
Overview: Components and Their Functions
The lubrication system is a critical component of Detroit Diesel V71 engines, ensuring that all moving parts operate smoothly, are protected from wear, and remain cool under extreme working conditions. By delivering clean, pressurized oil to bearings, camshafts, and other high-friction surfaces, this system reduces wear, prevents overheating, and minimizes engine maintenance costs.
Proper maintenance of the lubrication system is essential for the longevity and reliability of V71 engines. The system comprises several key components that work in unison to optimize oil circulation, maintain pressure, filter impurities, and dissipate heat.
Key Components of the Lubrication System
- Oil Pumps: Provide the necessary flow and pressure for oil distribution throughout the engine.
- Oil Pressure Regulation Valves: Stabilize oil pressure to ensure consistent lubrication across all engine speeds and temperatures.
- Oil Filters: Clean impurities from the oil to prevent damage to critical engine components.
- Oil Coolers: Regulate oil temperature by dissipating excess heat.
Each of these components plays a vital role in the overall health of the engine. A failure in any one part can lead to significant performance issues or even catastrophic engine failure.
Oil Pump for Detroit Diesel V71 Enginesfor Detroit Diesel V71 Engines
Types of Oil Pumps
Detroit Diesel V71 engines rely on robust gear-driven oil pumps to maintain the flow and pressure of oil. The type of pump varies based on the engine configuration:
- Gear-Driven Oil Pumps:
Oil Pump For Detroit Diesel 6V71 & 8V71 Engines (Left Hand)
- Commonly used in all V71 engines.
- Feature a pair of meshing spur gears (drive gear and driven gear) that create suction to draw oil from the oil pan and pressurize it for distribution.
- Mounted in the crankshaft front cover (6V71 and 8V71 engines) or on the main bearing caps (12V71 and 16V71 engines).
- Scavenging Oil Pumps:
Oil Pump for Detroit diesel engine 6V71 and 8V71
- Found in applications requiring additional oil removal or circulation, such as deep sump or marine engines.
- Typically mounted in tandem with the primary oil pump and include separate inlets for collecting oil from additional sump areas.
Oil Pump Operation
The gear-driven oil pumps operate by rotating two meshing gears. As the gears turn, they create a vacuum on the inlet side, drawing oil from the sump. The pressurized oil is then routed through galleries to the oil cooler, filters, and main oil distribution system. The pump ensures a steady supply of oil to critical components, such as the bearings, camshafts, and rocker arms, even under high load conditions.
Maintenance Procedures for Oil Pumps
- Removal:
- Drain the engine oil completely.
- Remove the oil pan to access the pump. For crankshaft-mounted pumps, remove the crankshaft front cover.
- Detach the oil inlet pipe and screen assembly.
- Inspection:
- Clean all pump components with fuel oil and dry them with compressed air.
- Inspect the gear teeth for wear or scoring.
- Measure the following clearances to ensure they meet specifications:
- Gear cavity depth: 0.982″–0.984″ for narrow gears; 1.302″–1.304″ for wide gears.
- Bushing-to-shaft clearance: 0.001″–0.0025″ (new parts) or up to 0.0035″ (used parts).
- End play between gears and cover: 0.002″–0.005″.
- Reassembly:
- Lubricate all components with clean engine oil during reassembly.
- Use self-locking bolts to secure the gear retaining plate to the pump body. Torque bolts to 13–17 lb-ft (18–23 N•m).
- Installation:
- Reinstall the oil pump, ensuring proper alignment with the drive gear on the crankshaft.
- Reattach the oil pan and refill the engine with the appropriate oil type and quantity.
Oil Pressure Regulation for Detroit Diesel V71 Engines
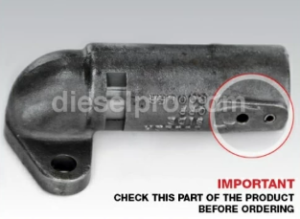
Functionality of Pressure Relief and Regulator Valves
Oil pressure regulation ensures consistent lubrication across varying engine speeds and loads. The lubrication system uses two types of valves:
- Pressure Relief Valve:
- Opens when oil pressure exceeds safe limits, routing excess oil back to the sump.
- Prevents damage to seals, gaskets, and components caused by over-pressurization.
- Pressure Regulator Valve:
- Maintains stable oil pressure, typically at 50 psi (345 kPa), regardless of temperature or engine speed.
- Allows excess oil to bypass the system and return to the sump.
Common Oil Pressure Issues and Troubleshooting
- Low Oil Pressure:
- Causes: Worn pump gears, clogged filters, or a malfunctioning regulator valve.
- Solution: Replace worn components and inspect valve springs for proper tension.
- High Oil Pressure:
- Causes: Blocked relief valve or improper oil viscosity.
- Solution: Clean or replace the relief valve and ensure the correct oil grade is used.
- Fluctuating Oil Pressure:
- Causes: Air in the oil system, loose connections, or worn bearings.
- Solution: Bleed the system, tighten connections, and inspect bearings for wear.
Maintenance and Adjustment of Pressure Valves
- Clean valve components with fuel oil and inspect for scoring or wear.
- Ensure the valve moves freely within its housing.
- Replace valve springs if they fail to meet specifications.
- Torque relief valve body bolts to 30–35 lb-ft (41–47 N•m) during reassembly.
Oil Filters for Detroit Diesel V71 Engines
Full-Flow vs. Bypass Oil Filters
- Full-Flow Filters:
- Positioned ahead of the oil cooler to filter all circulating oil.
- Equipped with a bypass valve that activates if the filter becomes clogged, allowing oil to bypass the filter and continue circulating.
- Bypass Filters:
- Supplementary filters that clean a portion of the oil at a finer level.
- Primarily used in high-performance or long-service-life applications.
Replacing the Oil Filter
- Preparation:
- Drain the oil from the filter housing using the drain plug.
- For spin-on filters, remove the filter using a strap wrench.
- Inspection and Cleaning:
- Clean the filter housing, ensuring no debris remains.
- Inspect the sealing surfaces for nicks or damage.
- Installation:
- For canister filters, install a new filter element and gasket.
- For spin-on filters, lubricate the gasket with clean oil and tighten the filter by hand until the gasket seats, then turn an additional two-thirds.
- Torque filter center studs to 50–60 lb-ft (68–81 N•m).
- Final Check:
- Refill
the engine oil and start the engine. Inspect for leaks and ensure proper oil pressure.
- Refill
Oil Coolers for Detroit Diesel V71 Engines
Types of Oil Coolers
- Plate-Type Coolers:
Oil Cooler For Detroit Diesel V71 Engines (13 Plates)
- Standard on most V71 engines. Consist of stacked plates that allow heat exchange between oil and coolant.
- Standard on most V71 engines. Consist of stacked plates that allow heat exchange between oil and coolant.
- Tube-Type Coolers:
- Used in marine applications or high-capacity systems. Oil flows through tubes surrounded by coolant for maximum heat transfer.
- Used in marine applications or high-capacity systems. Oil flows through tubes surrounded by coolant for maximum heat transfer.
Cleaning, Inspection, and Maintenance
- Cleaning:
- Flush the oil passages with 1,1,1-trichloroethane to remove sludge.
- Immerse the cooler in a solution of oxalic acid to clean the water passages.
- Inspection:
- Pressure test the cooler at 75–150 psi (517–1034 kPa) to check for leaks. Submerge the cooler in water and inspect for air bubbles.
- Replace any cooler with cracks, corrosion, or leaks.
- Reassembly:
- Install the cooler with new gaskets. Torque cooler housing bolts to 30–35 lb-ft (41–47 N•m).
- Ensure proper alignment of all connections to prevent leaks.
Importance of Lubrication System Maintenance
A well-maintained lubrication system is essential for the longevity and performance of Detroit Diesel V71 engines. Regular inspections, timely replacements of worn components, and adherence to recommended specifications will ensure optimal engine operation. By following these guidelines, technicians can safeguard against downtime, costly repairs, and premature engine failures, preserving the reliability and efficiency of these iconic engines.
Lubrication System & Related Components for Detroit Diesel 6V71 Non-Turbo Marine& Industrial Engines
Lubrication System & Related Components for Detroit Diesel 6V71 Turbo Marine& Industrial Engines
Lubrication System & Related Components for Detroit Diesel 8V71 Non-Turbo Marine& Industrial Engines
Lubrication System & Related Components for Detroit Diesel 8V71Turbo Marine& Industrial Engines
Lubrication System & Related Components for Detroit Diesel 12V71Turbo Marine& Industrial Engines
Lubrication System & Related Components for Detroit Diesel 16V71Turbo Marine& Industrial Engines