
Introduction
-
Torque Specifications for Critical Components
- Cylinder Head Bolts
- Connecting Rod Bolts
- Main Bearing Bolts
- Exhaust Manifold Bolts
- Rocker Arm Shaft Bolts
- Flywheel Bolts
- Turbocharger Mounting Bolts (if applicable)
-
Wear Limits and Clearance Specifications
- Cylinder Liners
- Piston Rings
- Main Bearings
- Connecting Rod Bearings
- Valve Clearance (Cold)
- Crankshaft
- Camshaft
-
Tips for Using Torque Tables and Specifications
- Verify Tools and Calibration
- Replace Worn Fasteners
- Ensure Proper Sequence
- Inspect Clearances During Overhauls
- Lubricate Threads as Needed
Introduction

Accurate specifications and torque settings are fundamental for maintaining the reliability, efficiency, and long-term performance of Detroit Diesel 6V71, 8V71, 12V71, and 16V71 engines. These engines are known for their robust design and heavy-duty applications, but incorrect torque application can lead to component failures, leaks, or even catastrophic engine damage. Ensuring that each fastener is tightened to the correct specification helps maintain proper assembly integrity, reduces the risk of mechanical failures, and extends the engine’s operational life.
This comprehensive guide offers detailed torque specifications for essential fasteners such as bolts, nuts, and studs used throughout the engine assembly. It also provides an in-depth analysis of wear limits and clearance specifications for critical components, including cylinder liners, bearings, and pistons. Adhering to these specifications is essential during routine maintenance, engine rebuilds, or component replacements to ensure each part performs as intended and maintains optimal engine function under demanding conditions.
Additionally, understanding and applying the correct specifications can simplify future maintenance and troubleshooting. Consistently following proper torque values and monitoring component wear will help detect potential issues early, ensuring that minor problems do not develop into major failures. By using this guide, mechanics and technicians can ensure that their Detroit Diesel V71 engines operate at peak performance, delivering reliable power and minimizing downtime.
Parts Catalog for Detroit Diesel V71 Marine Engines
- Parts Catalog for 6V71 Detroit Diesel Marine Engine
- Parts Catalog for 8V71 Detroit Diesel Marine Engine
- Parts Catalog for 12V71 Detroit Diesel Marine Engine
- Parts Catalog for 16V71 Detroit Diesel Marine Engine
Torque Specifications for Critical Components in Detroit Diesel V71 Engines
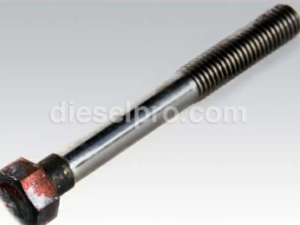
Proper torque application is essential for ensuring a secure and reliable assembly of Detroit Diesel Series V71 engines. Applying the correct torque values to fasteners helps maintain structural integrity, reduces the risk of component failure, and ensures optimal engine performance. Incorrect torque settings can lead to issues such as gasket leaks, fastener loosening, or even severe engine damage due to uneven pressure distribution. Therefore, it is crucial to adhere to the specified torque values during assembly, maintenance, and engine rebuilds.
In addition to securing components, proper torque application also helps prevent thread damage, warping, and stress-related failures. Fasteners that are under-torqued may loosen over time, while over-torqued fasteners can lead to stripped threads or distorted parts. Following the manufacturer-recommended torque specifications ensures that each component functions as designed, contributing to the overall longevity and efficiency of the engine.
Below are the detailed and recommended torque values for critical fasteners in Detroit Diesel Series V71 engines. These specifications should be followed meticulously to guarantee consistent assembly quality, reduce downtime, and enhance the engine’s operational lifespan.
1. Cylinder Head Bolts
- Torque Specification: 200-210 lb-ft (271-285 Nm)
- Sequence: Follow a crisscross pattern starting from the center and working outward to ensure even pressure distribution.
Cylinder Head Bolts & Related Components for 6V71 Non- Turbo Detroit Diesel Marine & Industrial Engines
Cylinder Head Bolts & Related Components for 6V71 Turbo Detroit Diesel Marine & Industrial Engines
Cylinder Head Bolts & Related Components for 8V71 Non- Turbo Detroit Diesel Marine & Industrial Engines
Cylinder Head Bolts & Related Components for 8V71 Turbo Detroit Diesel Marine & Industrial Engines
Cylinder Head Bolts & Related Components for 12V71 Non- Turbo Detroit Diesel Marine & Industrial Engines
Cylinder Head Bolts & Related Components for 12V71 Turbo Detroit Diesel Marine & Industrial Engines
Cylinder Head Bolts & Related Components for 16V71 Non- Turbo Detroit Diesel Marine & Industrial Engines
Cylinder Head Bolts & Related Components for 16V71 Turbo Detroit Diesel Marine & Industrial Engines
2. Connecting Rod Bolts
- Torque Specification: 45-50 lb-ft (61-68 Nm)
- Inspection:
- Check bolts for signs of stretching, wear, or thread damage.
- Replace any bolts showing elongation, cracks, or stripped threads.
Connecting Rod Bolts & Related Components for 6V71 Non- Turbo Detroit Diesel Marine & Industrial Engines
Connecting Rod Bolts & Related Components for 6V71 Turbo Detroit Diesel Marine & Industrial Engines
Connecting Rod Bolts & Related Components for 8V71 Non- Turbo Detroit Diesel Marine & Industrial Engines
Connecting Rod Bolts & Related Components for 8V71 Turbo Detroit Diesel Marine & Industrial Engines
Connecting Rod Bolts & Related Components for 12V71 Non- Turbo Detroit Diesel Marine & Industrial Engines
Connecting Rod Bolts & Related Components for 12V71 Turbo Detroit Diesel Marine & Industrial Engines
Connecting Rod Bolts & Related Components for 16V71 Non- Turbo Detroit Diesel Marine & Industrial Engines
Connecting Rod Bolts & Related Components for 16V71 Turbo Detroit Diesel Marine & Industrial Engines
3. Main Bearing Bolts
- Torque Specification: 220-230 lb-ft (298-312 Nm)
- Procedure:
- Tighten bolts incrementally in stages to prevent uneven pressure on the crankshaft.
- Re-check torque after initial assembly to confirm consistent seating.
4. Exhaust Manifold Bolts
- Torque Specification: 35-40 lb-ft (47-54 Nm)
- Recommendation:
- Use an anti-seize compound to prevent thread galling and ease future disassembly.
- Inspect bolts for signs of corrosion or weakening.
Exhaust Manifold Bolts & Related Components for 6V71 Non- Turbo Detroit Diesel Marine & Industrial Engines
Exhaust Manifold Bolts & Related Components for 6V71 Turbo Detroit Diesel Marine & Industrial Engines
Exhaust Manifold Bolts & Related Components for 8V71 Non- Turbo Detroit Diesel Marine & Industrial Engines
Exhaust Manifold Bolts & Related Components for 8V71 Turbo Detroit Diesel Marine & Industrial Engines
Exhaust Manifold Bolts & Related Components for 12V71 Non- Turbo Detroit Diesel Marine & Industrial Engines
Exhaust Manifold Bolts & Related Components for 12V71 Turbo Detroit Diesel Marine & Industrial Engines
Exhaust Manifold Bolts & Related Components for 16V71 Non- Turbo Detroit Diesel Marine & Industrial Engines
Exhaust Manifold Bolts & Related Components for 16V71 Turbo Detroit Diesel Marine & Industrial Engines
5. Rocker Arm Shaft Bolts
- Torque Specification: 35-40 lb-ft (47-54 Nm)
- Tips:
- Ensure rocker arms are properly aligned before final tightening.
- Re-check alignment post-assembly to avoid uneven wear.
Rocker Arm Shaft Bolts & Related Components for 6V71 Non- Turbo Detroit Diesel Marine & Industrial Engines
Rocker Arm Shaft Bolts & Related Components for 6V71 Turbo Detroit Diesel Marine & Industrial Engines
Rocker Arm Shaft Bolts & Related Components for 8V71 Non- Turbo Detroit Diesel Marine & Industrial Engines
Rocker Arm Shaft Bolts & Related Components for 8V71 Turbo Detroit Diesel Marine & Industrial Engines
Rocker Arm Shaft Bolts & Related Components for 12V71 Non- Turbo Detroit Diesel Marine & Industrial Engines
Rocker Arm Shaft Bolts & Related Components for 12V71 Turbo Detroit Diesel Marine & Industrial Engines
Rocker Arm Shaft Bolts & Related Components for 16V71 Non- Turbo Detroit Diesel Marine & Industrial Engines
Rocker Arm Shaft Bolts & Related Components for 16V71 Turbo Detroit Diesel Marine & Industrial Engines
6. Flywheel Bolts
- Torque Specification: 150-160 lb-ft (203-217 Nm)
- Procedure:
- Tighten in a star pattern to ensure even pressure and prevent warping.
- Tighten in a star pattern to ensure even pressure and prevent warping.
7. Turbocharger Mounting Bolts (If Applicable)
- Torque Specification: 30-35 lb-ft (41-47 Nm)
- Notes:
- Use high-temperature thread locker to maintain secure mounting.
- Re-check after initial engine run for any loosening due to heat expansion.
Turbocharger Mounting Bolts & Related Components for 6V71 Turbo Detroit Diesel Marine & Industrial Engines
Turbocharger Mounting Bolts & Related Components for 8V71 Turbo Detroit Diesel Marine & Industrial Engines
Turbocharger Mounting Bolts & Related Components for 12V71 Turbo Detroit Diesel Marine & Industrial Engines
Turbocharger Mounting Bolts & Related Components for 16V71 Turbo Detroit Diesel Marine & Industrial Engines
Wear Limits and Clearance Specifications For Detroit Diesel V71 Engines
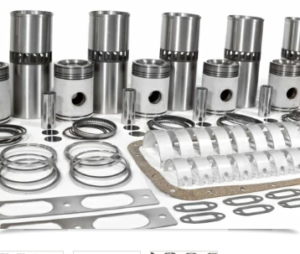
Wear limits and clearances are essential parameters for accurately evaluating the health and performance of Detroit Diesel Series V71 engines during routine maintenance, inspections, or complete rebuilds. Understanding and adhering to these specifications ensures that engine components function within their optimal operational range, reducing the risk of premature wear, mechanical failure, or reduced efficiency. Neglecting to monitor these limits can lead to significant issues such as poor compression, oil leakage, and excessive vibration, which may ultimately result in costly repairs or complete engine failure.
During maintenance or rebuilds, it is crucial to measure the wear and clearance of key engine components, including cylinder liners, pistons, bearings, and crankshafts. These measurements determine whether parts are still within their serviceable limits or need to be repaired or replaced. Even minor deviations from standard specifications can compromise the engine’s performance and reliability. Monitoring clearances also helps ensure proper lubrication, thermal expansion control, and optimal component interaction under operational stresses.
The following detailed specifications provide comprehensive guidelines for assessing the wear limits and clearances of critical components in Detroit Diesel Series V71 engines. These benchmarks are designed to assist technicians in making informed decisions during inspections and rebuilds, ensuring that the engine operates efficiently and maintains its durability over time.
1. Cylinder Liners
- Standard Inner Diameter: 4.250 inches (108 mm)
- Wear Limit: 4.270 inches (108.46 mm)
- Clearance Between Liner and Piston:
- New: 0.003-0.005 inches (0.076-0.127 mm)
- Maximum Wear: 0.007 inches (0.178 mm)
Overhaul Kit & Related Components for 6V71 Non- Turbo Detroit Diesel Marine & Industrial Engines
Overhaul Kit & Related Components for 6V71 Turbo Detroit Diesel Marine & Industrial Engines
Overhaul Kit & Related Components for 8V71 Non- Turbo Detroit Diesel Marine & Industrial Engines
Overhaul Kit & Related Components for 8V71 Turbo Detroit Diesel Marine & Industrial Engines
Overhaul Kit & Related Components for 12V71 Non- Turbo Detroit Diesel Marine & Industrial Engines
Overhaul Kit & Related Components for 12V71 Turbo Detroit Diesel Marine & Industrial Engines
Overhaul Kit & Related Components for 16V71 Non- Turbo Detroit Diesel Marine & Industrial Engines
Overhaul Kit & Related Components for 16V71 Turbo Detroit Diesel Marine & Industrial Engines
2. Piston Rings
- End Gap (Installed in Liner):
- New: 0.010-0.020 inches (0.254-0.508 mm)
- Maximum Wear: 0.040 inches (1.016 mm)
- Side Clearance in Groove:
- New: 0.001-0.003 inches (0.025-0.076 mm)
- Maximum Wear: 0.005 inches (0.127 mm)
Piston Rings & Related Components for 6V71 Non- Turbo Detroit Diesel Marine & Industrial Engines
Piston Rings & Related Components for 6V71 Turbo Detroit Diesel Marine & Industrial Engines
Piston Rings & Related Components for 8V71 Non- Turbo Detroit Diesel Marine & Industrial Engines
Piston Rings & Related Components for 8V71 Turbo Detroit Diesel Marine & Industrial Engines
Piston Rings & Related Components for 12V71 Non- Turbo Detroit Diesel Marine & Industrial Engines
Piston Rings & Related Components for 12V71 Turbo Detroit Diesel Marine & Industrial Engines
Piston Rings & Related Components for 16V71 Non- Turbo Detroit Diesel Marine & Industrial Engines
Piston Rings & Related Components for 16V71 Turbo Detroit Diesel Marine & Industrial Engines
3. Main Bearings
- Inner Diameter (Installed):
- Standard: 3.875-3.877 inches (98.43-98.48 mm)
- Clearance Between Bearing and Crankshaft:
- New: 0.001-0.003 inches (0.025-0.076 mm)
- Maximum Wear: 0.005 inches (0.127 mm)
4. Connecting Rod Bearings
- Bearing Clearance:
- New: 0.002-0.004 inches (0.051-0.102 mm)
- Maximum Wear: 0.006 inches (0.152 mm)
Connecting Rod Bearings & Related Components for 6V71 Non- Turbo Detroit Diesel Marine & Industrial Engines
Connecting Rod Bearings & Related Components for 6V71 Turbo Detroit Diesel Marine & Industrial Engines
Connecting Rod Bearings & Related Components for 8V71 Non- Turbo Detroit Diesel Marine & Industrial Engines
Connecting Rod Bearings & Related Components for 8V71 Turbo Detroit Diesel Marine & Industrial Engines
Connecting Rod Bearings & Related Components for 12V71 Non- Turbo Detroit Diesel Marine & Industrial Engines
Connecting Rod Bearings & Related Components for 12V71 Turbo Detroit Diesel Marine & Industrial Engines
Connecting Rod Bearings & Related Components for 16V71 Non- Turbo Detroit Diesel Marine & Industrial Engines
Connecting Rod Bearings & Related Components for 16V71 Turbo Detroit Diesel Marine & Industrial Engines
5. Valve Clearance (Cold)
- Intake Valve: 0.012 inches (0.305 mm)
- Exhaust Valve: 0.016 inches (0.406 mm)
Valve & Related Components for 6V71 Non- Turbo Detroit Diesel Marine & Industrial Engines
Valve & Related Components for 6V71 Turbo Detroit Diesel Marine & Industrial Engines
Valve & Related Components for 8V71 Non- Turbo Detroit Diesel Marine & Industrial Engines
Valve & Related Components for 8V71 Turbo Detroit Diesel Marine & Industrial Engines
Valve & Related Components for 12V71 Non- Turbo Detroit Diesel Marine & Industrial Engines
Valve & Related Components for 12V71 Turbo Detroit Diesel Marine & Industrial Engines
Valve & Related Components for 16V71 Non- Turbo Detroit Diesel Marine & Industrial Engines
Valve & Related Components for 16V71 Turbo Detroit Diesel Marine & Industrial Engines
6. Crankshaft
- Main Journal Diameter:
- Standard: 3.875-3.877 inches (98.43-98.48 mm)
- Maximum Wear: 0.003 inches (0.076 mm) taper or out-of-round
- Connecting Rod Journal Diameter:
- Standard: 3.000-3.002 inches (76.20-76.25 mm)
- Maximum Wear: 0.002 inches (0.051 mm) taper or out-of-round
Crankshaft & Related Components for 6V71 Non- Turbo Detroit Diesel Marine & Industrial Engines
Crankshaft & Related Components for 6V71 Turbo Detroit Diesel Marine & Industrial Engines
Crankshaft & Related Components for 8V71 Non- Turbo Detroit Diesel Marine & Industrial Engines
Crankshaft & Related Components for 8V71 Turbo Detroit Diesel Marine & Industrial Engines
Crankshaft & Related Components for 12V71 Non- Turbo Detroit Diesel Marine & Industrial Engines
Crankshaft & Related Components for 12V71 Turbo Detroit Diesel Marine & Industrial Engines
Crankshaft & Related Components for 16V71 Non- Turbo Detroit Diesel Marine & Industrial Engines
Crankshaft & Related Components for 16V71 Turbo Detroit Diesel Marine & Industrial Engines
7. Camshaft
- Lobe Height:
- Standard: 1.85 inches (46.99 mm)
- Minimum: 1.80 inches (45.72 mm)
- Journal Diameter:
- Standard: 2.249-2.251 inches (57.15-57.20 mm)
Camshaft & Related Components for 6V71 Non- Turbo Detroit Diesel Marine & Industrial Engines
Camshaft & Related Components for 6V71 Turbo Detroit Diesel Marine & Industrial Engines
Camshaft & Related Components for 8V71 Non- Turbo Detroit Diesel Marine & Industrial Engines
Camshaft& Related Components for 8V71 Turbo Detroit Diesel Marine & Industrial Engines
Camshaft & Related Components for 12V71 Non- Turbo Detroit Diesel Marine & Industrial Engines
Camshaft & Related Components for 12V71 Turbo Detroit Diesel Marine & Industrial Engines
Camshaft & Related Components for 16V71 Non- Turbo Detroit Diesel Marine & Industrial Engines
Camshaft & Related Components for 16V71 Turbo Detroit Diesel Marine & Industrial Engines
Tips for Using Torque Tables and Specifications
Correct torque application is essential for ensuring the long-term durability, optimal performance, and operational safety of Detroit Diesel V71 engines. Each fastener within the engine assembly must be tightened to precise specifications to maintain proper structural integrity, prevent leaks, and avoid premature wear or failure of critical components. Incorrect torque—whether under-torquing or over-torquing—can lead to engine malfunctions, reduced efficiency, or even severe mechanical damage.
Adhering to proper torque specifications is particularly critical during routine maintenance, major overhauls, or when replacing key engine parts. Accurate torque settings help distribute loads evenly across engine components, reduce the risk of distortion, and ensure that gaskets and seals maintain proper compression. This not only contributes to the smooth operation of the engine but also minimizes the risk of long-term wear and tear.
The following tips provide a more in-depth approach to achieving precise torque application and maintaining overall engine integrity. By following these guidelines, technicians can ensure that every assembly step is completed with accuracy, reducing the likelihood of failures and extending the lifespan of Detroit Diesel V71 engines. Consistent torque application is a fundamental practice for preserving engine performance and reliability under demanding operating conditions.
1. Verify Tools and Calibration
-
Use a Calibrated Torque Wrench: Always use a torque wrench that has been professionally calibrated to ensure accurate torque application. An incorrect reading can lead to under-tightening or over-tightening, which may cause damage to engine components or lead to mechanical failure.
-
Frequency of Calibration: Torque wrenches should be calibrated at least once every 12 months or after 5,000 cycles, whichever comes first. Additionally, calibrate the tool if it has been dropped or subjected to rough handling.
-
Pre-Check Before Critical Work: Before starting critical rebuilds or assembly processes, perform a quick test to ensure the torque wrench provides consistent and accurate readings. This simple check can prevent serious assembly errors.
-
Storage Best Practices: Store torque wrenches in a protective case and avoid exposing them to moisture or extreme temperatures. Always set the torque wrench to its lowest setting after use to maintain accuracy over time.
2. Replace Worn Fasteners
-
Visual Inspection: Before reassembly, inspect every bolt, nut, and stud for signs of wear, including stretching, cracking, and damaged threads. Fasteners subjected to high torque or vibration are more prone to these issues.
-
Stretch Check: If a bolt has been used multiple times, check for elongation. This can be done by comparing its length to a new bolt. Elongation may compromise the bolt’s ability to maintain the correct torque.
-
Thread Wear: Examine threads for stripping or damage, which can affect the ability of fasteners to hold torque. Replace any fasteners with worn or damaged threads to ensure assembly integrity.
-
Material Condition: Look for signs of corrosion, rust, or pitting, especially if the fasteners are exposed to high temperatures or humid environments. Replace affected parts promptly to avoid failure during operation.
-
Use of OEM-Matching Fasteners: When replacing fasteners, always use premium aftermarket parts that match original specifications for size, strength, and thread pitch to maintain proper torque application.
3. Ensure Proper Sequence
-
Follow Manufacturer-Specified Patterns: Adhere to the specified tightening sequences, such as a crisscross or star pattern, especially for components like cylinder heads and flywheels. This ensures even pressure distribution and prevents warping or component failure.
-
Incremental Torque Application: Tighten fasteners in incremental stages, gradually increasing to the final torque specification. This method helps avoid uneven pressure buildup and reduces the risk of gasket failure.
-
Re-Torque After Initial Assembly: After the first engine warm-up, recheck the torque on critical components. Thermal expansion can cause bolts to loosen slightly, and re-torquing ensures sustained fastening integrity.
-
Documentation: Keep a detailed record of torque values and sequences used during assembly. This record can be a valuable reference for future maintenance or troubleshooting.
4. Inspect Clearances During Overhauls
-
Measure Precisely: Use precise measurement tools such as micrometers, dial bore gauges, and feeler gauges to check wear limits and clearances of critical components like bearings, liners, and pistons.
-
Know the Limits: Always compare your measurements with the provided wear limits and clearances. If any component is approaching or exceeding its limit, consider replacement to avoid premature failure.
-
Check for Consistency: Measure multiple points on components such as crankshafts and camshafts to check for out-of-round or taper conditions. Inconsistent readings may indicate uneven wear and the need for machining or replacement.
-
Inspect Companion Parts: When inspecting a component for wear, always check the parts it interfaces with (e.g., when checking a bearing, also inspect the crankshaft journal). This ensures comprehensive maintenance and prevents future issues.
-
Document Measurements: Keep a log of all measurements during overhauls. This helps track wear patterns over time and can inform decisions during future maintenance.
5. Lubricate Threads as Needed
-
Use the Right Lubricant: Apply the recommended lubricant or anti-seize compound to bolt threads where specified. This helps achieve accurate torque readings and reduces the risk of galling or seizing during future disassembly.
-
Avoid Over-Application: Use lubricant sparingly to prevent excess from contaminating other engine components. Wipe away any surplus to avoid unwanted residue build-up.
-
Understand Material Needs: Recognize that different materials may require specific lubricants. For instance, stainless steel fasteners may require different anti-seize compounds compared to carbon steel bolts.
-
High-Temperature Considerations: For components subjected to high temperatures, ensure the lubricant or thread locker is rated to withstand the expected operating conditions.
-
Future Maintenance: Proper lubrication not only aids in achieving correct torque but also simplifies future disassembly. This prevents bolt seizure and reduces the risk of damaging components during maintenance.