When your Caterpillar engine starts showing signs of a failing cylinder head, the first instinct may be to send it to a machine shop for refurbishment. While this can sometimes be a cost-effective solution, in many cases, purchasing a new cylinder head is the better long-term investment. This article explores why buying a new cylinder head for your Caterpillar engine is often a superior choice compared to reconditioning your existing one.
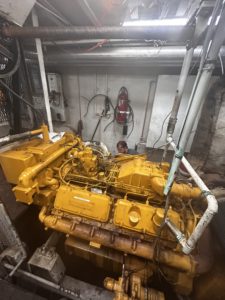
Key Takeaways
- Time Efficiency
- Cost Considerations
- Reliability & Longevity
- Machining Limitations
- Warranty & Guarantee
- Performance & Fuel Efficiency
- Availability & Compatibility
1. The Hidden Costs of Machining

Key Hidden Costs of Machining:
- Labor costs
- Additional repairs
- Downtime costs
- Multiple shop visits
- Material costs
- Shipping and handling
- Precision risks
- Long-term uncertainty
At first glance, sending a cylinder head to a machine shop appears to be the cheaper alternative. However, once you factor in all the associated costs, it may not be as cost-effective as it initially seems.
-
Labor Costs
Machining a cylinder head requires skilled labor, and shop rates can be steep. The process involves resurfacing, valve seat cutting, pressure testing, and potential welding. These tasks demand expertise and precision, and as complexity increases, so does the final bill. In some cases, the costs of machining alone can approach or even exceed the price of a brand-new cylinder head.
-
Additional Repairs
Often, once a machine shop begins work, they uncover additional problems such as hairline cracks, weak valve springs, worn-out valve guides, or corrosion. These issues can lead to extra machining and component replacements that were not initially anticipated. What starts as a simple resurfacing job can quickly turn into an expensive, time-consuming rebuild.
-
Downtime Costs
The longer an engine is out of commission, the more revenue and productivity are lost. Industrial, marine, and construction equipment downtime can be extremely costly. While machining can take anywhere from a few days to several weeks, a new cylinder head is readily available for installation, significantly reducing the time your equipment is non-operational.
-
Multiple Shop Visits
Even after machining, a rebuilt cylinder head may not perform as expected. If machining does not fully correct the issue or if further damage is discovered post-installation, the head may need to be sent back for additional work. This cycle of repairs can become frustrating and expensive, leading to further delays and higher costs.
-
Material Costs
Beyond labor, machining may require new valve seats, springs, and seals. These components add to the total cost, and if premium-grade materials are required, expenses can escalate quickly. Sometimes, the combined cost of labor and materials surpasses the price of a brand-new cylinder head.
-
Shipping and Handling
If you are not located near a reputable machine shop, shipping costs must be considered. Cylinder heads are heavy and can be costly to transport. Additionally, there’s always a risk of damage during transit, which could lead to even more expenses.
-
Precision Risks
Machining relies on precision, but even the best machine shops have limitations. If the cylinder head has been resurfaced multiple times in the past, there may not be enough material left to properly machine it again. Even small imperfections in the machining process can lead to compression loss, poor sealing, or uneven heat distribution, resulting in premature failure.
-
Long-Term Uncertainty
A machined cylinder head is still a used part with an unknown lifespan. While machining can restore functionality, it does not necessarily restore the head to a like-new condition. Over time, the wear and tear that originally caused the issue may resurface, forcing another costly repair or replacement sooner than expected.
A new cylinder head eliminates these uncertainties, providing a straightforward installation with predictable costs, a longer lifespan, and the peace of mind that comes with a brand-new component.
2. Time Is Money: Minimizing Downtime

Key Factors Contributing to Downtime
- Loss of business operations
- Logistics and shipping delays
- Risk of incomplete repairs
- Increased labor costs for idle workers
- Higher rental costs for temporary replacement equipment
- Customer dissatisfaction due to service delays
Re-machining a cylinder head can take several days to weeks, depending on the shop’s workload and part availability. This extended downtime can have severe financial consequences, impacting both direct and indirect costs.
-
Loss of Business Operations
When heavy equipment, marine vessels, or industrial machinery is out of service, it leads to project delays, disrupted schedules, and lost revenue. For industries reliant on continuous operation—such as construction, shipping, or power generation—downtime can cost thousands of dollars per day. If an engine failure happens in the middle of a high-demand period, the financial impact is even more severe. The longer the downtime, the greater the loss in revenue, productivity, and customer trust.
-
Logistics and Shipping Delays
Sending a cylinder head to a machine shop isn’t an instant fix. The process includes disassembling the engine, transporting the component, waiting for the machine shop to complete its work, and then reinstalling it. If the machine shop is backed up with other jobs or waiting on parts for your repair, the delay increases. Additionally, shipping mishaps or transit damage can lead to even longer delays, causing more financial strain.
-
Risk of Incomplete Repairs
If a machine shop discovers additional issues—such as cracks, excessive warping, or worn valve seats—it may require further machining or even replacement parts, which adds more time to the repair. Worse, if machining does not fully restore the cylinder head, performance issues may persist, requiring yet another round of repairs or a complete replacement later on. This cycle of rework leads to further downtime, unnecessary expenses, and potential frustration.
-
Increased Labor Costs for Idle Workers
In industries where equipment downtime affects crew productivity, the labor costs for idle workers can add up quickly. Employees waiting for an engine repair may be unable to perform their tasks, leading to financial losses in wages paid for unproductive hours. Additionally, if mechanics or technicians must dedicate extra time to troubleshooting a re-machined cylinder head that isn’t performing correctly, this adds to the operational inefficiency.
-
Higher Rental Costs for Temporary Replacement Equipment
Some businesses rent backup equipment when machinery is out of service, but these costs can be significant over time. Renting heavy machinery, boats, or industrial generators can quickly surpass the cost of simply purchasing a new cylinder head that would have minimized the downtime in the first place.
-
Customer Dissatisfaction Due to Service Delays
For businesses providing services that rely on Caterpillar engines—such as transport, marine operations, or industrial services—extended downtime can negatively impact customer satisfaction. Missed deadlines, unfulfilled contracts, and operational delays can lead to loss of business, damaged reputation, and dissatisfied clients who may take their business elsewhere.
A new cylinder head is ready for immediate installation, eliminating the risks of prolonged downtime and ensuring that your Caterpillar engine gets back to work quickly. Instead of dealing with uncertainties in machining, choosing a new cylinder head guarantees reliability, efficiency, and minimal disruption to your operations.
3. Reliability & Performance of a New Cylinder Head

Key Factors Affecting Reliability & Performance:
- Structural integrity
- Improved engineering
- Factory-tuned components
- Consistent compression and sealing
- Reduced risk of overheating and warping
- Elimination of past wear and fatigue
- Long-term cost savings and durability
Even after machining, an old cylinder head may not perform at the same level as a new one. The reconditioning process can restore some functionality, but it does not fully eliminate the risks associated with wear, fatigue, and previous damage. Opting for a new cylinder head ensures that your Caterpillar engine operates at peak efficiency, with consistent reliability and long-term durability.
-
Structural Integrity
Over time, metal fatigue weakens a cylinder head, making it more prone to future failures. Even after machining, stress points remain in the material, increasing the likelihood of cracks, leaks, or warping under extreme conditions. A new cylinder head eliminates this concern, providing a structurally sound component that meets OEM specifications without the risks associated with aging materials.
-
Improved Engineering
Many new cylinder heads are manufactured with design improvements that enhance performance and durability. Advances in metallurgy, cooling passages, and valve seat configurations improve heat dissipation, combustion efficiency, and overall reliability. These improvements help prevent common issues such as overheating, valve recession, and uneven wear, ensuring a longer-lasting component.
-
Factory-Tuned Components
New cylinder heads are manufactured to precise tolerances, ensuring optimal fitment, compression, and sealing. Machined cylinder heads, even when restored by skilled professionals, may still have small inconsistencies that affect performance. A new head eliminates the variability associated with re-machining, delivering a component that performs exactly as intended by the manufacturer.
-
Consistent Compression and Sealing
A key function of a cylinder head is to maintain proper compression. In a machined cylinder head, resurfacing can only do so much to correct minor imperfections. If the head has been machined multiple times in the past, it may no longer provide an ideal seal, leading to loss of compression, reduced power, and inefficient fuel combustion. A new cylinder head guarantees proper sealing, ensuring that compression remains at factory standards for optimal performance.
-
Reduced Risk of Overheating and Warping
Cylinder heads endure extreme temperatures and pressure fluctuations, making them susceptible to warping over time. Even after resurfacing, some old cylinder heads may have internal weaknesses that make them more likely to warp again. Warped heads lead to coolant leaks, improper valve seating, and inefficiencies in combustion. A brand-new head eliminates these risks, providing peace of mind that your engine will operate without overheating issues.
-
Elimination of Past Wear and Fatigue
Every time a cylinder head is used, microscopic stress fractures can form in the metal, weakening it over time. Re-machining can remove surface-level issues, but it cannot reverse the long-term effects of wear and tear. By choosing a new cylinder head, you eliminate the risk of inheriting previous damage, ensuring that your engine operates with a fresh, undamaged component.
-
Long-Term Cost Savings and Durability
While re-machining may seem like a cost-effective solution in the short term, it often leads to additional expenses down the line. A re-machined cylinder head may need further repairs sooner than expected, requiring another round of labor, downtime, and potential part replacements. A new cylinder head, on the other hand, provides long-term reliability, reducing the need for ongoing repairs and minimizing operational disruptions.
Instead of gambling on an older component, a new head offers peace of mind with guaranteed performance. It ensures that your Caterpillar engine runs efficiently, maintains proper combustion, and avoids unexpected failures caused by hidden weaknesses in a previously used part. Investing in a new cylinder head ultimately leads to improved fuel efficiency, enhanced engine longevity, and reduced maintenance costs, making it the smarter choice for long-term operation.
4. Warranty Protection and Long-Term Value
Key Benefits of a Warranty-Backed New Cylinder Head:
- Manufacturer’s warranty
- Better resale value
- Lower risk of rework
- Protection against defects and failures
- Increased engine reliability
- Cost savings on future repairs
Re-machined cylinder heads rarely come with strong warranties, leaving you fully responsible if something goes wrong. Even when some machine shops provide a limited guarantee, it usually only covers the specific work performed, not future failures that may arise due to the cylinder head’s pre-existing wear and tear. This lack of comprehensive protection can lead to unexpected repair costs down the line.
By purchasing a new cylinder head, you gain peace of mind with a manufacturer-backed warranty, which offers several advantages:
-
Manufacturer’s Warranty
Many reputable aftermarket suppliers offer warranties that cover defects in materials. These warranties provide coverage for premature failures, ensuring that you receive a replacement at no extra cost if something goes wrong. This added protection prevents unexpected expenses and reduces the financial risks associated with repairs.
-
Better Resale Value
A new cylinder head significantly increases the overall value of your equipment. Whether you plan to sell, trade, or upgrade your machinery in the future, having a new, warrantied cylinder head can make your equipment more attractive to buyers. Buyers prefer components with warranties because they provide assurance of quality and longevity, making your engine a more desirable asset in the resale market.
-
Lower Risk of Rework
A re-machined cylinder head may develop issues again, sometimes within a short period, forcing you to send it back for additional repairs. If these problems persist, you could end up replacing the cylinder head entirely, effectively doubling your expenses. A new cylinder head eliminates this risk by offering long-term reliability from the start, helping you avoid repeat labor costs and costly downtime.
-
Protection Against Defects and Failures
While machining can restore functionality, it does not necessarily restore a cylinder head to its original condition. Some internal defects may not be visible until the head is put back into operation, potentially causing failure. A new cylinder head, backed by a manufacturer’s warranty, guarantees that you are protected against these types of defects, offering a reliable and durable solution.
-
Increased Engine Reliability
A warrantied new cylinder head ensures that your engine will operate efficiently without unexpected breakdowns. The certainty that comes with a brand-new, defect-free component means fewer interruptions in your operations, better fuel efficiency, and an extended engine lifespan.
-
Cost Savings on Future Repairs
Investing in a new cylinder head now can save you significant amounts of money in the long run. With a strong warranty in place, you won’t have to pay out-of-pocket for defects, re-machining, or additional repairs if something goes wrong. This helps lower your total cost of ownership and enhances the value of your investment.
A warranty-backed new cylinder head removes these risks, ensuring that you’re covered for potential defects or failures. By choosing a new component, you protect your financial investment and gain a reliable, long-lasting solution for your Caterpillar engine.
6. Fuel Efficiency and Emissions Compliance
Key Issues Caused by a Worn-Out Cylinder Head:
- Increased fuel consumption
- Higher emissions
- Loss of power
- Poor air-fuel mixture control
- Overheating risks
- Inefficient combustion cycles
Cylinder heads play a crucial role in the internal combustion process, as they house the combustion chambers, valves, and passages that regulate the flow of air and fuel. A worn-out or damaged cylinder head can significantly impact fuel efficiency, emissions, and overall engine performance. Replacing an old, inefficient head with a new one ensures optimal combustion, reducing fuel costs and meeting environmental standards.
-
Increased Fuel Consumption:
A cylinder head that has uneven surfaces, damaged valves, or worn-out seals can cause improper compression, leading to incomplete combustion. When fuel isn’t burned efficiently, the engine requires more fuel to generate the same level of power, leading to excessive fuel consumption. Over time, this inefficiency adds up, increasing operational costs for equipment and vehicles that rely on Caterpillar engines.
-
Higher Emissions
Poor sealing and worn valve guides can allow oil to seep into the combustion chamber, leading to excessive smoke and increased hydrocarbon emissions. Additionally, inefficient combustion due to improper compression results in higher levels of unburned fuel in the exhaust, contributing to pollution. A new cylinder head eliminates these issues, ensuring proper sealing and optimal fuel combustion, reducing your environmental footprint.
-
Loss of Power
A compromised cylinder head reduces the engine’s ability to maintain adequate compression, directly affecting power output. This results in sluggish performance, poor acceleration, and increased engine strain. Operators may find themselves compensating for power loss by increasing throttle input, further contributing to fuel wastage. A new cylinder head restores compression to factory specifications, allowing the engine to deliver its full potential without unnecessary fuel consumption.
-
Poor Air-Fuel Mixture Control
The cylinder head plays a crucial role in ensuring a precise balance between air and fuel intake. A worn-out head can disrupt this balance, leading to an overly rich or lean mixture. This imbalance can cause engine knocking, misfires, and excessive carbon buildup. By installing a new cylinder head, you ensure proper air-fuel distribution, leading to a more stable and efficient combustion cycle.
-
Overheating Risks
Cracks in the cylinder head can cause coolant leaks, leading to overheating and potential engine failure. Overheating not only reduces engine efficiency but can also cause severe damage to pistons, valves, and gaskets. A new cylinder head eliminates these risks, ensuring a properly sealed cooling system that maintains ideal operating temperatures.
-
Inefficient Combustion Cycles
Worn-out cylinder heads may cause inconsistencies in combustion timing, leading to increased wear and tear on engine components. The loss of combustion efficiency directly affects the longevity of your engine, forcing it to work harder than necessary. A new cylinder head ensures that combustion occurs at optimal timing, reducing stress on other engine components and improving overall efficiency.
By investing in a new cylinder head, you restore proper combustion efficiency, improve fuel economy, and reduce emissions, ensuring that your Caterpillar engine meets performance and environmental standards.
7. When a Machine Shop Is a Viable Option
Situations Where Re-Machining a Cylinder Head Makes Sense
- Minimal damage with no cracks or deep warping
- Rare or out-of-production parts
- Budget constraints
- Limited engine use or short-term application
- Availability of high-quality machine shop services
While purchasing a new cylinder head is often the best long-term solution, there are cases where re-machining may still be a practical alternative. If the cylinder head has minor wear and can be effectively restored, a high-quality machine shop may be able to recondition it for continued use. However, several factors must be considered before choosing this option.
-
Minimal Damage
If a cylinder head has only minor surface wear, small imperfections, or slightly worn valve seats, a machine shop may be able to restore it effectively. Resurfacing, valve seat grinding, and pressure testing can bring a slightly worn head back to operational standards, extending its lifespan without the cost of full replacement. However, if deep cracks, severe warping, or major structural damage are present, re-machining may not be effective.
-
Rare or Out-of-Production Parts
Some Caterpillar engines, particularly older models, may have cylinder heads that are no longer in production. If finding a replacement is difficult or impossible, re-machining may be the only option to keep the engine running. In such cases, an experienced machine shop can perform custom repairs, such as welding cracks, installing valve seat inserts, or reinforcing weak areas to restore functionality.
-
Budget Constraints
For operators working within tight budget limitations, machining a cylinder head may be a more affordable short-term solution. If the cost of machining is significantly lower than purchasing a replacement, and the repair is expected to last a reasonable amount of time, this option may be worth considering. However, it’s important to factor in potential future repair costs, as a re-machined head may not last as long as a new one.
-
Limited Engine Use or Short-Term Application
If the engine in question is not used frequently or is only needed for a short-term application, re-machining may be an acceptable option. In cases where an engine is nearing the end of its service life and does not justify the expense of a brand-new cylinder head, machining can provide a temporary solution without over-investing in a long-term component.
-
Availability of High-Quality Machine Shop Services
Not all machine shops have the expertise or equipment necessary to properly recondition a cylinder head. If you choose to go this route, it’s essential to work with a reputable shop that specializes in heavy-duty diesel engine components. They should be capable of performing pressure testing, resurfacing, valve seat replacements, and thorough inspections to ensure the reconditioned head meets performance standards.
Important Considerations When Choosing a Machine Shop
- Ensure the shop has experience with Caterpillar cylinder heads
- Verify their ability to perform crack detection and pressure testing
- Ask for a warranty or guarantee on the re-machining work
- Compare the cost of machining versus purchasing a new head
- Consider the expected lifespan of the re-machined component
If a re-machined head is chosen, thorough testing should be conducted to confirm that it meets performance standards before reinstalling it. While reconditioning can be an economical alternative, the risks of shortened lifespan, future failures, and additional repair costs should always be weighed against the benefits of purchasing a new cylinder head.
In these cases, ensure that your machine shop has the expertise and equipment to perform high-quality reconditioning. If machining is not a viable solution, investing in a new cylinder head remains the best option for long-term reliability, performance, and cost savings.
Final Thoughts: The Smarter Investment
For many Caterpillar engine owners, a new cylinder head is a better investment than sending an old one to the machine shop. The advantages of reliability, efficiency, warranty coverage, and long-term cost savings outweigh the seemingly lower upfront costs of machining.
Key reasons to choose a new cylinder head over machining
- Avoid hidden costs associated with labor, additional repairs, and downtime.
- Eliminate unpredictable machine shop delays and get back to work faster.
- Ensure maximum reliability and performance with a brand-new component.
- Benefit from warranty protection, reducing financial risks.
- Improve fuel efficiency and reduce emissions with optimized combustion.
- Guarantee proper fitment and compatibility for a smooth installation.
If you’re looking for a durable and cost-effective solution for your Caterpillar engine, investing in a new aftermarket cylinder head is often the smartest choice. Whether you’re managing a fleet, running industrial equipment, or maintaining marine engines, the reliability and efficiency of a new cylinder head can keep your operations running smoothly for years to come.