
Introduction to the Cummins C Series
The Cummins C Series engines have established themselves as some of the most reliable and versatile powerplants in the world of diesel engines. Known for their robust construction, fuel efficiency, and long service life, these engines have been extensively used in a wide array of applications, including industrial machinery, marine vessels, trucking, agriculture, and construction equipment. First introduced in the late 1980s, the Cummins C Series quickly gained popularity due to its ability to deliver consistent performance under extreme operating conditions.
The Cummins C Series falls within the mid-range diesel engine category, with displacements typically around 8.3 liters (504.5 cubic inches). These engines are designed to offer a balance between power output and fuel efficiency, making them suitable for both light and heavy-duty applications. The series includes several models, each with unique features and configurations tailored to specific operational demands.
Parts Catalog for Cummins 6C Marine Engine
Parts Catalog for Cummins 6CT Marine Engine
Parts Catalog for Cummins 6CTA Marine Engine
Key attributes of the Cummins C Series include
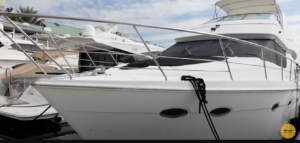
- Durable Cast Iron Construction: Ensures long-lasting performance in harsh environments.
- Turbocharging Options: Enhances power output and improves fuel efficiency.
- Ease of Maintenance: Simplified design allows for easier servicing and reduced downtime.
- Versatile Applications: Used in everything from marine propulsion systems to agricultural tractors.
The Cummins C Series engines are well-known for their mechanical simplicity combined with advanced engineering, allowing operators and mechanics to perform maintenance tasks with ease while enjoying the benefits of modern diesel technology.
Key Models Covered
The Cummins C Series comprises several notable models, with the most prominent being the 6C, 6CT, and 6CTA. Each model offers specific advantages based on its configuration, performance characteristics, and intended applications.
Cummins 6C
The Cummins 6C is the foundation of the C Series lineup. It is a 6-cylinder, inline diesel engine known for its mechanical simplicity and rugged construction. The 6C operates using a mechanical fuel injection system, which provides ease of maintenance and reliability, especially in regions where advanced diagnostic tools may not be readily available.
Key Features of the Cummins 6C:
- Displacement: 8.3 liters (504.5 cubic inches)
- Fuel System: Mechanical direct injection
- Power Output: Varies by application, typically between 150–250 horsepower
- Applications: Industrial equipment, generators, agricultural machinery, and medium-duty trucks
The 6C is often favored in applications where reliability and ease of service are prioritized over advanced electronic controls. Its straightforward mechanical design makes it an excellent choice for operations in remote locations or environments with limited access to specialized service centers.
Cummins 6CT
The Cummins 6CT builds upon the 6C’s solid foundation by incorporating turbocharging to improve power output and fuel efficiency. The addition of a turbocharger allows the engine to deliver more power without increasing its displacement, making it an efficient option for applications requiring greater performance.
Key Features of the Cummins 6CT:
- Displacement: 8.3 liters
- Fuel System: Mechanical direct injection with turbocharging
- Power Output: Typically ranges from 200–300 horsepower
- Applications: Heavy-duty trucks, construction machinery, marine auxiliary engines, and power generation
The turbocharged 6CT is popular in industries where higher torque and improved fuel economy are essential. The engine’s design allows for better airflow, resulting in more efficient combustion and reduced emissions compared to naturally aspirated engines.
Parts Catalog for Cummins 6CT Marine Engine
Cummins 6CTA
The Cummins 6CTA represents the most advanced version of the C Series, featuring turbocharging and an aftercooler (intercooler) to further enhance engine performance. The aftercooler cools the compressed air from the turbocharger before it enters the combustion chamber, increasing air density and improving combustion efficiency.
Key Features of the Cummins 6CTA:
- Displacement: 8.3 liters
- Fuel System: Mechanical or electronic direct injection with turbocharging and aftercooling
- Power Output: Typically ranges from 250–400 horsepower, depending on configuration
- Applications: Marine propulsion, heavy-duty construction equipment, transit buses, and military vehicles
The 6CTA is renowned for its high power-to-weight ratio, making it an ideal choice for demanding applications where performance and fuel efficiency are critical. Its combination of advanced cooling systems, robust internal components, and versatile tuning options has cemented its status as a favorite among operators who require both power and reliability.
Parts Catalog for Cummins 6CTA Marine Engine
Differences Between 1991 and 1994 Certification Levels
The 1991 and 1994 certification levels refer to changes in emissions standards and engine performance regulations implemented by agencies such as the Environmental Protection Agency (EPA). These certification levels were designed to address the growing concern over diesel engine emissions, particularly regarding nitrogen oxides (NOx), particulate matter (PM), and carbon monoxide (CO) emissions.
Understanding the differences between these certification levels is essential for operators, mechanics, and fleet managers who work with Cummins C Series engines, as they impact both engine design and maintenance practices.
Key Differences:
- Emission Standards:
- 1991 Certification Level: Focused on reducing particulate matter (PM) emissions and improving basic fuel efficiency. Engines from this era relied primarily on mechanical fuel injection systems and basic emission control technologies.
- 1994 Certification Level: Introduced stricter controls on NOx emissions, requiring engines to meet more stringent limits. This led to the adoption of advanced fuel injection systems, including the early integration of electronic control modules (ECMs) in some models.
- Fuel Injection Technology:
Electronic Injector for the 1994 and newer cummins 6C, 6CT and 6CTA engines
Mechanical Injector for cummins 6C, 6CT and 6CTA engines
- 1991 Engines: Predominantly mechanical injection systems, which are simple, durable, and easy to service without specialized tools.
- 1994 Engines: Began incorporating electronically controlled fuel injection systems to improve precision, fuel atomization, and combustion efficiency, reducing emissions and enhancing performance.
- Turbocharging and Aftercooling:
Turbocharger for Cummins 6CT and 6CTA Engines
- 1991 Models: Basic turbocharging without aftercoolers was common, limiting the potential for performance enhancements.
- 1994 Models: Greater use of aftercoolers (intercoolers) to improve air density and lower combustion temperatures, contributing to reduced NOx emissions and increased power output.
- Exhaust Gas Recirculation (EGR):
- 1991 Engines: Typically did not feature EGR systems, as they were not yet mandated for emissions compliance.
- 1994 Engines: Some models introduced EGR systems to reduce NOx emissions by recirculating a portion of the exhaust gases back into the intake manifold, lowering combustion temperatures.
- Durability and Service Life:
- Engines from both certification levels are known for their durability, but 1994 models often require more specialized diagnostic tools for troubleshooting due to the inclusion of electronic systems.
- Engines from both certification levels are known for their durability, but 1994 models often require more specialized diagnostic tools for troubleshooting due to the inclusion of electronic systems.
Understanding these differences is crucial when sourcing parts, performing diagnostics, or making adjustments to ensure compliance with regulatory requirements and optimal engine performance.
Importance of Proper Servicing and Maintenance
Proper servicing and maintenance are vital for maximizing the lifespan, performance, and efficiency of Cummins C Series engines. Regular maintenance helps identify potential issues before they escalate, reduces the risk of unexpected breakdowns, and ensures the engine operates within manufacturer specifications.
Key Maintenance Practices:
- Regular Oil Changes:
New oil pump, for use in Cummins 6C, 6CT and 6CTA engines.
- Diesel engines rely on high-quality oil to lubricate moving parts and reduce friction.
- Regular oil changes help prevent sludge buildup, contamination, and premature wear.
Lubrication System & Related Components for Cummins 6C Marine & Industrial Engines
Lubrication System & Related Components for Cummins 6CT Marine & Industrial Engines
Lubrication System & Related Components for Cummins 6CTA Marine & Industrial Engines
- Fuel System Maintenance:
Fuel Pump for Cummins 6CTA engine
- Replace fuel filters regularly to prevent clogging and ensure consistent fuel delivery.
- Bleed air from the fuel system after maintenance to avoid hard starts and performance issues.
Fuel System & Related Components for Cummins 6C Marine & Industrial Engines
Fuel System & Related Components for Cummins 6CT Marine & Industrial Engines
Fuel System & Related Components for Cummins 6CTA Marine & Industrial Engines
- Cooling System Care:
Fresh Water Pump for Cummins ISB 6.7, QSB 6.7, 6C, 6CT, 6CTA Engines
- Check coolant levels frequently and maintain the proper coolant mixture to prevent overheating.
- Inspect hoses, the radiator, and the water pump for leaks or signs of wear.
Cooling System & Related Components for Cummins 6C Marine & Industrial Engines
Cooling System & Related Components for Cummins 6CT Marine & Industrial Engines
Cooling System & Related Components for Cummins 6CTA Marine & Industrial Engines
Raw Water Pump & Related Components for Cummins 6C Marine & Industrial Engines
Raw Water Pump & Related Components for Cummins 6CT Marine & Industrial Engines
Raw Water Pump & Related Components for Cummins 6CTA Marine & Industrial Engines
- Valve Adjustments:
New intake valve, for Cummins 6C8.3, 6CT8.3 and 6CTA8.3 engines.
- Regular valve lash adjustments ensure proper engine timing and prevent valve damage.
- This practice is essential for maintaining compression and fuel efficiency.
Valve & Related Components for Cummins 6C Marine & Industrial Engines
Valve & Related Components for Cummins 6CT Marine & Industrial Engines
Valve & Related Components for Cummins 6CTA Marine & Industrial Engines
- Turbocharger Inspection:
Turbocharger for Cummins 6CT and 6CTA Engines
- Check for signs of turbo lag, excessive smoke, or oil leaks, which could indicate turbocharger issues.
- Keep the air filter clean to prevent debris from damaging the turbo.
Turbocharger & Related Components for Cummins 6CT Marine & Industrial Engines
Turbocharger & Related Components for Cummins 6CTA Marine & Industrial Engines
- Exhaust and Emissions System Checks:
Exhaust Manifold Marine for Cummins 6C, 6CT, 6CTA
- Inspect the exhaust manifold for leaks and the EGR system for proper operation.
- Monitor emission levels to ensure compliance with environmental regulations.
Exhaust & Related Components for Cummins 6C Marine & Industrial Engines
Exhaust & Related Components for Cummins 6CT Marine & Industrial Engines
Exhaust & Related Components for Cummins 6CTA Marine & Industrial Engines
- Electrical System Diagnostics:
Starter for Detroit Diesel – Cummins, 12 Volts – RH – New
- Test the battery, alternator, and starter motor regularly to avoid electrical failures.
- Check for parasitic draws that can drain the battery when the engine is off.
Electrical System & Related Components for Cummins 6C Marine & Industrial Engines
Electrical System & Related Components for Cummins 6CT Marine & Industrial Engines
Electrical System & Related Components for Cummins 6CTA Marine & Industrial Engines
Benefits of Proper Maintenance
- Extended Engine Life: Prevents premature wear and prolongs the lifespan of critical components.
- Improved Fuel Efficiency: Ensures the engine operates at peak efficiency, reducing fuel costs.
- Enhanced Reliability: Reduces the risk of breakdowns, minimizing downtime and repair expenses.
- Regulatory Compliance: Maintains emissions within legal limits, avoiding fines and penalties.
- Optimal Performance: Keeps the engine running smoothly, delivering the power needed for demanding applications.
Conclusion
The Cummins C Series engines—including the 6C, 6CT, and 6CTA—have proven to be some of the most reliable and versatile diesel engines in their class. Understanding the differences between the 1991 and 1994 certification levels is crucial for proper maintenance and regulatory compliance. Regular servicing and preventive maintenance not only ensure optimal performance but also contribute to the engine’s longevity, fuel efficiency, and environmental sustainability.
Whether used in trucks, boats, construction equipment, or power generators, the Cummins C Series remains a trusted choice for operators who demand durability, performance, and reliability in their diesel engines.
Parts Catalog for Cummins 6C Marine Engine
Parts Catalog for Cummins 6CT Marine Engine
Parts Catalog for Cummins 6CTA Marine Engine