
Preventive maintenance is essential for the long-term performance, reliability, and efficiency of Cummins ISB and QSB engines. These engines are designed for durability, but like all mechanical systems, they require regular upkeep to prevent wear, minimize downtime, and extend operational life. This comprehensive guide covers the importance of regular maintenance schedules, outlines key maintenance tasks that help extend engine life, and emphasizes the significance of monitoring engine performance metrics.
Parts Catalog Main Page for Cummins ISB Marine Engine
Cummins ISB 4.5 & Related Components
Cummins ISB 5.9 & Related components
Cummins ISB 6.7 & Related Components
Parts Catalog Main page for Cummins QSB Marine Engine
Cummins QSB 4.5 & Related Components
Cummins QSB 5.9 & Related Components
Cummins QSB 6.7 & Related Components
Cummins QSB 7.0 & Related Components
1. Importance of Regular Maintenance Schedules

A. Why Preventive Maintenance Matters
Preventive maintenance (PM) is a proactive approach that focuses on performing regular inspections, servicing, and minor repairs before major issues develop. It reduces the risk of unexpected breakdowns and ensures that the engine operates efficiently under all conditions.
Key Benefits of Preventive Maintenance:
- Increased Engine Longevity:
- Regular maintenance reduces wear on engine components, extending the lifespan of critical parts like pistons, valves, and turbochargers.
- Regular maintenance reduces wear on engine components, extending the lifespan of critical parts like pistons, valves, and turbochargers.
- Improved Fuel Efficiency:
- A well-maintained engine burns fuel more efficiently, leading to cost savings over time.
- A well-maintained engine burns fuel more efficiently, leading to cost savings over time.
- Reduced Downtime:
- Preventive maintenance helps identify and fix minor issues before they escalate into costly breakdowns, minimizing operational interruptions.
- Preventive maintenance helps identify and fix minor issues before they escalate into costly breakdowns, minimizing operational interruptions.
- Enhanced Safety:
- Regular inspections help detect potential safety hazards, such as fuel leaks, worn-out belts, or faulty brakes, reducing the risk of accidents.
- Regular inspections help detect potential safety hazards, such as fuel leaks, worn-out belts, or faulty brakes, reducing the risk of accidents.
- Lower Repair Costs:
- Addressing problems early prevents major failures that require expensive parts and labor.
- Addressing problems early prevents major failures that require expensive parts and labor.
- Compliance with Regulations:
- In industries where emissions and safety standards are regulated, preventive maintenance helps meet legal requirements.
- In industries where emissions and safety standards are regulated, preventive maintenance helps meet legal requirements.
B. Maintenance Schedule Intervals
The frequency of preventive maintenance depends on factors like the engine’s operating environment, load conditions, and hours of operation. Cummins recommends maintenance based on mileage (for on-highway applications) or operating hours (for industrial/marine engines).
Typical Maintenance Intervals:
- Daily/Pre-Operation Checks: Visual inspections, fluid level checks.
- Every 250 Hours or 6,000 Miles: Oil and filter changes, air filter inspection, battery checks.
- Every 500 Hours or 12,000 Miles: Fuel filter replacement, coolant system inspection.
- Annually or 1,000 Hours: Valve adjustments, coolant flush, turbocharger inspection.
Note: Always refer to the Cummins service manual for engine-specific maintenance intervals.
2. Key Maintenance Tasks to Extend Engine Life
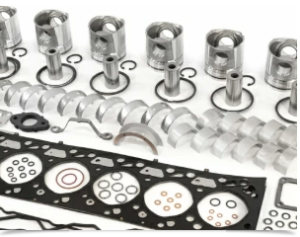
Proper preventive maintenance involves a combination of routine inspections, scheduled servicing, and proactive part replacements. Below are the key maintenance tasks critical for the longevity of Cummins ISB and QSB engines.
A. Engine Oil and Filter Maintenance
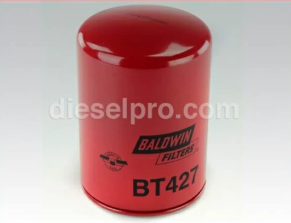
1. Regular Oil Changes
- Why It’s Important: Engine oil lubricates moving parts, reduces friction, and helps regulate temperature. Over time, oil degrades due to heat, contamination, and combustion by-products.
- Recommended Interval: Every 250-500 hours or as specified by Cummins, depending on operating conditions.
2. Signs of Oil Issues:
- Dark, dirty oil on the dipstick.
- Low oil pressure warning light.
- Unusual engine noises (knocking, ticking).
Best Practices:
- Use Cummins-recommended oil grades and specifications.
- Replace the oil filter with every oil change.
- Check for oil leaks around seals and gaskets.
Oil Filter & Related Components for Cummins ISB 4.5 Engine
Oil Filter & Related Components for Cummins ISB 5.9 Engine
Oil Filter & Related Components for Cummins ISB 6.7 Engine
Oil Filter & Related Components for Cummins QSB 4.5 Engine
Oil Filter & Related Components for Cummins QSB 5.9 Engine
Oil Filter & Related Components for Cummins QSB 6.7 Engine
Oil Filter & Related Components for Cummins QSB 7.0 Engine
B. Fuel System Maintenance
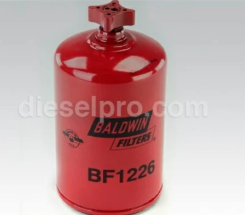
1. Fuel Filter Replacement
- Why It’s Important: Clean fuel is critical for optimal engine performance. The fuel filter prevents contaminants from reaching injectors and causing damage.
- Recommended Interval: Every 500 hours or 12,000 miles.
2. Water Separator Draining
- Why It’s Important: Diesel fuel can contain water, which promotes corrosion in the fuel system.
- Frequency: Check and drain water separators weekly, especially in humid environments.
3. Fuel Injector Inspection
- Signs of Issues: Hard starting, rough idling, poor fuel economy.
- Maintenance Tip: Use high-quality fuel and consider fuel additives to keep injectors clean.
Fuel Filter & Related Components for Cummins ISB 4.5 Engine
Fuel Filter & Related Components for Cummins ISB 5.9 Engine
Fuel Filter & Related Components for Cummins ISB 6.7 Engine
Fuel Filter & Related Components for Cummins QSB 4.5 Engine
Fuel Filter & Related Components for Cummins QSB 5.9 Engine
Fuel Filter & Related Components for Cummins QSB 6.7 Engine
Fuel Filter & Related Components for Cummins QSB 7.0 Engine
C. Cooling System Maintenance
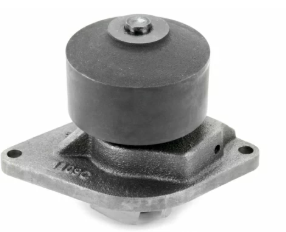
1. Coolant Level Checks
- Importance: Proper coolant levels prevent overheating, which can cause engine damage.
- Frequency: Check daily or before each operation.
2. Coolant Flush and Replacement
- Why It’s Necessary: Over time, coolant loses its anti-corrosion properties and can form deposits.
- Interval: Every 1,000 hours or as recommended by Cummins.
3. Radiator and Hose Inspections
- Look for leaks, cracks, or soft spots in hoses.
- Clean radiator fins to prevent airflow restrictions.
Cooling System & Related Components for Cummins ISB 4.5 Engine
Cooling System & Related Components for Cummins ISB 5.9 Engine
Cooling System & Related Components for Cummins ISB 6.7 Engine
Cooling System & Related Components for Cummins QSB 4.5 Engine
Cooling System & Related Components for Cummins QSB 5.9 Engine
Cooling System & Related Components for Cummins QSB 6.7 Engine
Cooling System & Related Components for Cummins QSB 7.0 Engine
Marine water pump for Cummins marine engines B & QSB
Raw Water Pump & Related Components for Cummins QSB 5.9 Engine
Raw Water Pump & Related Components for Cummins QSB 6.7 Engine
Raw Water Pump & Related Components for Cummins QSB 7.0 Engine
D. Air Intake System Maintenance

1. Air Filter Inspection and Replacement
- Why It’s Important: A clogged air filter reduces airflow, causing poor fuel efficiency and power loss.
- Frequency: Inspect every 250 hours and replace as needed.
2. Turbocharger Maintenance
- Routine Checks: Inspect for oil leaks, shaft play, and foreign object damage.
- Signs of Issues: Whining noises, black smoke, loss of power.
Air Filter & Related Components for Cummins ISB 4.5 Engine
Air Filter & Related Components for Cummins ISB 5.9 Engine
Air Filter & Related Components for Cummins ISB 6.7 Engine
Air Filter & Related Components for Cummins QSB 4.5 Engine
Air Filter & Related Components for Cummins QSB 5.9 Engine
Air Filter & Related Components for Cummins QSB 6.7 Engine
Air Filter & Related Components for Cummins QSB 7.0 Engine
E. Electrical System Maintenance
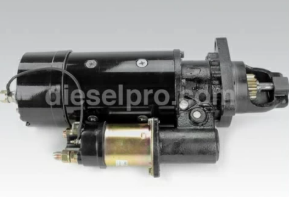
1. Battery Maintenance
- Tasks: Clean terminals, check for corrosion, and ensure tight connections.
- Test: Measure voltage regularly; a fully charged battery should read 12.6 volts.
2. Alternator and Starter Checks
- Inspect wiring for wear, loose connections, and proper grounding.
- Test alternator output to ensure the charging system is functioning.
Starter & Related Components for Cummins ISB 4.5 Engine
Starter & Related Components for Cummins ISB 5.9 Engine
Starter & Related Components for Cummins ISB 6.7 Engine
Starter & Related Components for Cummins QSB 4.5 Engine
Starter & Related Components for Cummins QSB 5.9 Engine
Starter & Related Components for Cummins QSB 6.7 Engine
Starter & Related Components for Cummins QSB 7.0 Engine
F. Exhaust and Emissions System Maintenance
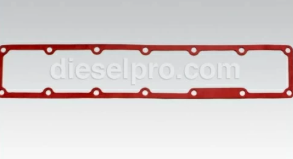
1. Diesel Particulate Filter (DPF) Checks
- Importance: DPF captures soot and particulates to reduce emissions.
- Maintenance: Monitor for regeneration cycles and clean or replace as needed.
2. Exhaust System Inspection
- Check for leaks, loose clamps, and corrosion.
G. Valve Adjustment

1. Why It’s Important:
- Correct valve clearance ensures optimal engine breathing, improving efficiency and performance.
- Interval: Every 1,000 hours or per Cummins’ recommendations.
Valve & Related Components for Cummins ISB 4.5 Engine
Valve & Related Components for Cummins ISB 5.9 Engine
Valve & Related Components for Cummins ISB 6.7 Engine
Valve & Related Components for Cummins QSB 4.5 Engine
Valve & Related Components for Cummins QSB 5.9 Engine
Valve & Related Components for Cummins QSB 6.7 Engine
Valve & Related Components for Cummins QSB 7.0 Engine
H. Lubrication System Inspection
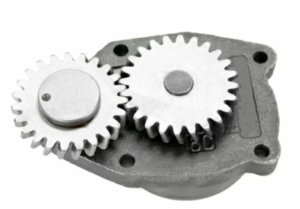
- Tasks: Check oil pressure, inspect for leaks, and monitor oil consumption.
- Importance: Proper lubrication prevents premature wear of engine components.
Lubrication System & Related Components for Cummins ISB 4.5 Engine
Lubrication System & Related Components for Cummins ISB 5.9 Engine
Lubrication System & Related Components for Cummins ISB 6.7 Engine
Lubrication System & Related Components for Cummins QSB 4.5 Engine
Lubrication System & Related Components for Cummins QSB 5.9 Engine
Lubrication System & Related Components for Cummins QSB 6.7 Engine
Lubrication System & Related Components for Cummins QSB 7.0 Engine
3. Monitoring Engine Performance Metrics
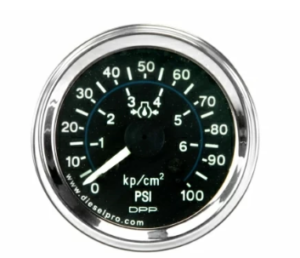
Effective preventive maintenance goes beyond scheduled tasks. Real-time monitoring of engine performance metricscan provide early warnings of potential issues.
A. Key Engine Performance Metrics to Monitor
1. Oil Pressure
- Normal Range: Typically between 30–60 PSI depending on load and RPM.
- Low Oil Pressure Causes: Low oil level, worn bearings, faulty oil pump.
- Monitoring Tools: Engine oil pressure gauge or ECM diagnostics.
2. Coolant Temperature
- Normal Range: 180°F to 210°F.
- High Temperature Causes: Coolant leaks, radiator clogs, failing water pump.
- Warning Signs: Temperature gauge spikes, coolant loss, or steam.
3. Exhaust Gas Temperature (EGT)
- Importance: High EGTs can damage the turbocharger and exhaust components.
- Safe Range: Typically under 1,250°F under heavy load.
- Causes of High EGT: Over-fueling, restricted airflow, turbo issues.
4. Boost Pressure (for Turbocharged Engines)
- Normal Range: Varies based on load but typically around 20–30 PSI for ISB & QSB engines.
- Low Boost Causes: Turbocharger failure, intercooler leaks, wastegate issues.
5. Battery Voltage
- Normal Range: 12.6 volts (engine off) and 13.8–14.4 volts (engine running).
- Low Voltage Causes: Failing alternator, battery issues, bad connections.
6. Fuel Economy
- Monitor fuel consumption regularly.
- Sudden drops in efficiency can indicate injector problems, air filter restrictions, or sensor failures.
B. Using Engine Diagnostic Tools
1. On-Board Diagnostic Systems (OBD)
- Cummins INSITE: A powerful diagnostic tool for accessing fault codes, performance data, and real-time monitoring.
2. ECM Data Analysis
- Review engine data logs to identify trends in temperature, pressure, and other parameters.
3. Remote Monitoring Systems
- Telematics: In fleet applications, remote diagnostics help monitor performance metrics, track maintenance schedules, and detect faults early.
4. Best Practices for Preventive Maintenance
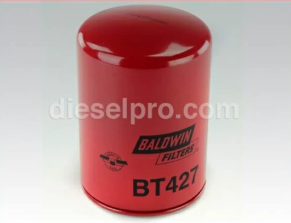
A. Keep Detailed Maintenance Records
- Track oil changes, filter replacements, inspections, and repairs.
- Benefit: Helps identify recurring issues and ensures compliance with warranty requirements.
B. Follow Manufacturer’s Guidelines
- Always refer to the Cummins service manual for recommended service intervals and procedures.
C. Train Operators and Technicians
- Ensure everyone handling the equipment understands basic maintenance tasks and can identify early warning signs.
D. Use Quality Parts and Fluids
- Use Cummins-approved filters, lubricants, and coolants to maintain performance and reliability.
E. Conduct Regular Visual Inspections
- Look for leaks, worn belts, corroded electrical connections, and other visible signs of trouble.
Oil Filter & Related Components for Cummins ISB 4.5 Engine
Oil Filter & Related Components for Cummins ISB 5.9 Engine
Oil Filter & Related Components for Cummins ISB 6.7 Engine
Oil Filter & Related Components for Cummins QSB 4.5 Engine
Oil Filter & Related Components for Cummins QSB 5.9 Engine
Oil Filter & Related Components for Cummins QSB 6.7 Engine
Oil Filter & Related Components for Cummins QSB 7.0 Engine
5. Troubleshooting Common Preventive Maintenance Issues
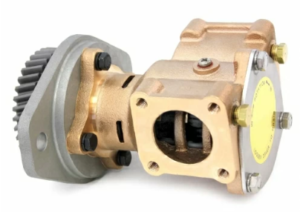
Symptom | Possible Cause | Maintenance Solution |
Low Oil Pressure | Low oil level, worn bearings | Check oil level, inspect bearings |
Overheating | Coolant leak, radiator clog, bad thermostat | Check coolant, flush system, replace thermostat |
Hard Starting | Weak battery, dirty fuel filters | Charge battery, replace filters |
Black Exhaust Smoke | Clogged air filter, injector issues | Replace air filter, inspect injectors |
Poor Fuel Economy | Underinflated tires, dirty injectors | Check tire pressure, clean injectors |
Raw Water Pump & Related Components for Cummins QSB 5.9 Engine
Raw Water Pump & Related Components for Cummins QSB 6.7 Engine
Raw Water Pump & Related Components for Cummins QSB 7.0 Engine
6. Developing a Preventive Maintenance Program
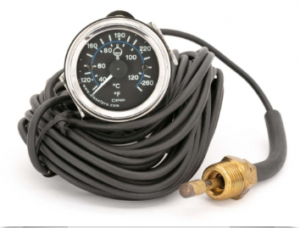
For fleets or businesses relying on Cummins engines, a structured PM program improves efficiency and reduces costs.
Steps to Build a PM Program:
- Assess Equipment Needs:
- Consider operating hours, load conditions, and environmental factors.
- Consider operating hours, load conditions, and environmental factors.
- Create a Maintenance Schedule:
- Define service intervals for each component.
- Define service intervals for each component.
- Assign Responsibilities:
- Designate technicians for specific maintenance tasks.
- Designate technicians for specific maintenance tasks.
- Implement Checklists:
- Use detailed checklists to ensure all inspections and services are performed correctly.
- Use detailed checklists to ensure all inspections and services are performed correctly.
- Review and Update Regularly:
- Adjust the program based on performance data and equipment usage patterns.
- Adjust the program based on performance data and equipment usage patterns.
Conclusion
Preventive maintenance is the key to maximizing the performance, reliability, and lifespan of Cummins ISB and QSB engines. By adhering to regular maintenance schedules, performing critical tasks like oil changes, fuel system inspections, and cooling system checks, and continuously monitoring engine performance metrics, operators can minimize downtime, reduce repair costs, and ensure their engines run at peak efficiency.
Whether managing a single engine or an entire fleet, a well-executed preventive maintenance program is an investment in productivity, safety, and cost savings. Always refer to Cummins’ service manuals for engine-specific guidelines and recommendations to keep your equipment running smoothly.
Parts Catalog Main Page for Cummins ISB Marine Engine
Cummins ISB 4.5 & Related Components
Cummins ISB 5.9 & Related components
Cummins ISB 6.7 & Related Components
Parts Catalog Main page for Cummins QSB Marine Engine
Cummins QSB 4.5 & Related Components
Cummins QSB 5.9 & Related Components
Cummins QSB 6.7 & Related Components
Cummins QSB 7.0 & Related Components