
Key Components of the Cooling System for Detroit Diesel V71 Engines (6V71, 8V71, 12V71, 16V71)
The cooling system of Detroit Diesel V71 engines is an essential subsystem that ensures optimal engine performance and longevity. Its primary purpose is to regulate the engine’s operating temperature, prevent overheating, and maintain thermal efficiency under various load and environmental conditions. Proper maintenance of this system is vital to prevent downtime and costly repairs. Below, we delve into the key components of this cooling system and their functionalities, maintenance requirements, and common issues, ensuring a comprehensive understanding for anyone operating or maintaining these iconic engines.
1. Water Pump

Overview
The water pump is the heart of the cooling system in Detroit Diesel V71 engines, responsible for ensuring the continuous circulation of coolant throughout the engine. It is a gear-driven centrifugal pump, designed for high reliability and efficiency.
Functionality
- Coolant Circulation: The pump drives coolant from the radiator (or heat exchanger in marine applications) through the engine block, cylinder liners, and heads. This process absorbs and dissipates heat generated during combustion.
- Pressure Maintenance: By maintaining consistent pressure, the water pump ensures that coolant reaches all engine areas evenly, avoiding localized hotspots.
Key Features
- Gear-Driven Design: The gear-driven mechanism ensures a constant pumping rate proportional to engine speed, making it durable and dependable.
- Centrifugal Mechanism: This design increases fluid velocity, efficiently moving coolant through the system.
Maintenance Considerations
- Inspect Impellers: Regularly check for wear, cracks, or damage that could reduce pumping efficiency.
- Housing Inspection: Ensure the pump housing is free from cracks or corrosion.
- Seal and Gasket Replacement: Worn seals can lead to coolant leaks, impacting system performance.
2. Water Manifold
Overview
The water manifold is critical for directing coolant to various parts of the engine, ensuring even temperature distribution across all components.
Functionality
- Coolant Distribution: Directs coolant to cylinder liners, cylinder heads, and other vital areas.
- Prevention of Hotspots: By ensuring an even flow, it prevents localized overheating, which could cause thermal stress and damage.
Design Features
- Durable Materials: Typically made from corrosion-resistant metals to withstand prolonged exposure to coolant and engine heat.
- Precision Engineering: Ensures smooth and balanced coolant flow.
Maintenance Considerations
- Debris Removal: Flush the manifold periodically to remove debris and prevent blockages.
- Leak Inspection: Check for cracks or leaks at connections and fittings.
- Secure Connections: Verify that all fittings are tight and free from corrosion.
3. Thermostats
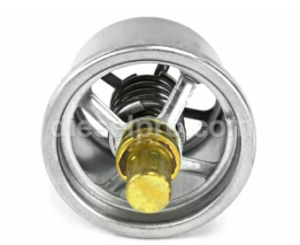
Overview
Thermostats play a vital role in regulating the engine’s operating temperature. They control the flow of coolant between the engine and the radiator, ensuring the engine warms up quickly and maintains an optimal temperature during operation.
Functionality
- Temperature Control: The thermostat remains closed during cold starts to restrict coolant flow, allowing the engine to reach operating temperature quickly.
- Automatic Opening: Once the coolant reaches the thermostat’s preset temperature (e.g., 170°F or 180°F), it opens, permitting coolant to circulate through the radiator or heat exchanger to dissipate excess heat.
Key Features
- Bi-Metallic Design: Most thermostats use a bi-metallic strip that reacts to temperature changes, providing precise control.
- Fail-Safe Mechanisms: Many thermostats are designed to fail in the open position, preventing engine overheating.
Maintenance Considerations
- Periodic Testing: Ensure the thermostat opens and closes at the designated temperature.
- Corrosion and Mechanical Checks: Replace thermostats showing signs of rust, sticking, or failure.
- Compatibility: Always use thermostats that match the engine’s operating specifications.
4. Radiator (Land Applications)
Overview
In land-based applications, the radiator is a key component of the cooling system, acting as a heat exchanger that dissipates heat from the coolant into the surrounding air.
Functionality
- Heat Dissipation: Hot coolant from the engine flows through the radiator, where it transfers heat to the air passing over the radiator’s surface.
- Enhanced Airflow: An engine-driven fan increases airflow through the radiator, improving heat exchange efficiency.
Key Features
- Tube-and-Fin Design: Maximizes the radiator’s surface area for effective heat transfer.
- Corrosion-Resistant Materials: Radiators are often constructed from aluminum or copper, chosen for their durability and thermal conductivity.
- Pressure Cap: Maintains system pressure, raising the boiling point of the coolant for more efficient heat dissipation.
Maintenance Considerations
- Fins and Tubes: Inspect and clean the fins to remove debris that could block airflow.
- Leak Checks: Regularly inspect for cracks or leaks in the tubes or connections.
- Pressure Cap Replacement: Replace the pressure cap periodically to maintain proper system pressure.
- Flushing: Remove sediment or scale buildup by flushing the radiator at recommended intervals.
5. Raw Water Pump (Marine Applications)

Overview
In marine applications, the raw water pump is a crucial component that draws seawater or freshwater from the environment into the engine’s cooling system. This pump is integral to both direct raw water-cooled and heat exchanger systems.
Functionality
- Water Intake: The pump draws water, which flows either through a heat exchanger or directly into the engine cooling system.
- Debris Management: Equipped with flexible impellers, these pumps can handle small debris and particles without immediate damage.
Key Features
- Flexible Impeller: Allows the pump to adapt to varying flow rates and minor debris without failure.
- Corrosion Resistance: Constructed from materials designed to withstand the harsh conditions of saltwater or brackish water environments.
Maintenance Considerations
- Impeller Replacement: Replace the impellers regularly to prevent failure.
- System Flushing: Remove accumulated debris or sand that could impair pump performance.
- Seal and Connection Checks: Inspect seals and fittings for leaks or wear.
6. Heat Exchanger (Marine Applications)
Overview
In marine cooling systems, the heat exchanger facilitates efficient heat transfer between the engine’s coolant and the raw water supply.
Functionality
- Dual Fluid Flow: Engine coolant flows through one side of the exchanger, while raw water flows through the other, allowing heat transfer without mixing fluids.
- Surface Area Maximization: Tubes and baffles inside the exchanger increase contact between fluids, enhancing cooling efficiency.
Key Features
- Durable Construction: Made from corrosion-resistant materials such as copper-nickel alloys to withstand marine environments.
- Modular Design: Enables easy disassembly for cleaning and maintenance.
Maintenance Considerations
- Cleaning: Remove fouling and scale from tubes and baffles regularly.
- Leak Prevention: Inspect for corrosion and replace seals and gaskets as needed.
- Raw Water Pump Monitoring: Ensure proper raw water flow rates to maintain heat exchanger performance.
Importance of Cooling System Maintenance
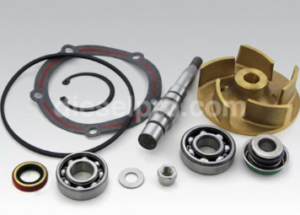
Preventative Care
- Consistent maintenance ensures steady engine performance by avoiding overheating and reducing wear on components.
- Proper cooling extends the lifespan of both the engine and its auxiliary components.
Common Cooling System Failures
- Overheating: Often caused by insufficient coolant flow, leaks, or a clogged radiator.
- Coolant Loss: Worn seals, cracked hoses, or leaks in the radiator or heat exchanger are common culprits.
- Corrosion and Scaling: These can block passages, reducing heat transfer efficiency.
- Pump Failures: Worn impellers or seals can lead to inadequate coolant circulation.
Best Practices for Maintenance
- Inspection: Conduct regular checks on all cooling system components for wear, leaks, or blockages.
- Coolant Quality: Use coolant and antifreeze blends specified by Detroit Diesel to prevent corrosion and freezing.
- System Flushes: Flush the system during scheduled maintenance intervals to remove sediment and scale.
- Prompt Repairs: Address minor issues, such as leaks or blockages, promptly to prevent escalation.
Summary and Conclusion
The cooling system of Detroit Diesel V71 engines is a sophisticated assembly of interconnected components that work in unison to regulate engine temperatures and ensure reliable performance. From the robust water pump to the efficient heat exchanger, each element plays a critical role in maintaining the engine’s operational health. Regular inspection, timely maintenance, and the use of high-quality replacement parts are essential to maximize the longevity and efficiency of these components. By following the best practices outlined above, operators can ensure their V71 engines perform optimally in both land and marine applications, minimizing downtime and preventing costly repairs.