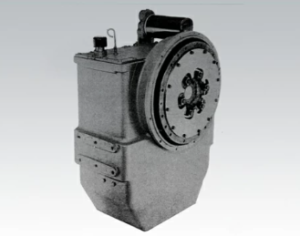
Introduction
Reassembling a Twin Disc MG516 or MG5161 marine transmission after overhaul, component repair, or deep inspection is a critical phase in the service process. Whether you’ve replaced clutch packs, refreshed seals, serviced the output shaft, or rebuilt the control valve, improper reassembly can undo all your hard work—and even damage internal components when the system is brought back online.
Parts Catalog for Twin Disc MG516 Marine Transmissions
Rebuilt Twin Disc MG516 Marine Transmissions
Plate Kit For Twin Disc MG516 Marine Transmission
Gasket Kits For Twin Disc MG516 Marine Transmission
This guide delivers expert-level tips and best practices for:
- Ensuring correct torque specification and bolt sequencing
- Using gasket sealants, anaerobic compounds, and RTV correctly
- Completing a comprehensive pre-startup inspection and system test
Disclaimer: Always refer to the official Twin Disc service manual for final torque specifications, installation procedures, and approved sealant types for your transmission’s exact configuration and serial number. This guide is designed to support accurate, high-quality work in field or shop settings.
Torque Specifications for Twin Disc MG516 Marine Gear
Proper torque application is the foundation of reliable reassembly. Under-torqued fasteners can loosen under vibration. Over-torqued bolts may damage castings, distort surfaces, or overstress threads. Always use a calibrated torque wrench and follow manufacturer torque values and tightening sequences.
Why Torque Specifications Matter
- Prevent leaks at mating flanges and covers
- Avoid crushing seals or gaskets
- Ensure uniform stress across the component
- Preserve the alignment of rotating assemblies
- Avoid thread failure or bolt breakage
- Maintain warranty validity on professional overhauls
General Torque Guidelines (Typical MG516 Values)
NOTE: Always cross-check with your exact model and serial number. These are typical values only.
Component | Torque Specification |
Oil pan bolts | 18–22 ft-lbs (24–30 Nm) |
Clutch housing cover | 45–55 ft-lbs (60–75 Nm) |
Output flange bolts | 180–220 ft-lbs (245–300 Nm) |
Valve body bolts | 10–14 ft-lbs (13–19 Nm) |
Shaft retaining nuts | 300+ ft-lbs (407+ Nm) |
Cooler hose fittings | 30–40 ft-lbs (40–54 Nm) |
Control lever mounting | 25–30 ft-lbs (34–41 Nm) |
Using a Torque Wrench Correctly
- Always zero and calibrate before use
- Use 3/8″ drive for mid-size bolts, 1/2″ or 3/4″ drive for high-torque applications
- Apply smooth, even force—never jerk the wrench
- Use anti-seize compound or thread locker only where specified
- Tighten bolts in a star or crisscross pattern to prevent warping
- For gaskets or flanges, perform progressive torqueing in two or three passes
Torque Sequencing Examples
A. Rear Cover Plate
- Use a star pattern across the cover
- Torque in stages: 25%, 50%, then 100% of final torque
- Recheck all bolts after full torque cycle
B. Output Shaft Flange
- Align bolt holes and insert all bolts finger-tight
- Torque sequentially while supporting the flange to avoid side load
- Recheck after first sea trial or 5 hours of operation
Fastener Cleaning and Preparation
- Remove all oil, dirt, and old thread sealant
- Chase threads with a tap or thread chaser
- Lubricate or apply sealant per instructions
- Replace any fastener showing thread damage, corrosion, or stretch marks
Use of Gasket Sealant and RTV for Twin Disc MG516 Marine Gear
Why Sealants Are Critical
Although many transmission gaskets provide a good seal when dry, in high-vibration and high-temperature environments like marine gear housings, a proper sealant strategy is essential. Sealants help:
- Prevent oil leaks
- Compensate for minor surface imperfections
- Improve sealing under thermal expansion
- Retain gaskets in vertical or overhead assemblies
- Extend gasket life during long-term operation
Types of Sealants Used in MG516 Service
Sealant Type | Use Case |
RTV Silicone (High Temp) | Cover plates, gear case sealing, inspection panels |
Anaerobic Gasket Maker | Close-fitting machined joints without gaskets |
Non-hardening Brush-On Sealant | Threads, pipe plugs, coolant/oil passages |
PTFE Pipe Thread Sealant | Hydraulic fittings, oil cooler lines |
Gasket Adhesive (3M Super Weatherstrip or similar) | Holding gaskets in place during assembly |
Best Practices: Using Gasket Sealants on MG516
- Clean All Surfaces Thoroughly
- Use non-chlorinated brake cleaner
- Remove old gasket material fully
- Finish with a wipe-down using lint-free cloth
- Apply Thin, Even Bead of RTV
- No more than 1/8” thick bead
- Avoid applying inside bolt holes or oil passage areas
- Do not over-apply—it can extrude into oil galleries
- Use Anaerobic Sealants for Close-Fit Metal Joints
- Apply only where flanges meet with tight tolerances
- Torque while wet—anaerobic formulas cure in the absence of air
- Brush-On Sealant for Threads
- Apply to plug threads, pipe fittings, and threaded sensors
- Avoid getting sealant inside oil passages
- Dry Fit Gaskets When Needed
- Some fiber gaskets are designed to seal dry
- Check manual for gasket-specific instructions
- Let RTV Cure Before Startup
- Most high-temp RTVs need at least 1 hour to skin over
- Full cure occurs in 24 hours but light use may be acceptable after 2–4 hours
Common Sealant Mistakes to Avoid
❌ Applying RTV inside bolt holes
❌ Mixing incompatible sealants (e.g., RTV + anaerobic)
❌ Using too much—excess can block oil passages
❌ Applying to oily or dirty surfaces
❌ Starting engine before sealant is cured
❌ Substituting plumber’s tape for PTFE paste on oil fittings
Pre-Startup Checks for Twin Disc MG516 Marine Gear
After reassembly, a careful and systematic inspection is critical before you hit the ignition switch. Even small oversights—like forgetting to tighten a drain plug or install a filter—can destroy a transmission on its first start.
Pre-Startup Inspection Categories
- Mechanical Assembly Checks
- Fluid Levels and Flow Verification
- Torque Rechecks
- Electrical and Control System Check
- Manual Rotation and Alignment
- Leak Prevention and Observation Setup
Step-by-Step Final Inspection Checklist
✅ 1. Confirm All Fasteners Are Torqued
- Use your torque log or checklist
- Recheck rear housing, flange bolts, valve body, clutch cover
- Ensure cooler fittings and plug threads are tight and sealed
✅ 2. Oil Filled to Proper Level
- Use Twin Disc-recommended oil (e.g., SAE 30 or 40 ND)
- Fill through the top fill port slowly
- Oil should reach “FULL” mark on dipstick or sight glass
- Let oil settle and recheck before cranking
✅ 3. New Filter Installed and Primed
- Replace spin-on or cartridge filter
- Fill with oil prior to installation if possible
- Check for double gaskets (old one stuck on housing)
✅ 4. Control Valve and Solenoids Connected
- Electrical connectors tight and seated
- Control cables properly aligned and greased
- If using EC300 or similar, verify calibration
✅ 5. Rotate Transmission Manually (If Possible)
- Turn output shaft by hand or with wrench
- Listen for scraping, binding, or gear clash
- Rotation should be smooth and silent
- If resistance is felt, stop and inspect
✅ 6. Inspect Seals and Breathers
- Shaft seals seated flush and not pinched
- Oil breather vent clean and unobstructed
- Drain plug and cooler lines leak-free
✅ 7. Verify Alignment with Prop Shaft
- Flanges should mate with <0.004″ deviation
- Use feeler gauges at 3, 6, 9, and 12 o’clock
- Shim feet or mounts as needed
✅ 8. Setup for Initial Start
- Transmission in neutral
- Engine cooling system functional
- Oil catch pans or absorbent pads under housing
- Have a torque wrench and pressure gauge ready
Initial Startup Procedure
- Start Engine at Idle
- Let oil circulate for 1–2 minutes
- Watch oil level and pressure
- Engage Forward and Reverse
- Shift briefly into forward and reverse
- Listen for engagement clicks and pressure stability
- Watch for leaks around filter, valve body, and shaft seals
- Warm Up Transmission
- Let oil reach ~160°F (71°C)
- Recheck oil level and top off
- Check for Foam or Contamination
- Oil should remain clear and free of bubbles
- Milky oil = water contamination
- Foamy oil = air in suction line or cooler breach
Pressure and Temperature Monitoring
- Use pressure port to verify forward/reverse clutch pressure
- Normal range: 250–310 PSI engaged, 15–50 PSI in neutral
- Monitor temperature at the oil cooler outlet
- Over 220°F indicates cooling problem
Post-Startup Torque Recheck
After initial operation, shut down and retorque:
- Rear cover bolts
- Flange coupling bolts
- Cooler line fittings
- Mounting foot hardware
- Solenoid and valve screws
Real-World Reassembly Oversights and Lessons
Example 1: Leaking Flange After Sea Trial
Mistake: RTV applied too thickly around output shaft
Effect: Excess sealant squeezed into bolt threads
Fix: Disassembled flange, cleaned threads, resealed with proper torque
Example 2: Oil Starvation at Startup
Cause: Filter installed dry and not primed
Result: 10 seconds of pressure lag burned clutch disc
Lesson: Always prefill filters when possible, and monitor pressure from key-on
Example 3: No Reverse After Rebuild
Findings: Valve spool installed backwards
Outcome: Valve removed, corrected orientation, reverse restored
Note: Label valve parts during disassembly
Final 30-Point Reassembly and Startup Checklist
- ✅ Gaskets cleaned and resealed
- ✅ Torque wrench used on all bolts
- ✅ RTV and sealant applied correctly
- ✅ Shaft seal installed flush
- ✅ Bearings lubed and clearances verified
- ✅ New O-rings installed throughout
- ✅ Filter replaced and filled
- ✅ Oil filled to “FULL”
- ✅ Breather clean and open
- ✅ Dipstick reads properly
- ✅ All ports plugged or connected
- ✅ Control valve installed and torqued
- ✅ Solenoids tested and wired
- ✅ Linkage or actuator reconnected
- ✅ Prop shaft alignment confirmed
- ✅ Transmission turned by hand
- ✅ No leftover parts or tools inside
- ✅ All bolts checked for torque
- ✅ No cross-threaded fasteners
- ✅ Cooler lines leak-free
- ✅ Oil pressure gauge installed
- ✅ Absorbent pads placed under gearbox
- ✅ Safety covers reinstalled
- ✅ Engine started at idle
- ✅ Forward/reverse tested
- ✅ No leaks observed
- ✅ Oil rechecked warm
- ✅ Pressure verified under load
- ✅ Gear shifts smooth and silent
- ✅ Logbook updated with parts, oil type, and service notes
Summary: Reassembly Tips and Best Practices for Twin Disc MG516 Marine Gear
Reassembling the Twin Disc MG516 is more than just bolting parts together—it’s a precision process that ensures every mechanical, hydraulic, and sealing system is aligned, torqued, sealed, and tested. By using proper torque values, selecting the right sealants, and completing a rigorous pre-startup checklist, you ensure:
- Proper clutch and gear function
- Long-term oil containment and cleanliness
- Minimal vibration and wear
- Accurate control response
- Safe and reliable operation under load
Parts Catalog for Twin Disc MG516 Marine Transmissions
Rebuilt Twin Disc MG516 Marine Transmissions
Plate Kit For Twin Disc MG516 Marine Transmission
Gasket Kits For Twin Disc MG516 Marine Transmission