
Introduction
The Cummins C Series engines—including the 6C, 6CT, and 6CTA—are known for their durability, efficiency, and reliability across various applications, such as marine, industrial, agricultural, and trucking industries. One of the most critical systems in ensuring these engines perform optimally is the fuel system. Proper fuel system maintenance not only improves fuel efficiency but also extends the lifespan of engine components and reduces the risk of expensive repairs.
Injectors & Related Components for Cummins 6C Marine & Industrial Engines
Injectors & Related Components for Cummins 6CT Marine & Industrial Engines
Injectors & Related Components for Cummins 6CTA Marine & Industrial Engines
Fuel System & Related Components for Cummins 6C Marine & Industrial Engines
Fuel System & Related Components for Cummins 6CT Marine & Industrial Engines
Fuel System & Related Components for Cummins 6CTA Marine & Industrial Engines
This comprehensive guide covers:
- Overview of the Fuel Injection System
- Cleaning and Replacing Fuel Injectors
- Diagnosing and Resolving Fuel Delivery Issues
By understanding how the fuel system works and following best maintenance practices, you can keep your Cummins C Series engine running smoothly for years to come.
1. Overview of the Fuel Injection System
A. The Role of the Fuel System

The fuel system in a Cummins C Series engine is responsible for delivering the right amount of diesel fuel to the engine’s combustion chambers at the correct pressure and timing. This process is critical for ensuring efficient combustion, which translates to optimal power output, fuel economy, and reduced emissions.
B. Key Components of the Fuel System
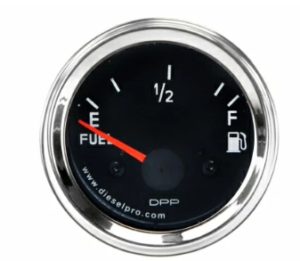
- Fuel Tank:
- Stores diesel fuel and supplies it to the engine via fuel lines.
- Requires periodic cleaning to prevent sediment buildup.
- Fuel Lift Pump:
- Draws fuel from the tank and sends it to the fuel filter and injection pump.
- Can be mechanical or electric depending on the engine variant.
- Fuel Filters:
- Primary Fuel Filter (Water Separator): Removes large contaminants and water.
- Secondary Fuel Filter: Provides finer filtration before fuel reaches the injectors.
- Fuel Injection Pump:
- Pressurizes fuel to the levels required for injection.
- Controls the timing and quantity of fuel delivered to each injector.
- Fuel Injectors:
- Spray fuel into the combustion chamber in a fine mist, ensuring complete combustion.
- Operate under extremely high pressures (up to 20,000 PSI in some models).
- Fuel Lines:
- High-pressure lines that deliver fuel from the injection pump to the injectors.
- High-pressure lines that deliver fuel from the injection pump to the injectors.
- Return Lines:
- Carry excess fuel back to the tank, helping to cool the injectors and maintain pressure balance.
C. Types of Fuel Injection Systems in Cummins C Series

- Mechanical Fuel Injection (Common in 6C and 6CT):
- Uses a mechanical injection pump to control fuel delivery.
- Known for simplicity and ease of maintenance.
- Electronic Fuel Injection (Some 6CTA Models):
- Controlled by an Electronic Control Module (ECM) for precise fuel delivery.
- Improves efficiency, power output, and emissions control.
2. Cleaning and Replacing Fuel Injectors
A. The Importance of Fuel Injector Maintenance
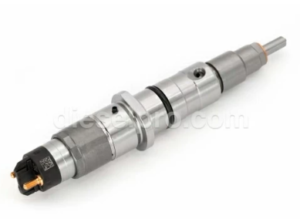
Fuel injectors play a critical role in engine performance by atomizing diesel fuel into a fine mist for efficient combustion. Over time, injectors can become clogged with carbon deposits, varnish, or contaminants from poor fuel quality. This leads to issues like:
- Poor fuel economy
- Rough idling
- Excessive exhaust smoke
- Loss of power
- Hard starting or misfires
Regular cleaning and timely replacement of injectors are essential to maintain optimal engine performance.
B. Symptoms of Faulty Fuel Injectors

- Rough Engine Idle: Uneven or shaky idling can indicate poor fuel spray patterns.
- Excessive Smoke:
- Black smoke: Over-fueling due to leaky injectors.
- White smoke: Unburned fuel from faulty injectors.
- Decreased Fuel Efficiency: Poor atomization results in incomplete combustion.
- Engine Knocking or Misfires: Irregular fuel delivery affects combustion timing.
- Difficulty Starting: Low fuel pressure or injector leaks can cause hard starts.
C. How to Clean Fuel Injectors
There are two main methods to clean fuel injectors: on-engine cleaning and off-engine ultrasonic cleaning.
1. On-Engine Injector Cleaning
Tools and Materials Needed:
- Diesel injector cleaning solution
- Fuel injector cleaning kit (pressurized canister)
- Wrenches and safety gear
Steps:
- Isolate the Fuel System: Disconnect the fuel pump and return lines.
- Connect the Cleaning Kit: Attach the pressurized canister filled with the cleaning solution to the fuel rail.
- Run the Engine: Start the engine and let it run on the cleaning solution until it stalls.
- Reconnect Fuel System: Reconnect fuel lines and test the engine.
Pros:
- Quick and doesn’t require removing injectors.
- Effective for mild to moderate buildup.
Cons:
- Not as thorough as off-engine cleaning.
- Won’t fix severe clogs or mechanical failures.
2. Off-Engine Ultrasonic Cleaning
Steps:
- Remove the Injectors: Carefully disconnect fuel lines and electrical connections.
- Initial Cleaning: Soak injectors in a cleaning solvent to loosen deposits.
- Ultrasonic Bath: Place injectors in an ultrasonic cleaner to remove stubborn debris.
- Flow Testing: After cleaning, perform a flow test to ensure proper spray patterns.
- Reinstallation: Reinstall injectors with new seals and gaskets.
Pros:
- Thorough cleaning, including internal components.
- Restores injectors close to factory performance.
Cons:
- Requires specialized equipment.
- More time-consuming.
D. Replacing Fuel Injectors
If cleaning doesn’t resolve performance issues, replacement may be necessary.
When to Replace Injectors:
- Persistent rough running after cleaning.
- Excessive fuel leakage from injector body.
- Failed flow tests during diagnostics.
- High mileage (over 100,000 miles or 4,000+ engine hours).
Steps for Replacement:
- Depressurize the Fuel System: Relieve fuel pressure to avoid accidents.
- Remove Old Injectors: Disconnect fuel lines and carefully remove injectors.
- Prepare New Injectors: Install new seals, O-rings, and washers.
- Install New Injectors: Torque bolts to manufacturer specifications.
- Prime the Fuel System: Bleed air from the system and check for leaks.
3. Diagnosing and Resolving Fuel Delivery Issues
A. Common Fuel Delivery Problems
- Air in the Fuel System:
- Symptoms: Hard starting, rough idle, stalling.
- Causes: Leaks in fuel lines, faulty connections, or improper bleeding after maintenance.
- Fix: Bleed the fuel system to remove trapped air.
- Fuel Starvation (Low Fuel Pressure):
- Symptoms: Loss of power, surging, or stalling under load.
- Causes: Clogged filters, weak lift pump, or restricted fuel lines.
- Fix: Replace filters, check the lift pump, and inspect for blockages.
- Fuel Contamination:
- Symptoms: Poor performance, injector damage, excessive smoke.
- Causes: Water, dirt, or microbial growth in the fuel tank.
- Fix: Drain contaminated fuel, clean the tank, and replace filters.
- Injector Leaks:
- Symptoms: Strong fuel odor, wet spots around injectors, poor fuel economy.
- Causes: Worn O-rings, cracked injector bodies, or loose fittings.
- Fix: Replace seals or injectors as needed.
B. Diagnostic Tools for Fuel System Troubleshooting
- Fuel Pressure Gauge:
- Measures fuel pressure at various points in the system.
- Normal pressure should be between 2500–3000 PSI for common rail systems.
- Diagnostic Scanner (Cummins INSITE):
- Reads error codes and monitors real-time fuel system data.
- Identifies issues like injector timing faults, fuel pressure irregularities, and sensor failures.
- Flow Test Equipment:
- Measures the volume of fuel delivered by each injector.
- Helps identify weak or clogged injectors.
- Smoke Tester:
- Identifies vacuum leaks that can introduce air into the fuel system.
- Identifies vacuum leaks that can introduce air into the fuel system.
C. Resolving Fuel Delivery Problems
- Bleeding Air from the System:
- Step 1: Loosen bleed screws on the fuel filter housing.
- Step 2: Use the manual primer pump to expel air until fuel flows without bubbles.
- Step 3: Tighten screws and start the engine to verify smooth operation.
- Replacing Fuel Filters:
- Always prime the system after replacing filters to prevent airlocks.
- Always prime the system after replacing filters to prevent airlocks.
- Checking for Leaks:
- Inspect all connections, fuel lines, and injector seals for signs of leakage.
- Inspect all connections, fuel lines, and injector seals for signs of leakage.
- Cleaning the Fuel Tank:
- Periodically drain and clean the tank, especially if contaminated fuel is suspected.
- Periodically drain and clean the tank, especially if contaminated fuel is suspected.
Proactive Tips for Fuel System Maintenance
- Use High-Quality Fuel:
- Purchase diesel from reputable sources to avoid contamination.
- Purchase diesel from reputable sources to avoid contamination.
- Add Fuel Stabilizers:
- Prevents microbial growth and improves fuel shelf life.
- Prevents microbial growth and improves fuel shelf life.
- Drain Water Separators Regularly:
- Water can cause corrosion and injector damage if not removed.
- Water can cause corrosion and injector damage if not removed.
- Inspect Fuel Lines and Connections:
- Check for cracks, leaks, or loose fittings during routine maintenance.
- Check for cracks, leaks, or loose fittings during routine maintenance.
- Keep the Tank Full:
- Reduces condensation buildup in the fuel tank, especially in humid environments.
- Reduces condensation buildup in the fuel tank, especially in humid environments.
Conclusion
Proper fuel system maintenance for your Cummins C Series engine is critical to ensuring long-term performance, fuel efficiency, and engine reliability. Understanding the fuel system’s components, recognizing signs of trouble, and following preventive maintenance practices will help you avoid costly repairs and downtime.
By regularly inspecting, cleaning, and replacing key fuel system components—especially the injectors, filters, and pumps—you can keep your Cummins engine operating at peak efficiency for thousands of hours.
Injectors & Related Components for Cummins 6C Marine & Industrial Engines
Injectors & Related Components for Cummins 6CT Marine & Industrial Engines
Injectors & Related Components for Cummins 6CTA Marine & Industrial Engines
Fuel System & Related Components for Cummins 6C Marine & Industrial Engines
Fuel System & Related Components for Cummins 6CT Marine & Industrial Engines
Fuel System & Related Components for Cummins 6CTA Marine & Industrial Engines