo Detroit Diesel
Fuel Manifold
The fuel manifold, often referred to as the fuel rail, ensures the even distribution of fuel to all injectors at the correct pressure.
- Function
Distributes fuel evenly and maintains a consistent pressure to support uniform injector operation.
- Maintenance Tips
Inspect the manifold regularly for leaks, blockages, or pressure irregularities that could disrupt fuel flow.
- Impact of Malfunction
An issue in the fuel manifold can result in uneven combustion, reduced power output, and potential damage to other fuel system components.
Integrated System Performance
Together, the fuel pump, filter, injectors, and manifold form a highly synchronized system that ensures precise fuel delivery. Proper maintenance of each component is essential for:
- Optimal Performance
Smooth power delivery and consistent engine operation.
- Efficiency: Maximizing fuel economy and reducing operating costs.
- Longevity:
Preventing premature wear or damage to engine components caused by fuel delivery issues.
Key Maintenance Practices
- Routine Inspections:
Regularly check all components for signs of wear, leaks, or damage.
- Scheduled Replacements:
Replace filters, pumps, or injectors as recommended by the manufacturer or based on performance indicators.
- Monitor Fuel Quality:
Ensure clean and high-quality fuel to minimize contamination risks.
By understanding the operation of each component and adhering to recommended maintenance schedules, operators can ensure the Detroit Diesel 149 Series engine delivers reliable performance even in the most demanding conditions.
Fuel Quality for Detroit Diesel 149 Engines (8V149, 12V149, 16V149): Importance of Clean, High-Quality Fuel
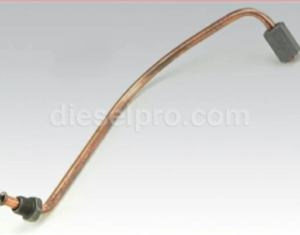
Using clean, high-quality fuel is critical for maintaining the performance, efficiency, and longevity of Detroit Diesel 149 Series engines. These high-performance engines demand precise fuel delivery, and any compromise in fuel quality can lead to system inefficiencies, reduced power, and even costly engine damage. Below is an expanded explanation of the importance of fuel quality and its impact on engine performance.
Preventing Injector Clogs
Fuel injectors in the Detroit Diesel 149 Series are precision-engineered components designed to atomize fuel into a fine mist for efficient combustion. Contaminants in fuel, such as dirt, water, and debris, can obstruct the injectors, leading to significant performance issues.
- Impact of Clogs:
Clogged injectors disrupt fuel atomization, causing incomplete combustion, reduced power output, rough idling, and increased emissions.
- Preventive Measures:
- Use fuel from reputable suppliers to minimize contaminants.
- Install additional fuel pre-filters to capture impurities before they reach the main fuel filter.
- Regularly inspect and clean fuel injectors to maintain performance.
Enhancing Combustion Efficiency
Clean, high-quality diesel fuel ensures efficient combustion by allowing the injectors to operate without obstruction and facilitating a proper air-fuel mixture.
- Benefits:
- Improved Fuel Economy: Efficient combustion maximizes energy extraction from fuel, reducing overall consumption.
- Increased Power Output: Engines run smoother and deliver higher performance when fuel quality is optimal.
- Reduced Emissions: Cleaner combustion leads to fewer harmful exhaust gases and soot buildup.
- Improved Fuel Economy: Efficient combustion maximizes energy extraction from fuel, reducing overall consumption.
- Fuel Additives:
Consider using Detroit Diesel-approved fuel additives to clean injectors, remove carbon deposits, and improve fuel stability. Avoid unapproved additives that may damage the fuel system.
Minimizing Wear on Fuel System Components
Low-quality or contaminated fuel accelerates wear on critical components such as the fuel pump, injectors, and fuel manifold.
- Risks of Contaminated Fuel:
- Corrosion: Water in the fuel promotes rust and corrosion within the system, damaging components.
- Abrasive Wear: Dirt and debris act as abrasives, causing premature wear on pumps and injectors.
- Shortened Component Life: Repeated exposure to impurities reduces the lifespan of fuel system parts.
- Solution: Use high-quality diesel fuel with a low water content and fewer contaminants. For added protection, consider water-separating filters or desiccant-based filtration systems.
Fuel Line Inspections: Ensuring Reliability and Safety
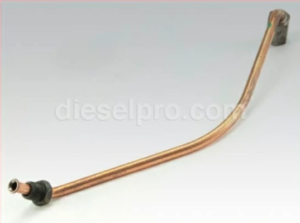
Fuel lines are the conduits that transport fuel from the tank to the engine. Their integrity is essential for maintaining consistent fuel delivery, preventing leaks, and avoiding performance disruptions. Regular inspection and proactive maintenance of fuel lines are crucial.
Inspecting for Leaks
Fuel leaks waste fuel, reduce pressure, and pose a serious fire hazard, especially in high-temperature environments.
- Signs of Leaks:
- Damp spots or wetness along fuel lines.
- Strong fuel odors around the engine or connections.
- Visible cracks or wear at fittings or along the hoses.
- Maintenance Practices:
- Tighten loose fittings and clamps immediately.
- Replace damaged or worn-out fuel lines to prevent further leakage.
- Conduct periodic pressure tests to ensure system integrity.
Checking for Wear and Deterioration
Fuel lines are exposed to various stressors, including vibration, heat, and moisture, which can lead to wear over time.
- Common Issues:
- Brittleness: Aging lines can become stiff and prone to cracking.
- Corrosion: Prolonged exposure to moisture can corrode metal fittings and degrade rubber hoses.
- Prevention:
- Inspect lines regularly for signs of cracking, bulging, or corrosion.
- Replace fuel lines at manufacturer-recommended intervals or when visible wear is detected.
- Use vibration-resistant hoses and clamps in high-vibration areas to reduce wear.
Ensuring Secure Connections
Loose fuel line connections can lead to fuel leaks, pressure drops, and fuel starvation, all of which negatively impact engine performance.
- Inspection Checklist:
- Verify all fittings are properly tightened.
- Inspect clamps and fasteners for looseness or damage.
- Replace worn or damaged clamps with high-pressure diesel-grade clamps to maintain secure connections.
- Key Maintenance: Perform routine torque checks on fasteners and fittings, particularly after heavy use or long runs.
Maintaining Pressure Consistency
Fuel pressure consistency is critical for optimal injector operation and combustion.
- Issues with Fluctuating Pressure:
Pressure drops or surges can disrupt fuel atomization, leading to incomplete combustion, power loss, and reduced efficiency.
- Solutions:
- Inspect fuel lines for blockages or leaks that may disrupt pressure.
- Test fuel pump performance to ensure it provides steady pressure.
- Consider installing a pressure regulator to stabilize fuel flow in areas prone to pressure fluctuations.
By properly maintaining the fuel system—ensuring clean, high-quality fuel, regular fuel line inspections, and maintaining the fuel pump, filter, injectors, and manifold—technicians can keep Detroit Diesel 149 Series engines running efficiently. These steps support consistent fuel delivery, improve engine performance, and help extend the life of the fuel system and engine overall.
Parts Catalog for 8V149 Detroit Diesel Marine Engine
Parts Catalog for 12V149 Detroit Diesel Marine Engine
Parts Catalog for 16V149 Detroit Diesel Marine Engine