Daily checks are essential for maintaining the reliability and efficiency of Detroit Diesel 149 Series engines (8V149, 12V149, and 16V149). These engines are often used in heavy-duty applications, making regular inspections crucial to avoid unexpected downtime and costly repairs. Daily checks focus on monitoring oil and coolant levels, conducting a visual inspection for leaks and wear, and listening for unusual sounds that may indicate potential issues. Performing these checks before operation helps identify problems early, ensuring safe and efficient engine performance.
Oil and Coolant Levels: Verifying Levels Before Operation and Topping Off as Necessary
Maintaining the correct oil and coolant levels is critical to ensuring the Detroit Diesel 149 Series engine operates smoothly and remains protected against damage from overheating or lack of lubrication. These levels should be checked daily, as both oil and coolant play vital roles in protecting engine components from excessive wear, overheating, and failure.
-
Oil Level Check
Oil Cooler for Detroit Diesel 12V149 Non – Turbo
Engine oil lubricates moving parts, reducing friction and preventing wear in critical components such as pistons, crankshafts, and camshafts. Running the engine with low oil levels can lead to severe damage, including overheating and premature wear.
- Step 1:
Ensure the engine is off and has been allowed to cool slightly before checking the oil level. Locate the oil dipstick, which is typically marked and accessible near the engine’s oil reservoir.
- Step 2:
Pull the dipstick out, wipe it clean with a cloth, then reinsert it fully before pulling it out again to check the oil level. The oil should be within the designated “Full” and “Add” marks on the dipstick.
- Step 3:
If the oil level is below the recommended range, add the appropriate oil type specified by Detroit Diesel. Avoid overfilling, as this can lead to increased pressure and potential oil leaks. Ensure the dipstick is properly secured after checking.
Lubrication & Related Components for 8V149 Non- Turbo Detroit Diesel Engines
Lubrication & Related Components for 8V149 Turbo Detroit Diesel Engines
Lubrication & Related Components for 12V149 Non-Turbo Detroit Diesel Engines
Lubrication & Related Components for 12V149 Turbo Detroit Diesel Engines
Lubrication & Related Components for 16V149 Non- Turbo Detroit Diesel Engines
Lubrication & Related Components for 16V149 Turbo Detroit Diesel Engines
- Step 1:
-
Coolant Level Check:
Fresh Water Pump for Detroit Diesel 16V149 Non Turbo
Coolant is essential for regulating the engine’s temperature, preventing overheating by circulating through the engine and dissipating heat. Low coolant levels can cause overheating, leading to issues such as warped cylinder heads, blown gaskets, and reduced engine efficiency.
- Step 1:
Allow the engine to cool before opening the radiator cap or coolant reservoir cap, as pressurized coolant can cause burns if released while hot.
- Step 2:
Check the coolant level in the radiator or expansion tank, depending on the engine setup. The level should be within the “Full” and “Low” marks on the reservoir or visible in the radiator neck.
- Step 3:
If the coolant is below the recommended level, add the appropriate coolant mixture specified for Detroit Diesel engines (typically a blend of antifreeze and distilled water). Ensure the radiator or reservoir cap is securely replaced to maintain system pressure.
- Step 1:
Regularly checking and maintaining proper oil and coolant levels protects the engine from damage caused by overheating or insufficient lubrication, especially under demanding operational conditions.
Visual Inspection: Checking for Leaks, Visible Wear, and Unusual Sounds
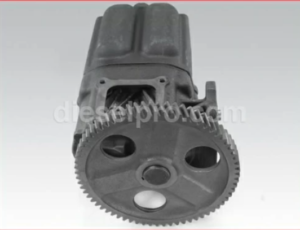
A thorough visual inspection of the engine can reveal early signs of potential issues, such as leaks, loose components, and worn parts. This inspection should also include listening for unusual sounds, which can indicate mechanical issues. Identifying these signs early allows for timely maintenance, preventing minor problems from escalating into major repairs.
-
Checking for Leaks
Oil, coolant, and fuel leaks are common issues that can lead to significant engine problems if left unaddressed. Each type of leak can indicate different issues within the engine.
- Oil Leaks
Look for oil stains or wet spots around the oil pan, valve covers, gaskets, and seals. Oil leaks can result from worn gaskets, loose bolts, or high engine pressure due to overfilled oil. If an oil leak is detected, monitor the leak location and repair it promptly to prevent oil loss and potential damage to engine components.
- Coolant Leaks
Check around the radiator, hoses, and coolant pump for any signs of coolant leakage, which may appear as wet spots or dried coolant deposits. Coolant leaks can reduce the cooling system’s efficiency, leading to overheating and damage to the cylinder head or gaskets. Replace worn hoses, seals, and clamps to address coolant leaks.
- Fuel Leaks
Look for signs of fuel leakage around the fuel lines, injectors, and fuel pump. Fuel leaks not only reduce efficiency but can also pose a safety hazard. Repair or replace leaking fuel lines and fittings immediately to prevent fuel loss and ensure safe operation.
- Oil Leaks
-
Inspecting for Visible Wear and Loose Components:
Daily visual inspections should include checking for visible wear, especially in parts exposed to movement, friction, or high temperatures. Additionally, look for any loose bolts, nuts, or fasteners.
- Belts and Hoses
Inspect belts for signs of fraying, cracks, or wear, as damaged belts can lead to accessory failure (such as the water pump or alternator). Check hoses for soft spots, cracks, or swelling, which can indicate a risk of bursting. Replace worn belts and hoses to ensure the engine’s auxiliary systems operate reliably.
- Mounting Bolts and Fasteners
Inspect critical bolts and fasteners on components such as the cylinder head, exhaust manifold, and accessory mounts. Loose bolts can cause vibrations, misalignment, and damage to parts over time. Tighten any loose fasteners according to manufacturer specifications to prevent component movement or wear.
- Air Filter
Check the air filter housing for proper placement and ensure that the filter is clean. A clogged air filter restricts airflow, reducing combustion efficiency and increasing fuel consumption. Clean or replace the air filter regularly to maintain optimal airflow.
Oil Filter & Related Components for Detroit Diesel Engines
- Belts and Hoses
-
Listening for Unusual Sounds
In addition to visual inspection, listen for any unusual noises while the engine is running. Different sounds can indicate specific mechanical issues that may require attention.
- Knocking or Tapping Sounds
Knocking sounds may be caused by improper valve clearance, worn bearings, or piston issues. If the engine is knocking, inspect the valve clearance and perform a tune-up if needed. If the knocking persists, further inspection of the crankshaft and bearings may be required.
- Squealing or Whining Sounds
A high-pitched squeal or whine is often a sign of a worn belt, misaligned pulley, or failing accessory component. Inspect belts and pulleys for wear or misalignment and replace them as needed to prevent accessory failure.
- Hissing or Leaking Sounds
A hissing noise may indicate a coolant or air leak. Check hoses, seals, and gaskets for any leaks. If a leak is detected, repair or replace the affected parts to maintain pressure and prevent overheating or pressure loss.
- Knocking or Tapping Sounds
Benefits of Daily Checks
Performing these daily checks on the Detroit Diesel 149 Series engines ensures the following benefits:
-
Reduced Risk of Breakdown
Catching potential issues like low oil or coolant, worn belts, or loose bolts early reduces the likelihood of unexpected breakdowns during operation.
-
Enhanced Safety:
Identifying fuel or coolant leaks before starting the engine improves safety by preventing potential fires or coolant-related overheating issues.
-
Extended Engine Life:
Regular checks allow for preventive maintenance, reducing wear and stress on engine components and extending the engine’s service life.
-
Optimal Performance and Efficiency:
Maintaining proper fluid levels, securing components, and ensuring proper airflow supports efficient combustion, which enhances engine power and fuel efficiency.
By incorporating these daily checks into routine maintenance, operators can keep their Detroit Diesel 149 Series engines in optimal working condition, preventing costly repairs and ensuring reliable performance in demanding applications.
Parts Catalog for 8V149 Detroit Diesel Marine Engine
Parts Catalog for 12V149 Detroit Diesel Marine Engine
Parts Catalog for 16V149 Detroit Diesel Marine Engine