Personal Safety General Safety Guidelines For Working On Detroit Diesel 149 Series Engines (8V149, 12V149, 16V49)
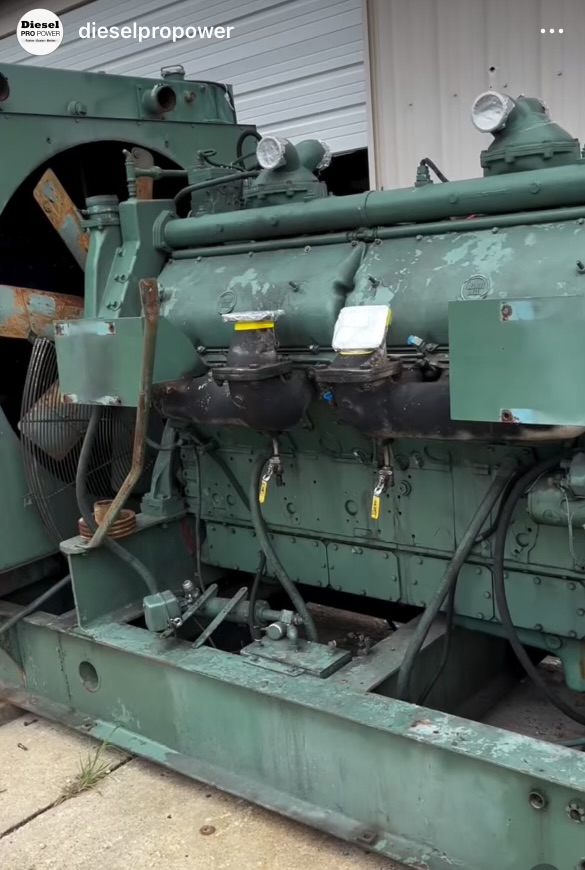
When working on heavy-duty engines like the Detroit Diesel 149 Series, following strict safety protocols is essential to prevent accidents and injuries. These engines, known for their power and large moving parts, require careful handling and attention to safety at every step of maintenance and repair. Key areas for personal safety include the use of protective gear, precautions around moving parts, and proper handling of chemicals.
Protective Gear Gear For Detroit Diesel 149 Series Engines (8V149, 12V149, 16V149)
Using the correct protective gear is essential when servicing Detroit Diesel 149 Series engines. These engines operate under high pressures and temperatures, and working around them exposes technicians to various risks, including flying debris, hot surfaces, and sharp edges. Wearing appropriate gear significantly reduces these risks.
- Eye Protection:
Safety goggles or face shields are vital to protect against debris, fuel spray, and other contaminants. Activities such as grinding, drilling, or cleaning parts with compressed air can send metal fragments or particles flying, which can cause serious eye injuries if unprotected. Safety goggles also protect against accidental splashes from fuel, oil, and cleaning chemicals.
- Gloves and Hand Protection:
Durable, oil-resistant gloves protect hands from sharp edges, hot surfaces, and contact with oils, solvents, or fuel. Engine parts like pistons, bearings, and gears can have sharp edges that cause cuts or abrasions, while contact with hot components or chemicals can cause burns or skin irritation. Proper gloves ensure hands are shielded from these hazards without limiting dexterity.
- Hearing Protection:
These engines are often very loud when running, and prolonged exposure to high noise levels can lead to hearing damage. Earplugs or earmuffs should be worn during testing or when engines are running to prevent long-term hearing loss, especially when working in confined spaces where noise levels are amplified.
- Protective Clothing and Footwear:
Overalls and steel-toed boots provide an added layer of protection against potential hazards. Overalls keep clothing clean from oil and grease while offering a barrier against minor burns and chemical splashes. Steel-toed boots protect feet from dropped tools or heavy components.
Cautions with Moving Parts
Detroit Diesel engines contain powerful moving parts, including belts, pulleys, fans, and crankshafts, that can cause severe injuries if not handled carefully. It’s essential to ensure that the engine is completely shut down and cannot be started accidentally when working near these components.
- Engine Off and Battery Disconnected:
Always turn the engine off and disconnect the battery before working near any moving parts. This precaution prevents accidental starts, which could engage belts, pulleys, or fans, creating a serious risk of entanglement or injury. Lockout-tagout procedures are recommended in settings where multiple people may be working on the engine to ensure no one accidentally starts the engine.
- Avoiding Loose Clothing and Jewelry:
When working around moving parts, avoid wearing loose clothing, jewelry, or watches, as these can easily become entangled in belts, pulleys, or fans. Entanglement can lead to severe injuries, including broken bones or cuts, especially in high-speed parts like cooling fans.
- Using Guards and Shields:
Many engines come equipped with protective guards or shields around moving parts. These should always be kept in place unless maintenance requires removal. Guards protect technicians by keeping hands, clothing, and tools away from dangerous parts, such as the fan blades and belts.
Chemical Handling
Handling chemicals is an integral part of engine maintenance, from using solvents to clean parts to dealing with fuels and lubricants. Proper handling of these chemicals is essential to protect against skin irritation, respiratory issues, and potential poisoning. Ventilation, protective equipment, and awareness of hazardous substances are all critical.
- Proper Ventilation: Always work in a well-ventilated area when handling solvents, fuel, or other chemicals to avoid inhaling fumes, which can be toxic or flammable. When working indoors, use exhaust fans or open windows to keep air circulating and minimize exposure to fumes. For confined spaces, respiratory masks with appropriate filters are recommended.
- Handling Solvents Safely: Solvents, including degreasers and parts cleaners, are common in engine maintenance but can be hazardous. Avoid using solvents like carbon tetrachloride, which is toxic and can damage the liver, kidneys, and central nervous system. Substitute safer alternatives when possible, and always wear gloves and eye protection when handling any solvent. If a spill occurs, clean it immediately to prevent fumes from accumulating.
- Storing and Disposing of Chemicals: Store chemicals in clearly labeled, approved containers away from heat sources, as some are highly flammable. Dispose of used oils, solvents, and other chemicals following environmental guidelines to avoid contamination. Many service facilities provide designated disposal containers for hazardous materials, reducing environmental impact and ensuring safe disposal practices.
- Avoiding Skin Contact and Ingestion: Avoid direct contact with chemicals by wearing gloves and washing hands thoroughly after handling them. Many chemicals used in engine maintenance can cause skin irritation or burns. Never siphon fuel or other liquids by mouth, as ingestion can lead to severe poisoning. In case of accidental ingestion or exposure, seek medical attention immediately.
By following these safety protocols—using appropriate protective gear, exercising caution with moving parts, and handling chemicals responsibly—technicians and operators can reduce the risk of accidents and injuries while working on Detroit Diesel 149 Series engines. These preventive measures ensure a safer work environment, allowing maintenance and repairs to be completed efficiently and effectively.
Engine Safety For Detroit Diesel 149 Series Engines (8V149, 12V149, 16V49)
Ensuring engine safety is paramount when working on Detroit Diesel 149 Series engines. These powerful, heavy-duty engines have large, complex components and electrical systems that require specific precautions to protect both the operator and the equipment. Key areas of focus include disconnecting the battery to prevent accidental starting and following proper lifting techniques to handle heavy components safely.
Battery Disconnect: Precautions to Avoid Accidental Starting
Disconnecting the battery is a critical first step before beginning any maintenance or repair work on the engine. The Detroit Diesel 149 Series engines use powerful batteries to operate, and accidental starting during maintenance can pose serious risks, including injury from moving parts or damage to engine components. Properly disconnecting the battery reduces the risk of unexpected starts and ensures a safe working environment.
- Complete Power Isolation:
Before starting any work, disconnect the battery cables completely, isolating the power source from the engine. This prevents any possibility of electrical engagement that could trigger the starter. Be sure to disconnect both the positive and negative terminals to ensure full isolation.
- Use of Lockout-Tagout (LOTO):
In professional or shared workshop settings, lockout-tagout procedures provide additional safety. Locking out the battery with a tag indicating the maintenance work underway prevents accidental reconnection by another technician. This safety measure is particularly useful when multiple workers may be accessing the same equipment.
- Discharge Stored Electrical Energy:
Some engine systems store residual electrical energy, even after the battery is disconnected. Allow time for capacitors or other components to fully discharge before proceeding with maintenance. This can prevent accidental sparks or minor shocks, especially when working with electrical components or near fuel systems.
- Disconnecting Additional Power Sources:
Besides the main battery, ensure any auxiliary power sources, such as secondary batteries or external power supplies, are also disconnected. This comprehensive approach helps ensure that the engine remains completely de-energized throughout the maintenance process, minimizing the chance of unexpected starts.
Proper Lifting Techniques: Securing Heavy Components Correctly
The Detroit Diesel 149 Series engines consist of substantial, heavy components that can be hazardous to lift or move without the proper equipment and techniques. Using safe lifting methods and securing heavy parts are essential for both personal safety and equipment protection. Proper handling minimizes the risk of injury from dropped parts, strains, or accidents due to improperly secured items.
- Using Engine Lifter Brackets as Recommended:
The 149 Series engines are equipped with designated lifting brackets engineered to support their weight safely. Always use these lifting points or brackets specifically recommended by Detroit Diesel. Attaching lifting devices to non-designated points can lead to structural damage or even cause the component to slip, increasing the risk of injury or engine damage.
- Choosing the Right Lifting Equipment:
For lifting large components such as cylinder heads, blocks, or turbochargers, use hoists, cranes, or hydraulic jacks rated for the appropriate weight capacity. These heavy-duty lifting tools provide stability and reduce strain on technicians, helping to prevent musculoskeletal injuries. Ensure that lifting slings or chains are securely attached and tested for weight limits that match or exceed the component’s weight.
- Securing Components Before Lifting:
Before moving any heavy part, confirm that the component is stable and balanced to avoid shifting or slipping during the lift. For irregularly shaped items, use additional supports or rigging to ensure they remain steady while being lifted. Stabilizing each part prevents unexpected movements that could result in injury or damage.
- Avoiding Manual Lifting of Heavy Parts:
Components like pistons, crankshafts, and heads are often too heavy for manual lifting without risk of strain or injury. Avoid lifting these by hand and instead rely on lifting devices or a team lift with appropriate techniques. If manual lifting is necessary for smaller parts, follow proper lifting techniques: keep your back straight, lift with your legs, and avoid twisting movements.
- Clear Pathways and Workspaces:
Before moving large components, ensure that the pathway and surrounding workspace are clear of obstacles. This preparation helps prevent tripping or dropping heavy parts, allowing for smooth and safe movement. If transporting parts across longer distances, use carts or dollies to reduce strain.
- Gradual and Controlled Movements:
When lowering components back into place or positioning them for installation, proceed slowly and in a controlled manner to avoid sudden drops. Gradual movements reduce the likelihood of misalignment, accidental damage, or injury. Using adjustable lifting devices allows precise control, particularly when aligning heavy parts during reassembly.
Following these engine safety practices—disconnecting the battery to prevent accidental starts and using proper lifting techniques for heavy components—ensures a safer working environment when maintaining or repairing Detroit Diesel 149 Series engines. These precautions help protect operators and equipment, reducing the risk of injury and ensuring that the engine remains in optimal condition throughout its service life.
Workspace Setup For Detroit Diesel 149 Series Engines (8V149, 12V149, 16V49)
Setting up a well-organized workspace is essential for maintaining the integrity and cleanliness of sensitive components in the Detroit Diesel 149 Series engines. These engines have complex systems and high-precision parts that can be compromised by contamination from dirt, dust, or foreign particles. A clean, orderly workspace not only promotes efficiency but also ensures that maintenance and repair tasks can be completed safely and effectively. Key elements of workspace setup include maintaining a clean area and preparing tools for quick, organized access.
Clean Workspace: Importance of a Clean, Organized Area
Maintaining a clean workspace is crucial when working on heavy-duty engines like the 8V149, 12V149, and 16V149 models. The engine’s internal components—such as pistons, injectors, and cylinder heads—are highly sensitive to contamination. Even minor dirt or debris can damage these parts, leading to premature wear, reduced engine efficiency, or malfunctions. A clean workspace reduces the risk of contamination, supporting the engine’s reliability and performance.
- Protection of Sensitive Components: During disassembly and reassembly, the workspace should be free from dust, oil spills, and metal shavings. Internal components like fuel injectors and turbochargers require absolute cleanliness to prevent issues such as clogging or abrasion. Dust or metal particles can affect their performance and potentially lead to failures.
- Organized Surfaces: Designate clean, spacious work surfaces for holding engine parts, tools, and small components during maintenance. Use workbenches with non-slip, easy-to-clean surfaces, and cover benches with clean cloths or mats to protect parts from scratches. Designated surfaces help keep the area tidy and prevent tools or parts from getting mixed up or lost.
- Regular Cleaning Routines: Establish a cleaning routine to keep the workspace in optimal condition before, during, and after maintenance tasks. This includes wiping down surfaces, sweeping floors, and ensuring all spills are immediately cleaned to avoid slips or contamination. Consider using compressed air to blow dust off tools and surfaces, but do so away from sensitive parts to avoid recontaminating cleaned components.
- Storage of Parts and Supplies: Store frequently used parts and supplies, such as oil, lubricants, and replacement gaskets, in clearly labeled, easily accessible containers. This practice keeps the workspace uncluttered, reducing the likelihood of contamination from spilled fluids or misplaced parts. Use cabinets with sealed doors to store smaller parts and containers to protect them from dust.
- Contamination Prevention: To prevent contamination of sensitive parts, wear disposable gloves and use clean lint-free cloths when handling internal engine components. Avoid placing parts directly on the floor or other dirty surfaces; instead, use clean, designated areas or parts trays. If possible, set up a separate, enclosed clean room or area specifically for working with critical components.
Tool Preparation: Recommendations for Quick, Organized Access
Proper tool preparation and organization are essential for efficient maintenance and repair work. Keeping tools accessible, clean, and organized ensures that tasks are completed smoothly and reduces the risk of errors or delays. With Detroit Diesel 149 Series engines, having the right tools on hand and within easy reach supports a seamless workflow and helps prevent accidental contamination of engine components.
- Tool Storage and Organization: Use toolboxes, pegboards, or shadow boards to keep tools organized and in designated areas. Shadow boards, in particular, allow you to see at a glance which tools are in use or missing, ensuring nothing is left inside the engine or misplaced. An organized setup prevents tools from being scattered around, reducing the chance of losing important items.
- Dedicated Tool Stations for Specific Tasks: Consider setting up tool stations tailored to specific tasks, such as engine disassembly, valve adjustments, or fuel system maintenance. This arrangement keeps specialized tools, such as torque wrenches or injector pullers, readily accessible when needed. Grouping tools by task streamlines the workflow and minimizes the time spent searching for the right tool.
- Cleaning and Inspection of Tools: Before using any tool, inspect it for cleanliness and condition. Dirty or damaged tools can introduce contaminants into the engine, while worn-out tools may not perform effectively, risking damage to components. Regularly clean and inspect tools, wiping them down after each use, and ensure they are stored in a clean environment.
- Accessibility of Frequently Used Tools: Place frequently used tools within easy reach, ideally on a nearby workbench or in a tool chest with top storage. This reduces the time spent retrieving commonly needed tools, such as screwdrivers, pliers, and wrenches. For larger tools like torque wrenches or engine hoists, keep them in designated spaces within the immediate work area for easy access.
- Use of Tool Trays and Carts: Tool trays and rolling carts allow you to keep essential tools close to the engine, especially useful when moving around the workspace or working on large engines like the 149 Series. Trays keep smaller tools organized and prevent them from being misplaced. Carts with multiple levels can be used to separate tools for different tasks, adding to workflow efficiency.
- Protective Tool Covers: When not in use, protect tools with covers or keep them in drawers to prevent dust buildup. Specialized tools for sensitive tasks, like injector calibration or valve adjustments, should be stored in protective cases or bags to keep them in pristine condition.
By maintaining a clean workspace and organizing tools for quick access, technicians working on Detroit Diesel 149 Series engines can ensure a smooth and safe workflow. These practices prevent contamination, improve efficiency, and help preserve the integrity of the engine’s components, leading to better maintenance outcomes and enhanced engine reliability.
Parts Catalog for Detroit Diesel 8V149 Engine
Parts Catalog for Detroit Diesel 12V149 Engine
Parts Catalog for Detroit Diesel 16V149 Engine