
Injector Removal and Installation, Fuel Line Inspection and Testing, Fuel Inlet and Drain Line Restriction Testing, and Air in Fuel System Troubleshooting
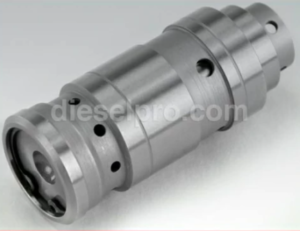
The injectors and fuel lines of the Cummins ISM, ISMe, and QSM11 engines play a critical role in fuel delivery and combustion efficiency. The injectors must deliver precise amounts of fuel at high pressure into the combustion chamber, while the fuel lines must transport fuel without leaks or restrictions.
A faulty injector or fuel line can result in power loss, excessive fuel consumption, rough idling, black or white smoke, and difficulty starting. Routine inspection, testing, and maintenance of the injectors and fuel lines are essential for ensuring engine performance, fuel efficiency, and emissions compliance.
This guide provides a detailed step-by-step process for removing and installing injectors, inspecting and testing fuel lines, diagnosing inlet and drain line restrictions, and troubleshooting air in the fuel system.
For specific torque values, injection timing adjustments, and service intervals, consult an OEM service manual or contact Diesel Pro Power for expert guidance.
Parts Catalog for ISM Cummins Marine and Industrial Engines
Fuel System & Related Components for Cummins ISM engine
Injector & Related Components for Cummins ISM engine
Parts Catalog for QSM11 Cummins Marine and Industrial Engines
Fuel System & Related Components for Cummins QSM11 engine
Injector & Related Components for Cummins QSM11 engine
Injector Removal and Installation for Cummins ISM, ISMe, and QSM11
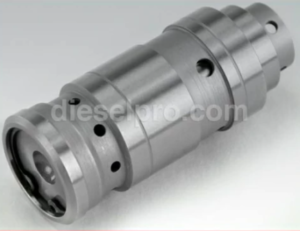
The fuel injectors in Cummins ISM, ISMe, and QSM11 engines are electronically controlled and must be installed with precision to ensure correct fuel delivery and spray pattern.
Step 1: Preparing for Injector Removal
- Shut Down the Engine and Allow it to Cool
- Work on a cold engine to avoid burns and component damage.
- Work on a cold engine to avoid burns and component damage.
- Disconnect the Battery to Prevent Accidental Cranking
- Remove the negative (-) battery cable.
- Remove the negative (-) battery cable.
- Relieve Fuel System Pressure
- Remove the fuel pump fuse and crank the engine for 5–10 seconds.
- Remove the fuel pump fuse and crank the engine for 5–10 seconds.
- Remove the Valve Cover
- Loosen the valve cover bolts and carefully lift off the cover.
- Inspect the gasket for wear or cracks before reinstallation.
Step 2: Removing the Injectors
- Disconnect the Injector Wiring Harness
- Unplug the electrical connectors from each injector.
- Label each connector for easy reinstallation.
- Remove the Fuel Injector Hold-Down Bolts
- Loosen the injector hold-down bolts evenly to prevent stress on the cylinder head.
- Loosen the injector hold-down bolts evenly to prevent stress on the cylinder head.
- Extract the Fuel Injectors from Their Bores
- Use an injector puller tool to carefully remove each injector.
- If the injectors are stuck, apply penetrating oil and gently rotate them to loosen deposits.
- Inspect the Injector Seals and O-Rings
- Check for cracked, worn, or damaged seals.
- If necessary, replace with new Cummins-approved seals.
Step 3: Installing New or Reconditioned Injectors
- Lubricate the Injector O-Rings and Sealing Surfaces
- Apply clean engine oil or assembly lube to prevent damage during installation.
- Apply clean engine oil or assembly lube to prevent damage during installation.
- Insert the Injectors into Their Respective Cylinders
- Ensure the injector nozzles align with the fuel spray chamber.
- Ensure the injector nozzles align with the fuel spray chamber.
- Tighten the Injector Hold-Down Bolts
- Torque the bolts to manufacturer specifications in the correct sequence.
- Torque the bolts to manufacturer specifications in the correct sequence.
- Reconnect the Electrical Harness and Valve Cover
- Secure the injector wiring connectors and replace the valve cover gasket if worn.
- Secure the injector wiring connectors and replace the valve cover gasket if worn.
- Prime the Fuel System and Start the Engine
- Cycle the ignition ON and OFF multiple times to purge air.
- Check for fuel leaks and verify smooth operation.
Fuel Line Inspection and Testing for Cummins ISM, ISMe, and QSM11
The fuel lines deliver fuel from the tank to the injectors under high pressure. Any leaks, blockages, or restrictions can cause fuel starvation and loss of power.
Step 1: Inspecting Fuel Lines for Wear and Leaks
- Perform a Visual Inspection
- Look for cracks, leaks, or fuel stains along the lines.
- Look for cracks, leaks, or fuel stains along the lines.
- Check for Loose or Damaged Fittings
- Ensure fuel connections are tight and free from corrosion.
- Ensure fuel connections are tight and free from corrosion.
- Use a Flashlight to Inspect for Fuel Leaks
- Run the engine at idle and full load and check for leaks.
- Run the engine at idle and full load and check for leaks.
Step 2: Testing Fuel Line Pressure and Flow
- Connect a Fuel Pressure Gauge to the Fuel Rail
- Normal idle fuel pressure: 25–35 psi
- Normal cranking pressure: 40–50 psi
- Check for Pressure Drops While Running
- A sudden pressure drop may indicate a leaking injector or weak fuel pump.
- A sudden pressure drop may indicate a leaking injector or weak fuel pump.
- Inspect Return Line Flow
- Measure the flow rate of the return line to detect restrictions.
- Measure the flow rate of the return line to detect restrictions.
Fuel Inlet and Drain Line Restriction Testing
Fuel inlet and drain line restrictions can cause fuel starvation, high fuel consumption, and rough engine performance.
Step 1: Identifying Symptoms of Fuel Line Restrictions
Symptom | Possible Cause | Recommended Actions |
Engine stalls at high RPM | Fuel inlet line restriction | Inspect and clean fuel inlet lines |
Excessive smoke | Restricted fuel drain line | Check for debris in drain line |
Loss of power under load | Blocked fuel filter or return line | Replace fuel filter, inspect return lines |
Step 2: Testing Fuel Inlet Line Restrictions
- Use a Vacuum Gauge on the Fuel Line
- Connect a vacuum gauge before the fuel pump.
- Excessive vacuum pressure (>5 inHg) indicates a restriction in the fuel inlet line.
- Inspect and Clean the Fuel Line
- Remove debris, kinks, or collapsed sections.
- Ensure proper routing of fuel lines to prevent restrictions.
Step 3: Testing Fuel Drain Line Restrictions
- Measure Fuel Return Flow with a Flow Meter
- Restricted return flow may cause excessive fuel pressure at the injectors.
- Restricted return flow may cause excessive fuel pressure at the injectors.
- Inspect the Drain Line for Clogs or Bends
- Clean the line using compressed air or fuel system cleaner.
- Clean the line using compressed air or fuel system cleaner.
Air in Fuel System Troubleshooting for Cummins ISM, ISMe, and QSM11
Air in the fuel system can lead to hard starting, rough idling, and reduced fuel injection efficiency.
Step 1: Identifying Symptoms of Air in the Fuel System
✔ Engine sputters or stalls after startup
✔ Bubbles in the fuel filter or fuel lines
✔ Loss of power under acceleration
✔ Excessive cranking before engine starts
Step 2: Diagnosing Air Leaks in the Fuel System
- Check for Bubbles in the Fuel Filter Housing
- Remove the fuel filter and inspect for air bubbles.
- Remove the fuel filter and inspect for air bubbles.
- Use a Clear Fuel Line to Detect Air Entry
- Replace a section of the fuel supply line with clear tubing.
- Watch for air bubbles forming during operation.
- Perform a Fuel System Pressure Test
- A drop in pressure may indicate leaks or air intrusion.
- A drop in pressure may indicate leaks or air intrusion.
Step 3: Fixing Air Leaks in the Fuel System
- Replace Faulty Seals and Clamps
- Inspect and replace damaged O-rings, gaskets, and hose clamps.
- Inspect and replace damaged O-rings, gaskets, and hose clamps.
- Prime the Fuel System After Repair
- Cycle the ignition ON and OFF multiple times to remove trapped air.
- Cycle the ignition ON and OFF multiple times to remove trapped air.
Final Notes on Fuel System Maintenance for Cummins ISM, ISMe, and QSM11
✔ Use high-quality diesel fuel and filters to prevent clogging and injector damage.
✔ Inspect fuel lines regularly to catch leaks early.
✔ Prime the fuel system properly after any service to remove air pockets.
✔ Follow OEM torque specifications when reinstalling injectors and fuel lines.
✔ Consult Diesel Pro Power for expert guidance and replacement parts.
By following these detailed procedures, you can ensure optimal fuel delivery, improved engine efficiency, and extended service life for Cummins ISM, ISMe, and QSM11 engines.
Parts Catalog for ISM Cummins Marine and Industrial Engines
Fuel System & Related Components for Cummins ISM engine
Injector & Related Components for Cummins ISM engine
Parts Catalog for QSM11 Cummins Marine and Industrial Engines
Fuel System & Related Components for Cummins QSM11 engine
Injector & Related Components for Cummins QSM11 engine