Beyond injector timing and valve clearance adjustments, regular tune-ups also involve thorough inspections of major engine components to identify wear and tear. Identifying and addressing signs of wear early helps prevent more severe damage and extends the engine’s operational life.
Cylinder Block Inspection for Detroit Diesel 149 Series Engines (8V149, 12V149, 16V149)
The cylinder block is the primary structural component of the engine, supporting the cylinders, crankshaft, bearings, and cooling and lubrication systems. Regular inspection of the cylinder block is essential for detecting early signs of wear, damage, or failure that could lead to costly repairs or operational downtime. Follow these steps and recommendations for a thorough inspection:
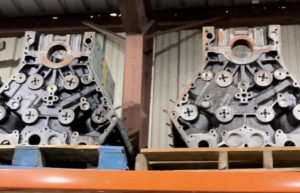
1. Key Areas to Inspect
- High-Stress Zones:
- Pay special attention to areas prone to cracking due to thermal and mechanical stress:
- Bolt Holes: Cracks often develop around bolt holes due to uneven torque application or thermal cycling.
- Cylinder Walls: Inspect the walls for signs of cracking, warping, or pitting caused by wear or improper coolant maintenance.
- Deck Surface: Check for surface flatness and cracks near coolant and oil passage openings.
- Bolt Holes: Cracks often develop around bolt holes due to uneven torque application or thermal cycling.
- Pay special attention to areas prone to cracking due to thermal and mechanical stress:
- Leak Points:
- Inspect areas where coolant or oil circulates for evidence of leaks:
- Look for dried residue, discoloration, or pooling around seals, gaskets, or fittings.
- Ensure coolant and oil passages are free of blockages or corrosion that could reduce flow efficiency.
- Inspect areas where coolant or oil circulates for evidence of leaks:
- Warping:
- Use a straight edge and feeler gauge to check the flatness of the cylinder block’s deck. Warping can compromise head gasket sealing and lead to coolant or oil leaks.
- Warping is often caused by overheating or improper torque during reassembly.
2. Tools for Inspection
- Flashlight and Inspection Mirror:
- A bright flashlight combined with an inspection mirror allows you to examine hard-to-reach areas for cracks or damage.
- A bright flashlight combined with an inspection mirror allows you to examine hard-to-reach areas for cracks or damage.
- Magnetic Particle Inspection (MPI):
- For ferrous materials, MPI can detect surface and near-surface cracks. This non-destructive test highlights defects that are invisible to the naked eye.
- For ferrous materials, MPI can detect surface and near-surface cracks. This non-destructive test highlights defects that are invisible to the naked eye.
- Dye Penetrant Testing:
- Apply a dye penetrant to the block’s surface to identify hairline cracks. This method is especially useful for detecting cracks in non-ferrous components.
- Apply a dye penetrant to the block’s surface to identify hairline cracks. This method is especially useful for detecting cracks in non-ferrous components.
- Pressure Testing:
- Apply pressurized air or fluid to the cooling and lubrication passages to detect leaks or weak points.
3. Inspection Process
- Visual Examination:
- Clean the cylinder block thoroughly using a solvent or steam cleaning process to remove dirt, oil, and grease.
- Inspect all visible surfaces for cracks, corrosion, or wear. Look for discoloration or deposits that could indicate coolant or oil leaks.
- Check for Cracks:
- Focus on high-stress areas, using a flashlight or dye penetrant to highlight minor cracks.
- For structural verification, use MPI if the block material allows.
- Inspect for Leaks:
- Look for evidence of past or active leaks around gasket surfaces, coolant passages, and oil galleries.
- Pressure-test the block to confirm the integrity of internal passageways.
- Verify Warping:
- Use a straight edge and feeler gauge to measure deck flatness. Refer to Detroit Diesel specifications for acceptable tolerances.
- A warped block may require resurfacing or replacement to ensure proper sealing with the cylinder head.
4. Preventive Measures
- Torque Properly:
- Ensure all bolts are torqued to manufacturer specifications during assembly to reduce stress on the cylinder block.
- Ensure all bolts are torqued to manufacturer specifications during assembly to reduce stress on the cylinder block.
- Maintain Cooling System:
- Use high-quality coolant with appropriate corrosion inhibitors to protect cylinder walls and cooling passages.
- Use high-quality coolant with appropriate corrosion inhibitors to protect cylinder walls and cooling passages.
- Regular Cleaning:
- Clean the block during every major service interval to prevent buildup of oil, grease, or deposits that could mask damage or contribute to corrosion.
- Clean the block during every major service interval to prevent buildup of oil, grease, or deposits that could mask damage or contribute to corrosion.
- Monitor Operating Temperatures:
- Prevent overheating by ensuring the cooling system is functioning properly, with no blockages in the block’s coolant passages.
Cylinder Head Inspection for Detroit Diesel 149 Series Engines (8V149, 12V149, 16V149)
The cylinder head plays a critical role in the operation of Detroit Diesel 149 Series engines, housing essential components such as the valves, injectors, and cooling passages. Regular inspection of the cylinder head during tune-ups is vital to ensure engine reliability, prevent performance issues, and identify early signs of damage or wear.

Importance of Cylinder Head Inspection
- Key Functions:
- The cylinder head seals the top of the engine block and forms the combustion chamber.
- It houses intake and exhaust valves, fuel injectors, and coolant passages that regulate temperature and manage the airflow necessary for combustion.
- Common Issues:
- Warping: Caused by overheating, leading to poor sealing with the engine block and head gasket failure.
- Cracks: Develop due to thermal stress, particularly around high-stress areas like valve seats or coolant passages.
- Valve Seat Wear: Results in reduced sealing, leading to compression loss and poor combustion efficiency.
Inspection Process
- Visual Inspection for Surface Damage:
- Clean the Cylinder Head:
- Before inspection, clean the cylinder head thoroughly using a solvent or steam cleaning process to remove carbon deposits, grease, and oil.
- Before inspection, clean the cylinder head thoroughly using a solvent or steam cleaning process to remove carbon deposits, grease, and oil.
- Check for Cracks:
- Inspect high-stress areas around valve seats, injector ports, and coolant passages for cracks. Use a flashlight or magnifying glass to identify hairline cracks that may not be visible to the naked eye.
- Inspect high-stress areas around valve seats, injector ports, and coolant passages for cracks. Use a flashlight or magnifying glass to identify hairline cracks that may not be visible to the naked eye.
- Dye Penetrant Testing:
- Apply a dye penetrant to detect fine surface cracks that may not be visible during a standard visual inspection.
- Apply a dye penetrant to detect fine surface cracks that may not be visible during a standard visual inspection.
- Clean the Cylinder Head:
- Inspect for Warping:
- Use a Straight Edge:
- Place a precision straight edge across the deck surface of the cylinder head.
- Check for gaps with a feeler gauge at multiple points, especially near coolant and oil passage openings.
- Measure Against Tolerances:
- Compare the feeler gauge readings to the manufacturer’s allowable warping limits. Warping beyond tolerances requires resurfacing or replacement of the cylinder head.
- Compare the feeler gauge readings to the manufacturer’s allowable warping limits. Warping beyond tolerances requires resurfacing or replacement of the cylinder head.
- Use a Straight Edge:
- Examine Valve Seats and Guides:
- Valve Seat Wear:
- Inspect valve seats for pitting, erosion, or loss of material that may prevent proper sealing with the valves.
- Inspect valve seats for pitting, erosion, or loss of material that may prevent proper sealing with the valves.
- Valve Guides:
- Check the guides for wear or looseness, which can lead to improper valve alignment and reduced compression efficiency.
- Check the guides for wear or looseness, which can lead to improper valve alignment and reduced compression efficiency.
- Valve Seat Wear:
- Check Coolant Passages:
- Inspect the coolant passages for signs of blockages, corrosion, or cracks that could result in coolant leaks.
- Ensure passages are clean and free of debris to maintain optimal cooling performance.
Tools and Techniques
- Straight Edge and Feeler Gauge:
- Use a straight edge and feeler gauge to measure warping and flatness of the cylinder head deck.
- Recommended clearance tolerance: Refer to Detroit Diesel specifications.
- Dye Penetrant or Magnetic Particle Inspection (MPI):
- For crack detection, use a dye penetrant for non-ferrous heads or MPI for ferrous materials.
- For crack detection, use a dye penetrant for non-ferrous heads or MPI for ferrous materials.
- Pressure Testing:
- Apply pressurized air or coolant to the cylinder head passages to detect leaks or weak points. Submerge the cylinder head in water during testing to identify bubbles from leaks.
When to Repair or Replace
- Warped Cylinder Heads:
- Minor warping within allowable tolerances can be corrected by machining or resurfacing the deck.
- Severe warping requires replacement to avoid further damage to the engine block or head gasket.
- Cracked Cylinder Heads:
- Small, non-structural cracks may be repaired by welding or sealing, but cracks near valve seats or coolant passages often require replacement.
- Small, non-structural cracks may be repaired by welding or sealing, but cracks near valve seats or coolant passages often require replacement.
- Damaged Valve Seats:
- Regrind or replace valve seats to restore proper sealing and compression.
Preventive Measures
- Monitor Engine Temperatures:
- Overheating is the primary cause of warping and cracks. Regularly check and maintain the cooling system to prevent excessive temperatures.
- Overheating is the primary cause of warping and cracks. Regularly check and maintain the cooling system to prevent excessive temperatures.
- Proper Torque Procedures:
- Follow manufacturer-recommended torque specifications and sequences when reassembling the cylinder head to prevent uneven stress.
- Follow manufacturer-recommended torque specifications and sequences when reassembling the cylinder head to prevent uneven stress.
- Regular Maintenance:
- Clean the cylinder head and inspect it during every major service interval to catch potential issues early.
Valve Wear Inspection for Detroit Diesel 149 Series Engines (8V149, 12V149, 16V149)
Exhaust and intake valves in Detroit Diesel 149 Series engines endure extreme heat and pressure during each combustion cycle. Over time, these conditions can lead to wear and damage, impacting the valves’ ability to seal effectively. Regular inspection and maintenance of valves and their seats are critical for maintaining compression and ensuring optimal engine performance.

Common Causes of Valve Wear
- Heat and Pressure:
- Exhaust valves are particularly vulnerable due to exposure to hot combustion gases, leading to pitting or burning.
- Intake valves, though less exposed to heat, can still experience wear due to contamination or improper seating.
- Corrosion and Deposits:
- Carbon buildup from incomplete combustion can erode valve surfaces and affect sealing.
- Corrosive gases from fuel or coolant leaks may attack valve materials.
- Improper Maintenance:
- Delayed or incorrect valve clearance adjustments can lead to excessive wear on valves and seats.
Key Areas to Inspect
- Valve Faces:
- Inspect for pitting, cracks, or signs of burning. Excessive wear on the valve face reduces the ability to form a tight seal with the valve seat.
- Inspect for pitting, cracks, or signs of burning. Excessive wear on the valve face reduces the ability to form a tight seal with the valve seat.
- Valve Seats:
Valve Seats For Detroit Diesel 149 Series Engines
- Examine seats for erosion, warping, or loss of material. Damaged seats can result in poor compression and reduced engine efficiency.
- Examine seats for erosion, warping, or loss of material. Damaged seats can result in poor compression and reduced engine efficiency.
- Valve Guides:
Valve Guide For Detroit Diesel 149 Series Engines
- Check for excessive wear or looseness in the guides, which can cause valve misalignment and improper seating.
- Check for excessive wear or looseness in the guides, which can cause valve misalignment and improper seating.
- Valve Stems:
Valve Stem Seal For Detroit Diesel 149 Series Engine
- Inspect for scoring, bending, or signs of excessive wear. Damaged stems can impede smooth valve operation.
Inspection Process
- Visual Examination:
- Remove the cylinder head to access the valves.
- Clean the valves and seats to remove carbon deposits or residue, allowing for a clear inspection.
- Use a flashlight or magnifying glass to inspect for small cracks or pits.
- Check Valve Seating:
- Apply a thin layer of marking compound to the valve face and rotate it against the seat. Examine the pattern to confirm even contact.
- Uneven or partial contact indicates misalignment or wear on the valve or seat.
- Measure Valve Stem Clearance:
- Use a micrometer to measure the diameter of the valve stem and compare it to manufacturer specifications.
- Check the clearance between the valve stem and guide using a feeler gauge.
- Pressure Testing:
- For a comprehensive check, conduct a pressure test on the cylinder head to identify potential leaks around the valves.
Maintenance and Repair
- Regrinding Valves:
- Use a valve grinder to reface worn valve faces and restore a smooth, sealing surface.
- Ensure the angle of the valve matches the angle of the seat (e.g., 30° or 45°, depending on engine specifications).
- Replacing Valves and Seats:
- If valves or seats are beyond repair, replace them with high-quality components to restore compression and efficiency.
- Use a specialized seat cutter or machine shop service to replace damaged valve seats.
- Adjusting Valve Clearance:
- After reinstalling valves, adjust the valve clearance to ensure proper opening and closing during engine operation.
Preventive Measures
- Regular Tune-Ups:
- Include valve inspections and adjustments in the regular maintenance schedule to catch early signs of wear.
- Include valve inspections and adjustments in the regular maintenance schedule to catch early signs of wear.
- Quality Fuel and Lubrication:
- Use high-quality fuel and maintain proper lubrication to minimize carbon buildup and wear.
- Use high-quality fuel and maintain proper lubrication to minimize carbon buildup and wear.
- Monitor Operating Conditions:
- Avoid overheating and ensure proper engine cooling to reduce thermal stress on valves.
Piston and Cylinder Wear: Inspection and Maintenance For Detroit Diesel 149 Series (8V149, 12V149, 16V149)
The pistons and cylinders in Detroit Diesel 149 Series engines operate under high temperatures and pressures, with continuous movement during the engine cycle. Over time, this exposure can lead to wear, resulting in reduced compression, increased oil consumption, and overall performance issues. Regular inspection and maintenance are crucial to address wear and prolong engine life.

Common Causes of Wear
- Heat and Friction:
- Combustion heat and the friction from piston movement can cause scoring and scratches on the cylinder walls.
- Combustion heat and the friction from piston movement can cause scoring and scratches on the cylinder walls.
- Improper Lubrication:
-
Insufficient or degraded oil can result in increased metal-to-metal contact, accelerating wear on pistons and cylinder walls.
-
- Contamination:
- Dirt, debris, or carbon buildup entering the combustion chamber can lead to abrasions on the piston surface and cylinder walls.
- Dirt, debris, or carbon buildup entering the combustion chamber can lead to abrasions on the piston surface and cylinder walls.
- Overloading or Overheating:
- Operating the engine under excessive load or at high temperatures can weaken components and increase wear.
Key Areas to Inspect
- Cylinder Walls:
- Look for scoring, scratches, or uneven wear patterns.
- Measure the diameter at multiple points using a bore gauge to detect tapering or out-of-round conditions.
- Pistons:
- Inspect piston crowns for carbon deposits or heat damage.
- Examine the sides of the pistons for scoring or signs of abnormal wear.
- Piston Rings:
- Check for cracks, loss of tension, or excessive wear on the rings.
- Worn piston rings can result in oil blow-by (oil entering the combustion chamber) and loss of compression.
- Oil Scraper and Compression Rings:
- Inspect the oil scraper ring for signs of clogging or damage.
- Verify the fit and spring tension of the compression rings.
Inspection Process
- Disassemble and Clean:
- Remove pistons and cylinder liners from the engine.
- Clean all components thoroughly to remove carbon deposits and oil residue.
- Visual Inspection:
- Examine piston skirts and crowns for scoring, cracks, or pitting.
- Inspect the cylinder liner surfaces for scratches, wear marks, or hot spots.
- Measure Clearances:
- Use a micrometer to measure piston diameter and compare it with the cylinder bore diameter.
- Check the gap between piston rings using a feeler gauge to ensure it is within manufacturer specifications.
- Leakage Test:
- Conduct a compression test or cylinder leakage test before disassembly to identify potential areas of concern.
Repair and Maintenance
- Honing Cylinder Walls:
- If minor scratches or wear are present, use a cylinder honing tool to create a crosshatch pattern that supports oil retention and reduces friction.
- Ensure honing is performed uniformly to maintain cylinder roundness.
- Re-boring Cylinders:
- For severe wear or tapering, re-bore the cylinder to a larger size and install oversize pistons and rings.
- For severe wear or tapering, re-bore the cylinder to a larger size and install oversize pistons and rings.
- Replace Worn Pistons and Rings:
- Install a Piston Installation Kit specifically designed for Detroit Diesel 149 Series engines.
- Replace piston rings, ensuring they are correctly oriented and seated to provide optimal sealing.
- Inspect and Replace Liners:
- If the cylinder liner is cracked or excessively worn, replace it with a new liner designed for your engine configuration.
Preventive Measures
- Use High-Quality Oil:
- Maintain proper lubrication with high-quality engine oil that meets or exceeds Detroit Diesel specifications.
- Maintain proper lubrication with high-quality engine oil that meets or exceeds Detroit Diesel specifications.
- Regular Maintenance:
- Include piston and cylinder inspections during routine tune-ups to catch early signs of wear.
- Include piston and cylinder inspections during routine tune-ups to catch early signs of wear.
- Monitor Engine Temperatures:
- Prevent overheating by ensuring the cooling system is functioning correctly and free from blockages.
- Prevent overheating by ensuring the cooling system is functioning correctly and free from blockages.
- Replace Air Filters:
- Use clean, high-efficiency air filters to prevent contaminants from entering the combustion chamber.
Signs of Piston and Cylinder Wear
- Blue Smoke from Exhaust: Indicates oil entering the combustion chamber due to worn piston rings.
- Loss of Compression: Caused by poor sealing between the piston and cylinder walls.
- Increased Oil Consumption: A result of worn oil scraper rings or damaged cylinder walls.
Injector Condition: Inspection and Maintenance For Detroit Diesel 149 Series Engines (8V149, 12V149, 16V149)

The injectors in Detroit Diesel 149 Series engines play a critical role in delivering precise amounts of fuel into the combustion chamber at the correct pressure and timing. Any issues with the injectors can lead to uneven fuel distribution, incomplete combustion, increased emissions, and engine misfire. Regular inspection and maintenance of injectors are essential to ensure efficient engine operation and prevent costly repairs.
Common Signs of Injector Issues
- Poor Engine Performance:
- Reduced power output, irregular idle, or hesitation during acceleration can indicate uneven fuel distribution caused by faulty injectors.
- Reduced power output, irregular idle, or hesitation during acceleration can indicate uneven fuel distribution caused by faulty injectors.
- Increased Smoke or Emissions:
- Black smoke may result from over-fueling due to leaking injectors.
- White smoke often indicates unburned fuel caused by improper atomization.
- Fuel Leakage:
- Leaks around the injector body or nozzle can disrupt fuel pressure and lead to inefficient combustion.
- Leaks around the injector body or nozzle can disrupt fuel pressure and lead to inefficient combustion.
- High Fuel Consumption:
- Worn or clogged injectors may cause the engine to burn more fuel than necessary to achieve desired power levels.
Inspection Process
- Visual Inspection:
- Remove injectors from the engine and examine the nozzles for carbon buildup, discoloration, or pitting.
- Check the injector body for cracks, corrosion, or signs of fuel leakage.
- Spray Pattern Testing:
- Use an injector test bench to evaluate the spray pattern. A consistent, fine mist indicates proper atomization, while uneven or dripping sprays suggest clogging or internal wear.
- Use an injector test bench to evaluate the spray pattern. A consistent, fine mist indicates proper atomization, while uneven or dripping sprays suggest clogging or internal wear.
- Pressure Testing:
- Test the injectors’ ability to maintain proper fuel pressure. Injectors that fail to hold pressure or show delayed response should be cleaned or replaced.
- Test the injectors’ ability to maintain proper fuel pressure. Injectors that fail to hold pressure or show delayed response should be cleaned or replaced.
- Carbon Buildup Removal:
- Inspect the injector tips for soot and carbon deposits. Excessive buildup can block fuel flow, affecting combustion efficiency.
Maintenance Steps

- Cleaning:
- Use an ultrasonic cleaner or specialized injector cleaning solutions to remove carbon deposits and restore nozzle functionality.
- Manually clean the nozzle tips with a soft brush, ensuring no abrasive materials are used to avoid damage.
- Replacing Worn Components:
- If wear is observed on nozzles, seals, or injector bodies, replace the injector or its components with high-quality replacements specified for Detroit Diesel 149 Series engines.
- If wear is observed on nozzles, seals, or injector bodies, replace the injector or its components with high-quality replacements specified for Detroit Diesel 149 Series engines.
- Seal and O-Ring Replacement:
- Always install new seals and O-rings during injector reinstallation to prevent leaks and maintain proper fuel pressure.
- Always install new seals and O-rings during injector reinstallation to prevent leaks and maintain proper fuel pressure.
- Reinstall and Torque:
- When reinstalling injectors, ensure they are torqued to the manufacturer’s specifications to avoid over-tightening, which could damage the injector body or mounting threads.
Preventive Measures
- Use High-Quality Fuel:
- Low-quality or contaminated fuel can accelerate injector wear and clogging. Always use fuel that meets Detroit Diesel’s specifications.
- Low-quality or contaminated fuel can accelerate injector wear and clogging. Always use fuel that meets Detroit Diesel’s specifications.
- Replace Fuel Filters Regularly:
- Clean fuel filters prevent debris and contaminants from reaching the injectors, extending their lifespan.
- Clean fuel filters prevent debris and contaminants from reaching the injectors, extending their lifespan.
- Schedule Regular Inspections:
- Include injector inspections in the engine’s routine maintenance schedule to catch issues early and prevent more extensive damage.
Cooling System Check for Detroit Diesel 149 Series Engines (Marine and Non-Marine Applications) (8V149, 12V149, 16V149)
The cooling system in Detroit Diesel 149 Series engines is vital to maintaining optimal operating temperatures and preventing overheating. Whether the engine is used in marine or non-marine applications, certain components are specific to each environment, while others serve both. Proper inspection and maintenance of the cooling system are crucial for ensuring reliable performance and prolonging engine life.

Key Components in Cooling Systems
Universal Components (Marine and Non-Marine Applications)
- Water Jacket:
- Surrounds the cylinders to absorb and transfer heat from the combustion process.
- Check for signs of corrosion, scaling, or blockages that could restrict coolant flow.
- Thermostat:
Thermostat For Detroit Diesel 149 Series Engine
- Regulates the flow of coolant based on engine temperature.
- Inspect for proper operation, ensuring it opens and closes at the specified temperature range (160°F to 195°F).
- Hoses and Seals:
- Examine coolant hoses for cracks, bulges, or leaks, and inspect seals for signs of wear.
- Replace deteriorated components to prevent coolant leaks and maintain system integrity.
- Water Pump:
Detroit Diesel 16V149 Freshwater Pump
- Circulates coolant through the system.
- Inspect for bearing wear, impeller damage, and leaks around the pump housing.
- Coolant Condition:
- Ensure the coolant is clean and at the proper level. Discolored or contaminated coolant indicates the need for a flush and refill.
Marine-Specific Components
- Heat Exchanger:
Detroit Diesel 149 Series Heat Exchanger Core
- Transfers heat from the engine coolant to raw seawater. Functions similarly to a radiator in non-marine systems.
- Inspect for fouling, scaling, or corrosion in the tubes that may reduce heat transfer efficiency.
- Pressure test the exchanger for leaks.
- Raw Water Pump:
Detroit Diesel 149 Series Raw Water Pump
- Draws seawater into the cooling system for the heat exchanger.
- Inspect impellers and seals for wear caused by debris, sand, or saltwater.
- Seawater Strainer:
Sea Water Strainer
- Filters raw seawater before it enters the cooling system.
- Regularly clean the strainer to prevent blockages and maintain unrestricted water flow.
- Sacrificial Anodes:
- Installed in heat exchangers to prevent corrosion from electrolysis in seawater systems.
- Inspect and replace anodes regularly to protect metal components.
Non-Marine-Specific Components
- Radiator:
- Dissipates heat into the air through coolant circulation.
- Inspect for bent or clogged fins, as well as leaks around the core.
- Clean the radiator with compressed air or a soft brush to maintain airflow.
- Cooling Fan:
- Pulls air through the radiator to enhance heat dissipation.
- Inspect for cracks, loose mounts, or belt tension issues.
Inspection and Maintenance Procedures
- Visual Inspection:
- Examine all components for signs of leaks, rust, or wear, regardless of the system type.
- Pay close attention to connections, gaskets, and seals for evidence of coolant seepage.
- Pressure Testing:
- Use a cooling system pressure tester to identify leaks in hoses, heat exchangers, radiators, or other components.
- Monitor for pressure loss to locate weak points or cracks in the system.
- Thermostat Testing:
- Remove and test the thermostat in a controlled water bath to verify it opens and closes at the correct temperature.
- Remove and test the thermostat in a controlled water bath to verify it opens and closes at the correct temperature.
- Coolant Flow Check:
- For marine engines, ensure the raw water pump delivers sufficient seawater to the heat exchanger.
- For non-marine systems, verify coolant flow through the radiator and ensure the fan operates correctly.
- Flush the Cooling System:
- Flush the system to remove rust, scale, or debris. Use an appropriate cleaning solution for marine or non-marine applications.
- Rinse thoroughly with distilled water before refilling with fresh coolant.
- Coolant Replacement:
- Refill the system with coolant that meets Detroit Diesel specifications:
- A 50/50 mix of antifreeze and distilled water for corrosion protection and temperature regulation.
- Refill the system with coolant that meets Detroit Diesel specifications:
Preventive Measures
- Monitor Operating Temperatures:
- Regularly observe temperature gauges during operation to ensure the engine remains within the recommended range.
- Regularly observe temperature gauges during operation to ensure the engine remains within the recommended range.
- Maintain Coolant Quality:
- Test coolant for pH balance and additive levels, replacing it every 2–3 years or as recommended by Detroit Diesel.
- Test coolant for pH balance and additive levels, replacing it every 2–3 years or as recommended by Detroit Diesel.
- Clean External Components:
- For radiators and heat exchangers, remove dirt, debris, or fouling to maintain efficient heat exchange.
- For radiators and heat exchangers, remove dirt, debris, or fouling to maintain efficient heat exchange.
- Inspect Belts and Clamps:
- Check drive belts for the water pump and fan for proper tension and wear.
- Tighten or replace hose clamps to secure connections.
- Protect Against Corrosion:
- In marine systems, flush raw water systems with fresh water after use in saltwater environments.
- Replace sacrificial anodes regularly in seawater cooling systems.
Signs of Cooling System Problems
- Overheating:
- Can result from clogged passages, low coolant levels, or a malfunctioning thermostat.
- Can result from clogged passages, low coolant levels, or a malfunctioning thermostat.
- Coolant Leaks:
- Visible pooling under the engine or white residue around hoses and connections.
- Visible pooling under the engine or white residue around hoses and connections.
- Rust or Discolored Coolant:
- Indicates contamination or corrosion, reducing the effectiveness of the cooling system.
- Indicates contamination or corrosion, reducing the effectiveness of the cooling system.
- Steam or High Pressure:
- Suggests blockages or head gasket failure.
Crankshaft and Bearing Wear: Inspection and Maintenance For Detroit Diesel 149 Series Engines (8V149, 12V149, 16V149)
The crankshaft is a critical component of the Detroit Diesel 149 Series engine, converting the pistons’ linear motion into rotational energy to drive the engine. Supporting this motion are the main and connecting rod bearings, which must remain in excellent condition to ensure smooth operation. Regular inspection of the crankshaft and bearings is essential to prevent engine vibrations, performance loss, and catastrophic failures.

Common Causes of Crankshaft and Bearing Wear
- High Operating Loads:
- Prolonged exposure to high loads can lead to stress fractures or excessive wear on the crankshaft journals.
- Prolonged exposure to high loads can lead to stress fractures or excessive wear on the crankshaft journals.
- Improper Lubrication:
- Insufficient or contaminated oil reduces the protective film between moving parts, causing metal-to-metal contact and accelerated wear.
- Insufficient or contaminated oil reduces the protective film between moving parts, causing metal-to-metal contact and accelerated wear.
- Misalignment:
- Improper installation of bearings or crankshaft components can create uneven pressure, resulting in localized wear or scoring.
- Improper installation of bearings or crankshaft components can create uneven pressure, resulting in localized wear or scoring.
- Contamination:
- Dirt, metal shavings, or debris in the oil can score crankshaft surfaces and damage bearings.
Inspection Process
- Disassemble and Clean:
- Remove the crankshaft and bearings for a thorough inspection.
- Clean all components using a solvent to remove oil, grease, and debris.
- Inspect the Crankshaft:
- Journals:
- Examine main and rod journals for scoring, scratches, or cracks. Use a flashlight and magnifying glass to detect fine surface imperfections.
- Measure journal diameters with a micrometer and compare to manufacturer specifications to ensure they are within allowable tolerances.
- Crankshaft Surface:
- Check for signs of overheating, such as discoloration or heat spots.
- Look for corrosion or pitting caused by contaminants in the oil.
- Journals:
- Check Bearings:
- Visual Inspection:
- Inspect the main and connecting rod bearings for signs of wear, pitting, or deformation.
- Look for uneven wear patterns, which may indicate misalignment or insufficient lubrication.
- Thickness Measurement:
- Use a micrometer to measure bearing thickness. Bearings worn below manufacturer-specified limits must be replaced.
- Use a micrometer to measure bearing thickness. Bearings worn below manufacturer-specified limits must be replaced.
- Check for Embedded Particles:
- Inspect the bearing surfaces for dirt, debris, or metal fragments embedded in the material.
- Inspect the bearing surfaces for dirt, debris, or metal fragments embedded in the material.
- Visual Inspection:
- Measure Clearance:
- Use plastigage or a similar tool to measure the clearance between the crankshaft journals and bearings.
- Compare the clearance values to the Detroit Diesel specifications for the 149 Series engines. Excessive clearance indicates bearing wear and may require replacement.
- Inspect Balancing and Alignment:
- Check the crankshaft for proper balance and alignment. Bent or misaligned crankshafts can cause vibrations and uneven bearing wear.
Repair and Maintenance
- Crankshaft Repairs:
- Polishing:
- Minor scratches or scoring on the crankshaft journals can be removed through polishing, restoring a smooth surface.
- Minor scratches or scoring on the crankshaft journals can be removed through polishing, restoring a smooth surface.
- Grinding:
- For significant wear or scoring, journals can be ground to an undersize and matched with undersized bearings.
- For significant wear or scoring, journals can be ground to an undersize and matched with undersized bearings.
- Crack Repairs:
- Use magnetic particle inspection (MPI) to detect cracks. Cracked crankshafts must be repaired professionally or replaced if the damage is extensive.
- Use magnetic particle inspection (MPI) to detect cracks. Cracked crankshafts must be repaired professionally or replaced if the damage is extensive.
- Polishing:
- Bearing Replacement:
- Replace all worn or damaged bearings with a crankshaft bearing set designed specifically for Detroit Diesel 149 Series engines.
- Use high-quality, manufacturer-recommended bearings to ensure longevity and reliability.
- Reassembly and Torque:
- Reinstall the crankshaft and bearings according to the manufacturer’s torque specifications.
- Apply assembly lube to bearings during installation to ensure proper lubrication on startup.
Preventive Measures
- Use High-Quality Oil:
- Use lubricants that meet or exceed Detroit Diesel specifications to maintain an adequate protective film on crankshaft and bearing surfaces.
- Use lubricants that meet or exceed Detroit Diesel specifications to maintain an adequate protective film on crankshaft and bearing surfaces.
- Change Oil and Filters Regularly:
- Follow the recommended oil change intervals to prevent contamination and ensure consistent lubrication.
- Follow the recommended oil change intervals to prevent contamination and ensure consistent lubrication.
- Monitor Engine Operation:
- Pay attention to unusual vibrations, noise, or performance drops, which may indicate crankshaft or bearing wear.
- Pay attention to unusual vibrations, noise, or performance drops, which may indicate crankshaft or bearing wear.
- Follow Maintenance Schedules:
- Include crankshaft and bearing inspections during routine tune-ups to catch early signs of wear or damage.
Signs of Crankshaft and Bearing Wear
- Vibrations:
- Excessive wear or misalignment can cause engine vibrations, leading to further damage if unaddressed.
- Excessive wear or misalignment can cause engine vibrations, leading to further damage if unaddressed.
- Low Oil Pressure:
- Worn bearings increase oil clearance, reducing system pressure and leading to inadequate lubrication.
- Worn bearings increase oil clearance, reducing system pressure and leading to inadequate lubrication.
- Knocking Noise:
- Worn or loose bearings can produce a knocking sound, particularly under load or during acceleration.
- Worn or loose bearings can produce a knocking sound, particularly under load or during acceleration.
- Metal Shavings in Oil:
- Presence of metallic debris in the oil may indicate advanced wear or damage to the crankshaft or bearings.
Regular tune-ups that include injector timing, valve clearance adjustments, and comprehensive inspections for wear and tear keep the Detroit Diesel 149 Series engines in top condition. By addressing potential issues early, these tune-ups enhance the engine’s efficiency, prolong its service life, and prevent unexpected breakdowns in demanding applications.
Parts Catalog for 8V149 Detroit Diesel Marine Engine
Parts Catalog for 12V149 Detroit Diesel Marine Engine
Parts Catalog for 16V149 Detroit Diesel Marine Engine