Cylinder Block For Detroit Diesel 149 Series Engines (8V149, 12V149, 16V149)
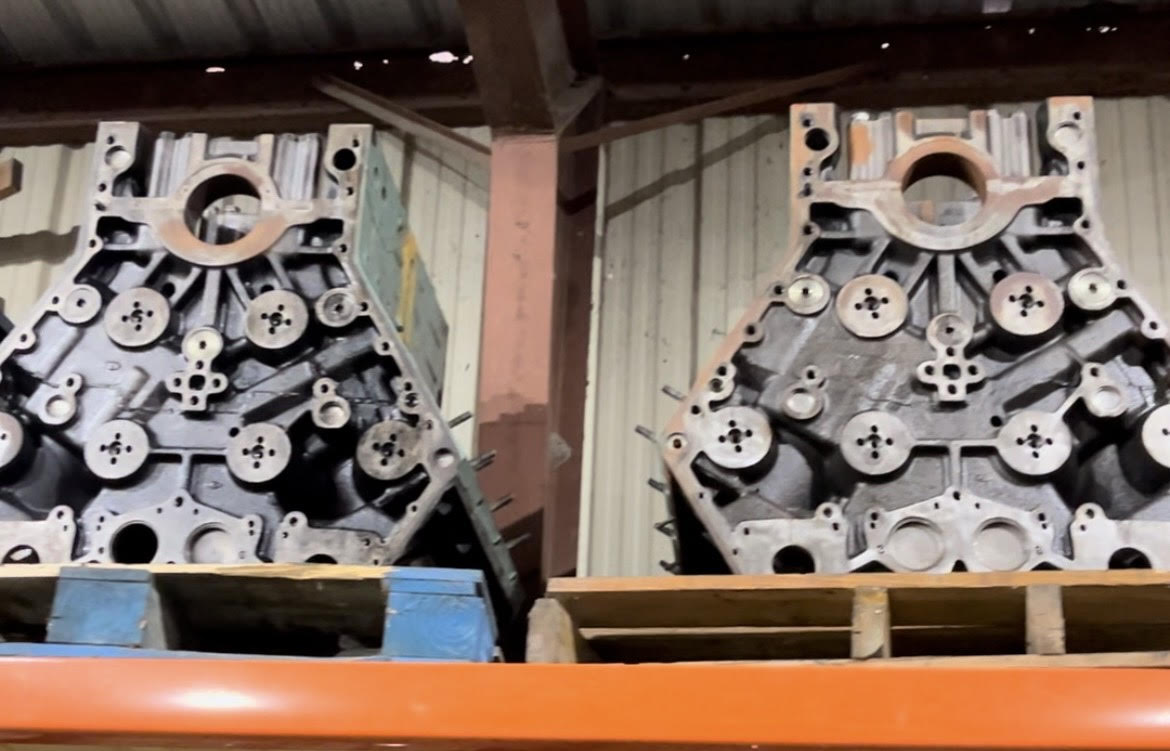
The cylinder block is a foundational component in the Detroit Diesel 149 Series engines (8V149, 12V149, and 16V149), providing the main structural framework for the engine and supporting various critical systems. Its durability and strength are essential for housing key components that generate and control power. Routine maintenance of the cylinder block ensures that the engine operates smoothly and remains reliable for demanding applications. Essential aspects of the cylinder block include its structure and role, maintenance tips, and effective cleaning and testing procedures.
Structure and Role: The Engine’s Main Frame
The cylinder block is constructed from heavy-duty cast iron or aluminum alloy, materials chosen for their ability to withstand high levels of heat and pressure. The design of the cylinder block is tailored to hold and align essential engine components, including the cylinders, crankshaft, and bearings, which are all crucial for the engine’s performance.
- Housing and Support for Key Components:
The cylinder block acts as the central housing for the engine’s pistons, which move within the cylinders to create the power needed for operation. It also holds the crankshaft in place, with the crankshaft converting the up-and-down motion of the pistons into rotational motion that powers the engine. Other vital components, such as camshafts and connecting rods, are also secured by the cylinder block, which keeps them in precise alignment for efficient operation.
- Integrated Cooling and Lubrication Passages:
Within the cylinder block, there are numerous passages and channels specifically designed for the flow of coolant and oil. These cooling passages allow coolant to circulate around the cylinders, dissipating heat generated during combustion to prevent overheating. Lubrication channels, on the other hand, deliver oil to the bearings, crankshaft, and other moving parts, reducing friction and wear. Together, these systems ensure that the engine operates at optimal temperature and maintains efficient lubrication.
- Engine’s Structural Integrity:
The cylinder block is a large, solid piece that supports the weight of the entire engine assembly. Its design distributes stress evenly across its structure, helping it withstand the intense forces generated during each combustion cycle. This structural strength is essential for the heavy-duty applications in which the Detroit Diesel 149 Series engines are often used, such as marine and industrial settings, where reliability is paramount.
Maintenance Tips: Ensuring Structural Integrity and Performance
Regular maintenance of the cylinder block helps ensure its longevity and prevents small issues from developing into major problems. Technicians should inspect for any signs of wear or damage during routine maintenance, as this can help identify potential risks before they affect engine performance.
- Inspecting for Cracks and Fractures:
Over time, the high temperatures and mechanical stresses within the cylinder block can lead to the development of cracks, particularly around high-stress areas like bolt holes, coolant passages, and bearing seats. Using visual inspection methods or specialized tools such as dye penetrant testing can help identify even minor cracks. Addressing these issues early can prevent oil or coolant leaks that could impair the engine’s functionality.
- Checking Bearing Caps for Wear:
The bearing caps secure the crankshaft bearings within the cylinder block, ensuring the crankshaft remains stable during operation. Regular inspection of these caps is crucial, as worn caps can lead to crankshaft misalignment or excessive bearing wear. Checking for signs of fretting (a condition where metal surfaces wear away due to small oscillating movements) or loosening can help maintain proper alignment of the crankshaft, preventing serious issues.
- Monitoring Bolt Torque and Thread Condition:
The bolts that hold the cylinder head and main bearing caps in place within the cylinder block are subject to significant stress. Over time, these bolts can loosen, or the threads within the block can wear out, compromising the security of the connections. Regularly checking and re-torquing these bolts to manufacturer specifications can prevent issues like head gasket leaks and crankshaft misalignment. Worn threads should be repaired promptly to avoid further damage.
Cleaning and Testing: Maintaining Optimal Condition
Regular cleaning and testing of the cylinder block are essential for keeping it in pristine condition, ensuring that all internal passages remain clear and that there are no hidden issues that could compromise engine performance. These cleaning and testing procedures help detect leaks, prevent overheating, and ensure effective lubrication.
- Solvent Baths for Thorough Cleaning:
Solvent baths are highly effective for removing grease, oil, and other contaminants that accumulate on the cylinder block over time. By submerging the block in a solvent solution, technicians can dissolve stubborn buildup from both the outer and inner surfaces. After soaking, brushing or scrubbing any remaining deposits helps achieve a clean block that is ready for inspection. This step ensures that contaminants don’t obstruct cooling or lubrication passages, which could affect engine efficiency.
- Steam Cleaning to Clear Residual Buildup:
Steam cleaning uses high-temperature steam to remove residue and dirt from the cylinder block’s surfaces and internal passages. The steam’s heat loosens dirt and oil without using harsh chemicals, making it an environmentally friendly method. Steam cleaning is especially useful for clearing cooling and lubrication passages, ensuring these channels remain unobstructed and allowing coolant and oil to flow freely. After steam cleaning, the cylinder block should be carefully dried to prevent any moisture from causing corrosion.
- Pressure Testing to Detect Leaks and Weaknesses:
Pressure testing is a vital method for checking the cylinder block’s integrity. By applying pressure to the cooling and lubrication passages, technicians can detect leaks that may allow coolant or oil to escape. Any leak, no matter how minor, could compromise the engine’s performance by reducing the coolant or oil levels. Pressure testing verifies that the cylinder block is capable of withstanding operating conditions and helps ensure that all internal channels are sealed and secure.
- Magnetic Particle Inspection (MPI) for Crack Detection:
For cast iron or other ferrous materials, Magnetic Particle Inspection (MPI) is a non-destructive testing method used to detect surface and near-surface cracks. This method applies a magnetic field to the metal, causing iron particles to gather around any cracks or faults, making them visible to technicians. MPI is particularly useful for identifying structural weaknesses that might not be visible to the naked eye, especially in high-stress areas around bolt holes or near the cylinder bores.
- Rust Prevention and Protective Coatings:
Once cleaned, the cylinder block should be dried thoroughly to prevent moisture from causing rust. For engines that will be stored or left unused for a period, applying a rust-preventive oil to the block’s external surfaces helps protect against corrosion. This preventive measure is especially important for engines in marine environments, where saltwater exposure can accelerate corrosion.
By following these maintenance tips and cleaning procedures, technicians can ensure the cylinder block of the Detroit Diesel 149 Series engines remains in optimal condition. Routine inspections and preventive care support the cylinder block’s structural integrity, maintain efficient cooling and lubrication, and extend the engine’s overall lifespan, making it reliable for high-performance applications
Cylinder Head For Detroit Diesel 149 Series Engines (8V149, 12V149, 16V149)

The cylinder head is a crucial component of the Detroit Diesel 149 Series engines, including models 8V149, 12V149, and 16V149. It plays a key role in engine operation by housing the exhaust valves, fuel injectors, and cooling passages, all of which work together to facilitate efficient combustion, exhaust expulsion, and temperature regulation. Maintaining the cylinder head in top condition is essential for the engine’s overall performance and longevity. This section covers the cylinder head’s key functions and common issues along with preventive maintenance tips.
Cylinder Head & Related Components for Detroit Diesel 8V149 Non – Turbo Engine
Cylinder Head & Related Components for Detroit Diesel 8V149 Turbo Engine
Cylinder Head & Related Components for Detroit Diesel 12V149 Non – Turbo Engine
Cylinder Head & Related Components for Detroit Diesel 12V149 Turbo Engine
Cylinder Head & Related Components for Detroit Diesel 16V149 Non – Turbo Engine
Cylinder Head & Related Components for Detroit Diesel 16V149 Turbo Engine
Key Functions: Housing Exhaust Valves, Fuel Injectors, and Cooling Systems
The cylinder head serves as a complex assembly for several essential systems in the engine, each with specific functions that contribute to the efficient operation of the combustion process. Proper interaction between these systems is crucial for optimal performance, as the cylinder head helps manage both the fuel supply and exhaust output while maintaining consistent temperatures within the engine.
- Exhaust Valves:
Detroit Diesel 149 Series Valve Kits (8V149, 12V149, 16V149)
The cylinder head houses the exhaust valves, which are responsible for releasing exhaust gases generated during combustion. These valves open at precisely timed intervals, allowing burned gases to exit the combustion chamber and flow into the exhaust manifold. The exhaust valves must withstand extreme heat and pressure, and their proper operation is essential for maintaining engine efficiency. Misalignment or improper sealing of these valves can lead to reduced engine performance, higher emissions, and overheating.
Valve Kit & Related Components for Detroit Diesel 8V149 Non – Turbo Engine
Valve Kit & Related Components for Detroit Diesel 8V149 Turbo Engine
Valve Kit & Related Components for Detroit Diesel 12V149 Non – Turbo Engine
Valve Kit & Related Components for Detroit Diesel 12V149 Turbo Engine
Valve Kit & Related Components for Detroit Diesel 16V149 Non – Turbo Engine
Valve Kit & Related Components for Detroit Diesel 16V149 Turbo Engine
- Fuel Injectors:
Detroit Diesel Injector (120) For 149 Series Engines
The fuel injectors, also located within the cylinder head, are responsible for delivering fuel to the combustion chamber at a specific pressure and timing. Injectors spray a fine mist of diesel fuel into the chamber, where it mixes with compressed air to ignite and produce the power needed to drive the engine. The injectors are designed to deliver precise amounts of fuel for each combustion cycle, making their position and function within the cylinder head critical to fuel efficiency and power output.
Fuel Injectors & Related Components for Detroit Diesel 8V149 Non – Turbo Engine
Fuel Injectors & Related Components for Detroit Diesel 8V149 Turbo Engine
Fuel Injectors & Related Components for Detroit Diesel 12V149 Non – Turbo Engine
Fuel Injectors & Related Components for Detroit Diesel 12V149 Turbo Engine
Fuel Injectors & Related Components for Detroit Diesel 16V149 Non – Turbo Engine
Fuel Injectors & Related Components for Detroit Diesel 16V149 Turbo Engine
- Cooling Passages:
To prevent overheating, the cylinder head incorporates a network of coolant passages that allow coolant to flow through, absorbing heat generated during combustion. This cooling system works in tandem with the engine block’s cooling channels, regulating temperatures and protecting sensitive components like exhaust valves and injectors from excessive heat. If cooling passages become blocked or degraded, the engine’s temperature control is compromised, which could lead to overheating and potential damage to the cylinder head and other engine parts.
The integration of these systems within the cylinder head supports the combustion cycle’s efficiency and helps maintain balance in the engine. Together, the exhaust valves, fuel injectors, and cooling system ensure the engine’s consistent power output, efficient fuel consumption, and controlled temperatures.
Common Issues: Addressing Wear, Valve Clearance, and Cylinder Head Replacement
The cylinder head is exposed to high heat and pressure, which makes it susceptible to various types of wear and potential damage over time. Regular inspection and maintenance can help address common issues that affect cylinder head performance, such as valve wear, improper clearances, and potential cracking. Here are some common issues and tips for preventive care:
- Wear on Exhaust Valves and Seats:
Exhaust valves and their seats within the cylinder head can wear down over time due to continuous exposure to high temperatures and pressure. This wear can lead to poor sealing, which allows exhaust gases to leak back into the combustion chamber, reducing engine efficiency and power output. Regular inspection of valve seats and replacing worn exhaust valves as needed helps maintain proper sealing. Lapping the valves (polishing and grinding them to create a smooth, precise seal) can restore proper sealing if wear is minimal.
- Maintaining Proper Valve Clearance:
The clearance between the valves and rocker arms (the mechanism that opens and closes the valves) must be adjusted accurately. If valve clearance is too tight, it can prevent the valve from closing completely, causing gas leaks and overheating. If the clearance is too wide, it can lead to inefficient fuel combustion and a loss of engine power. Regularly adjusting the valve clearances according to manufacturer specifications ensures that the valves open and close at the right intervals, contributing to optimal combustion and preventing premature valve wear.
- Injector Wear and Carbon Buildup:
Fuel injectors can develop wear or become clogged with carbon deposits, which can impact fuel delivery and spray patterns. Uneven fuel distribution results in incomplete combustion, reducing fuel efficiency and increasing emissions. Cleaning or replacing fuel injectors periodically and using high-quality diesel fuel with detergent additives can help minimize carbon buildup and injector wear. Regular injector inspection is also recommended to ensure consistent fuel atomization, contributing to smoother and more efficient engine performance.
- Cooling Passage Blockages:
Blockages in the cylinder head’s cooling passages can lead to localized overheating, which may damage the cylinder head and other engine components. Scale or mineral deposits from coolant can accumulate in the cooling channels, restricting flow and reducing heat dissipation. Regular flushing of the cooling system prevents buildup, and inspecting the cylinder head for any coolant leaks or corrosion helps ensure effective cooling. Replacing coolant with fresh, clean coolant at recommended intervals also aids in maintaining the cooling system’s effectiveness.
- Cylinder Head Cracks and Warping:
Over time, the cylinder head may develop cracks or warping due to extreme heat and pressure, especially if the engine has experienced episodes of overheating. Cracks typically form around high-stress areas like valve seats or coolant passages. Warping can lead to poor sealing between the cylinder head and engine block, causing coolant or oil leaks. Pressure testing or magnaflux testing (a non-destructive method using magnetic particles) can detect cracks. If cracks or warping are severe, the cylinder head may need to be replaced to maintain proper function.
- Head Gasket Failure:
The head gasket, which seals the junction between the cylinder head and engine block, can fail due to excessive pressure, heat, or improper installation. A failed head gasket often results in coolant leaks, oil contamination, or reduced compression. Signs of head gasket failure include white exhaust smoke (indicating coolant leakage into the combustion chamber), reduced engine power, and overheating. Replacing the head gasket promptly and ensuring proper torque during installation can prevent additional damage to the cylinder head and block.
By performing regular maintenance on the cylinder head—monitoring valve clearances, inspecting injectors for wear, cleaning cooling passages, and checking for cracks or gasket issues—technicians can prevent common problems and maintain the engine’s reliability. These practices help ensure the 149 Series engine continues to operate at peak efficiency, providing consistent power and performance in demanding applications.
Fuel System For Detroit Diesel 149 Series Engines (8V149, 12V149, 16V149)
The fuel system in Detroit Diesel 149 Series engines, including the 8V149, 12V149, and 16V149 models, is a critical component that ensures efficient fuel delivery for optimal combustion and power output. This system consists of multiple interconnected components designed to supply fuel under high pressure to each cylinder, where it is atomized and ignited to drive the engine. Proper maintenance of the fuel system is essential for maintaining the engine’s performance, fuel efficiency, and longevity.
Components and Operation: Fuel Pump, Filter, Injectors, and Manifold
The fuel system includes several key components, each playing a specific role in delivering fuel to the combustion chambers. Understanding the function of each part helps ensure proper maintenance and troubleshooting when issues arise.
- Fuel Pump:
The fuel pump is responsible for drawing fuel from the tank and delivering it under pressure to the fuel injectors. In the Detroit Diesel 149 Series, the pump must consistently provide high-pressure fuel to meet the demands of the engine, particularly under heavy load conditions. If the fuel pump does not deliver adequate pressure, the engine may experience power loss, poor fuel economy, or even failure to start. Regular inspection of the fuel pump for wear and replacing it as necessary are key to ensuring consistent fuel delivery.
- Fuel Filter:
The fuel filter protects the injectors and other sensitive parts of the fuel system by removing contaminants such as dirt, rust, and debris from the fuel. Clean fuel is essential for preventing injector clogs and ensuring proper combustion. In the 149 Series engines, the fuel filter is located between the fuel pump and the injectors, where it traps impurities before they can enter the fuel injectors. Regularly replacing the fuel filter is crucial, as a clogged filter can restrict fuel flow, causing the engine to run lean, lose power, or misfire.
- Fuel Injectors:
The fuel injectors are responsible for atomizing fuel and delivering it in a fine spray into the combustion chamber at precisely timed intervals. This atomization ensures efficient mixing with air, allowing for complete combustion. Injectors in the 149 Series must withstand high pressures and deliver fuel at consistent, precise timings for optimal performance. Clogged or worn injectors can cause uneven fuel distribution, leading to rough idling, poor fuel efficiency, and reduced power output. Routine inspection, cleaning, and replacement of injectors as needed are essential for maintaining engine performance.
- Fuel Manifold:
The fuel manifold, also known as the fuel rail, distributes fuel evenly to the injectors. It maintains a consistent fuel pressure to ensure that each injector receives the correct amount of fuel at the required pressure. A properly functioning fuel manifold helps ensure smooth and even combustion across all cylinders. Issues in the manifold, such as pressure imbalances or blockages, can lead to poor engine performance and uneven power distribution. Checking for leaks or blockages in the manifold is a key maintenance step to ensure optimal fuel delivery.
Together, these components work to deliver fuel in a precise and controlled manner, supporting efficient combustion and consistent power output. Properly maintaining each component helps prevent fuel delivery issues that can impact engine performance and longevity.
Fuel Quality: Importance of Clean, High-Quality Fuel
Using clean, high-quality fuel is essential for the longevity and performance of the Detroit Diesel 149 Series engines. Low-quality or contaminated fuel can introduce impurities into the fuel system, leading to clogged injectors, reduced efficiency, and even engine damage. High-quality fuel burns more efficiently and reduces the buildup of carbon deposits, which can impair engine function over time.
- Preventing Injector Clogs:
Impurities in the fuel, such as dirt, water, or other contaminants, can clog the fuel injectors. When injectors are clogged, fuel does not atomize properly, leading to incomplete combustion and decreased power output. High-quality diesel fuel typically contains fewer impurities, reducing the risk of clogging. Using a reputable fuel supplier and, if necessary, installing an additional fuel pre-filter can help prevent contaminants from reaching the injectors.
- Enhancing Combustion Efficiency:
Clean fuel allows for complete and efficient combustion, resulting in better fuel economy, more power, and reduced emissions. Fuel additives that clean the injectors and prevent carbon buildup can also improve efficiency and prolong the life of the fuel system components. However, it’s essential to use only additives approved by Detroit Diesel to avoid unintended damage to the fuel system.
- Minimizing Wear on Fuel System Components:
Contaminated or low-quality fuel can cause premature wear on the fuel pump, injectors, and other components. Water in the fuel, for example, can lead to corrosion within the fuel system, damaging components and reducing their lifespan. High-quality diesel fuel with lower water content and fewer contaminants extends the life of fuel system parts and helps maintain consistent performance.
Fuel Line Inspections: Checking for Leaks and Wear
Fuel lines are essential for safely transporting fuel from the tank to the fuel pump, filter, injectors, and manifold. Regular inspections of these lines help prevent leaks, ruptures, and pressure loss, all of which can impact engine performance and fuel efficiency. Detecting issues early can prevent more serious problems, such as fuel starvation or fire hazards.
- Inspecting for Leaks:
Fuel leaks not only waste fuel but can also pose fire hazards in high-temperature areas. Inspect fuel lines and connections for any signs of dampness, fuel odor, or visible cracks that could indicate a leak. Tightening fittings and replacing damaged lines help ensure the fuel system remains sealed and operates at optimal pressure. Immediate repair of leaks is essential to prevent dangerous conditions and fuel loss.
- Checking for Wear and Deterioration:
Over time, fuel lines may become brittle, cracked, or corroded, particularly if exposed to heat, vibration, or moisture. Regularly inspecting fuel lines for signs of wear or deterioration helps prevent unexpected failures. Replacing aging fuel lines is a proactive measure that can prevent interruptions in fuel supply and potential fuel spills. For high-vibration areas, use vibration-resistant hoses to reduce wear.
- Ensuring Secure Connections:
Loose or improperly connected fuel lines can result in fuel leakage, pressure drops, and fuel starvation, which affects combustion. Ensure all fuel line connections are secure and free from damage. Periodically check clamps and fasteners, especially in areas with high vibration, to prevent loosening over time. Using fuel line clamps designed for high-pressure diesel systems ensures that connections remain tight and reliable.
- Maintaining Pressure Consistency:
Consistent fuel pressure is necessary for the injectors to operate correctly, as fluctuations in pressure can disrupt fuel atomization and lead to inefficient combustion. Inspecting fuel lines and the fuel pump regularly helps maintain the correct pressure throughout the system, ensuring each injector receives the required amount of fuel. For areas with fluctuating pressure, consider adding a pressure regulator to stabilize fuel flow.
By properly maintaining the fuel system—ensuring clean, high-quality fuel, regular fuel line inspections, and maintaining the fuel pump, filter, injectors, and manifold—technicians can keep Detroit Diesel 149 Series engines running efficiently. These steps support consistent fuel delivery, improve engine performance, and help extend the life of the fuel system and engine overall.
Cooling System For Detroit Diesel 149 Series Engines (8V149, 12V149, 16V149)

The cooling system in the Detroit Diesel 149 Series engines, including models 8V149, 12V149, and 16V149, is essential for maintaining the engine’s operating temperature and preventing overheating. As these engines are often used in heavy-duty applications, such as marine, industrial, and trucking environments, effective cooling is vital to ensure consistent performance and protect sensitive components from thermal stress. The cooling system consists of several key components, including the engine water jacket and centrifugal pump, each of which plays a specific role in circulating coolant and dissipating heat.
Purpose and Components: Engine Water Jacket, Centrifugal Pump, and Consistent Water Flow
The cooling system in Detroit Diesel 149 Series engines is designed to circulate coolant throughout the engine, absorbing heat generated during combustion and transferring it away from critical components. The water jacket, centrifugal pump, and consistent water flow are integral to this process, ensuring that the engine remains within safe temperature limits, especially during high-load conditions.
- Engine Water Jacket:
The water jacket is a series of passages cast into the cylinder block and cylinder head, surrounding each cylinder to absorb heat from the combustion process. Coolant flows through the water jacket, directly removing heat from high-temperature areas such as the cylinder walls and combustion chambers. This heat transfer process prevents components from overheating and reduces the risk of thermal damage, such as cylinder head warping or cracking. The water jacket’s design also helps maintain uniform temperature distribution, which reduces mechanical stress and supports efficient combustion.
- Centrifugal Pump:
The centrifugal pump, often driven by the engine itself, circulates coolant through the water jacket and other parts of the cooling system. As the pump spins, it creates centrifugal force, pushing coolant through the system at a controlled rate. The pump’s ability to maintain consistent coolant flow is essential for preventing localized overheating, as it ensures that each area of the engine receives a continuous supply of coolant. Proper operation of the centrifugal pump is critical for high-load applications, where maintaining cooling efficiency is necessary for preventing performance degradation or component damage.
- Thermostat and Temperature Control:
The thermostat is another key component of the cooling system, regulating the coolant flow based on engine temperature. When the engine is cold, the thermostat remains closed, allowing the coolant to bypass the radiator and circulate within the engine, helping it reach optimal operating temperature quickly. As the engine warms up, the thermostat opens to allow coolant to pass through the radiator, where heat is dissipated. This temperature control mechanism is essential for efficient engine warm-up and helps prevent the engine from running too cold or overheating.
- Radiator:
The radiator, though not directly part of the engine block, plays a crucial role in the cooling system by dissipating heat from the coolant. The coolant flows from the water jacket to the radiator, where it passes through thin tubes with a large surface area. Air flowing over these tubes removes heat from the coolant, lowering its temperature before it is recirculated back to the engine. Regular inspection and cleaning of the radiator are essential for maintaining its efficiency, as clogged or damaged fins can reduce airflow and hinder cooling performance.
Consistent water flow is vital to the cooling system’s effectiveness, as it ensures the coolant reaches all areas of the engine that require heat dissipation. If the flow is interrupted or becomes inconsistent, certain engine parts can overheat, leading to potential failures. Therefore, maintaining each component of the cooling system, from the water jacket to the centrifugal pump, is essential to keep the engine running smoothly and prevent overheating.
Fresh Water Pump & Related Components for Detroit Diesel 8V149 Non – Turbo Engine
Fresh Water Pump & Related Components for Detroit Diesel 8V149 Turbo Engine
Fresh Water Pump & Related Components for Detroit Diesel 12V149 Non – Turbo Engine
Fresh Water Pump & Related Components for Detroit Diesel 12V149 Turbo Engine
Fresh Water Pump & Related Components for Detroit Diesel 16V149 Non – Turbo Engine
Fresh Water Pump & Related Components for Detroit Diesel 16V149 Turbo Engine
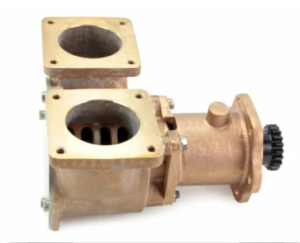
Marine Raw Water Pump & Related Components for Detroit Diesel 8V149 Non – Turbo Engine
Marine Raw Water Pump & Related Components for Detroit Diesel 8V149 Turbo Engine
Marine Raw Water Pump & Related Components for Detroit Diesel 12V149 Non – Turbo Engine
Marine Raw Water Pump & Related Components for Detroit Diesel 12V149 Turbo Engine
Marine Raw Water Pump & Related Components for Detroit Diesel 16V149 Non – Turbo Engine
Marine Raw Water Pump & Related Components for Detroit Diesel 16V149 Turbo Engine
Scale and Corrosion: Preventing Buildup and Addressing Blocked Passages for Efficient Cooling
Scale and corrosion are common issues in cooling systems, especially in heavy-duty engines like those in the Detroit Diesel 149 Series. These problems arise due to impurities in the coolant, as well as reactions between the coolant and the metal surfaces inside the engine. Preventing and managing scale and corrosion is essential to maintaining efficient coolant flow and ensuring the engine’s long-term reliability.
- Scale Buildup:
Scale forms when dissolved minerals in the coolant, such as calcium and magnesium, precipitate and adhere to the surfaces of the water jacket, radiator, and other cooling components. This buildup reduces the effectiveness of heat transfer, as the scale acts as an insulating layer, trapping heat within the engine. Over time, scale can significantly reduce cooling efficiency and may even block narrow coolant passages, leading to localized overheating and potential engine damage. To prevent scale buildup, it’s important to use high-quality, low-mineral coolant and to change the coolant at the intervals recommended by Detroit Diesel.
- Corrosion:
Corrosion occurs when metal surfaces in the cooling system react with oxygen, coolant additives, or contaminants, leading to rust and other forms of degradation. Corrosion can weaken the structure of components like the water jacket and radiator, creating leaks that reduce coolant levels and impair the cooling system’s performance. Regular coolant replacement, along with the use of corrosion inhibitors, helps protect metal surfaces from rust. Using a coolant mixture with the correct balance of water and antifreeze also reduces the likelihood of corrosion.
- Preventive Maintenance for Scale and Corrosion: Flushing the cooling system periodically is one of the most effective ways to remove accumulated scale and prevent corrosion. A coolant flush involves draining the old coolant, introducing a cleaning solution to dissolve any buildup, and thoroughly rinsing the system before refilling it with fresh coolant. This process removes scale and rust, ensuring that coolant can flow freely through the system. For engines exposed to hard water or other contaminants, more frequent flushing may be necessary to prevent buildup.
- Inspection of Cooling Passages:
During routine maintenance, technicians should inspect cooling passages within the water jacket for any signs of blockage or buildup. Blocked passages can cause overheating by preventing coolant from reaching certain areas of the engine, leading to uneven cooling and potential damage. Using inspection cameras or specialized tools, technicians can assess the condition of internal passages and address any obstructions before they become serious.
- Using Quality Coolant and Additives:
High-quality coolant with rust inhibitors and other protective additives can prevent scale and corrosion. Diesel engines typically require a specific type of coolant, formulated to handle the higher temperatures and pressures characteristic of diesel operation. Choosing a coolant that meets Detroit Diesel’s specifications helps minimize scale and corrosion. In environments where scale buildup is a concern, water softeners or demineralized water can be used in the coolant mix to reduce mineral content.
- Monitoring for Leaks and Testing Coolant Condition:
Regularly checking for coolant leaks and testing coolant condition are important preventive steps. Leaks can occur due to corrosion or deterioration of seals, leading to reduced coolant levels and impaired cooling. Testing the coolant’s pH and concentration helps determine whether it needs replacement, as coolant that is too acidic or lacks protective additives is more likely to cause corrosion and scale buildup.
By maintaining the cooling system in the Detroit Diesel 149 Series engines and addressing scale and corrosion proactively, technicians can ensure that the engine remains within optimal temperature limits. Proper coolant quality, regular flushing, and thorough inspections prevent blockages and inefficiencies, protecting the engine from overheating and extending its operational life.
Exhaust System For Detroit Diesel 149 Series (8V149, 12V149, 16V149)
The exhaust system in Detroit Diesel 149 Series engines, including the 8V149, 12V149, and 16V149 models, is essential for expelling exhaust gases generated during combustion and maintaining efficient engine performance. A well-maintained exhaust system ensures that gases exit the engine smoothly, preventing back pressure and minimizing the risk of overheating. Key components of this system include exhaust valves, manifolds, and other parts that need regular maintenance and inspection to keep the engine functioning at optimal levels.
Components and Maintenance: Role of Exhaust Valves and Manifolds, Cleaning Buildup, and Ensuring Free Airflow
The exhaust system in these engines comprises several interconnected components that guide exhaust gases from the cylinders to the exhaust outlet, allowing for safe and efficient expulsion. Regular maintenance, including cleaning and inspection, is essential to prevent clogs, leaks, and other issues that could affect engine performance.
- Exhaust Valves:
The exhaust valves play a critical role in regulating the release of exhaust gases from the combustion chamber after each power stroke. These valves open and close at precise intervals, allowing gases to exit the cylinder and enter the exhaust manifold. Because they are exposed to high temperatures and corrosive gases, exhaust valves are susceptible to wear, carbon buildup, and potential warping. Regular inspection and cleaning help maintain their integrity and prevent issues like improper sealing or loss of compression. Adjusting the valve clearance at recommended intervals ensures optimal timing and prevents premature wear.
- Exhaust Manifold:
The exhaust manifold collects exhaust gases from each cylinder and channels them into the exhaust pipe. This component is designed to withstand high temperatures and pressure, and its structural integrity is crucial for efficient exhaust flow. Manifolds can become clogged with soot and carbon deposits, which restricts airflow and can lead to back pressure, reducing engine efficiency. Regularly cleaning the manifold and inspecting for cracks, leaks, or other damage ensures that gases are expelled efficiently. If cracks or damage are detected, immediate repair or replacement is recommended to prevent exhaust leaks and maintain performance.
- Turbocharger (if equipped):
Some Detroit Diesel 149 Series engines are equipped with turbochargers, which use exhaust gases to boost intake air pressure and improve engine power. The turbocharger relies on clean exhaust flow to function efficiently. Carbon buildup on the turbine or within the exhaust piping can reduce turbocharger performance and increase exhaust back pressure. Regular cleaning and inspection of the turbocharger and associated components help maintain optimal performance and fuel efficiency.
- Exhaust Piping and Muffler:
The exhaust piping directs gases away from the engine and towards the muffler or exhaust outlet. In addition to directing airflow, the piping and muffler help reduce noise and control emissions. Over time, exhaust pipes and mufflers can corrode or accumulate soot, which can restrict airflow and reduce efficiency. Regular inspection and cleaning prevent blockages and ensure that gases are expelled smoothly, reducing the strain on the engine.
- Heat Shields and Insulation:
Heat shields and insulation protect surrounding components from the high temperatures generated by the exhaust system. Ensuring these shields are securely in place prevents heat damage to nearby parts and enhances safety. Damaged or missing heat shields should be replaced promptly to maintain proper heat management.
Proper maintenance of these components, including cleaning and inspecting for damage, supports efficient exhaust flow, reduces the risk of back pressure, and minimizes the likelihood of overheating or power loss. Keeping the exhaust system in top condition also helps control emissions, contributing to environmental compliance.
Inspection Tips: Detecting Exhaust Leaks or Valve Wear that Can Impact Engine Performance
Routine inspection of the exhaust system is crucial for detecting issues early and preventing performance loss or damage. By following these inspection tips, technicians can identify potential problems with exhaust leaks, valve wear, and other components that could affect the engine’s efficiency.
- Detecting Exhaust Leaks:
Exhaust leaks not only reduce engine efficiency but can also lead to hazardous emissions in the surrounding area. Common signs of exhaust leaks include increased engine noise, visible smoke around the exhaust manifold, and a strong smell of exhaust fumes in the engine compartment. During inspection, look for any signs of black soot around the manifold, pipe connections, or turbocharger. Small leaks may be detectable by feeling for escaping air around the exhaust system joints or using a smoke machine to identify the source of the leak.
- Inspecting Exhaust Valves for Wear:
Exhaust valves are exposed to high temperatures and can wear down over time, affecting their ability to seal properly. Valve wear can lead to exhaust gas recirculation into the combustion chamber, reducing power and efficiency. To inspect exhaust valves, remove the valve cover and examine the valve seats for signs of pitting, cracking, or erosion. If the valves are not seating properly, perform a valve adjustment or replace the valves and seats as necessary to maintain proper sealing and timing.
- Checking for Carbon Buildup:
Carbon deposits accumulate on exhaust valves, manifolds, and turbochargers, restricting airflow and reducing efficiency. Carbon buildup on exhaust valves can prevent them from closing completely, leading to compression loss and reduced power. Examine the valves and manifold for black soot or hardened deposits, especially around the valve stems and seats. If buildup is significant, clean these components using a carbon cleaner or abrasive brush, being careful not to damage the valve surfaces.
- Examining the Turbocharger (if applicable):
Turbochargers rely on unrestricted exhaust flow to operate effectively. Inspect the turbocharger housing and turbine blades for soot or carbon deposits that can impair performance. Spin the turbine by hand to check for smooth operation and listen for unusual noises, which could indicate bearing wear. If the turbocharger shows signs of excessive buildup or damage, clean or replace it as needed to restore proper function.
- Inspecting Manifold and Pipe Connections:
The exhaust manifold and pipes should be free from cracks, loose bolts, or corrosion. Over time, repeated heating and cooling can cause metal to warp, leading to leaks or misalignments in the manifold and pipe connections. Examine these areas closely, especially around bolts and gasket joints. Tighten any loose connections and replace damaged gaskets to prevent exhaust leaks.
- Monitoring for Excessive Noise or Vibrations:
Changes in engine noise or vibrations can indicate issues within the exhaust system, such as a loose or damaged component. Listen for unusual sounds during engine operation, which may point to exhaust leaks, loose manifold bolts, or worn-out gaskets. Unusual vibrations or rattling noises could suggest a problem with the exhaust piping or muffler. Addressing these symptoms early prevents additional strain on the exhaust system and ensures smooth engine operation.
By performing regular inspections, technicians can detect signs of wear, leaks, and other issues within the exhaust system of the Detroit Diesel 149 Series engines. Proper maintenance and early identification of problems help ensure that exhaust gases are expelled efficiently, protecting the engine’s performance and longevity. Keeping the exhaust system in optimal condition also helps maintain compliance with emissions standards and reduces environmental impact.